Bathroom Partitions Hardware Home Depot

Across the United States, a growing concern is emerging within the construction and facilities management sectors: the availability and pricing of bathroom partition hardware, a seemingly mundane component with significant ramifications. Delays in obtaining these essential parts are stalling projects, increasing costs, and prompting questions about supply chain resilience and the role of major retailers like Home Depot in the market.
The issue centers on the essential yet often overlooked hardware required for assembling and installing bathroom partitions. This hardware includes items such as hinges, latches, brackets, and mounting systems, crucial for the functionality and structural integrity of public and commercial restrooms. While Home Depot is a major player in the home improvement market, their role in supplying these specific components to large-scale commercial projects is under scrutiny amidst reports of shortages and fluctuating prices.
The Impact on Construction and Renovation
Delays in acquiring bathroom partition hardware can have a cascading effect on construction schedules. Contractors and facility managers report waiting weeks, sometimes months, for deliveries that were previously readily available. This delay impacts not only the restroom construction itself but also overall project timelines, leading to increased labor costs and potential penalties for missed deadlines.
"We've experienced significant delays in several projects due to the unavailability of specific hardware," says Mark Thompson, a project manager at a commercial construction firm in Chicago. "What used to take a few days to procure now takes weeks, and that throws off the entire schedule."
The increased cost of hardware is another major concern. Contractors report that prices for certain components have risen sharply, impacting project budgets and forcing difficult decisions about material substitutions. This situation puts additional strain on already tight budgets, especially for smaller businesses and non-profit organizations.
Home Depot's Role and Response
Home Depot, as a major retailer of construction materials, is a significant source for many contractors and facility managers. However, the company's supply chain for specialized hardware, like that used in bathroom partitions, is facing challenges. Some contractors express frustration over inconsistent stock levels and difficulty obtaining bulk orders through Home Depot's online or in-store channels.
When contacted for comment, a Home Depot spokesperson acknowledged the challenges in the current supply chain environment. They stated that Home Depot is actively working to mitigate disruptions and improve product availability. The company also emphasized their commitment to providing competitive pricing and alternative product options whenever possible.
"We are aware of the supply chain constraints impacting various sectors, including construction. Our teams are working diligently with suppliers to improve inventory levels and minimize disruptions for our customers," the Home Depot representative said.
Alternative Suppliers and Mitigation Strategies
Faced with delays and rising costs, contractors are exploring alternative suppliers and implementing mitigation strategies. Some are turning to specialized distributors who focus solely on bathroom partitions and related hardware.
These distributors often have closer relationships with manufacturers and can provide more reliable supply chains, though potentially at a higher upfront cost. Others are opting for design changes or material substitutions to reduce their reliance on specific hardware components, which requires careful consideration of building codes and aesthetic requirements.
Looking Ahead: Building a More Resilient Supply Chain
The current situation highlights the need for a more resilient and diversified supply chain for construction materials, including seemingly small components like bathroom partition hardware. Industry experts suggest that fostering stronger relationships between manufacturers, distributors, and retailers is crucial to improving communication and forecasting demand.
Investing in domestic manufacturing and reducing reliance on single-source suppliers can also help mitigate future disruptions. As construction activity continues to rebound, addressing these supply chain vulnerabilities will be essential to ensuring projects stay on schedule and within budget.
The availability and pricing of bathroom partition hardware may seem like a niche issue, but it underscores broader challenges in the construction industry. By understanding the complexities of the supply chain and implementing proactive strategies, stakeholders can work together to build a more resilient and efficient system for delivering essential building components.
