Terrapin Beer Company Shipping & Receiving
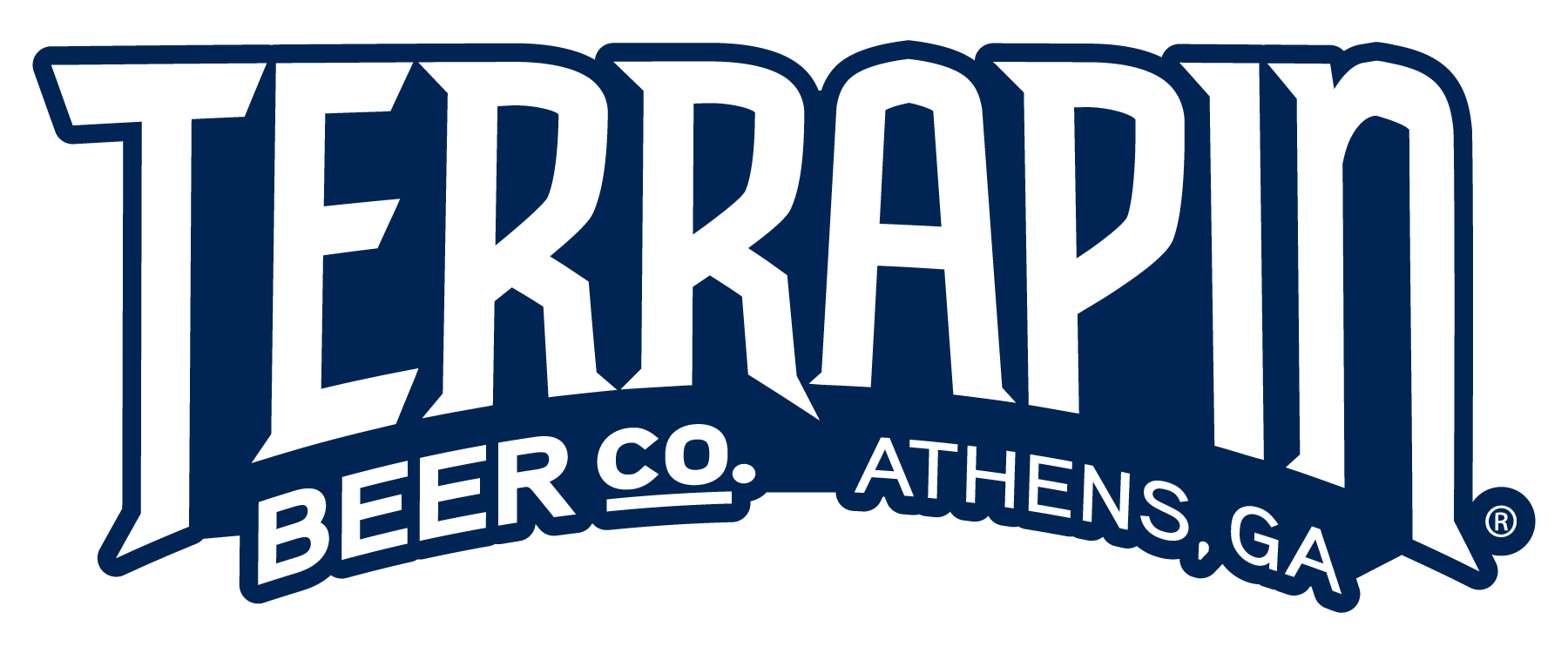
Terrapin Beer Company, a fixture of the Athens, Georgia, craft brewing scene, is streamlining its shipping and receiving operations with a series of strategic upgrades. These changes aim to improve efficiency and adapt to the evolving demands of the beer industry.
These enhancements at Terrapin come at a crucial time, as craft breweries navigate increasing competition and complex supply chain dynamics. Efficient logistics are essential for maintaining profitability and ensuring product freshness in a market where consumer expectations are constantly rising. This article will explore the details of these operational adjustments and their potential impact on Terrapin’s future.
The Evolution of Shipping and Receiving at Terrapin
Terrapin Beer Company, founded in 2002, has grown from a small operation to a significant regional player. Its shipping and receiving department plays a vital role in the brewery’s overall success.
