Quality Of Construction Q4 Vs Q3
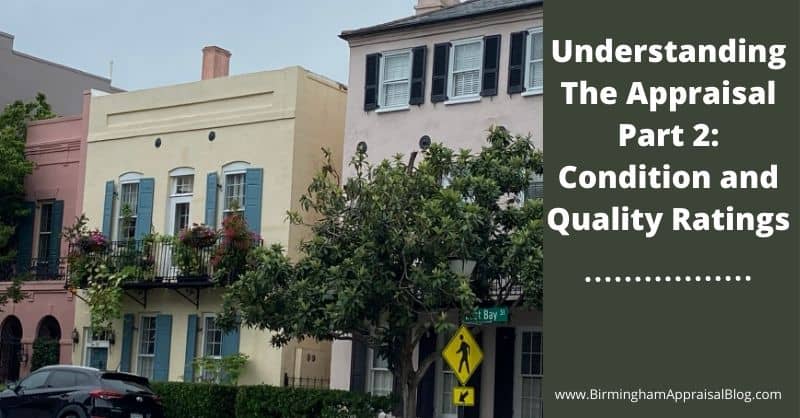
The construction industry, a cornerstone of economic activity, is facing heightened scrutiny as concerns mount over the quality of work being delivered. Recent data comparing the fourth quarter (Q4) of [Year] to the third quarter (Q3) of [Year] reveals a worrying trend: a noticeable dip in construction quality across several key metrics. This decline has triggered alarm bells among industry experts, policymakers, and consumers alike, prompting calls for immediate action to address the root causes and mitigate potential long-term consequences.
This article delves into the specifics of the observed decline in construction quality between Q3 and Q4, analyzes the factors contributing to this downturn, and explores potential solutions to restore and enhance the industry's commitment to excellence. We will examine official statements, data from reputable organizations, and expert opinions to present a comprehensive and balanced view of the current situation, its implications, and the road ahead. The stakes are high, as compromised construction quality can lead to safety hazards, increased costs, and diminished public trust in the built environment.
Deteriorating Quality Metrics: A Closer Look
Data from the [National Construction Quality Index - NCQI], a leading indicator of construction performance, shows a significant decrease in its composite score from 92.5 in Q3 to 87.1 in Q4. This drop of over 5 points represents a substantial decline, signaling widespread issues across the industry.
Specifically, the NCQI identified several areas experiencing the most pronounced degradation. These include structural integrity, materials compliance, and workmanship standards.
Reports of faulty concrete, substandard steel, and improper installations have increased significantly in Q4.
Structural Integrity Concerns
A key component of construction quality, structural integrity, saw a concerning decline. The number of reported incidents of structural defects, ranging from minor cracks to more serious foundation issues, increased by 15% between Q3 and Q4, according to data from the [American Society of Civil Engineers - ASCE].
This rise in structural problems raises serious safety concerns, potentially endangering occupants and undermining the long-term durability of buildings and infrastructure.
ASCE officials expressed their concern, stating that, "This trend is alarming and demands immediate attention to prevent catastrophic failures."
Materials Compliance Issues
Another area of significant concern is the compliance of construction materials with established standards and specifications. The [Construction Materials Testing Agency - CMTA] reported a 12% increase in instances of non-compliant materials being used in construction projects during Q4 compared to Q3.
This includes instances of using substandard concrete mixes, steel that doesn't meet strength requirements, and insulation materials with lower R-values than specified. The use of non-compliant materials can compromise the safety and performance of structures, leading to premature deterioration and increased maintenance costs.
Workmanship Standards Under Scrutiny
Beyond materials and structural integrity, workmanship standards have also come under increased scrutiny. Anecdotal evidence from site inspections and client complaints suggests a decline in the quality of craftsmanship across various trades, including masonry, plumbing, and electrical work.
Poor workmanship can lead to a variety of problems, such as leaks, electrical hazards, and aesthetic defects, impacting the functionality and value of buildings.
