Air Filtration Solutions For The Power Industry
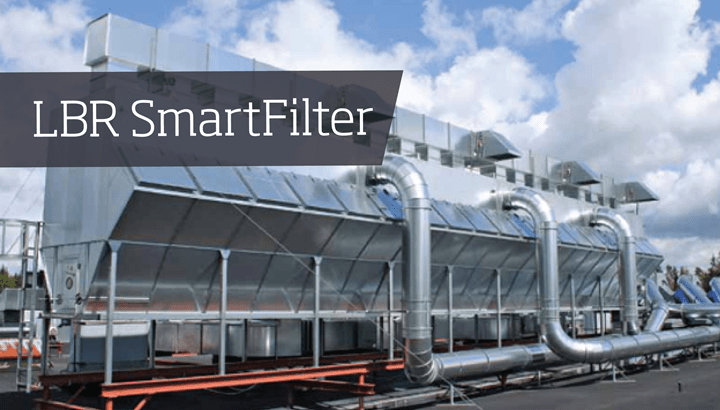
Imagine a bustling power plant, a symphony of whirring turbines and humming generators working tirelessly to keep our homes lit and our industries powered. Now, picture an invisible threat lurking within, microscopic particles silently impacting the plant’s efficiency and the health of its workers. Air filtration, often unseen and unsung, stands as the vigilant guardian, protecting this critical infrastructure.
The power industry, a cornerstone of modern society, faces unique challenges in maintaining operational efficiency and regulatory compliance. Effective air filtration solutions are not merely a nice-to-have but a necessity, safeguarding equipment from damage, improving worker health and safety, and minimizing environmental impact. This article explores the evolving landscape of air filtration in the power industry, highlighting its significance, examining current technologies, and peering into the future of clean air in power generation.
The Silent Threat: Understanding Air Contamination in Power Plants
Power plants, regardless of their energy source—coal, gas, nuclear, or renewable—are inherently susceptible to air contamination. Coal-fired plants contend with fly ash, particulate matter, and sulfur dioxide. Gas turbines are vulnerable to compressor fouling from airborne particles. Nuclear facilities require stringent filtration systems to manage radioactive particles and maintain air purity.
These contaminants, if left unchecked, can wreak havoc. Airborne particles erode turbine blades, reduce heat exchanger efficiency, and clog ventilation systems. This leads to costly downtime, increased maintenance expenses, and reduced power output. Moreover, exposure to these pollutants poses significant health risks to plant personnel, including respiratory illnesses and cardiovascular problems.
According to a 2022 report by the U.S. Energy Information Administration (EIA), unplanned outages in power plants cost the U.S. economy billions of dollars annually, with a significant portion attributable to equipment failures exacerbated by air contamination. This highlights the economic imperative of investing in robust air filtration systems.
A Multi-Layered Defense: Types of Air Filtration Technologies
The power industry employs a range of air filtration technologies, each designed to capture specific types of contaminants. These solutions often work in tandem, creating a multi-layered defense against airborne threats.
Pre-Filters: The First Line of Defense
Pre-filters, typically made of pleated or washable materials, are the first line of defense against larger particles such as dust, pollen, and insects. They extend the lifespan of more sophisticated filters by capturing the bulk of the particulate matter, preventing premature clogging and reducing maintenance frequency.
High-Efficiency Particulate Air (HEPA) Filters: Capturing the Invisible
HEPA filters are renowned for their ability to capture at least 99.97% of particles that are 0.3 microns in diameter. They are crucial in nuclear power plants and other facilities where capturing even the smallest radioactive particles is essential. These filters are also increasingly used in control rooms and other areas where worker health and safety are paramount.
Activated Carbon Filters: Neutralizing Odors and Gases
Activated carbon filters are designed to remove gaseous pollutants, odors, and volatile organic compounds (VOCs). They work through a process called adsorption, where pollutant molecules adhere to the surface of the activated carbon material. These filters are particularly important in power plants that burn fossil fuels, where they help to mitigate the release of harmful gases into the atmosphere.
Electrostatic Precipitators (ESPs): A High-Voltage Solution
ESPs use an electrical charge to remove particles from the air stream. Particles are charged as they pass through an electric field and then collected on oppositely charged plates. ESPs are commonly used in coal-fired power plants to remove fly ash from flue gas, contributing to cleaner emissions.
Baghouse Filters: Fabric Filtration for Heavy Duty Applications
Baghouse filters use fabric bags to trap particulate matter. Dirty air is passed through the bags, and the particles are captured on the fabric surface. Baghouses are highly effective in removing large quantities of dust and are commonly used in industries like cement and power generation, where high volumes of particulate matter are generated.
