Difference Between Engineering Stress And True Stress

The collapse of a bridge, the failure of an aircraft wing, or the rupture of a pipeline – all underscore the critical importance of understanding material behavior under stress. While engineers meticulously design structures and components, the accuracy of their calculations hinges on choosing the right measure of stress.
A seemingly subtle but crucial distinction exists between two fundamental concepts: engineering stress and true stress. Ignoring this difference, especially at high levels of deformation, can lead to catastrophic design flaws, jeopardizing both safety and structural integrity.
The Nut Graf: Unpacking the Core Difference
This article will delve into the contrasting definitions of engineering stress and true stress. We'll explore how they are calculated, how they diverge under tensile loading, and why true stress provides a more accurate representation of material behavior, particularly when dealing with significant plastic deformation. Finally, we'll examine the practical implications of using one over the other in various engineering applications.
Engineering Stress: A Simple, Yet Imperfect, Metric
Engineering stress, also known as nominal stress, is defined as the applied force divided by the original cross-sectional area of the material. It's a straightforward calculation: σe = F/A0, where σe is the engineering stress, F is the applied force, and A0 is the original cross-sectional area. This simplicity makes it a convenient metric for many routine engineering calculations.
However, engineering stress assumes that the cross-sectional area remains constant throughout the deformation process. This assumption holds reasonably well for small deformations, but it breaks down as the material undergoes significant plastic deformation, especially during tensile testing.
In essence, engineering stress provides an underestimation of the actual stress experienced by the material at the point of necking or fracture.
True Stress: A More Accurate Representation of Reality
True stress, on the other hand, considers the instantaneous cross-sectional area of the material. As the material is stretched, its cross-sectional area decreases, and true stress accounts for this change. The formula for true stress is: σt = F/Ai, where σt is the true stress, F is the applied force, and Ai is the instantaneous cross-sectional area.
This measurement provides a more realistic picture of the stress state within the material. True stress reflects the actual load being borne by the diminishing cross-section, offering a more accurate depiction of the material's resistance to deformation.
Consequently, true stress is always higher than engineering stress after the onset of necking in a tensile test.
Tensile Testing: A Case Study in Divergence
The difference between engineering stress and true stress becomes particularly evident during a tensile test. Initially, the engineering stress-strain curve and the true stress-strain curve are nearly identical.
However, once the material reaches its ultimate tensile strength (UTS) and necking begins, the engineering stress starts to decrease. This decrease happens even though the material is still requiring an increasing amount of force to elongate.
Conversely, the true stress continues to rise, accurately reflecting the increasing force concentrated on the shrinking cross-sectional area at the neck.
Necking: The Point of No Return
Necking is a localized deformation that occurs in ductile materials under tensile stress. It is characterized by a significant reduction in the cross-sectional area in a small region of the specimen.
The engineering stress-strain curve suggests that the material is becoming weaker after the UTS, which is misleading. The true stress-strain curve, however, shows that the material is actually becoming stronger due to strain hardening, accurately reflecting the material's increased resistance to deformation in the necked region.
Understanding this difference is vital for predicting material behavior under extreme conditions.
Applications and Implications
The choice between using engineering stress and true stress depends on the specific application. For designs involving small deformations, engineering stress is often sufficient and computationally simpler.
However, in situations involving large plastic deformations, such as metal forming processes (e.g., forging, rolling, extrusion) or failure analysis, using true stress is crucial for accurate modeling and prediction. Ignoring the distinction in these cases can lead to inaccurate predictions of material behavior and potentially catastrophic failures.
Software used for finite element analysis (FEA) often incorporates true stress-strain relationships for accurate simulations of material behavior under complex loading conditions.
The Importance of Material Models
Accurate material models are essential for engineering calculations. These models describe the relationship between stress and strain for a given material.
While simple linear elastic models may be sufficient for some applications, more complex models that incorporate true stress and strain are needed for situations involving large plastic deformations. These advanced models, often calibrated using experimental data, are capable of capturing the non-linear behavior of materials and predicting their response under a wide range of loading conditions.
Researchers continually refine these models to improve their accuracy and predictive capabilities, driving advancements in material science and engineering.