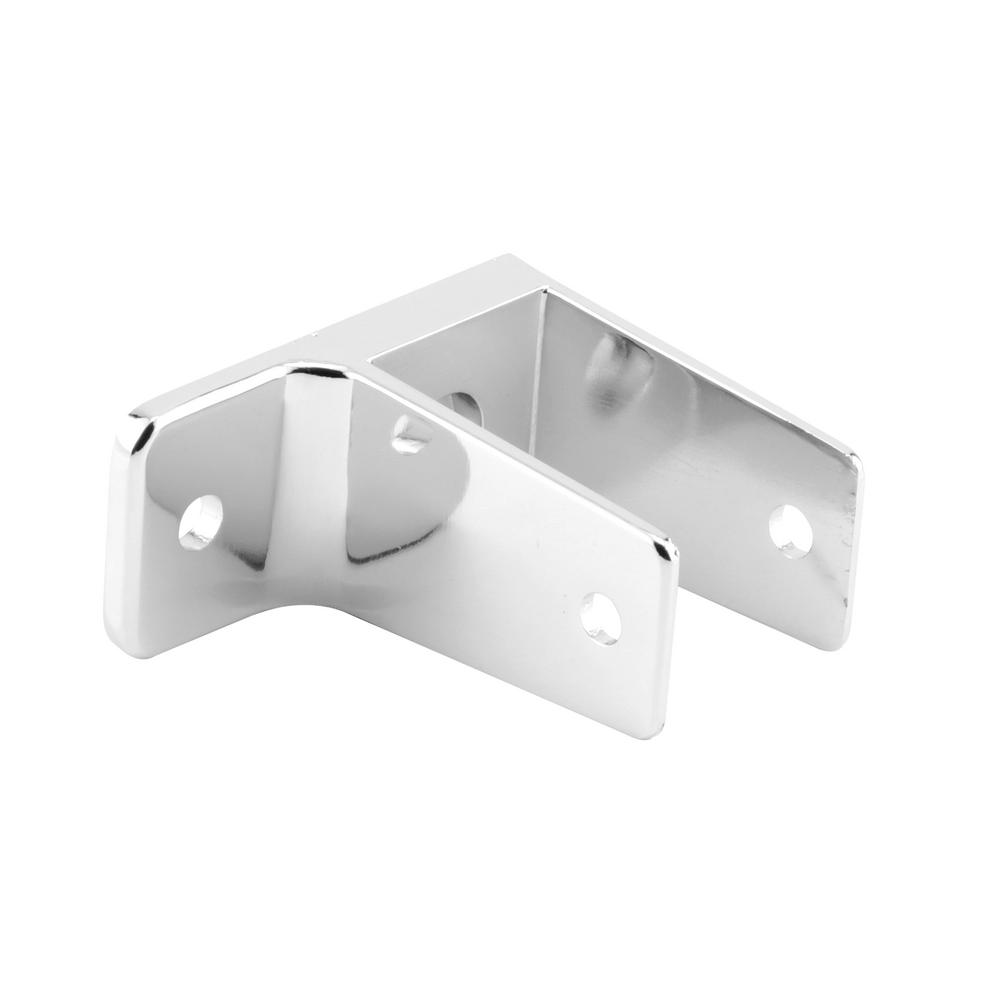


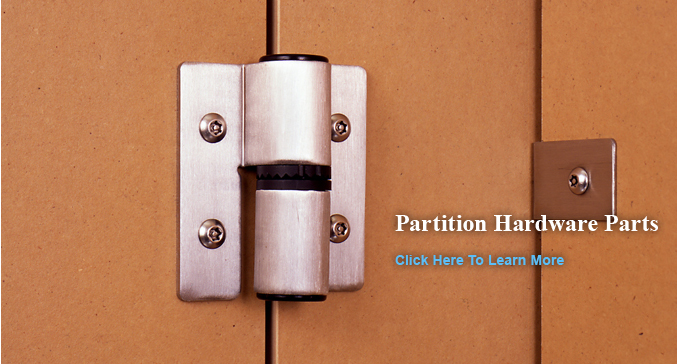

