Cost Of Concrete Flatwork Per Square Foot

Homeowners and contractors alike are feeling the pinch as the cost of concrete flatwork, such as patios, driveways, and sidewalks, continues to fluctuate across the United States. This price volatility presents challenges for budgeting and project planning, impacting both residential and commercial construction projects.
The national average cost for concrete flatwork currently ranges from $6 to $12 per square foot, but this figure can vary significantly depending on several factors. These factors include geographic location, the complexity of the project, the chosen finish, and the prevailing market prices for materials and labor.
Factors Influencing Concrete Flatwork Costs
One of the most significant cost drivers is location. Areas with higher labor costs, stricter environmental regulations, and longer transportation distances for materials tend to have pricier concrete work.
For instance, states like California and New York typically experience higher costs compared to states in the Midwest or South. These differences can stem from local economic conditions, union presence, and the demand for skilled concrete finishers.
Material Costs: A Key Component
The price of cement, aggregate (sand and gravel), and other admixtures directly impacts the overall cost. Fluctuations in these commodity prices, often influenced by global supply chains and energy costs, can create price volatility.
Reinforcement, such as wire mesh or rebar, is also a crucial component, especially for driveways or areas expected to bear heavy loads. The amount and type of reinforcement will influence the final price.
Labor and Project Complexity
Labor costs account for a substantial portion of the total expense. Skilled concrete finishers are needed for proper mixing, pouring, leveling, and finishing.