Root Causes of the Quality Decline
Several factors are believed to be contributing to the decline in construction quality observed in Q4. These include workforce shortages, supply chain disruptions, and increased cost pressures.
Each of these factors creates unique challenges for contractors and developers, impacting their ability to deliver high-quality projects.
Workforce Shortages
The construction industry has been grappling with a shortage of skilled workers for several years, and this issue has been exacerbated in recent months. A study by the [Associated General Contractors of America - AGC] found that 83% of construction firms reported difficulty finding qualified workers in Q4.
This shortage has forced contractors to rely on less experienced or less skilled labor, leading to increased errors and lower quality workmanship.
The AGC report stated, "The skilled labor shortage is the single biggest threat to the construction industry's ability to meet demand and maintain quality standards."
Supply Chain Disruptions
Global supply chain disruptions, stemming from factors such as the COVID-19 pandemic and geopolitical instability, have significantly impacted the availability and cost of construction materials. Delays in material deliveries can disrupt project schedules and force contractors to use alternative materials, potentially compromising quality.
Furthermore, increased material costs can incentivize contractors to cut corners in other areas, such as labor or quality control, to stay within budget.
The [Construction Industry Research and Information Association - CIRIA] has highlighted the need for greater resilience in supply chains to mitigate future disruptions.
Increased Cost Pressures
Rising material costs and labor costs have put significant pressure on construction firms' profit margins. This can lead to a focus on cost-cutting measures that ultimately compromise quality.
Contractors may be tempted to use cheaper materials, reduce quality control inspections, or rush projects to minimize expenses. This pursuit of short-term cost savings can have significant long-term consequences, leading to increased maintenance costs, structural failures, and reputational damage.
Potential Solutions and the Path Forward
Addressing the decline in construction quality requires a multifaceted approach involving industry stakeholders, policymakers, and educational institutions. Possible solutions include increased investment in workforce training, strengthening supply chain resilience, and enhanced quality control measures.
These measures should be implemented in conjunction to produce a more comprehensive solution.
Investing in Workforce Training
To address the skilled labor shortage, the industry needs to invest in comprehensive training programs to attract and retain qualified workers. This includes apprenticeship programs, vocational training, and continuing education opportunities.
These programs should focus on developing both technical skills and a strong commitment to quality workmanship.
Government incentives and subsidies can play a vital role in supporting these training initiatives.
Strengthening Supply Chain Resilience
Diversifying supply chains and establishing strategic partnerships with suppliers can help mitigate the impact of disruptions. Contractors should also consider investing in inventory management systems to ensure adequate supplies of critical materials are available when needed.
Collaboration between industry stakeholders and policymakers is essential to develop more resilient supply chains.
Enhancing Quality Control Measures
Contractors need to implement robust quality control programs that include regular inspections, testing, and documentation. Independent third-party inspections can provide an objective assessment of construction quality and identify potential problems early on.
Furthermore, stricter enforcement of building codes and regulations is crucial to ensure that construction projects meet minimum quality standards.
The use of technology, such as drones and AI-powered quality control systems, can also enhance the efficiency and accuracy of inspections.
Conclusion
The observed decline in construction quality between Q3 and Q4 is a serious concern that demands immediate attention. Workforce shortages, supply chain disruptions, and increased cost pressures are all contributing factors to this decline.
Addressing these challenges requires a collaborative effort involving industry stakeholders, policymakers, and educational institutions. By investing in workforce training, strengthening supply chain resilience, and enhancing quality control measures, the construction industry can restore its commitment to excellence and ensure the delivery of safe, durable, and high-quality buildings and infrastructure. The future of the built environment depends on it.