The current upgrades focus on several key areas, including warehouse management, inventory tracking, and transportation logistics. These changes intend to modernize the entire flow of goods in and out of the brewery.
Key Upgrades and Improvements
One of the most significant improvements is the implementation of a new warehouse management system (WMS). This system allows for real-time tracking of inventory levels and automated order fulfillment, reducing the potential for errors and delays.
“The new WMS is a game-changer for us,” says Brian “Spike” Buckowski, Terrapin’s brewmaster and co-founder. “It provides us with the visibility we need to make informed decisions and optimize our processes.”
Another crucial element of the upgrade involves improved transportation logistics. Terrapin has partnered with a new carrier network to ensure timely and reliable delivery of its products to distributors and retailers across the Southeast.
The brewery has also invested in new equipment, including forklifts and palletizers, to streamline the loading and unloading of trucks. These investments reduce the physical strain on employees and accelerate the overall process.
Impact on Operations and Consumers
The modernization of shipping and receiving operations is expected to have a positive impact on Terrapin’s overall efficiency. By reducing errors and delays, the brewery can improve its order fulfillment rates and maintain stronger relationships with its distributors and retailers.
The improvements will lead to fresher beer reaching consumers more quickly. This benefits consumers who value the quality and freshness of craft beer.
Furthermore, the increased efficiency could lead to cost savings for Terrapin, which could potentially translate into more competitive pricing for consumers. However, the brewery has not commented on potential price adjustments.
Sustainability Initiatives
Terrapin is also committed to incorporating sustainable practices into its shipping and receiving operations. The brewery has implemented a recycling program for packaging materials and is exploring the use of alternative fuels for its delivery trucks.
“Sustainability is a core value at Terrapin,” says a company spokesperson. “We are always looking for ways to reduce our environmental impact and operate more responsibly.”