Complex projects involving intricate designs, custom colors, or specialized finishes, such as stamped concrete or exposed aggregate, will inevitably require more labor and expertise, leading to higher costs. Projects requiring extensive site preparation, including excavation or grading, will also add to the expense.
Finishes and Customization
The type of finish chosen significantly affects the price. A basic broom finish is the most economical option, while more decorative finishes like stamped concrete or polished concrete command a premium.
Adding color pigments or integral colors to the concrete mix also increases material costs. Custom designs and intricate patterns require more labor-intensive work and therefore increase the overall price per square foot.
Impact on Homeowners and Businesses
The fluctuating cost of concrete flatwork can significantly impact homeowners planning renovations or new construction. Budgets need to be flexible to accommodate potential price increases.
Businesses relying on concrete for parking lots, sidewalks, or loading docks also need to factor in these costs when planning expansions or repairs. Unforeseen cost increases can strain budgets and delay projects.
“We’ve seen concrete prices fluctuate significantly over the past year,” said John Miller, a local contractor. “Clients need to be prepared for potential adjustments to their initial estimates.”
Mitigating Cost Increases
Several strategies can help mitigate the impact of rising concrete prices. Obtaining multiple quotes from reputable contractors is crucial.
Choosing simpler designs and standard finishes can also reduce costs without compromising the functionality. Consider phasing the project, completing only the most essential areas first.
Planning the project during the off-season (typically late fall or winter in some regions) may also result in lower prices due to reduced demand. Scheduling flexibility is key to navigating market fluctuations.