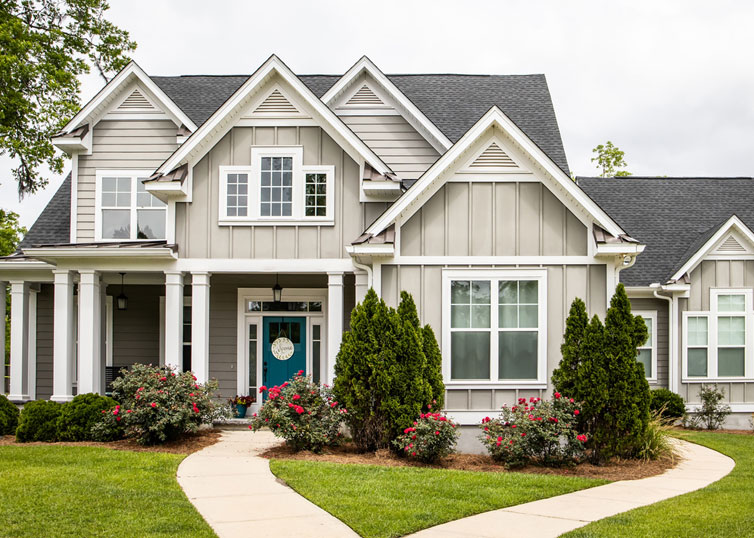

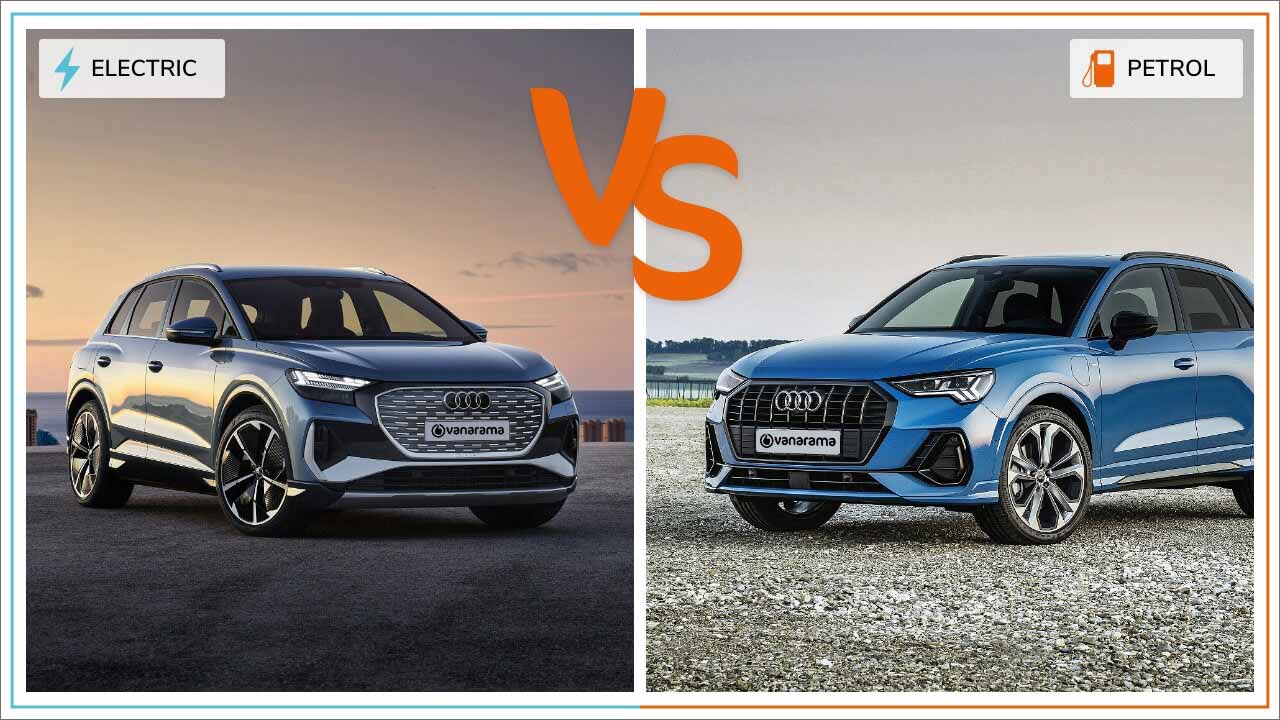