Beyond Filtration: Monitoring and Maintenance
Effective air filtration is not a set-it-and-forget-it solution. Regular monitoring and maintenance are crucial to ensure optimal performance and prevent costly failures.
Differential pressure monitoring, for example, allows operators to track the pressure drop across a filter, indicating when it is becoming clogged and needs to be replaced. Air quality sensors can provide real-time data on particulate matter levels, allowing for proactive adjustments to filtration systems. Scheduled maintenance, including filter replacements and system inspections, is essential to prevent breakdowns and ensure long-term reliability.
The National Air Filtration Association (NAFA) provides guidance and certifications for air filtration professionals, emphasizing the importance of proper installation, maintenance, and performance testing. Their resources are invaluable for power plant operators seeking to optimize their air filtration strategies.
The Future of Air Filtration in the Power Industry
The power industry is undergoing a significant transformation, driven by the need for cleaner energy and greater efficiency. This shift is influencing the evolution of air filtration technologies.
Advanced materials, such as nanofibers and self-cleaning coatings, are being developed to improve filter efficiency and longevity. Smart filtration systems, equipped with sensors and data analytics, are enabling predictive maintenance and optimized filter performance. Integration with Building Management Systems (BMS) is allowing for remote monitoring and control of air filtration systems, improving operational efficiency and reducing labor costs.
Moreover, the increasing adoption of renewable energy sources, such as solar and wind power, is creating new demands for air filtration solutions. While these sources are inherently cleaner than fossil fuels, they still require air filtration