Moving Forward: A Call for Precision
The distinction between engineering stress and true stress is more than just a theoretical exercise. It's a fundamental concept with profound implications for engineering design and safety.
As materials science advances and engineers tackle increasingly complex challenges, a thorough understanding of true stress and its accurate incorporation into material models becomes even more critical. By embracing a more precise understanding of material behavior, engineers can design safer, more durable, and more reliable structures and components.
Ignoring this nuance risks underestimating material capabilities, leading to potential failures. Ultimately, a commitment to accurate material characterization and modeling is a commitment to the safety and integrity of the engineered world around us.
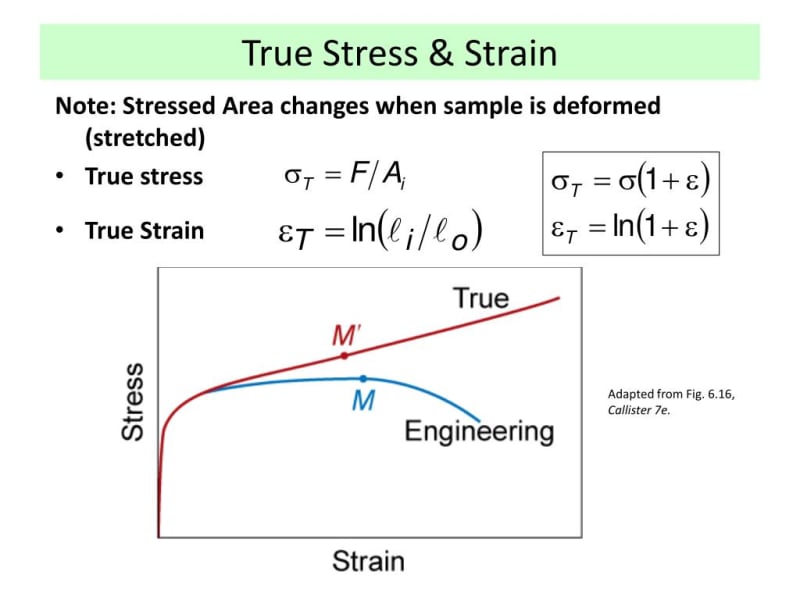
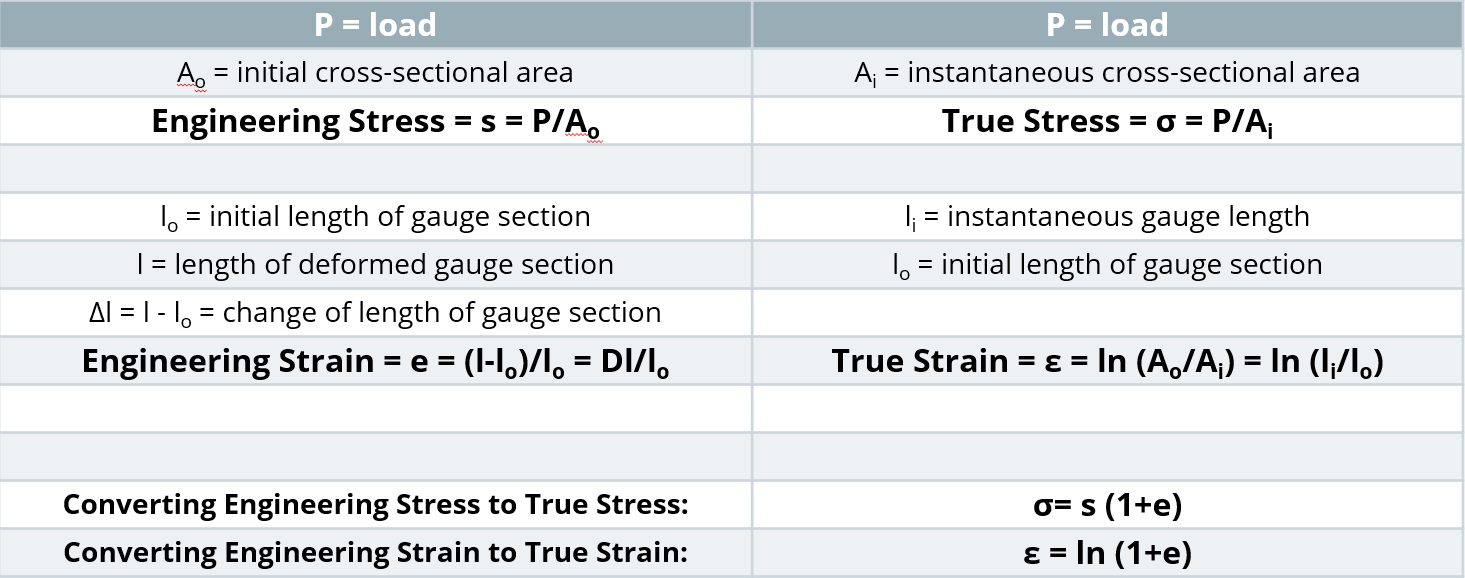
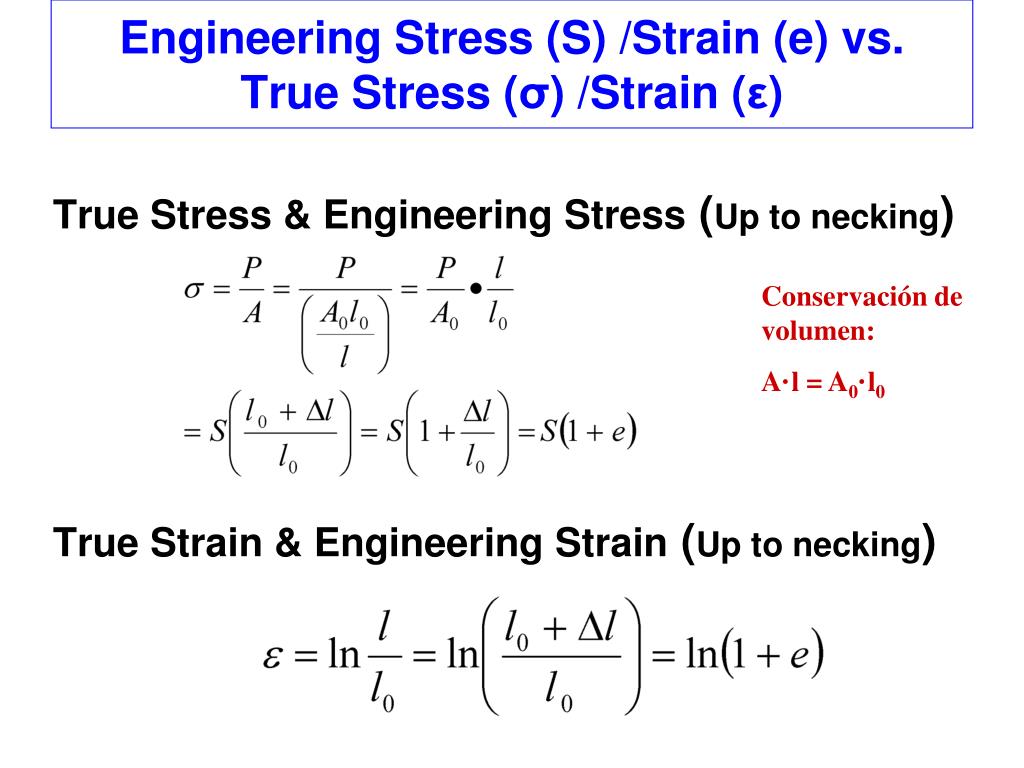

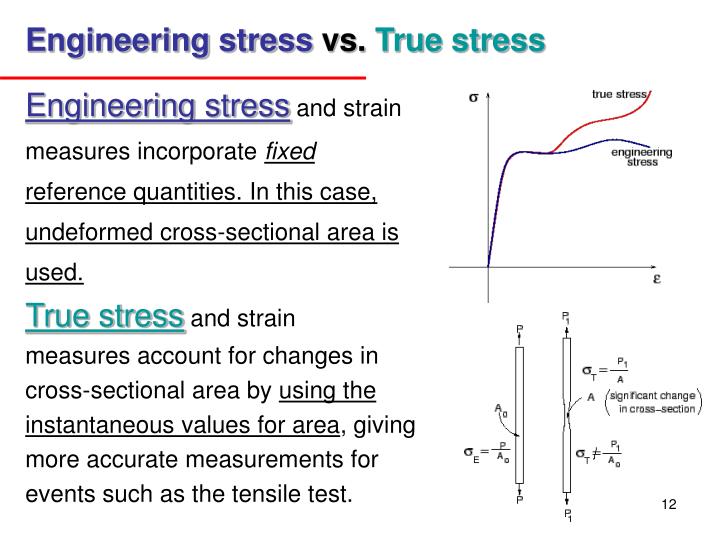

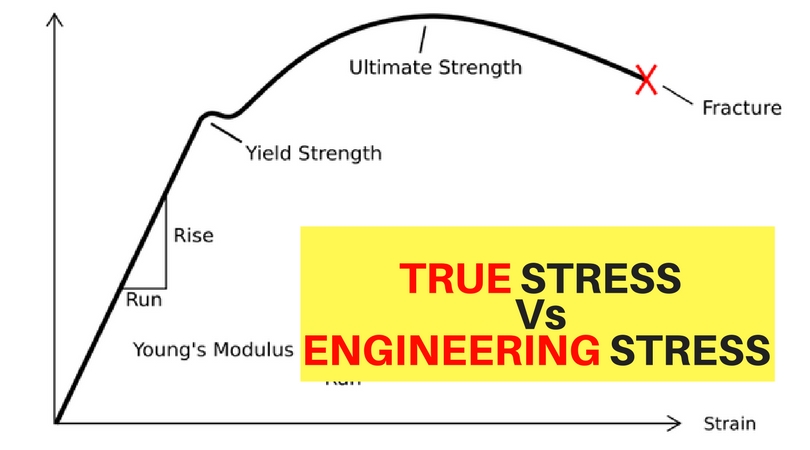