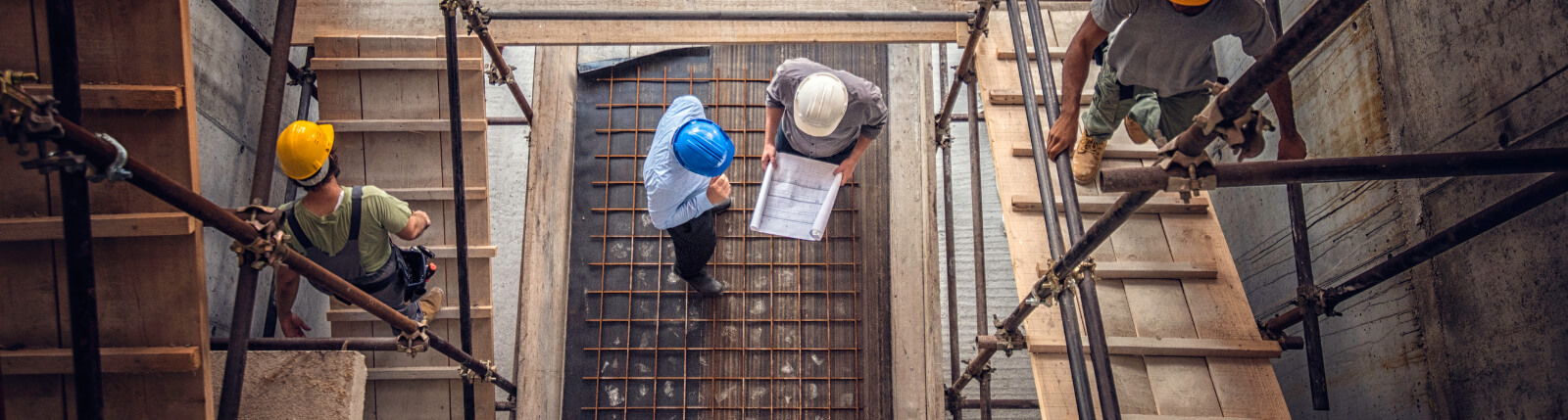