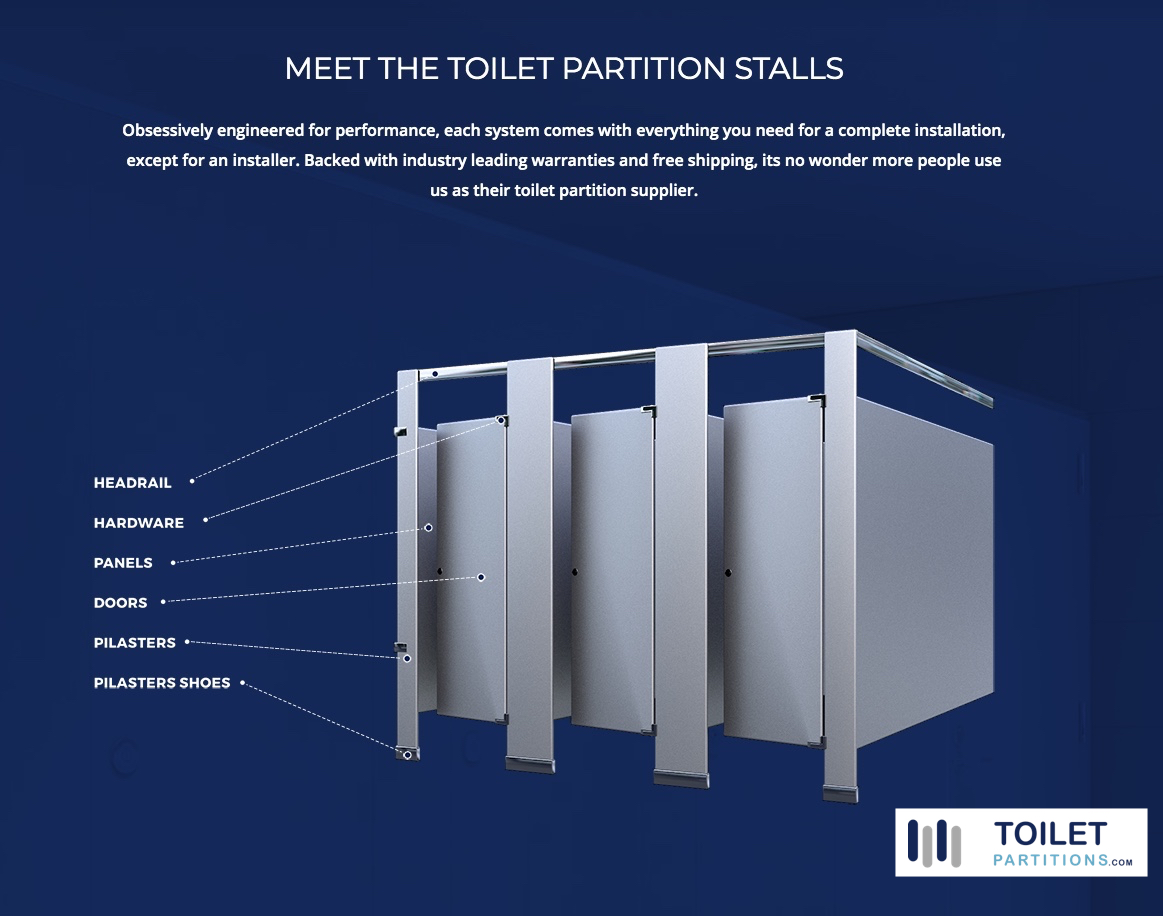