The Future of Concrete Costs
Industry experts predict that concrete prices will likely remain volatile in the near term, influenced by global economic factors and supply chain disruptions. Staying informed about market trends and consulting with experienced contractors are essential for successful project planning.
Technological advancements in concrete production and application may offer long-term cost-saving solutions. Innovations such as self-healing concrete or alternative cementitious materials could potentially stabilize prices and reduce maintenance costs in the future.
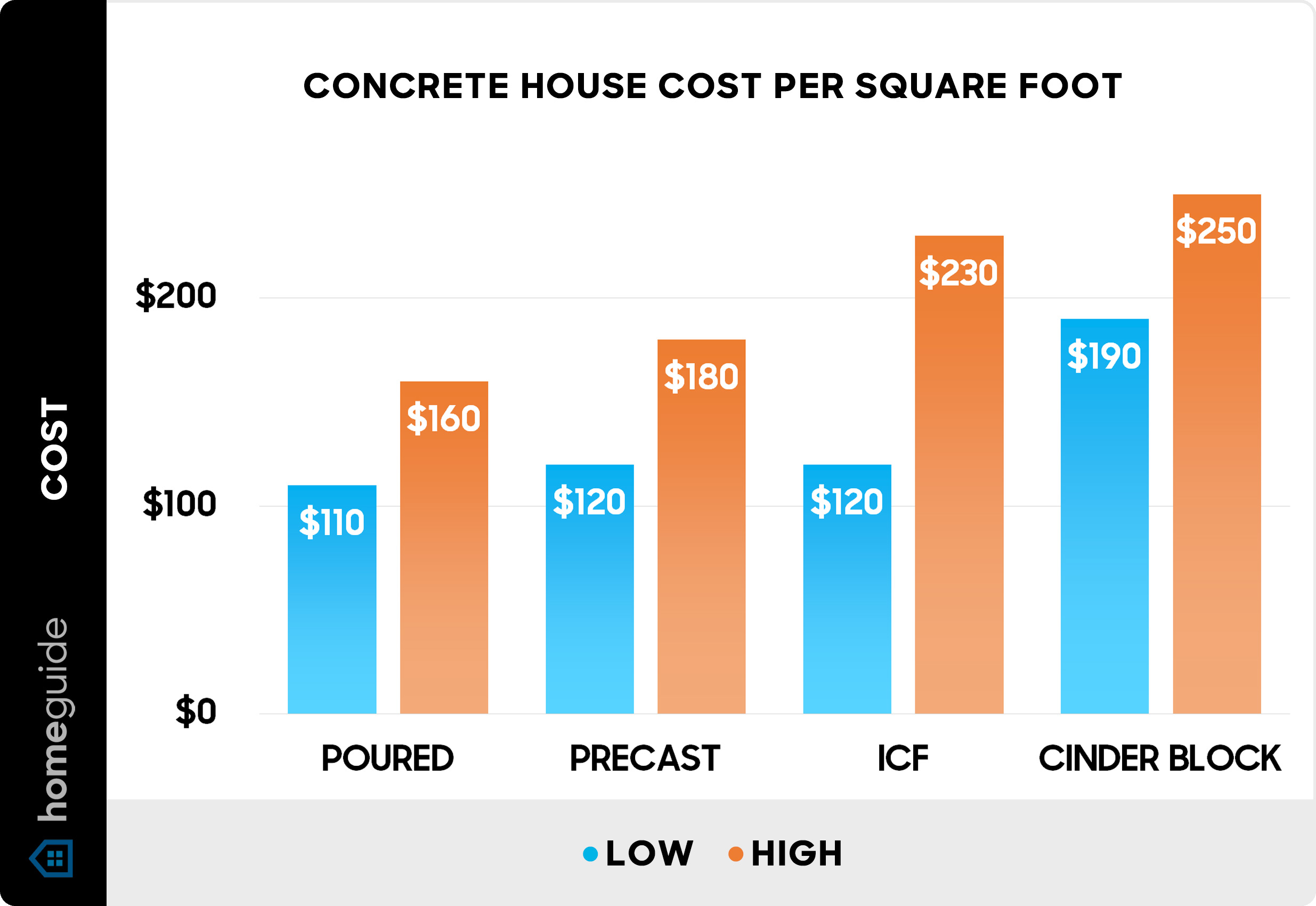
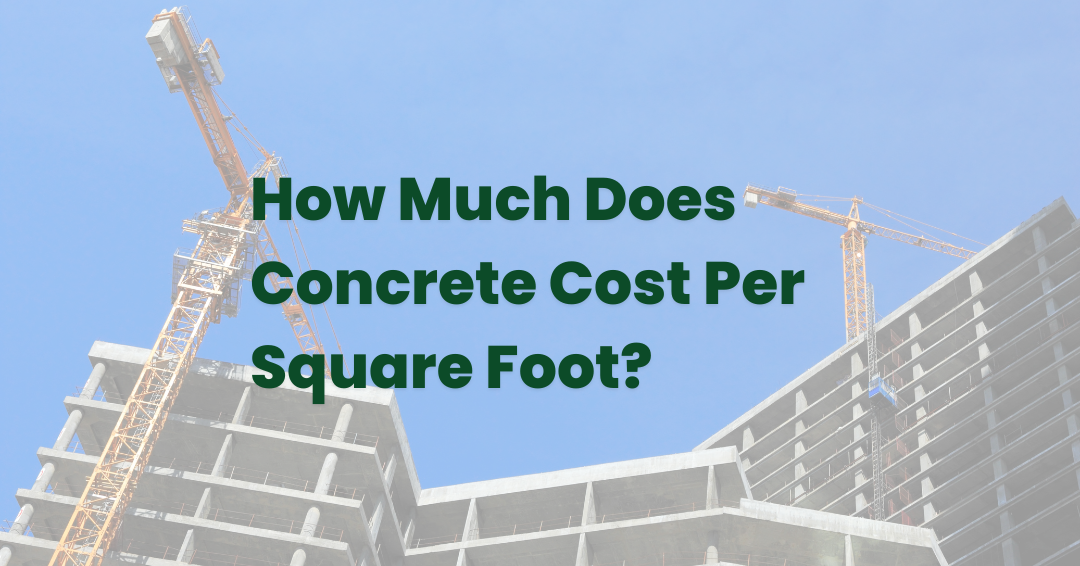
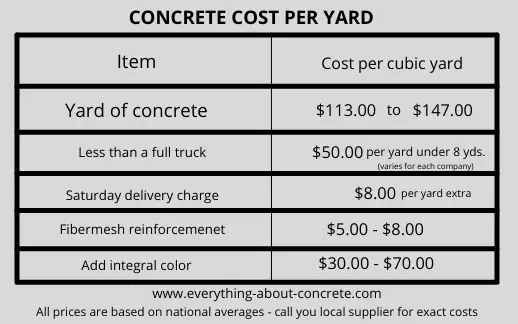
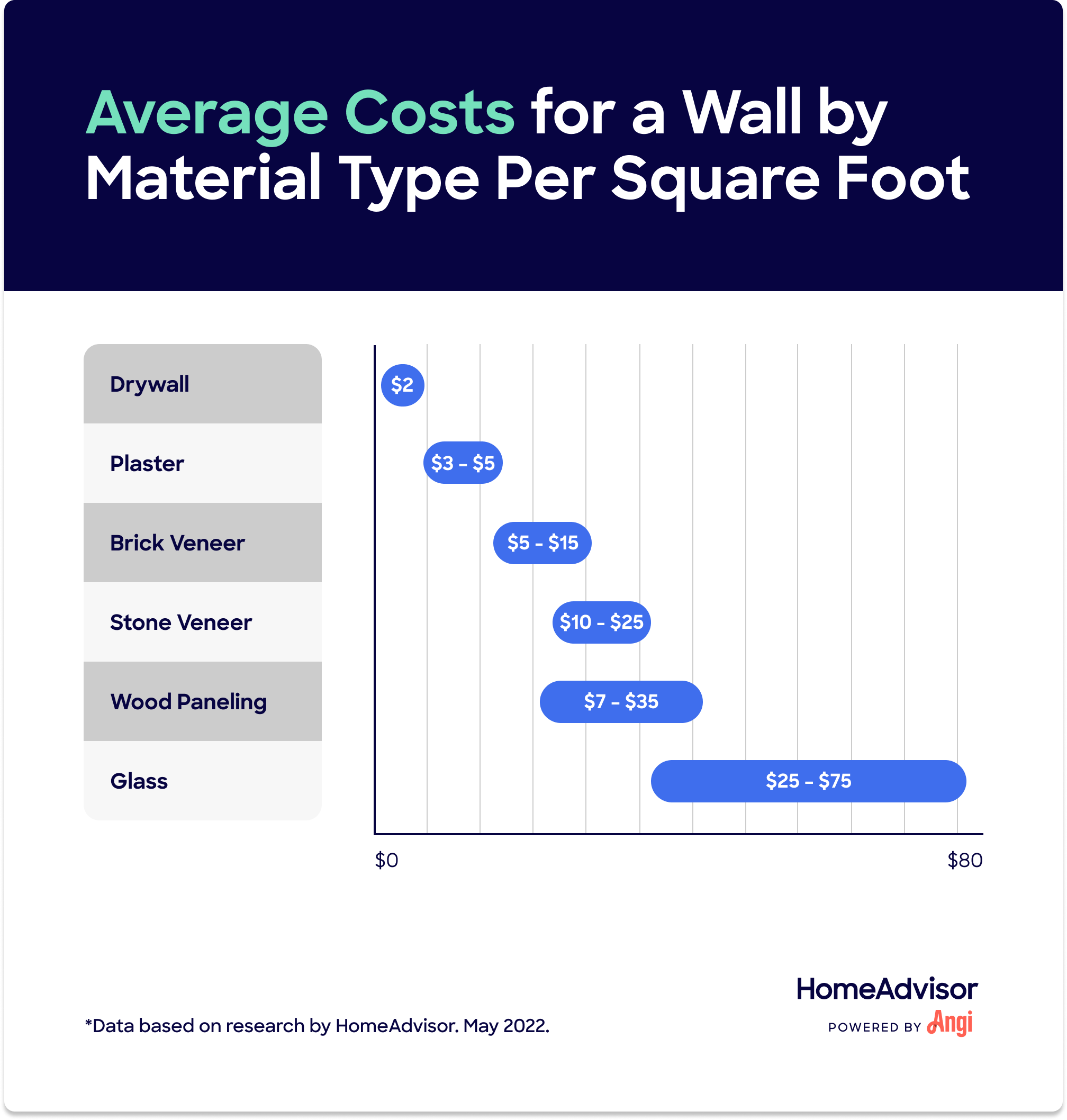
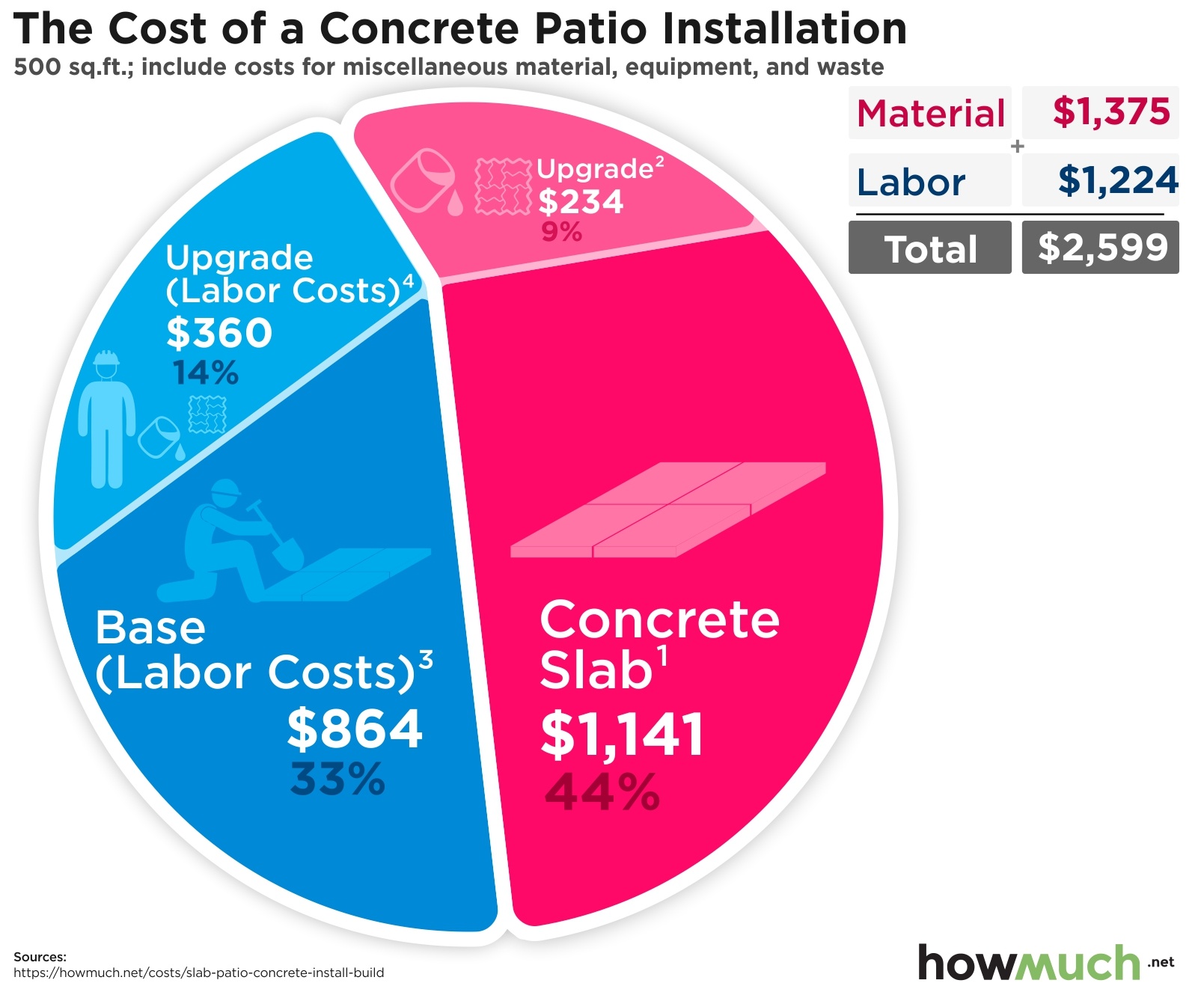

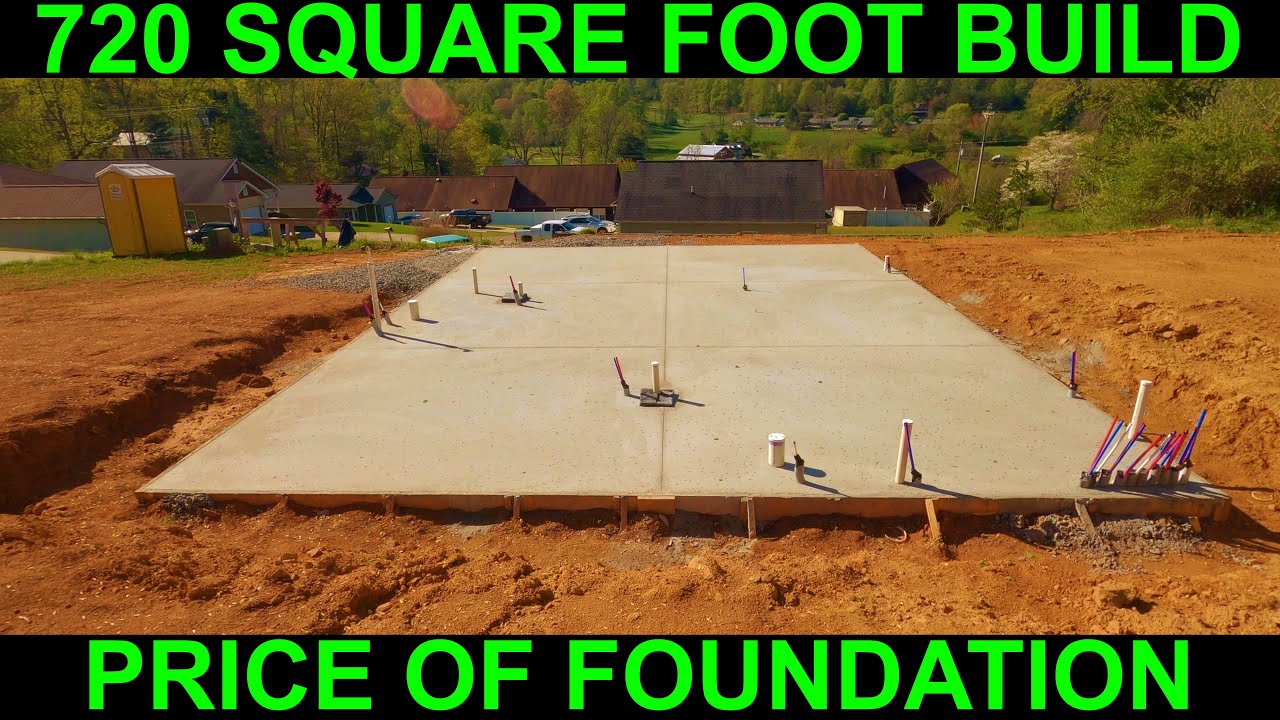
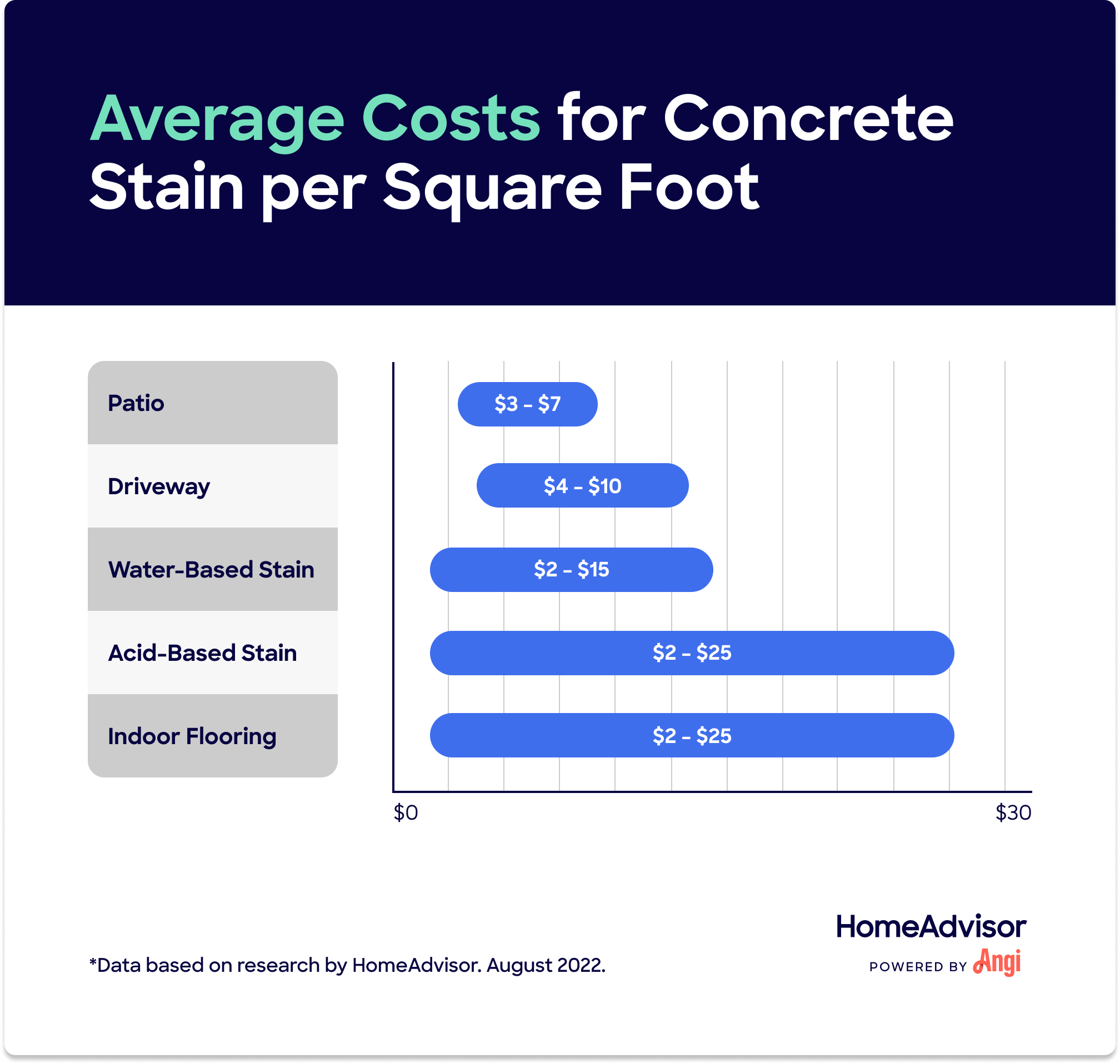
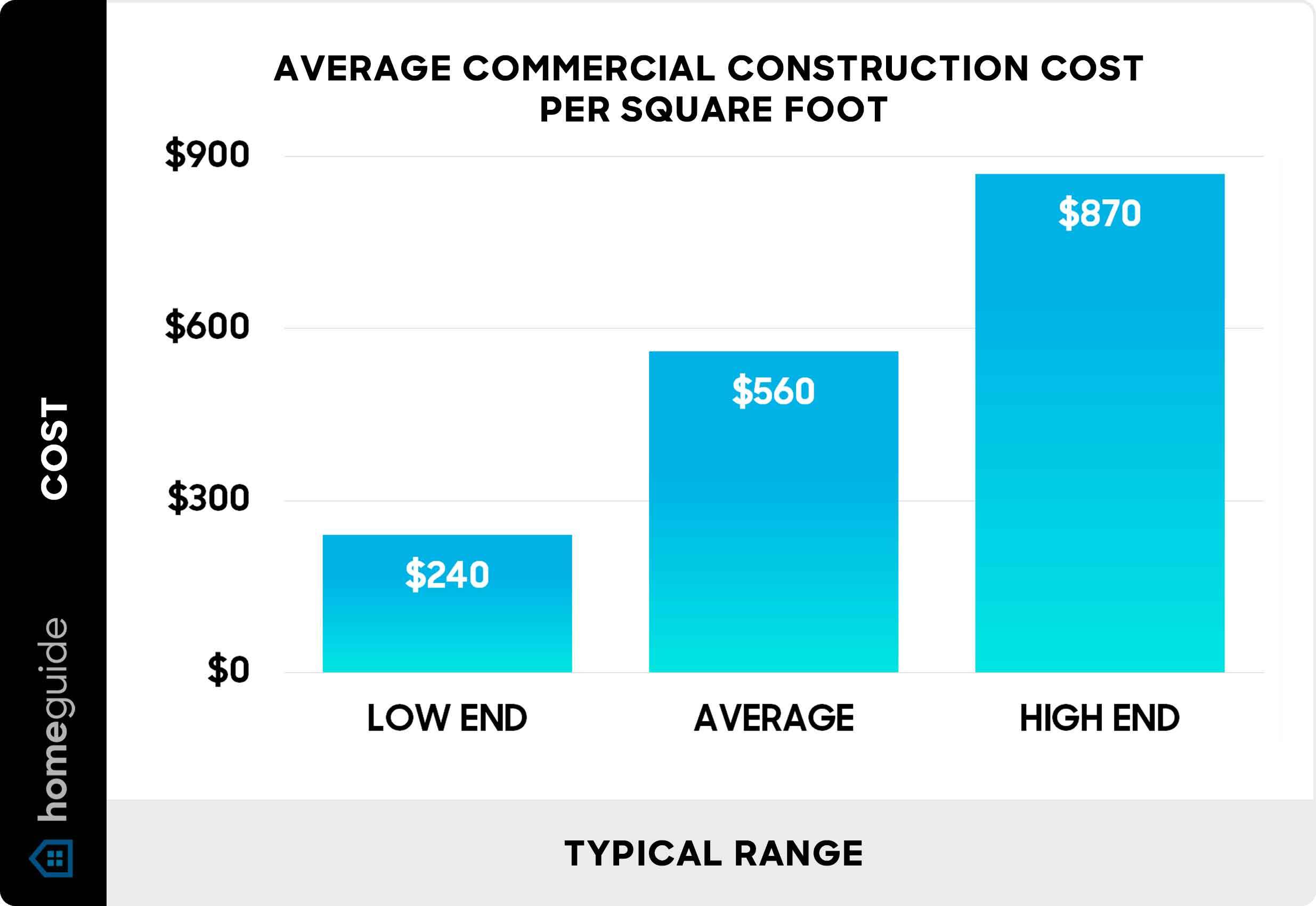
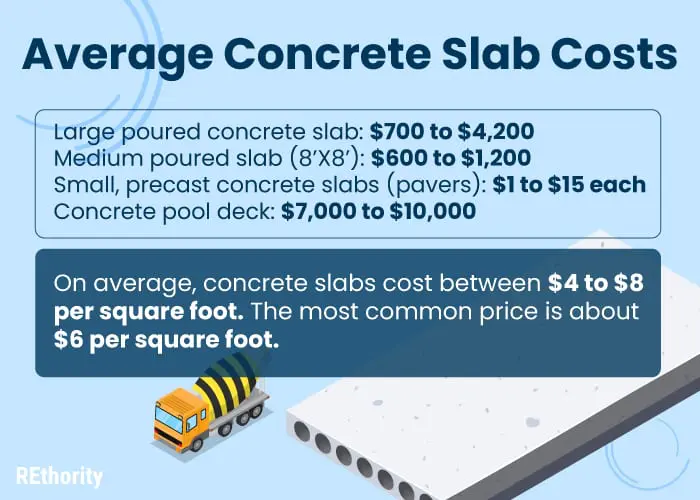
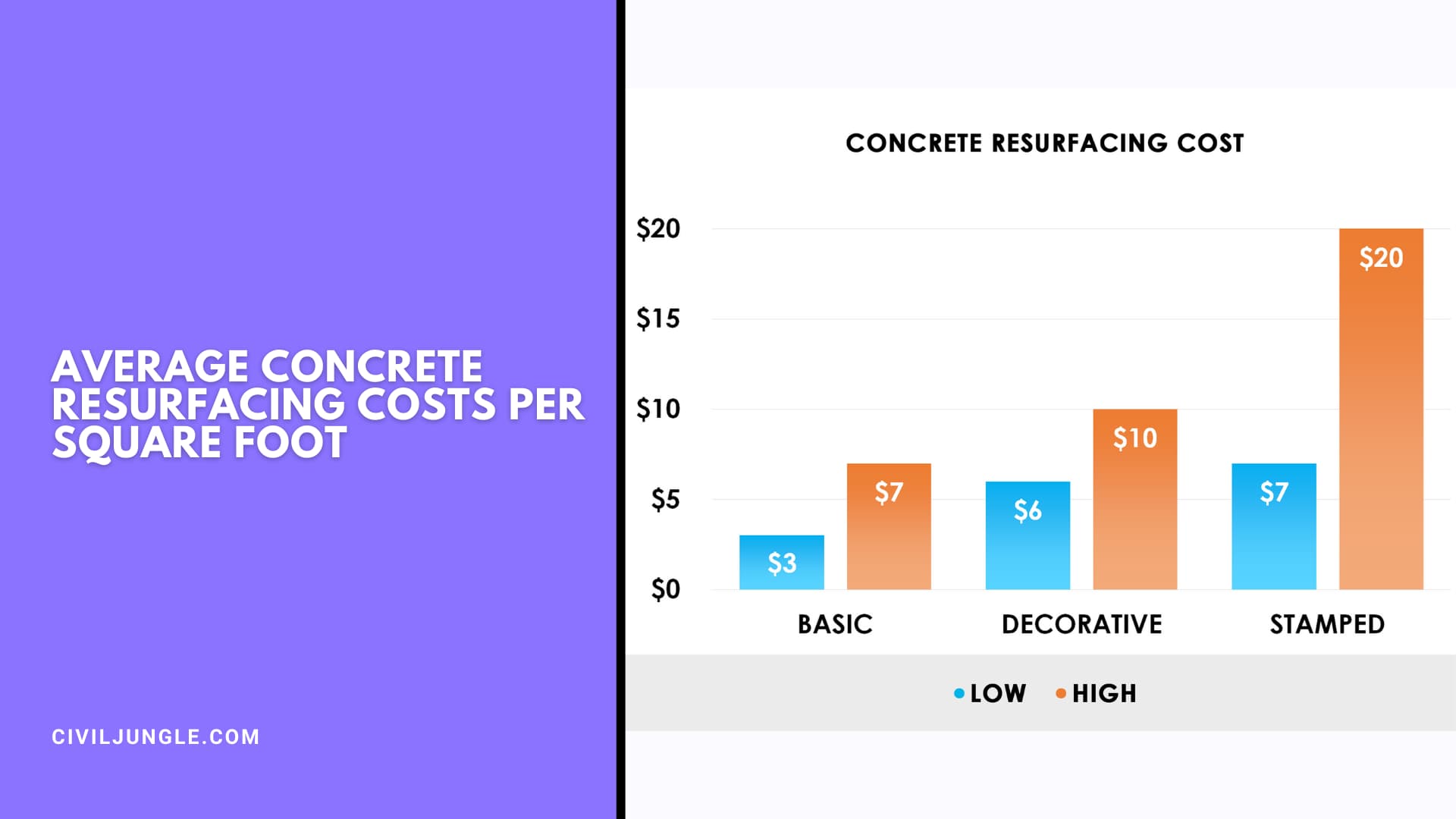
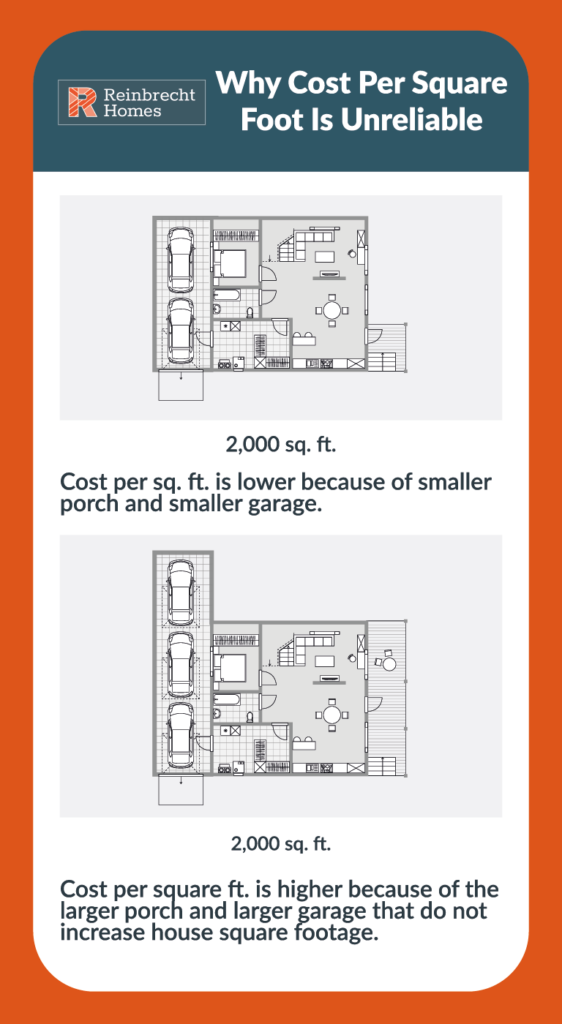
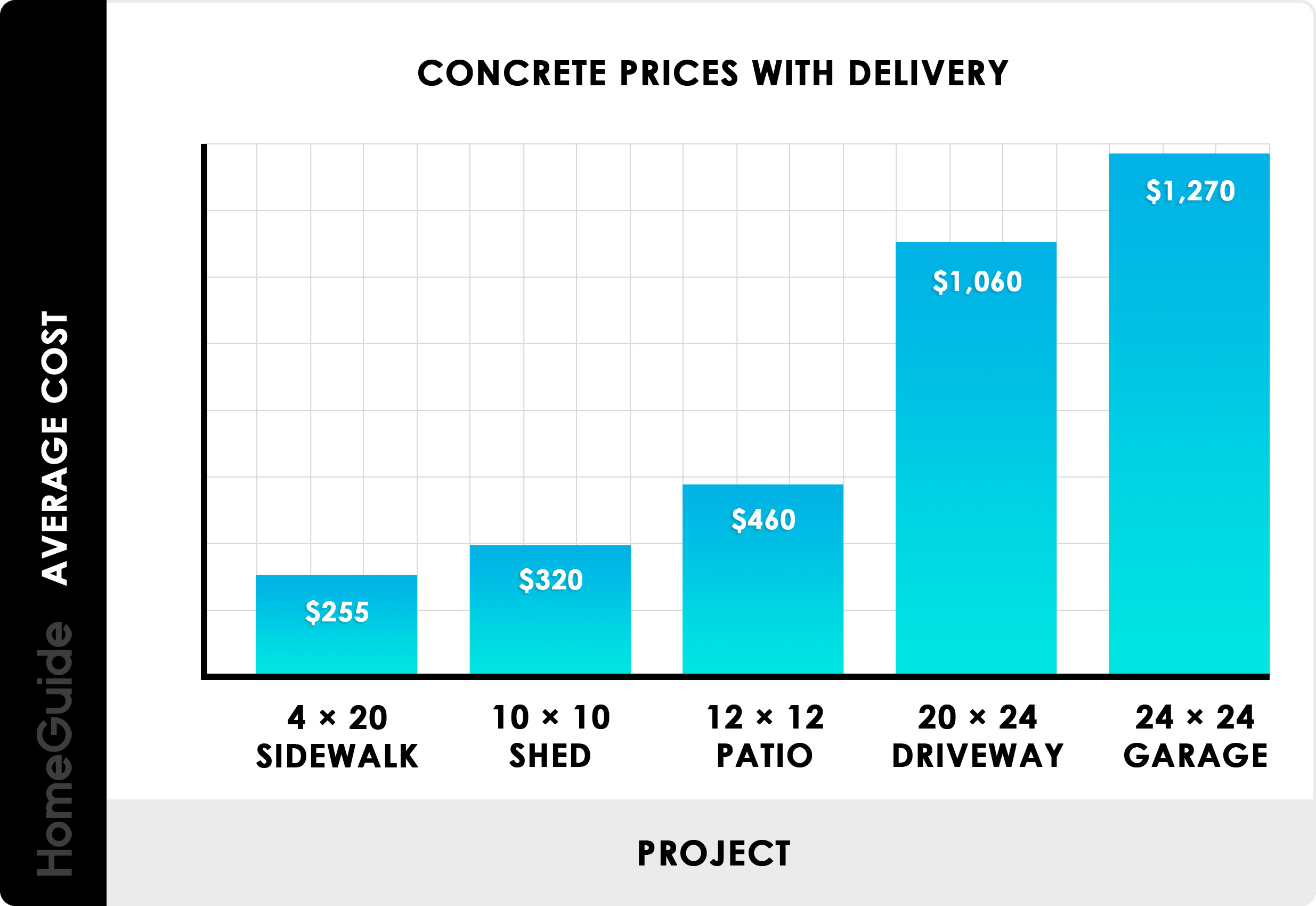


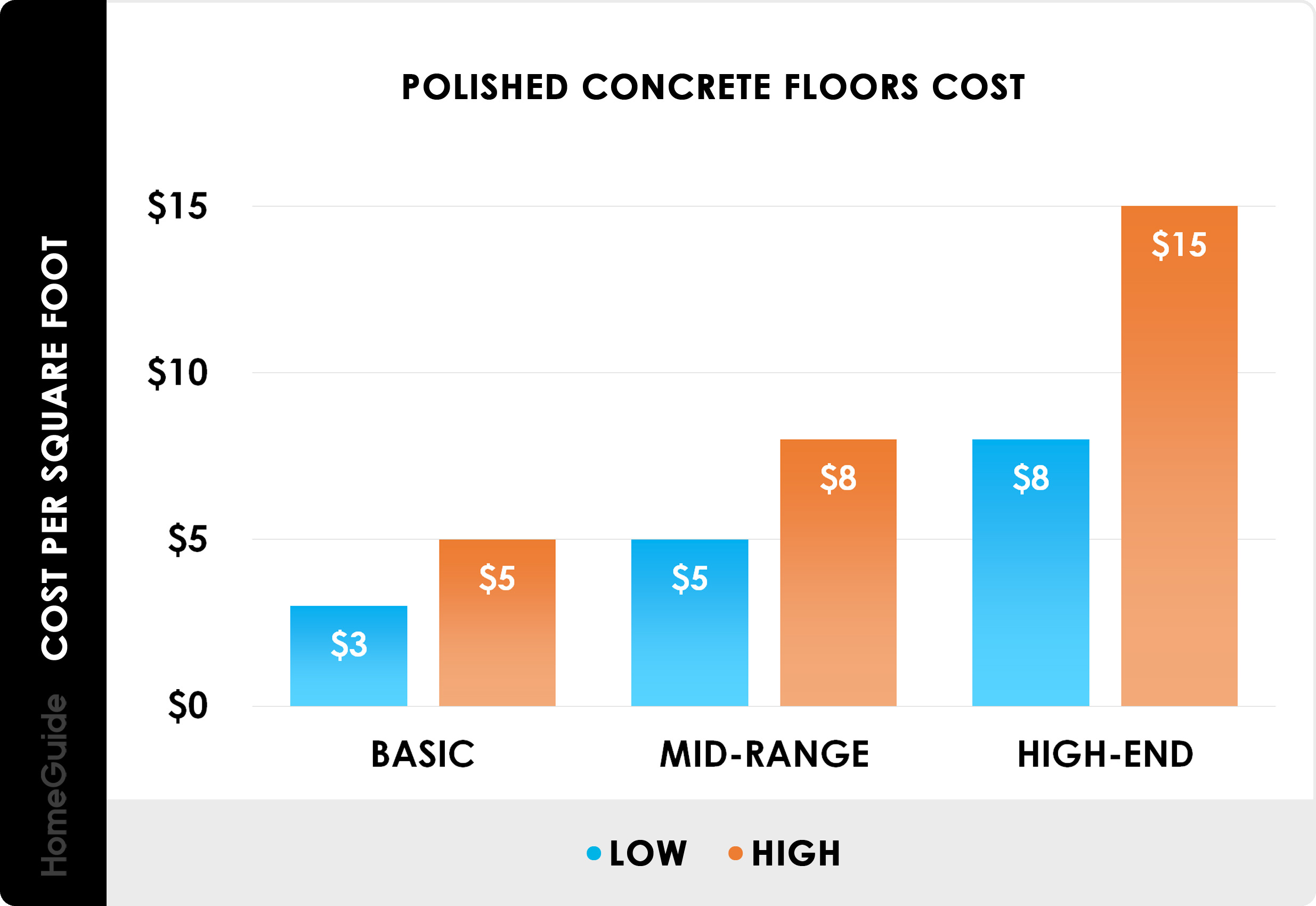
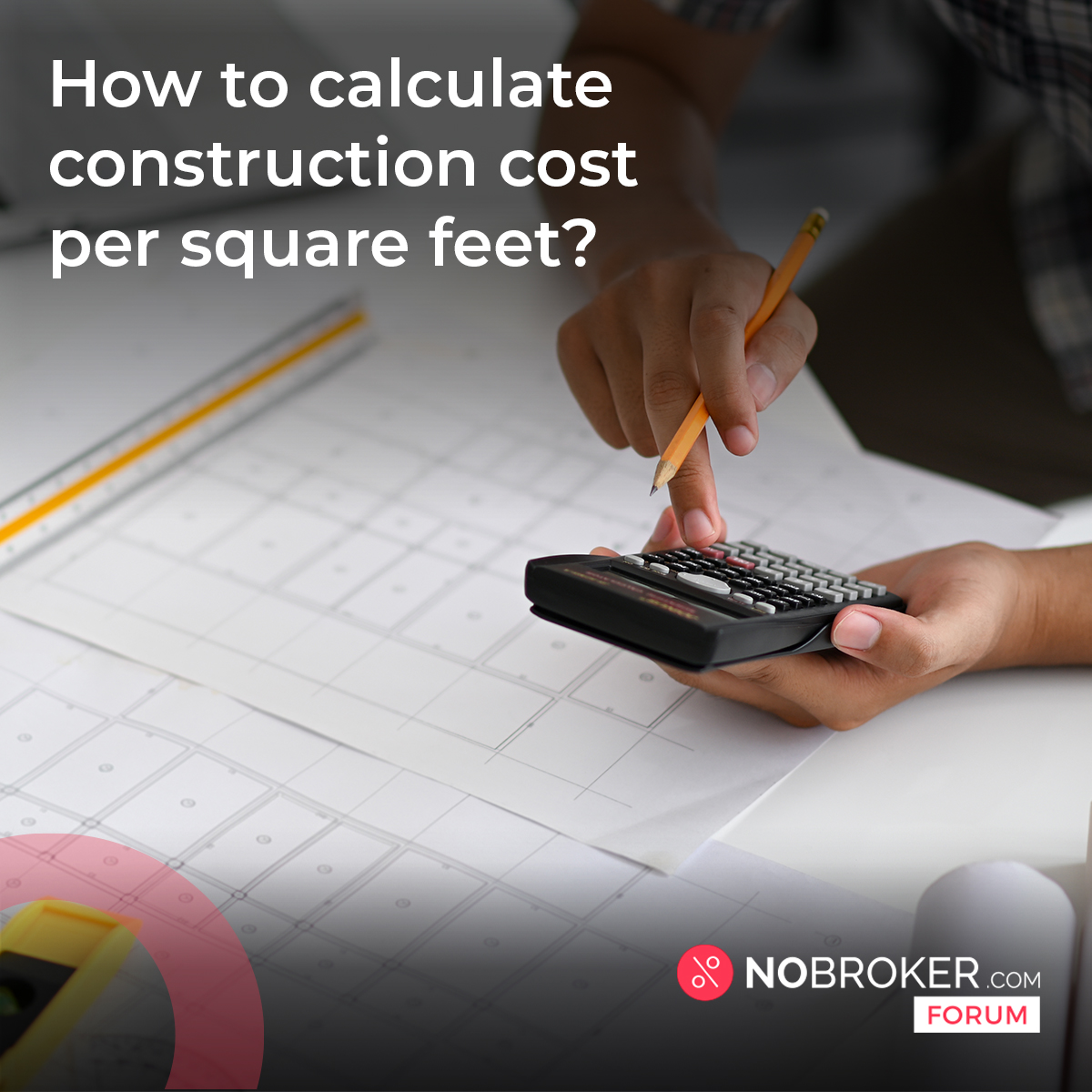
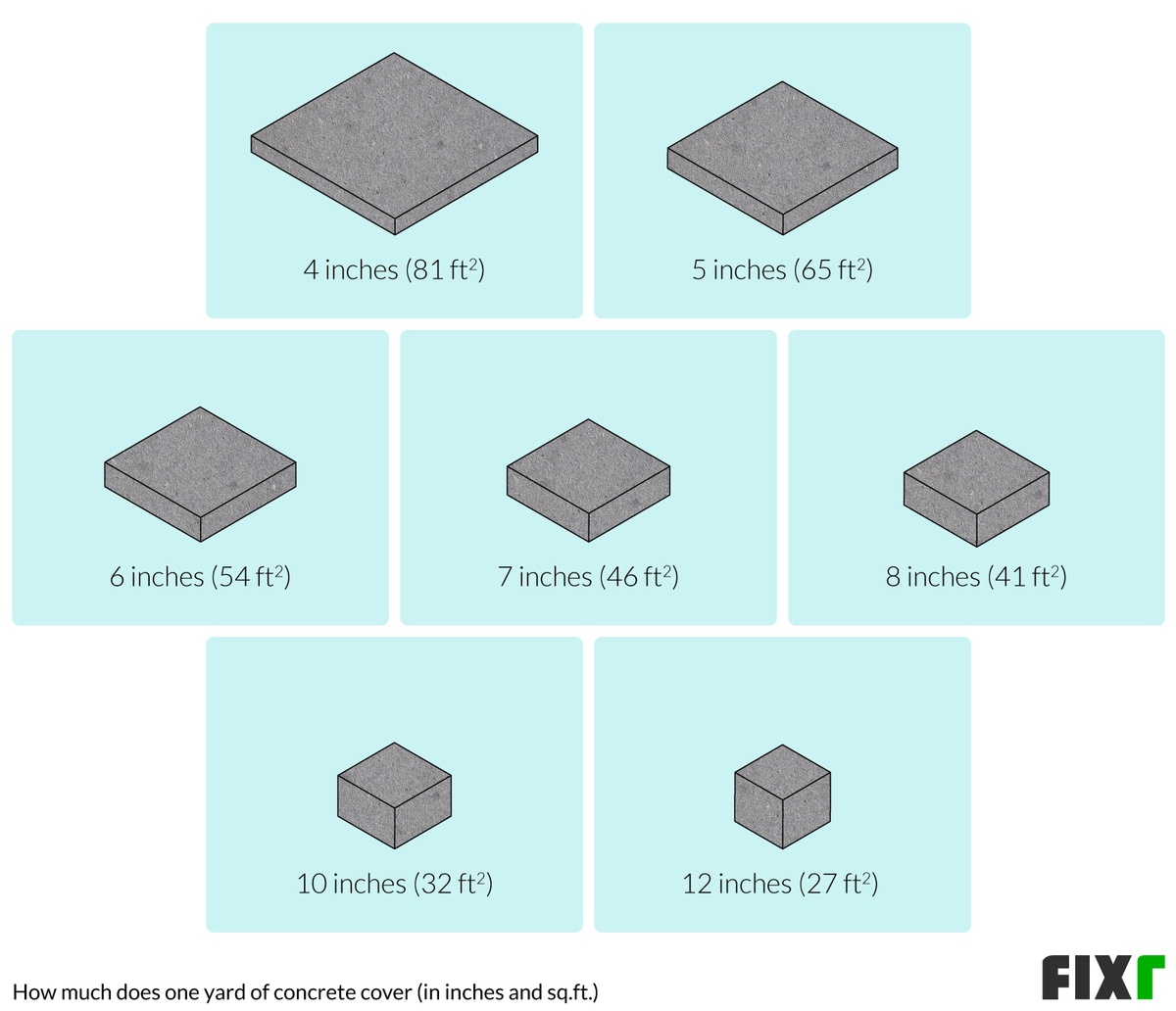