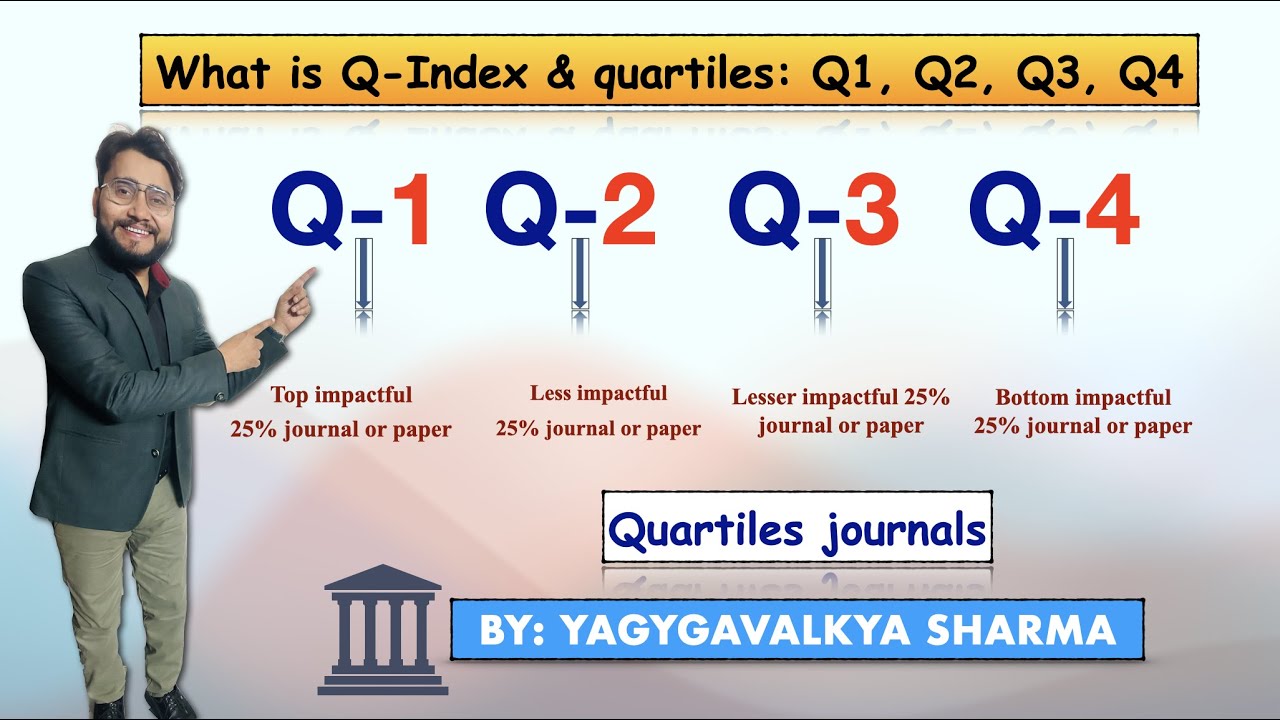



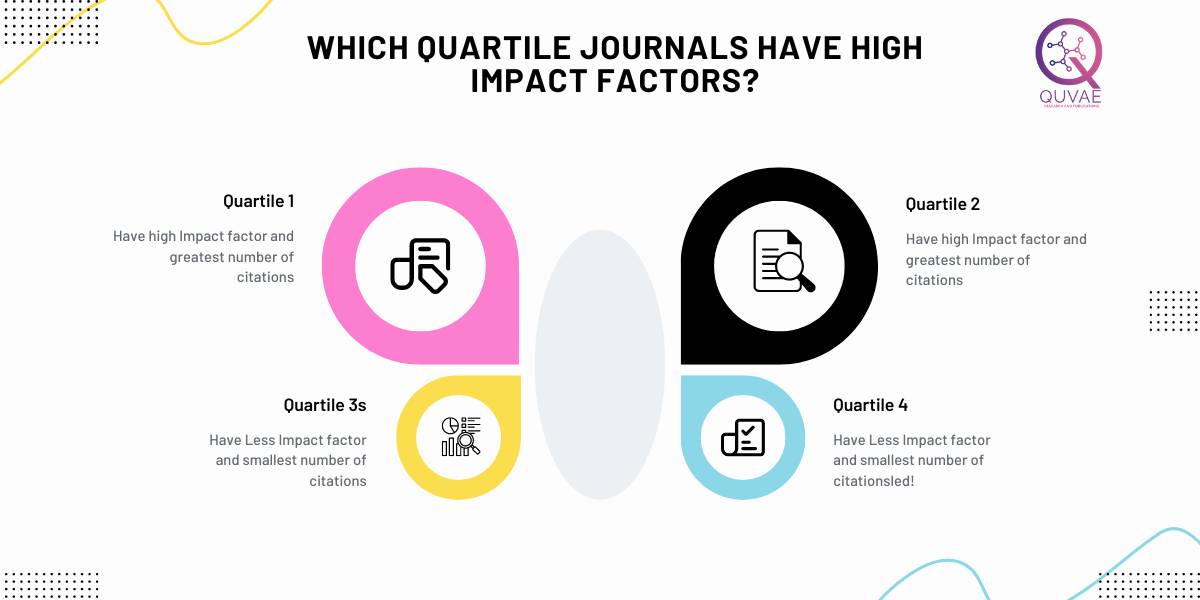