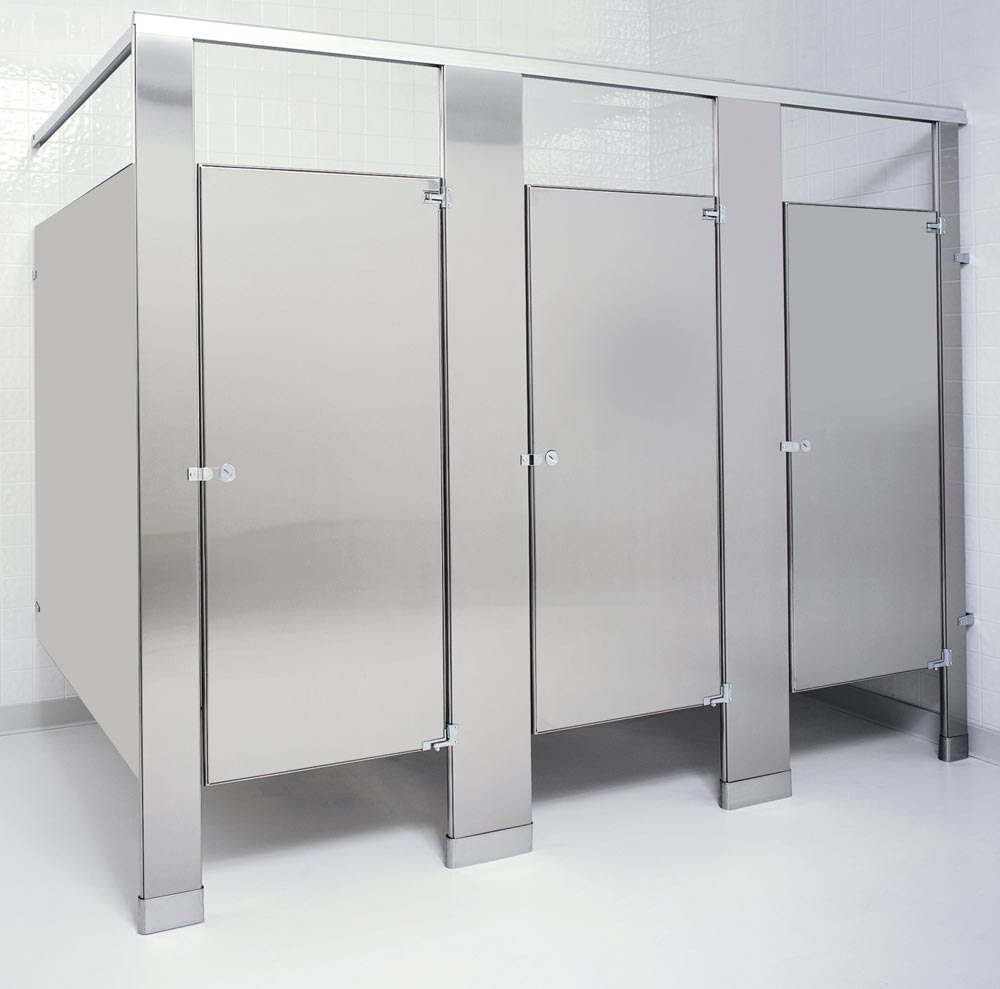

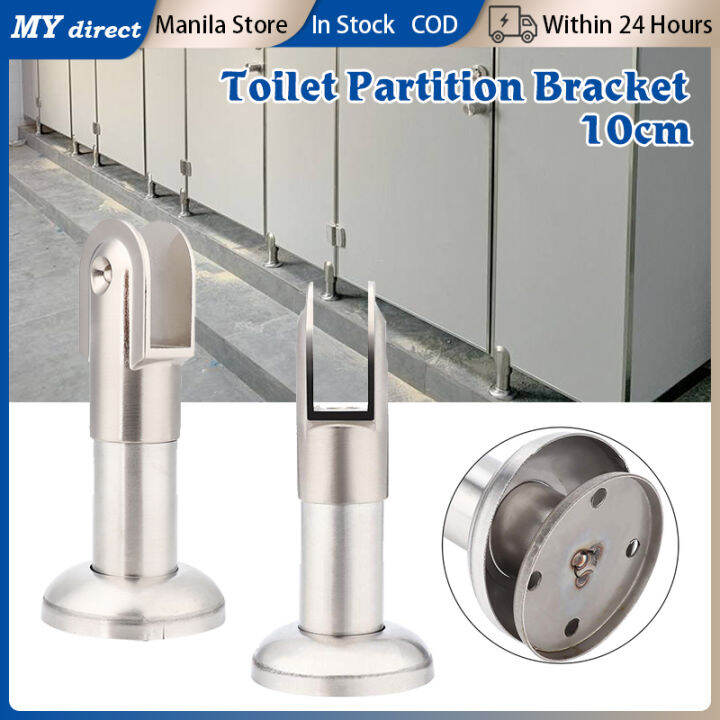