to protect sensitive electronic equipment from dust and other contaminants.
A Breath of Fresh Air: Conclusion
Air filtration in the power industry is far more than a technical detail; it is a crucial component of operational efficiency, worker safety, and environmental stewardship. As the power industry continues to evolve, innovative air filtration solutions will play an increasingly vital role in ensuring a clean and sustainable energy future. The invisible shield that protects our power plants is a testament to human ingenuity, a reminder that even the smallest details can have a profound impact on our world.
The dedication of engineers, technicians, and researchers in advancing air filtration technology brings a sense of hope. Their work ensures that the power that fuels our lives is generated in a way that protects both people and the planet. It's a quiet revolution, one filter at a time.
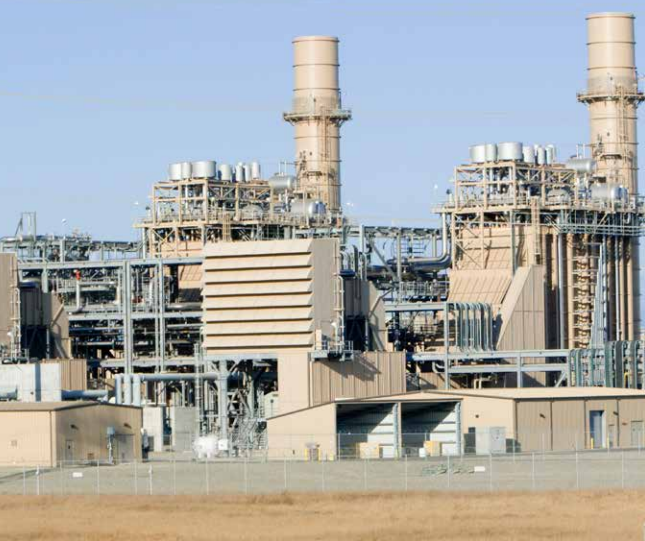