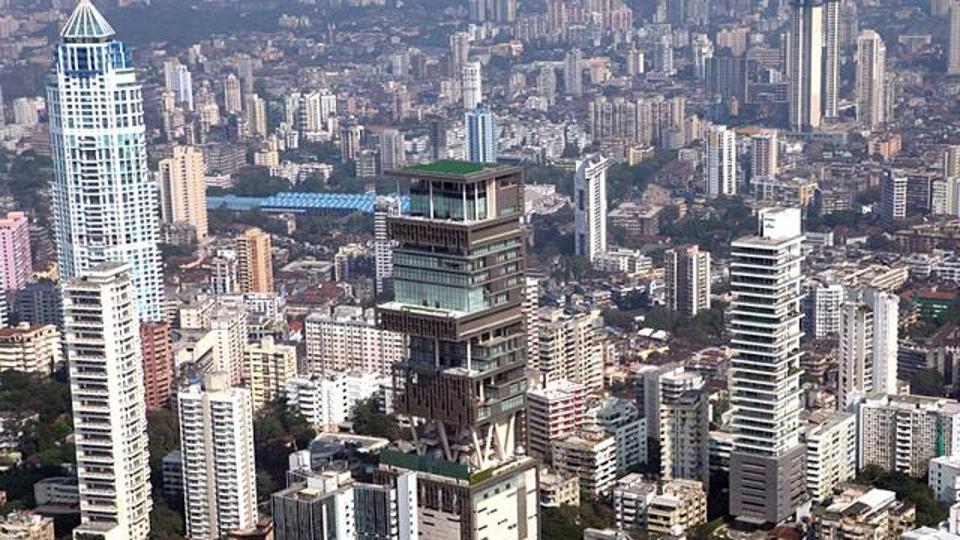