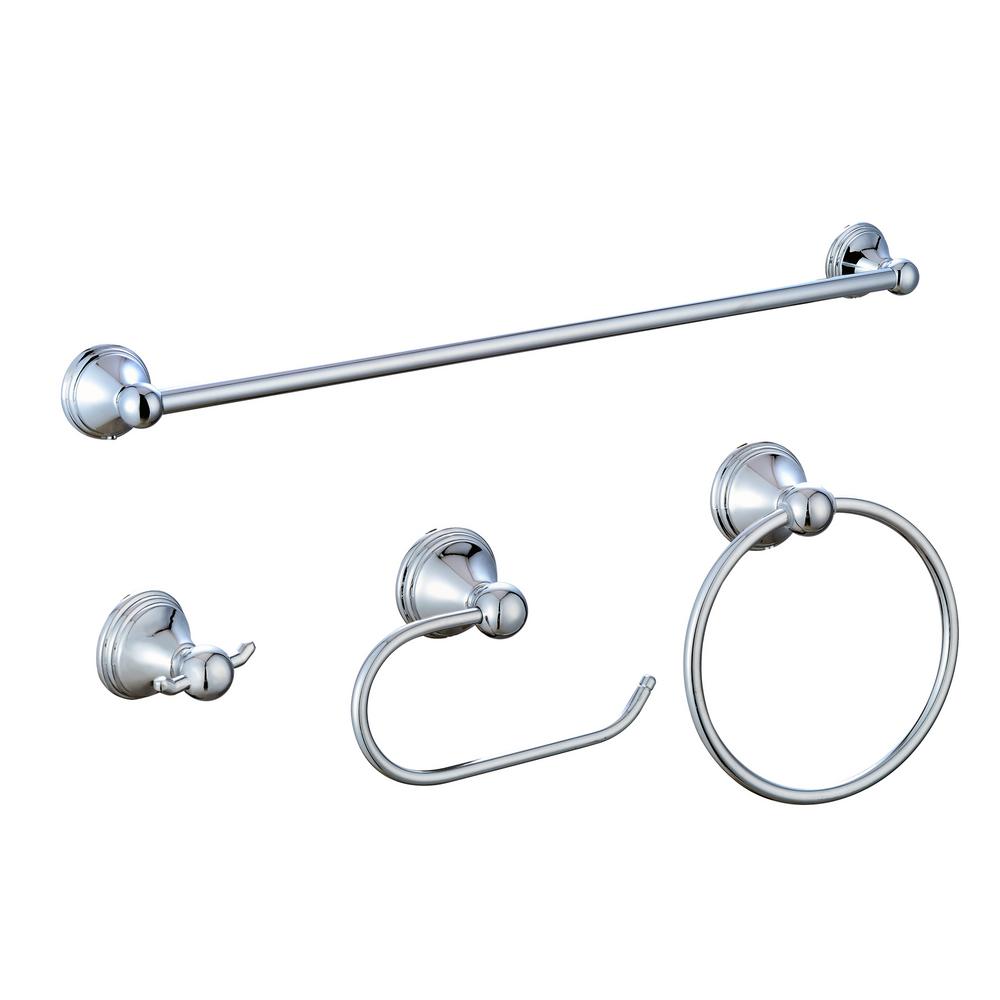