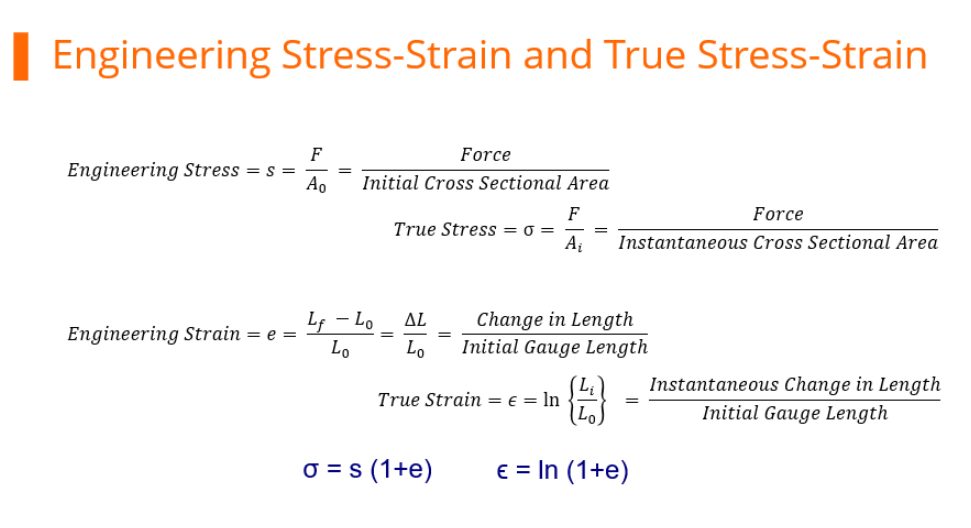


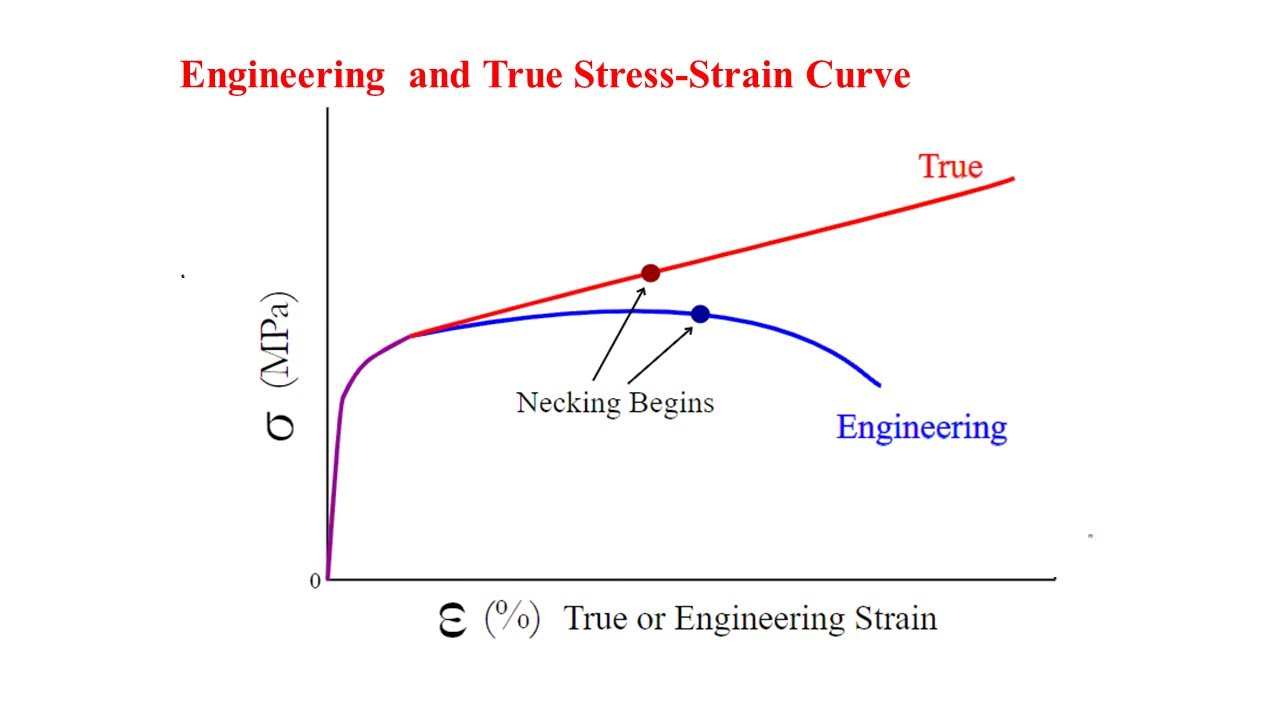

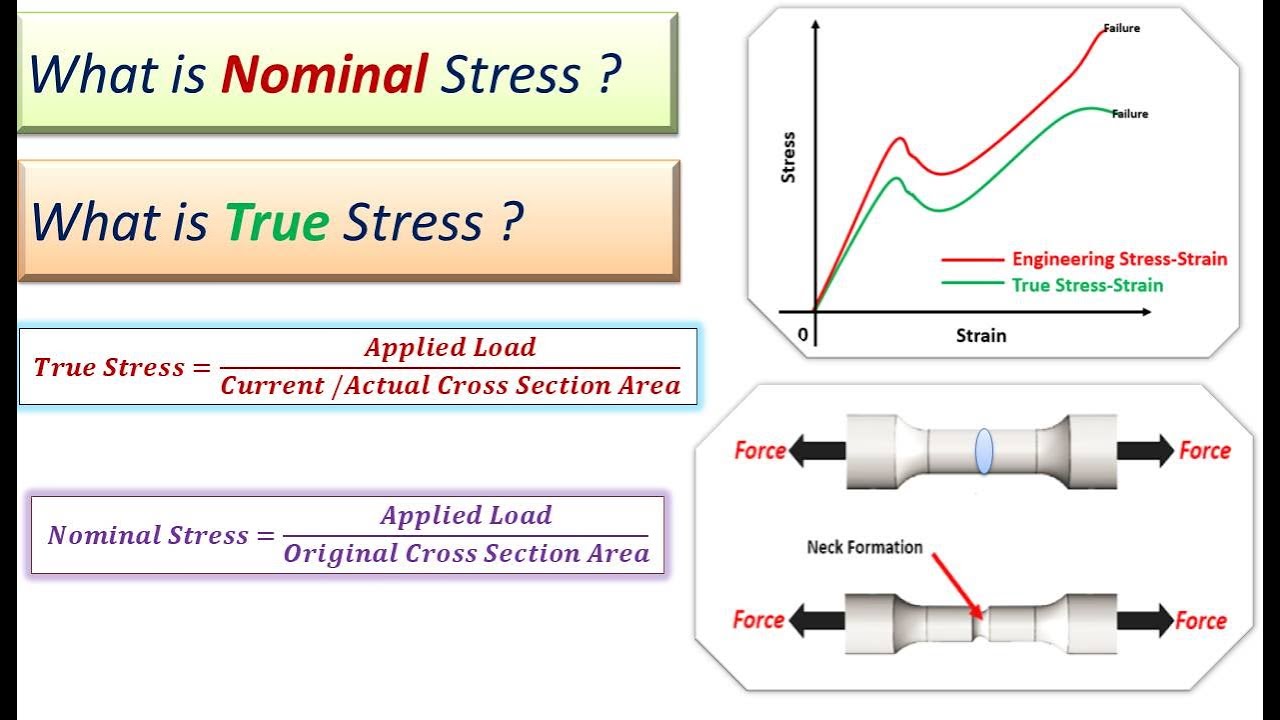
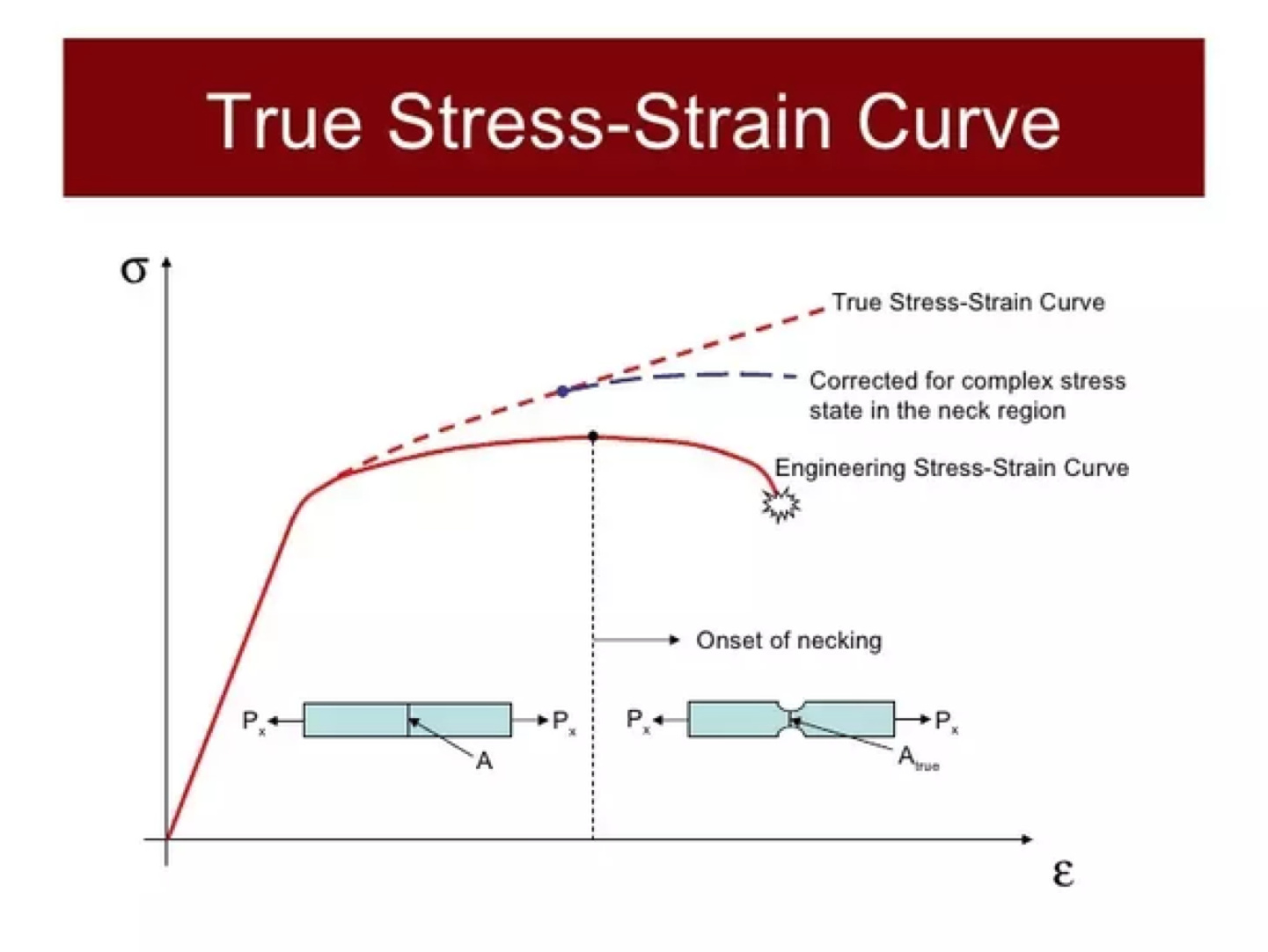
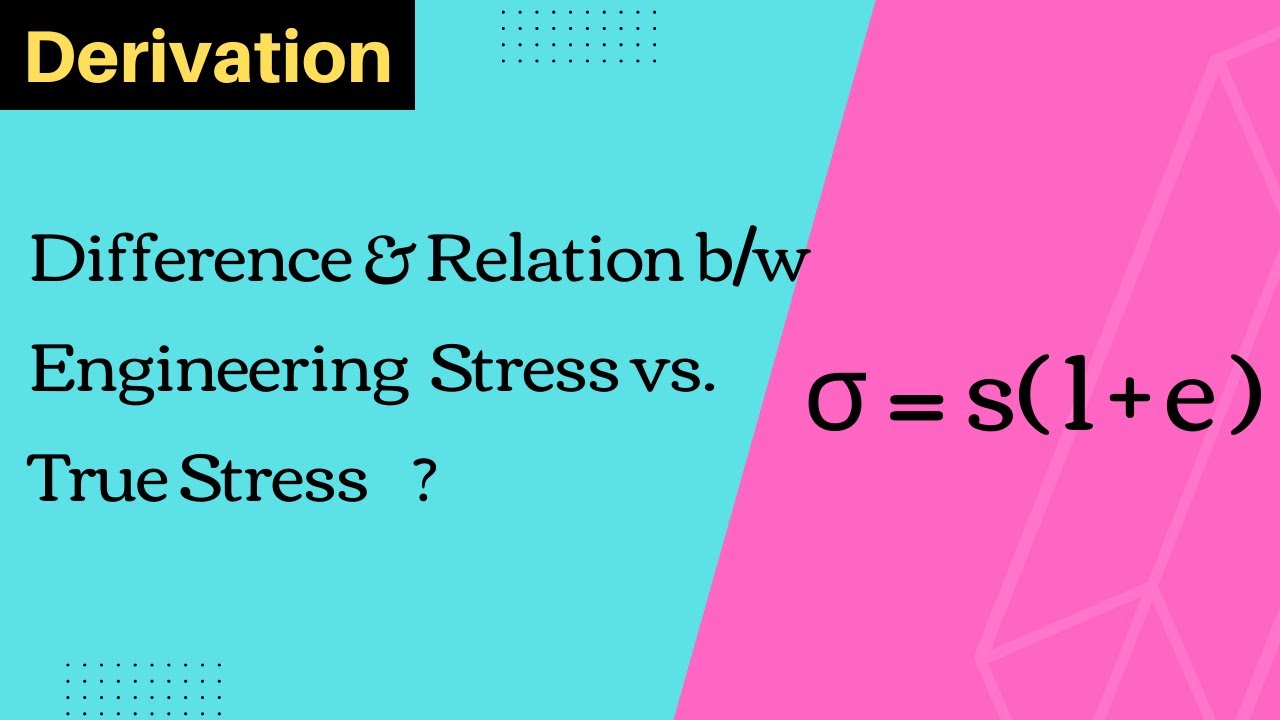