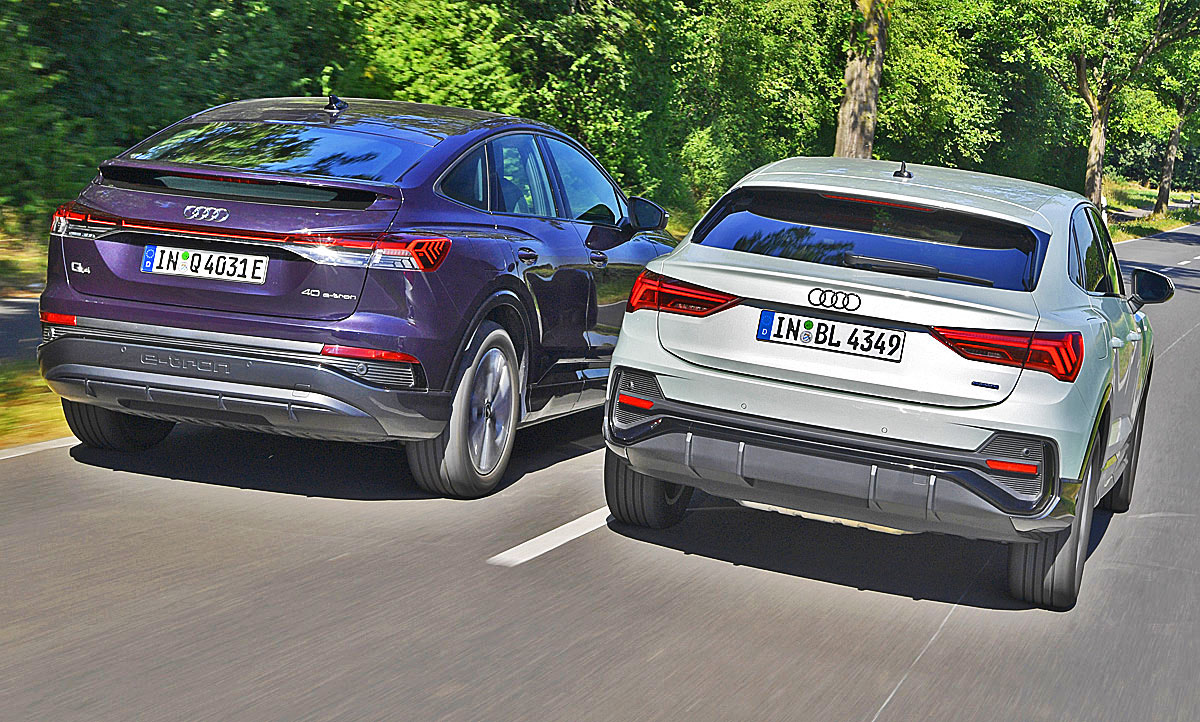

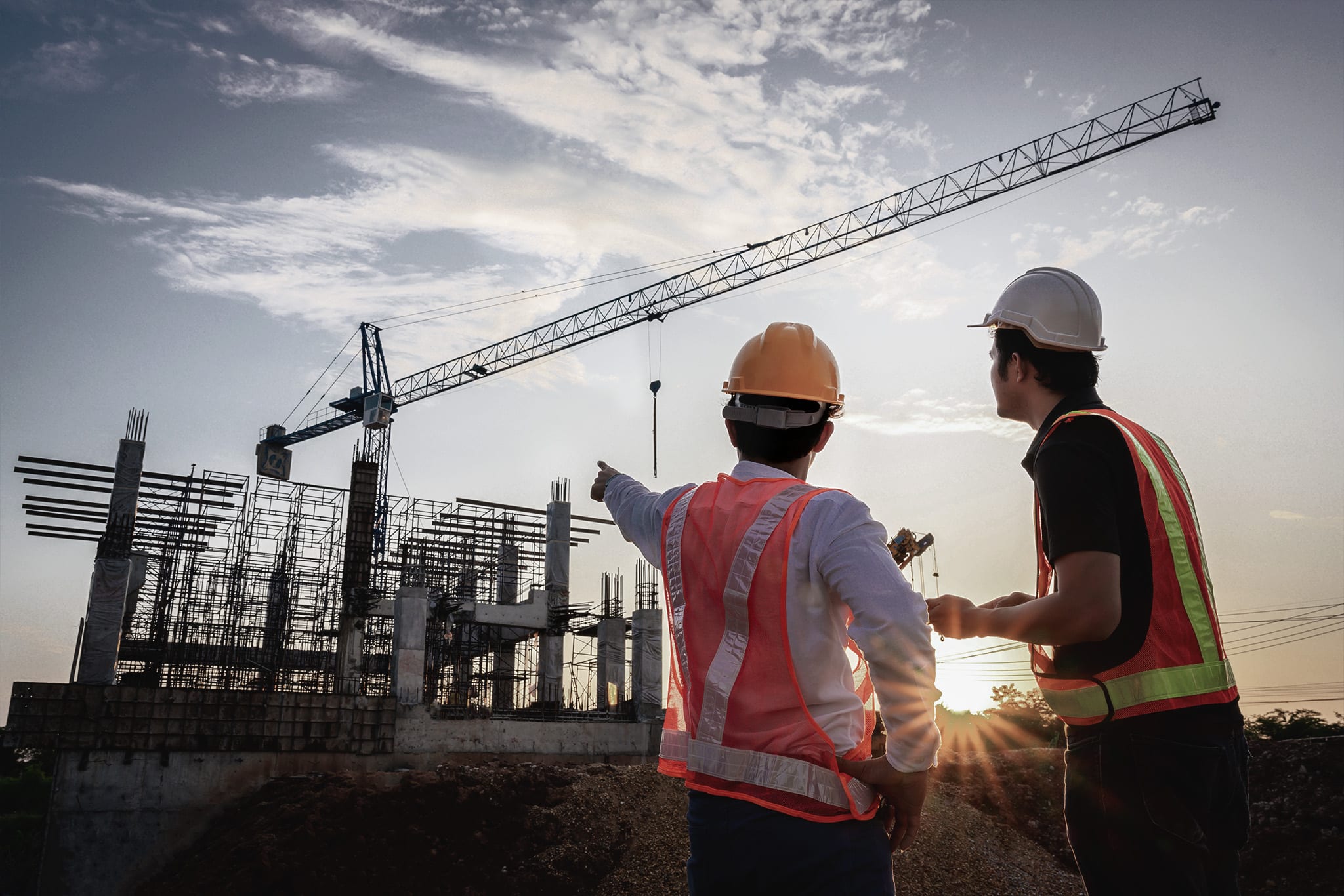