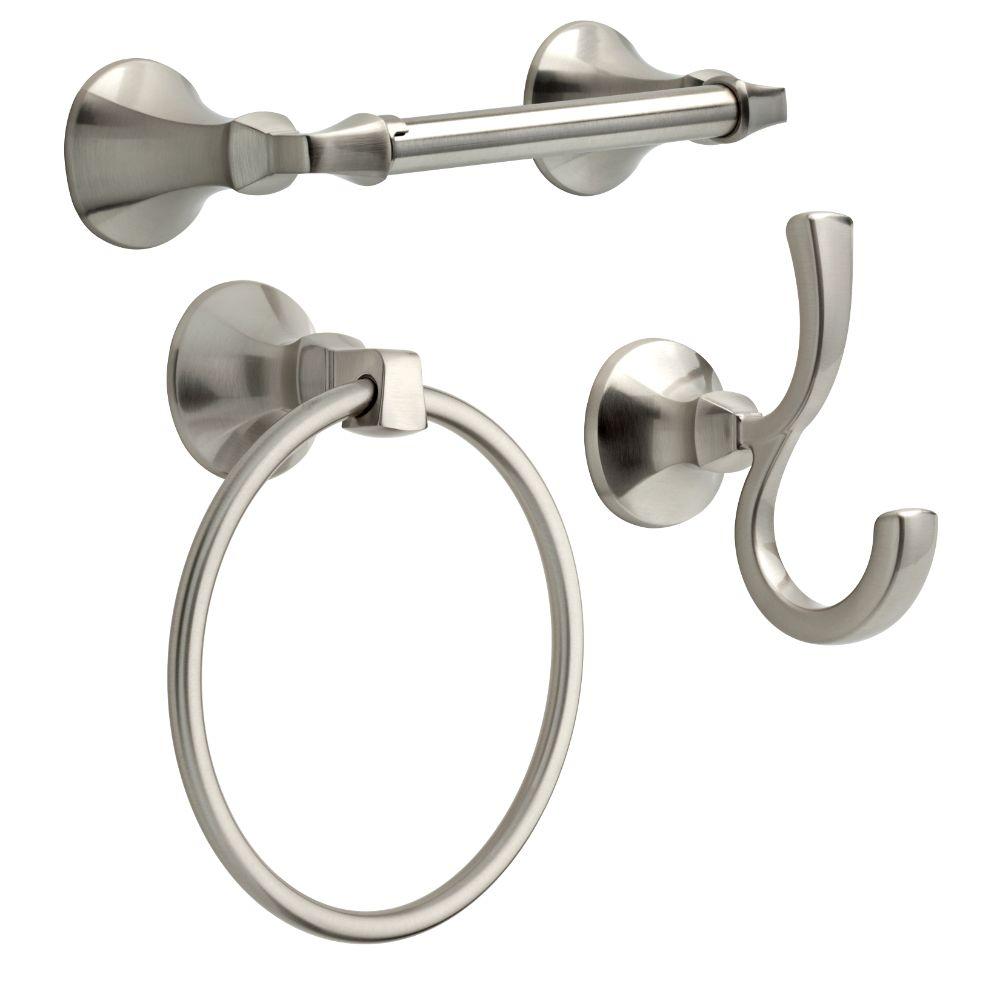

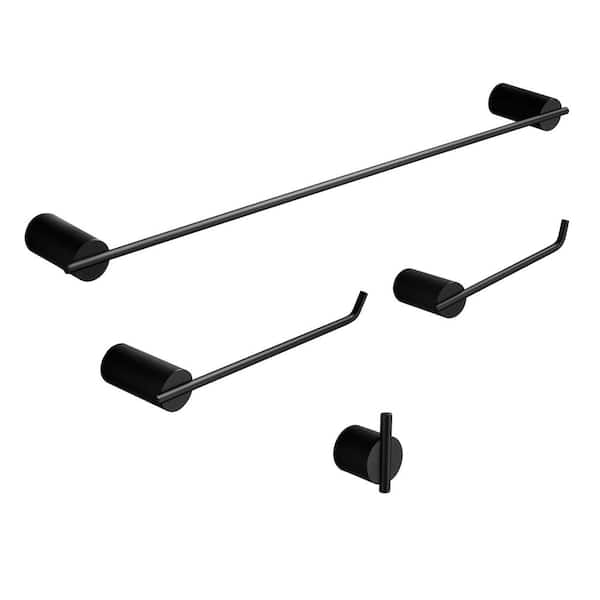