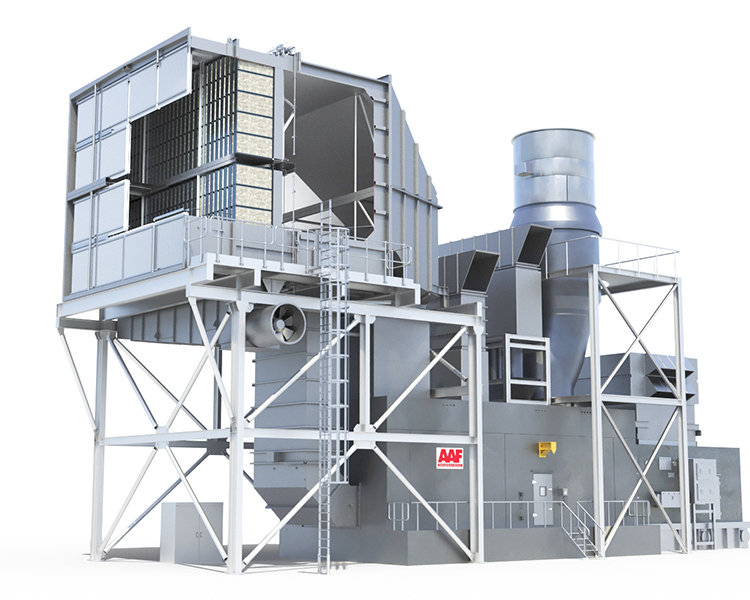
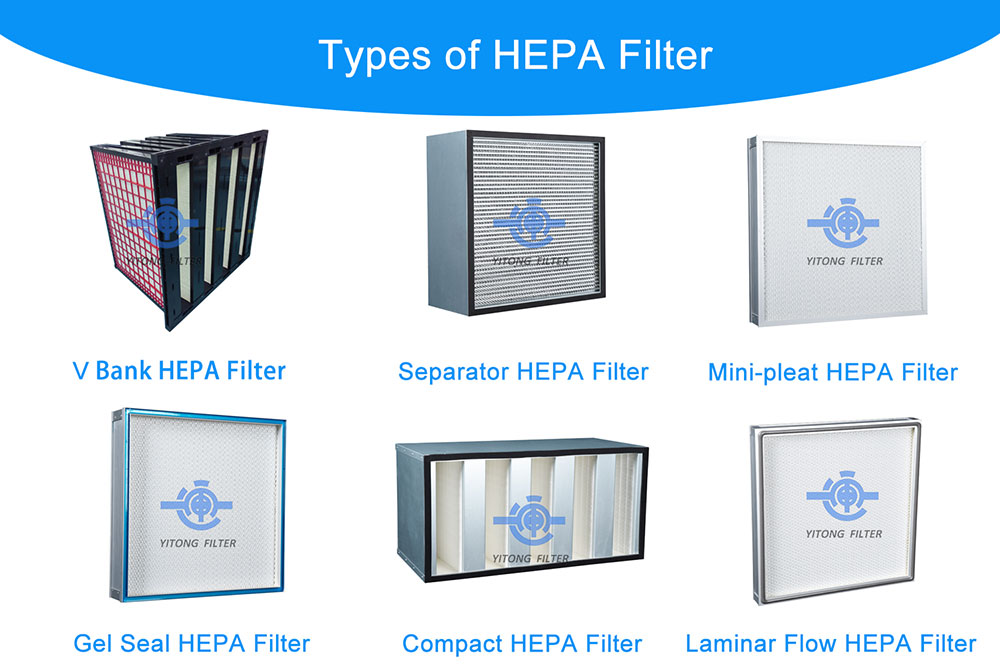

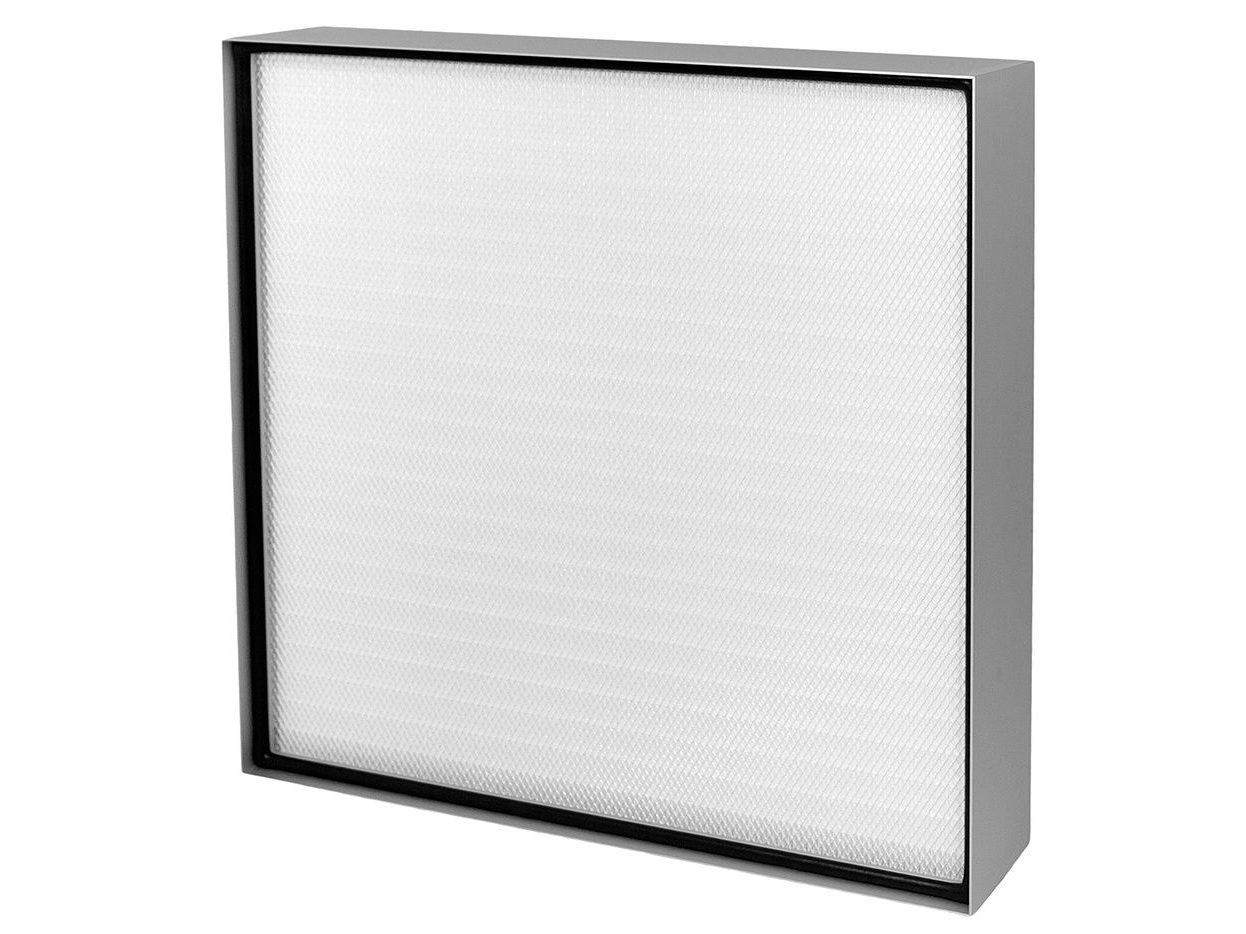

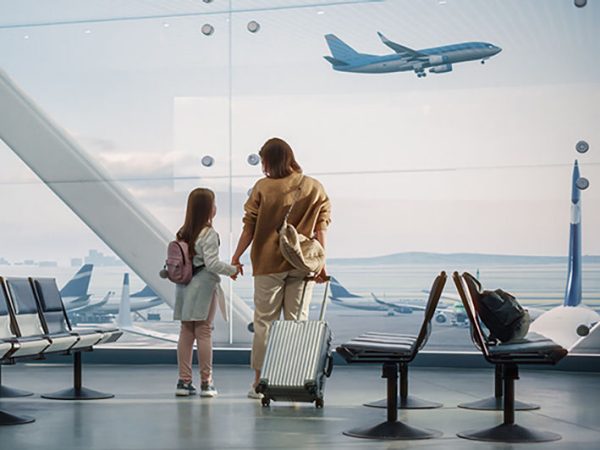
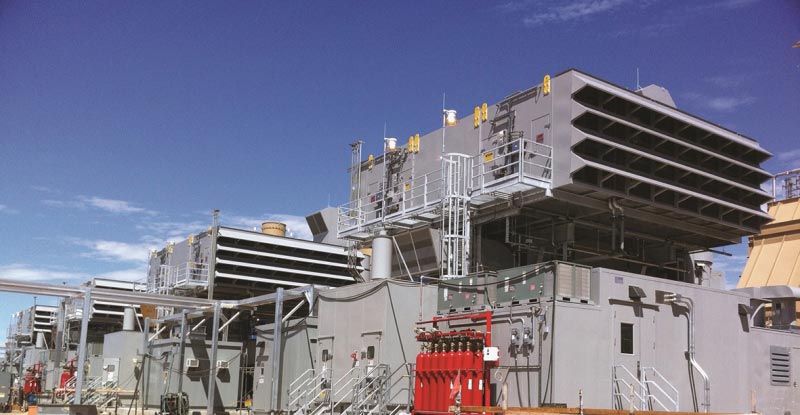
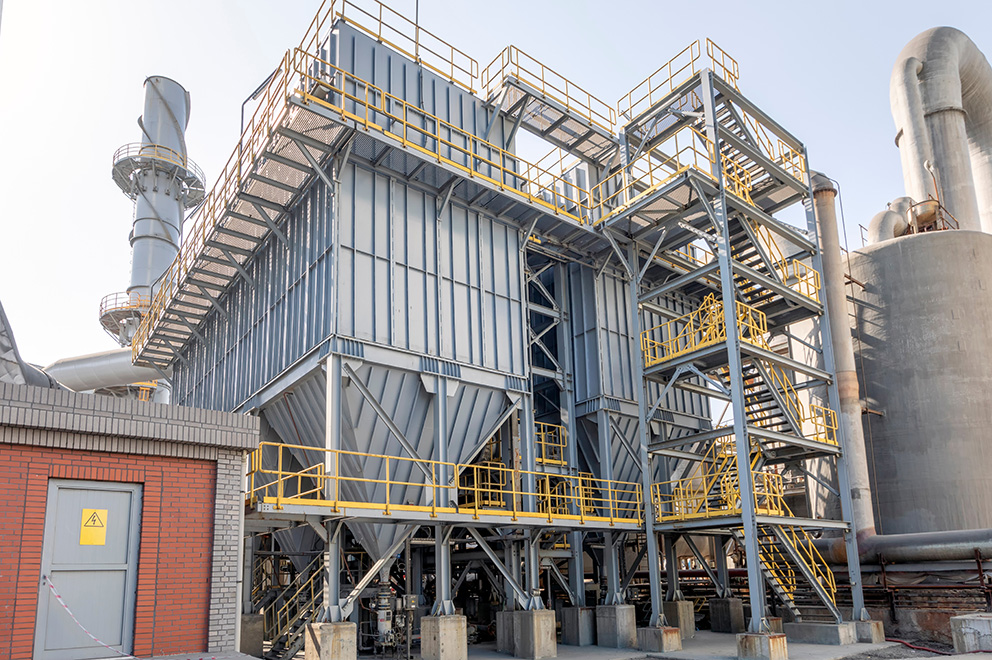

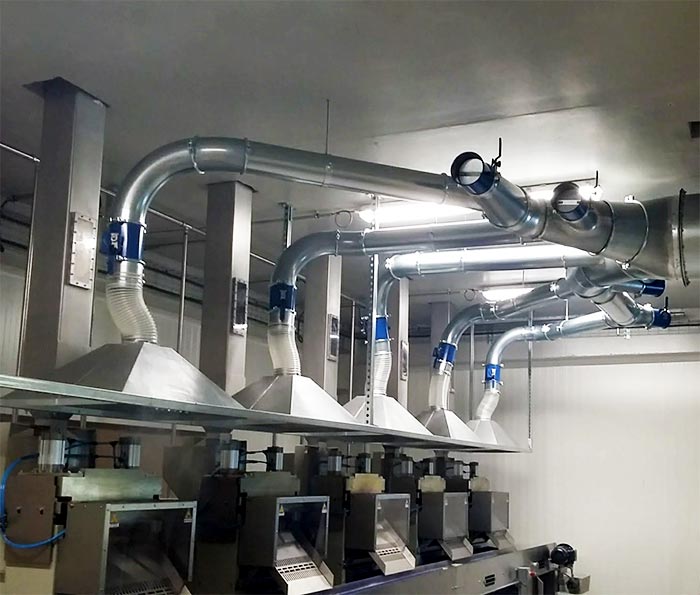
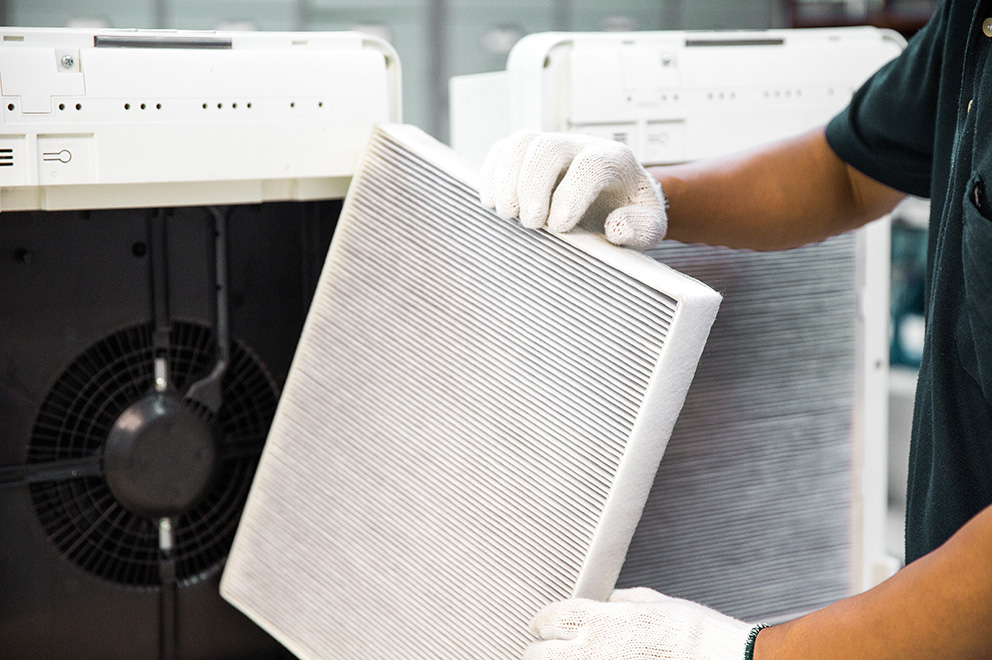

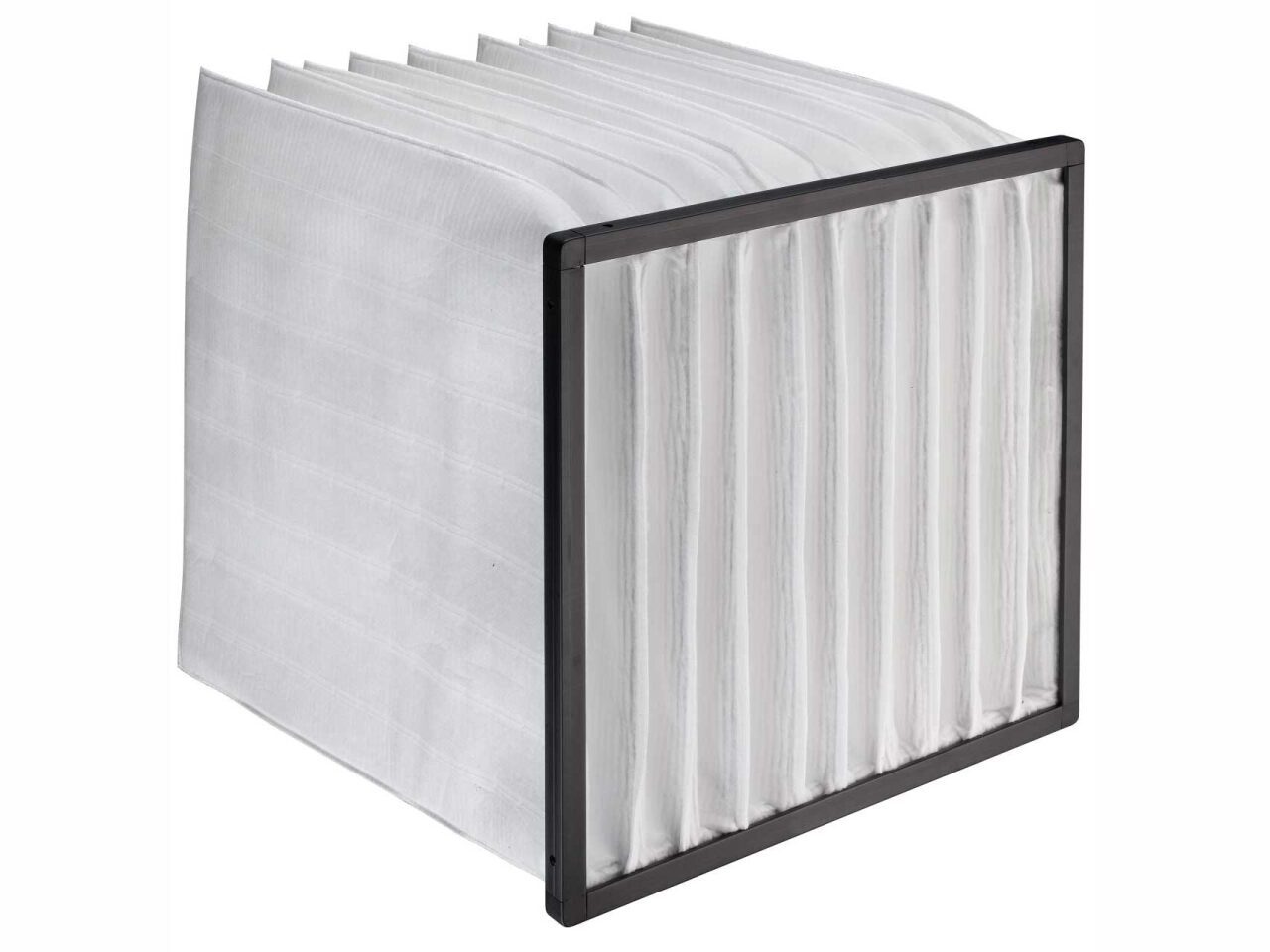
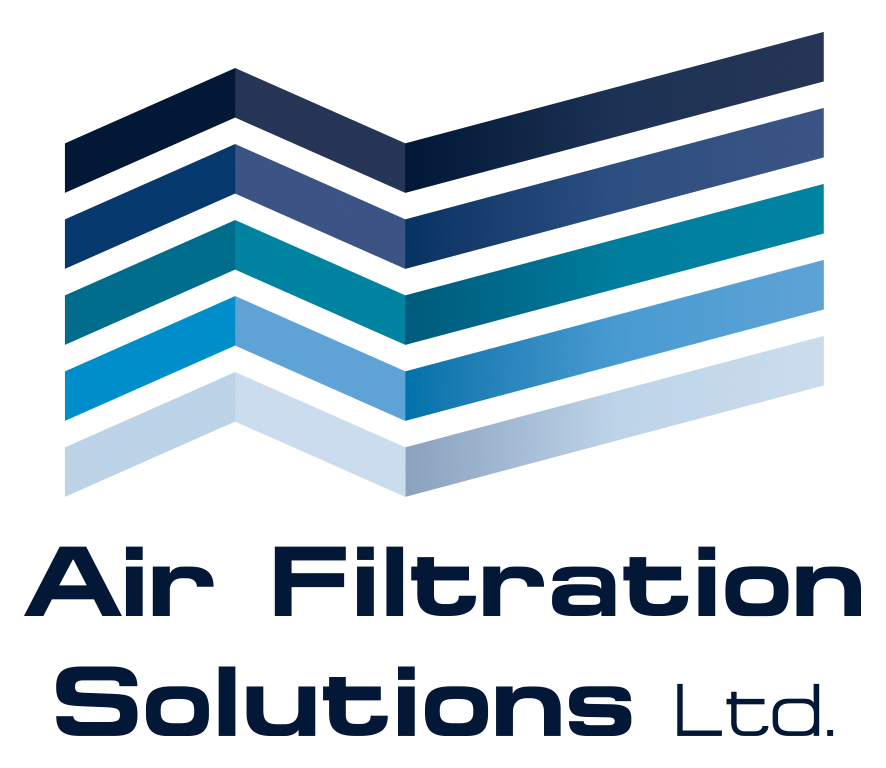

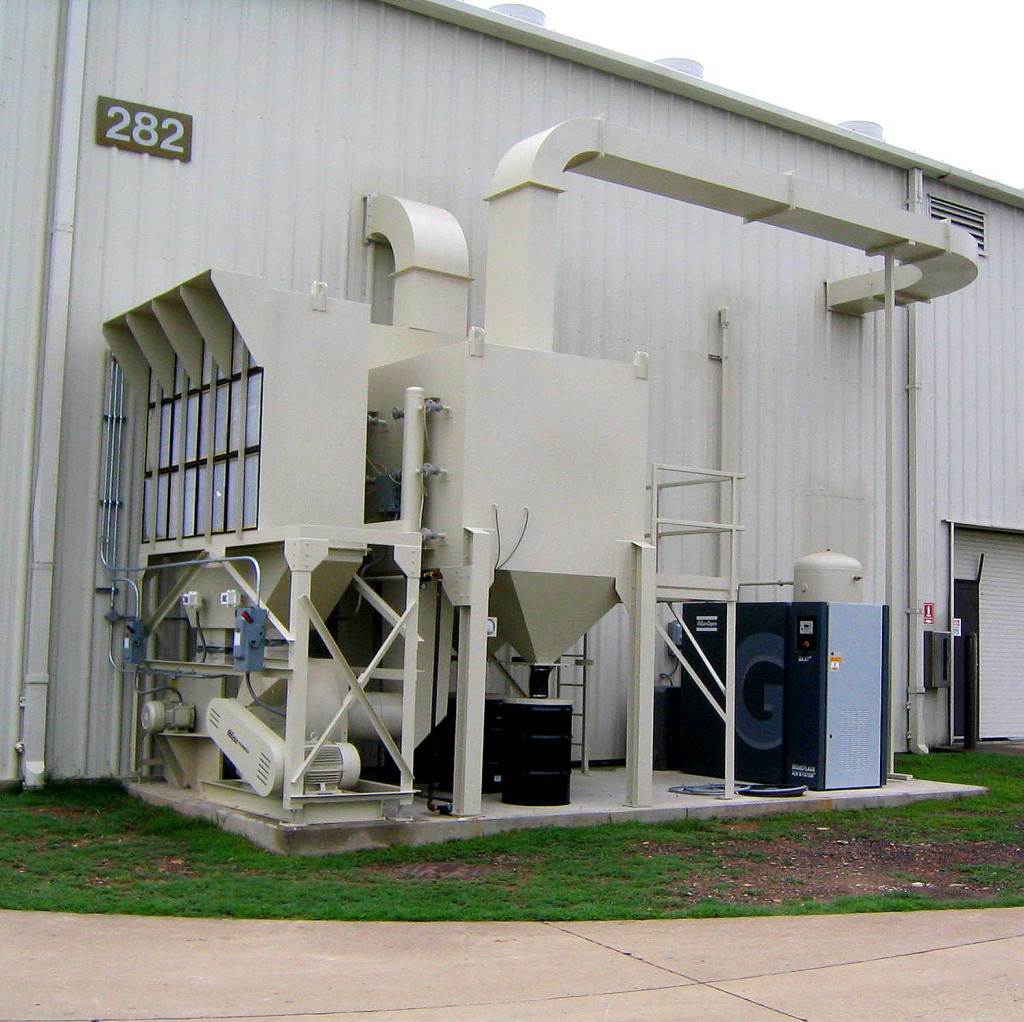
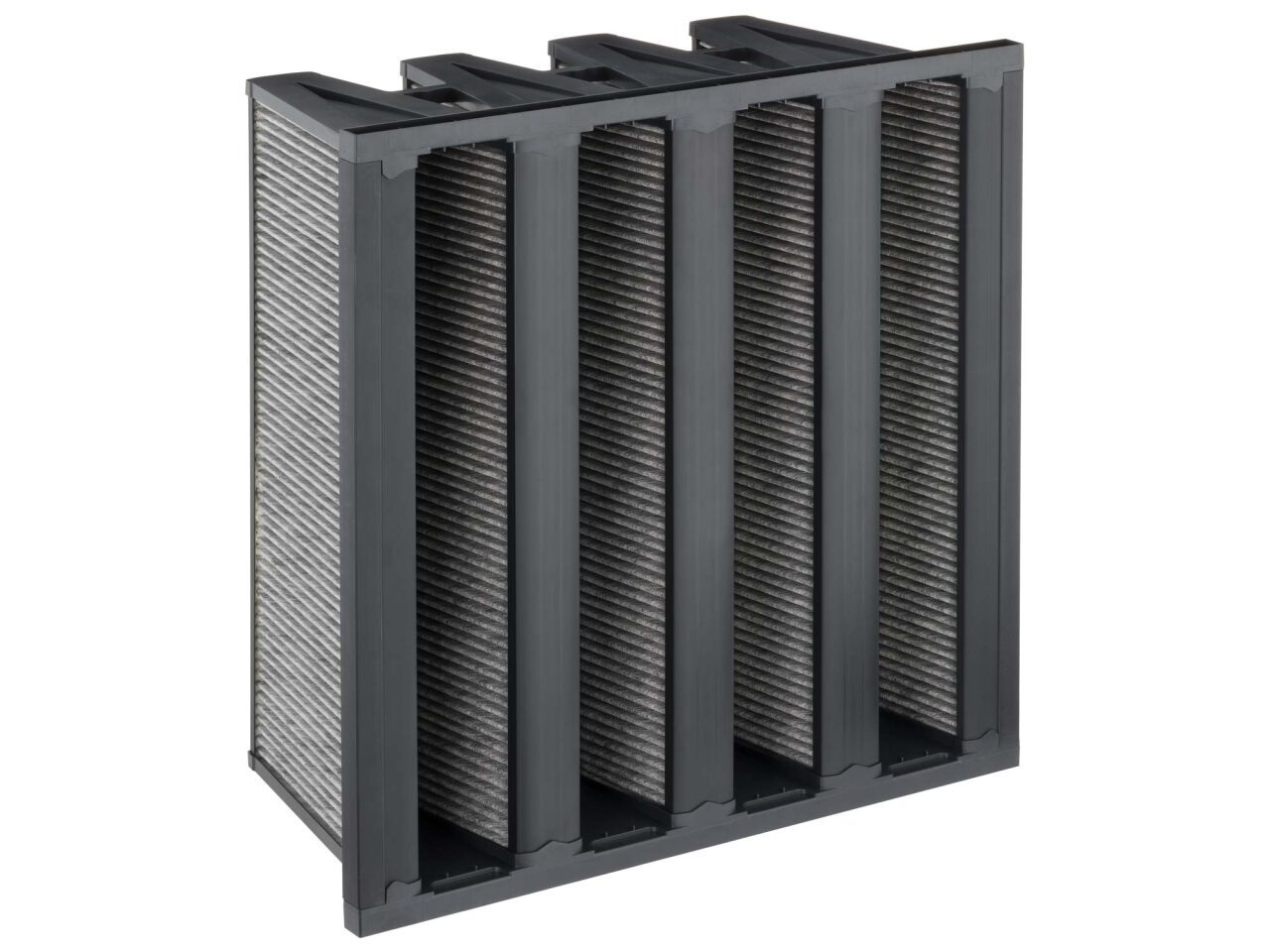