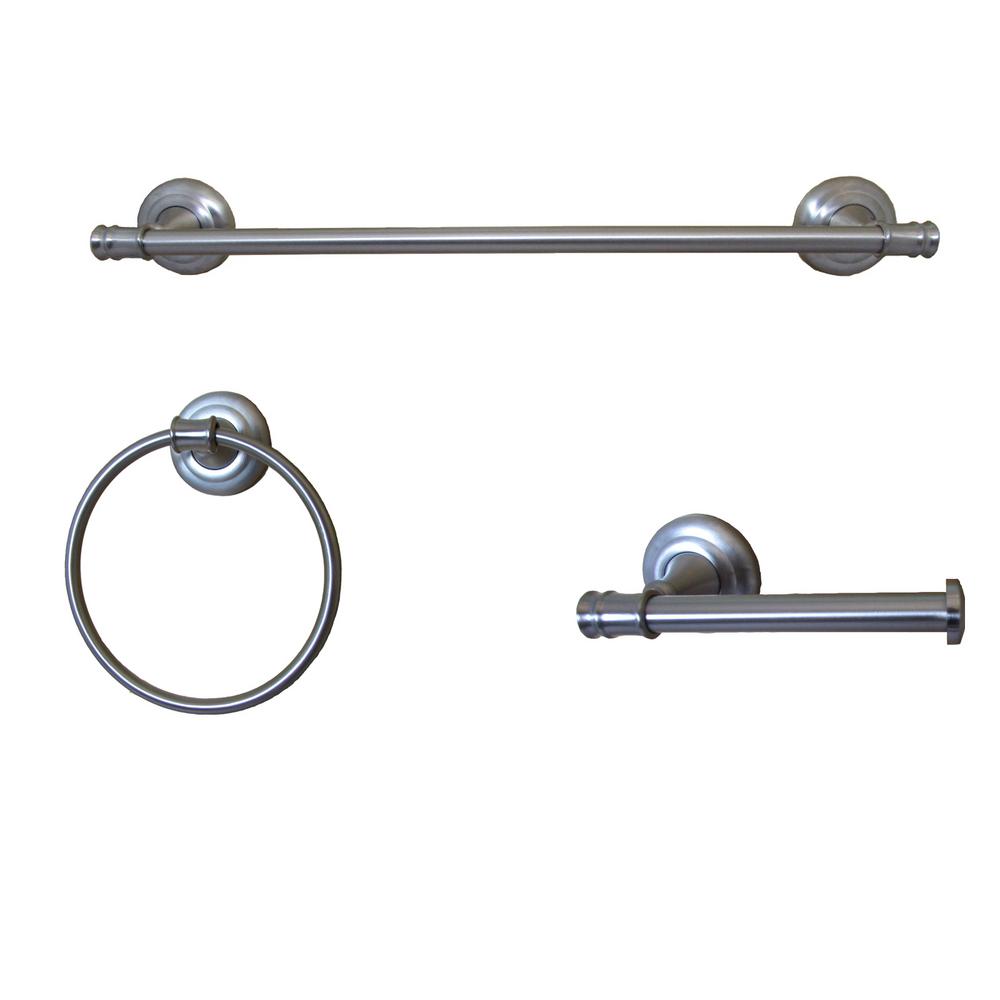
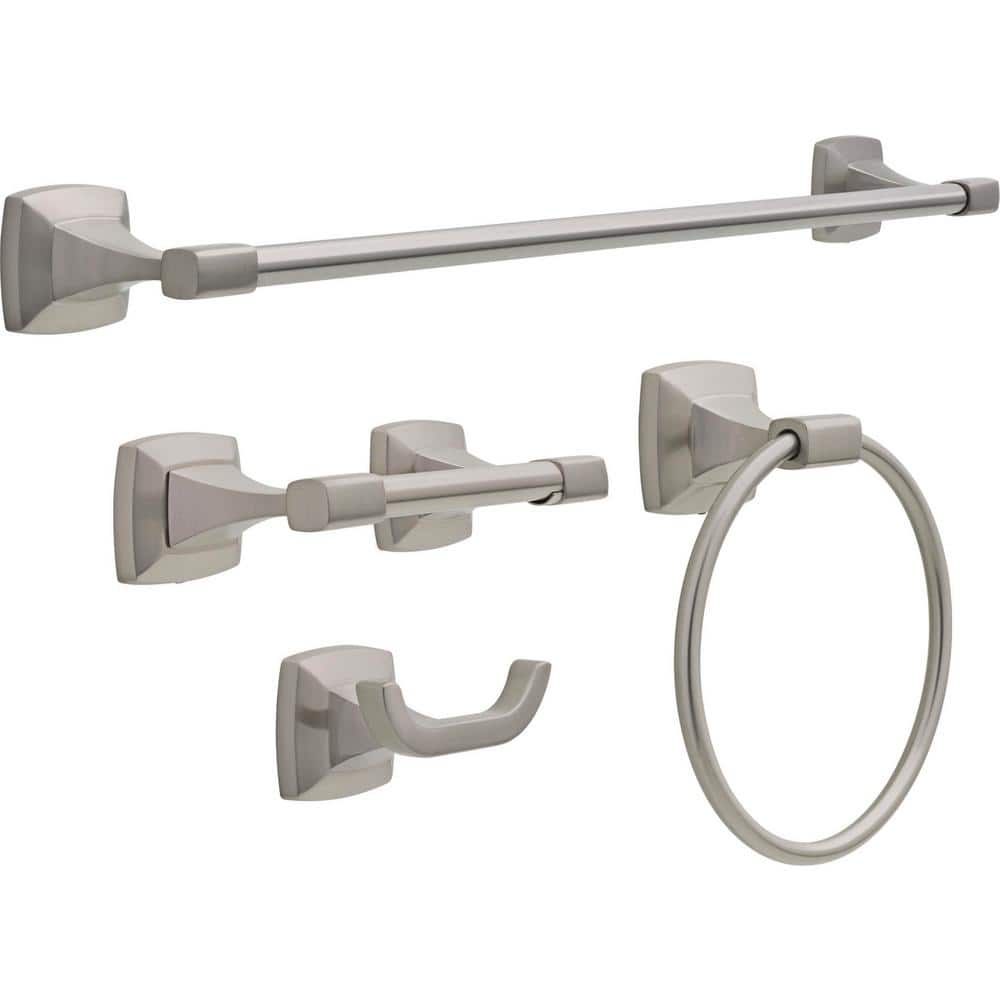
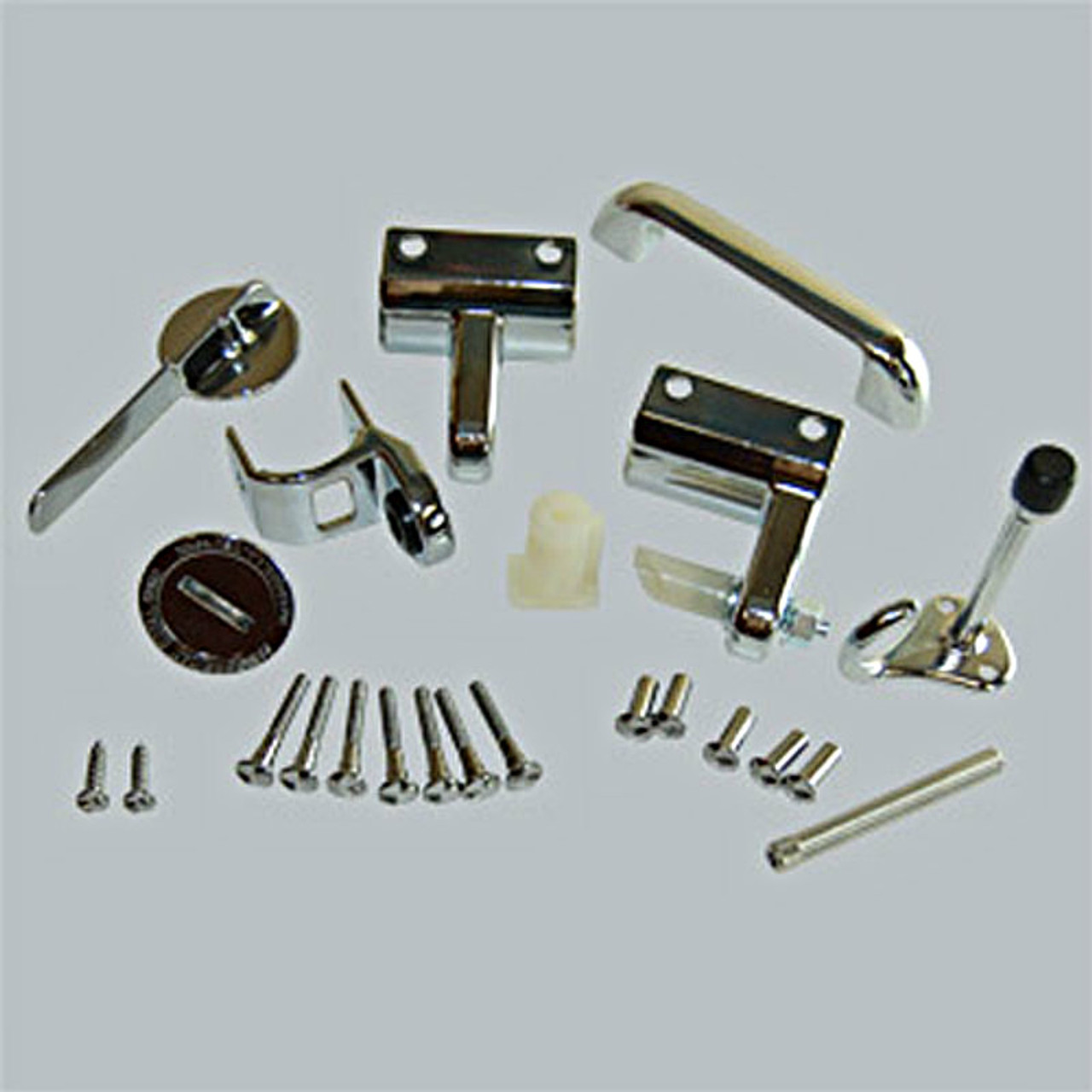