The brewery is also exploring the possibility of using reusable pallets and containers to reduce waste. These initiatives align with the broader trend of sustainability in the craft brewing industry.
Challenges and Opportunities
Despite the potential benefits, implementing these changes also presents challenges. Training employees on the new WMS and integrating it with existing systems requires careful planning and execution.
The brewery must also manage the transition effectively to minimize disruption to its existing operations. However, Terrapin is confident that it can overcome these challenges and realize the full potential of the upgrades.
The investment in shipping and receiving modernization positions Terrapin Beer Company for continued success in the competitive craft beer market. By improving efficiency and sustainability, the brewery can strengthen its brand and build lasting relationships with its customers.
This strategic move reflects a broader trend within the craft brewing industry, where operational excellence is becoming increasingly important. Breweries that can efficiently manage their supply chains and deliver fresh, high-quality products are best positioned to thrive in the years to come.
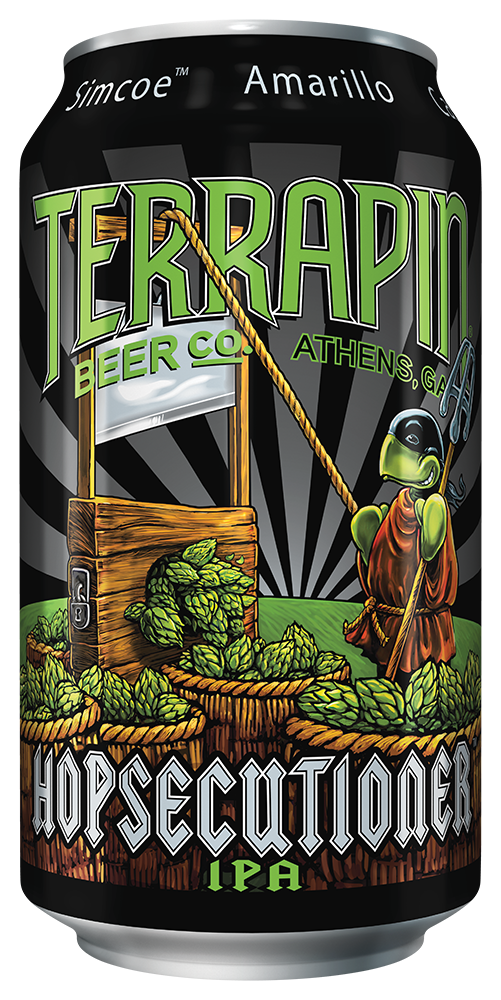

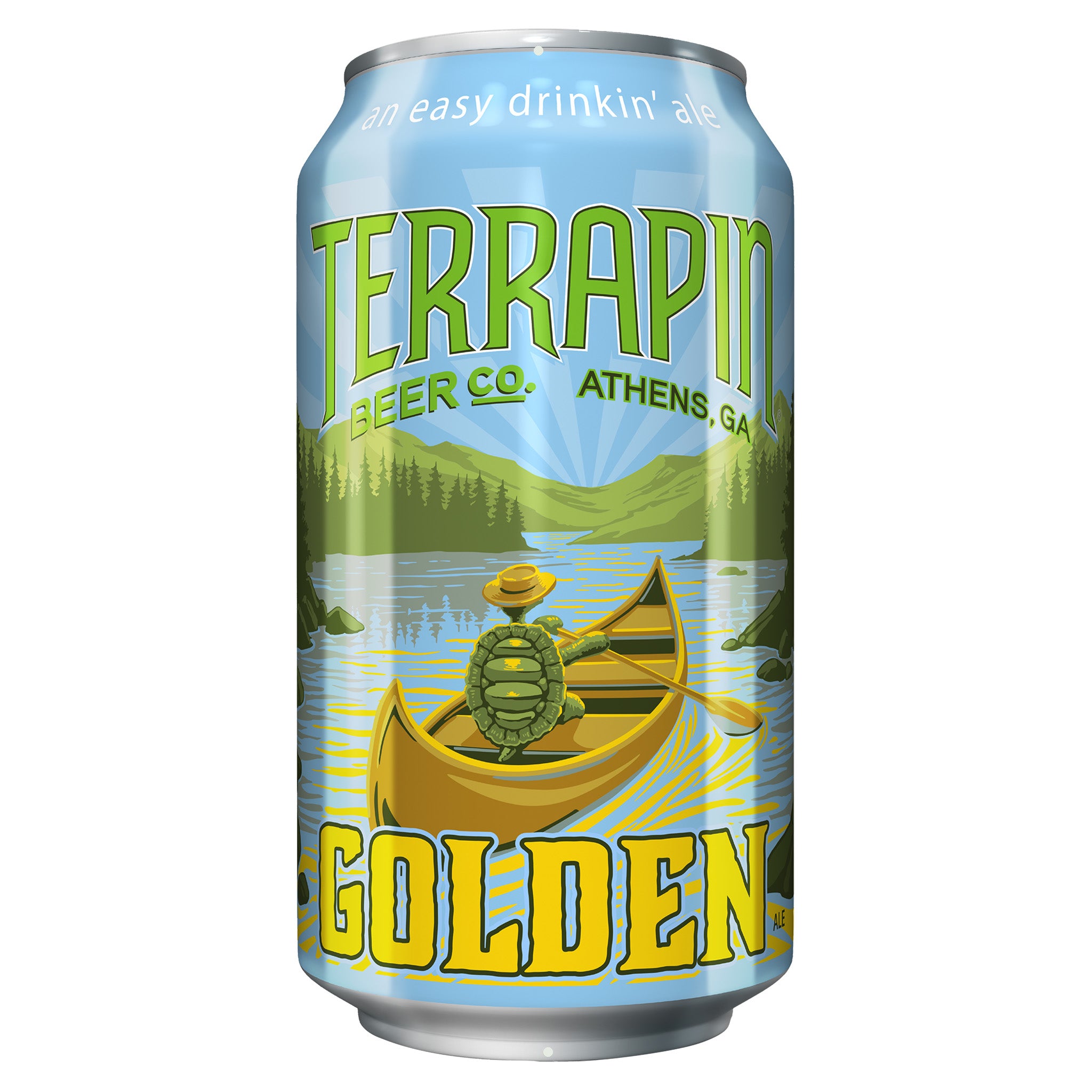
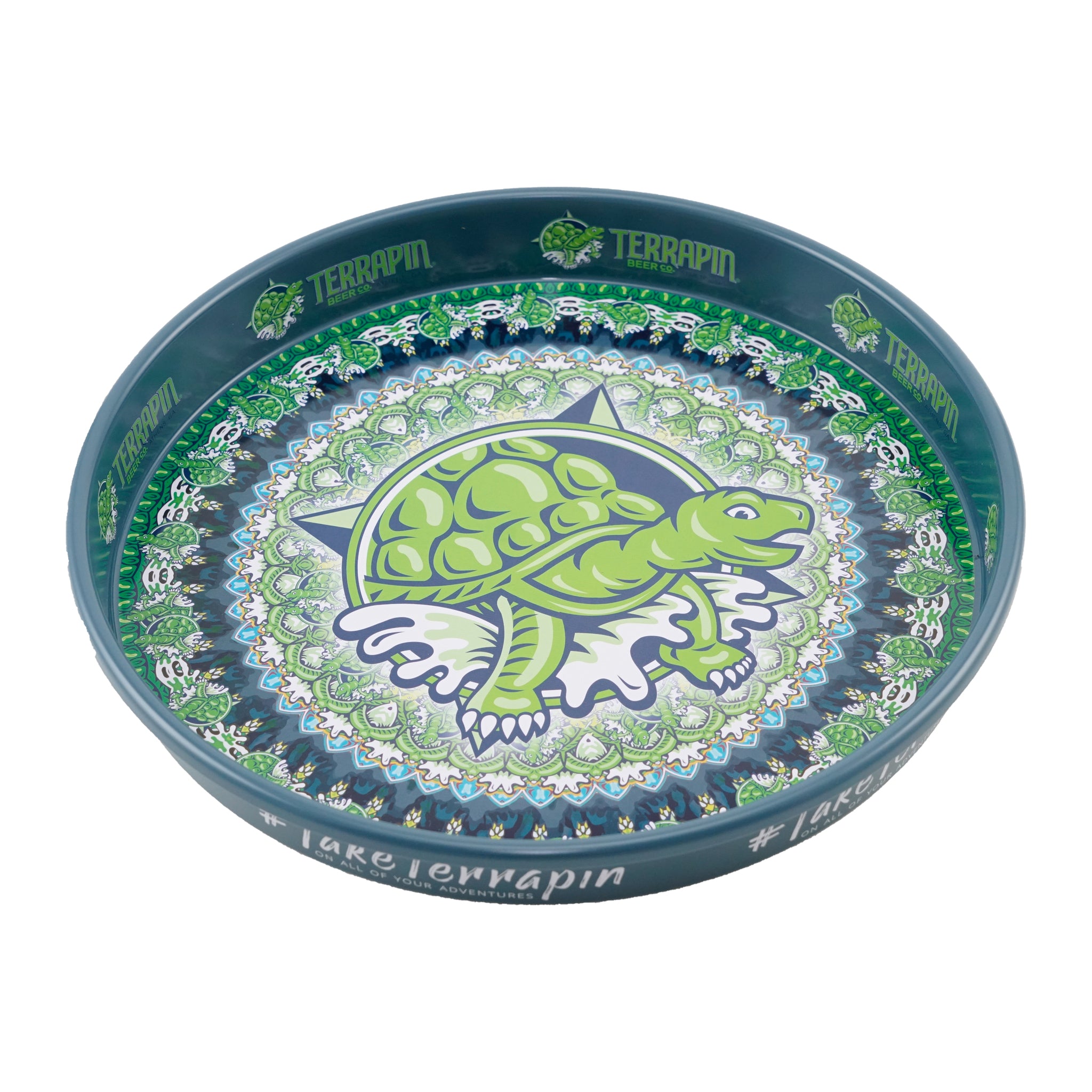

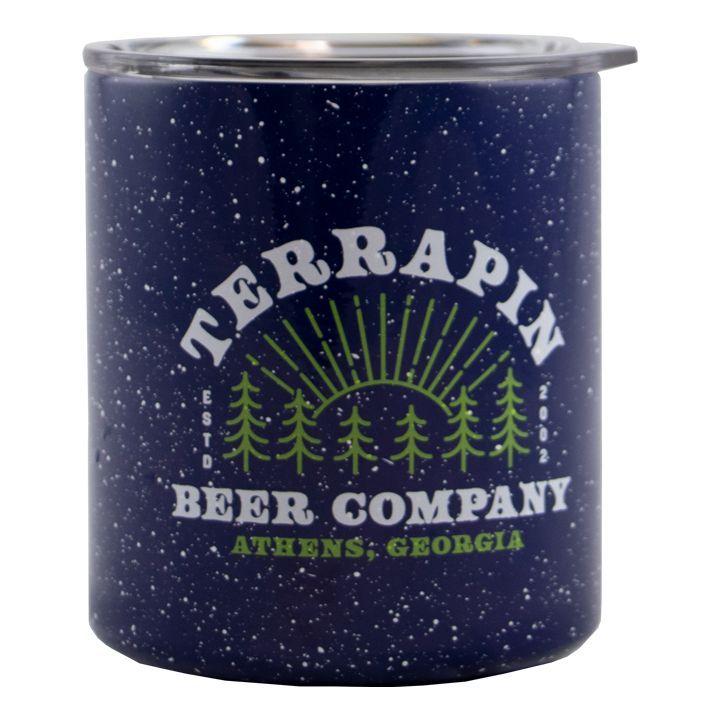
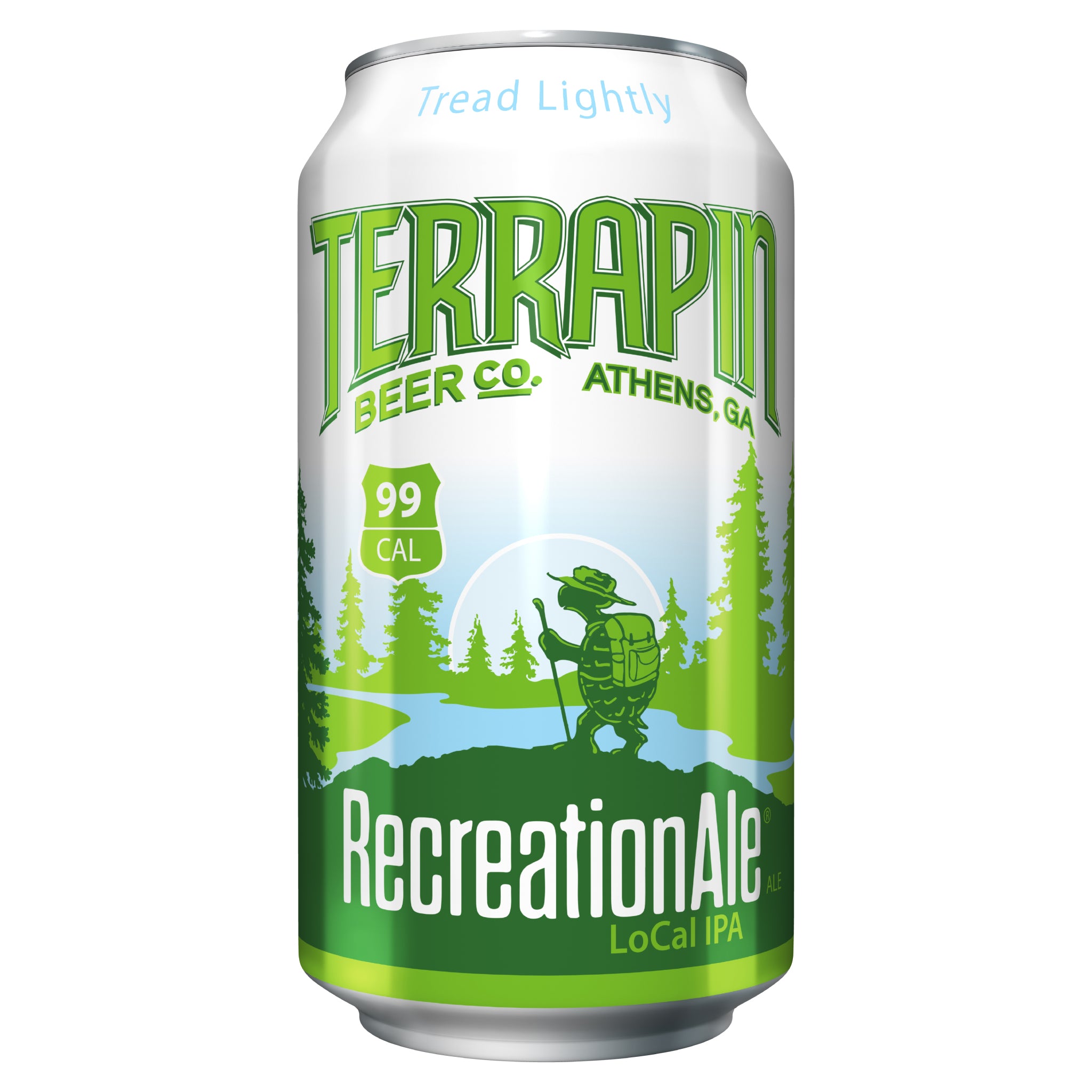
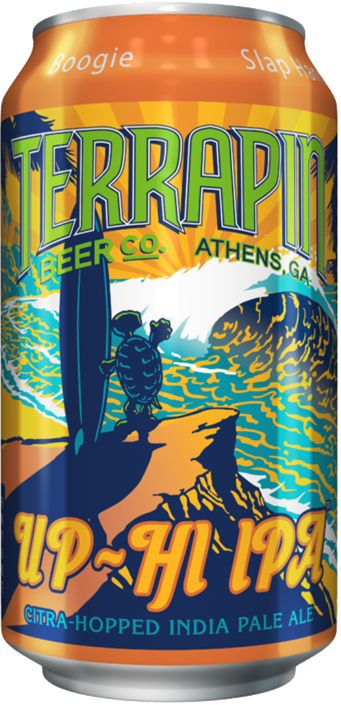
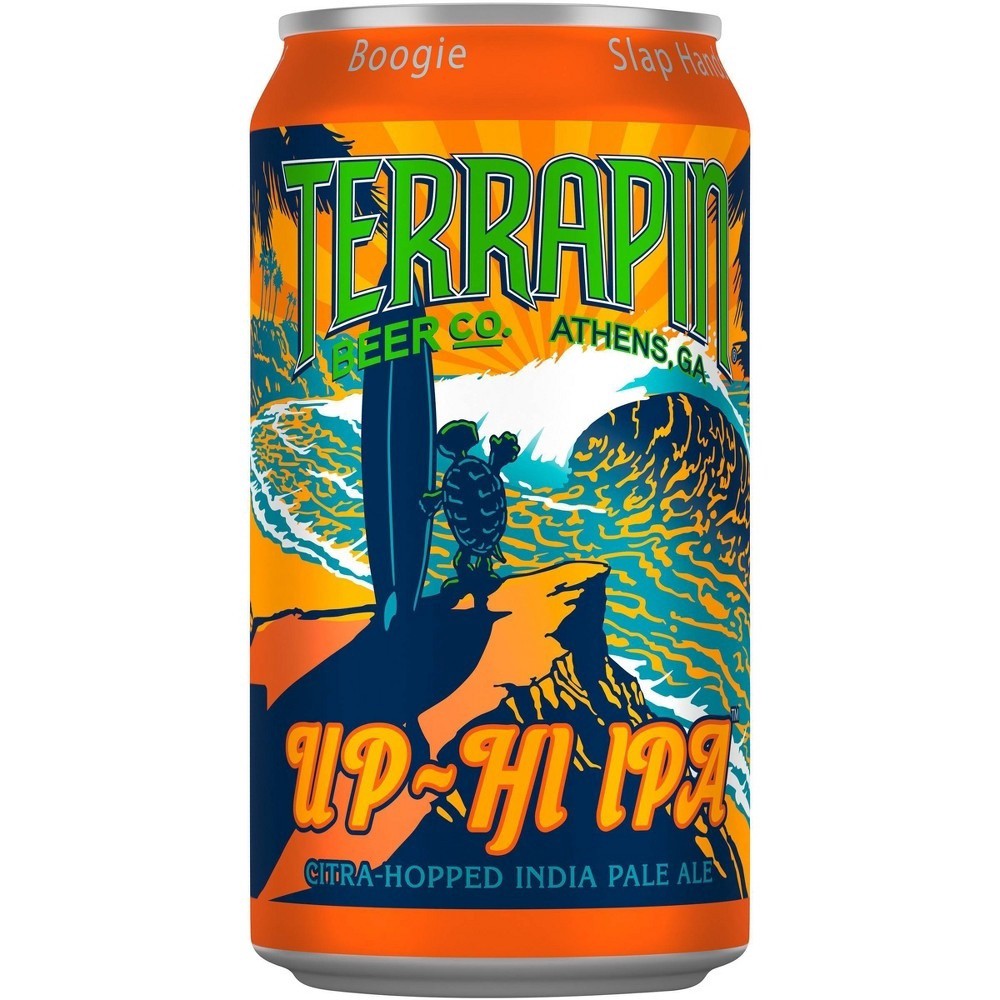
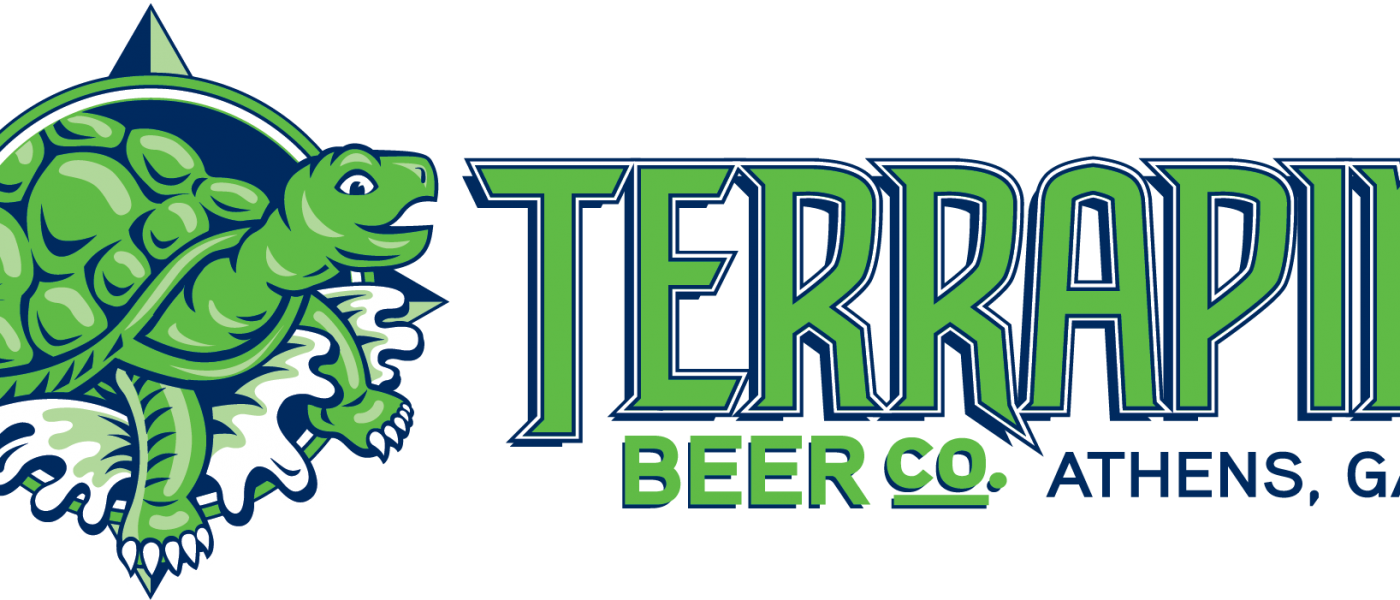
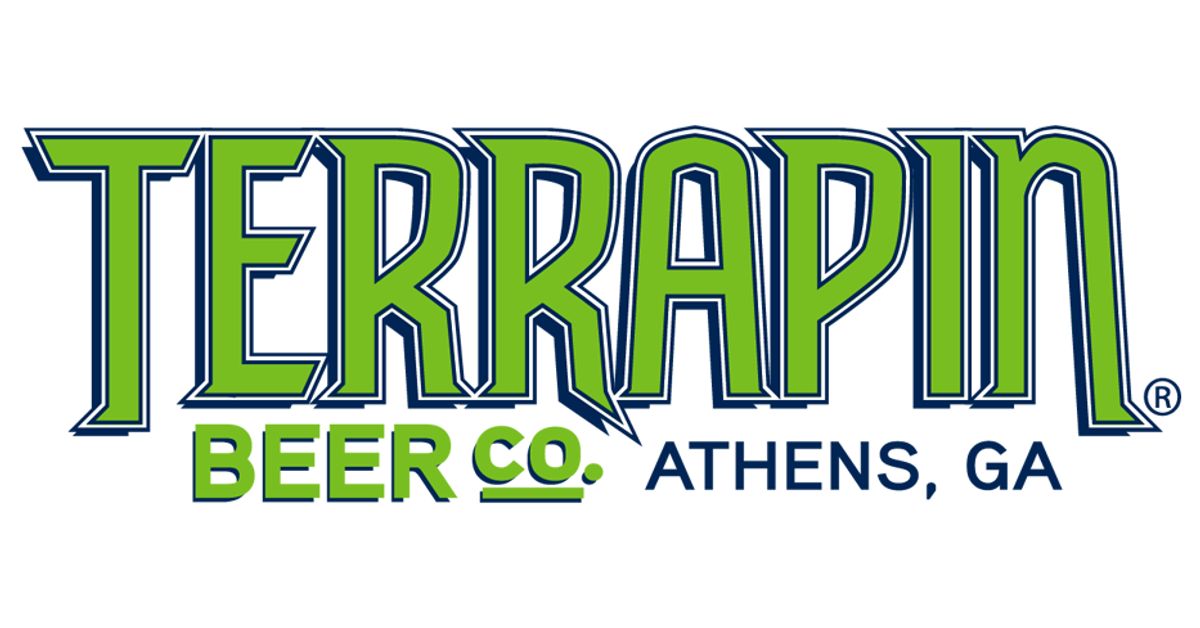

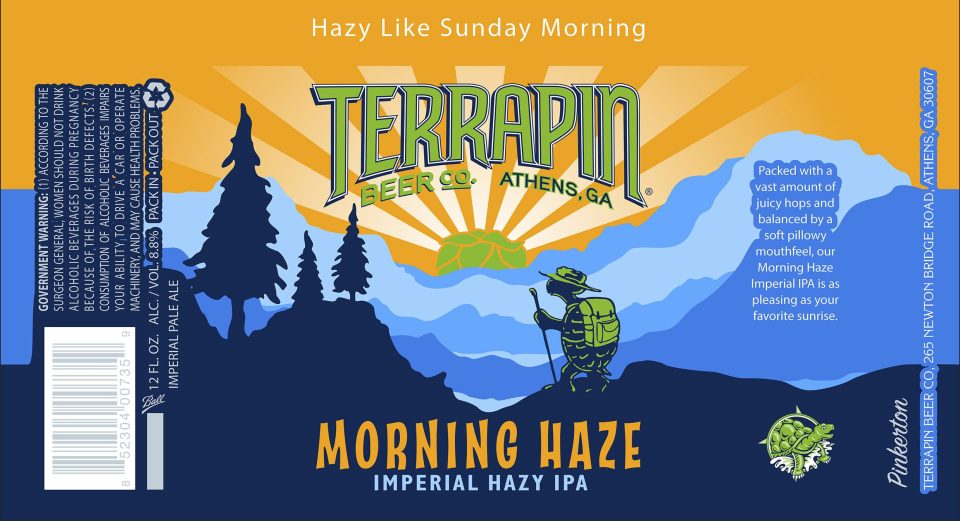

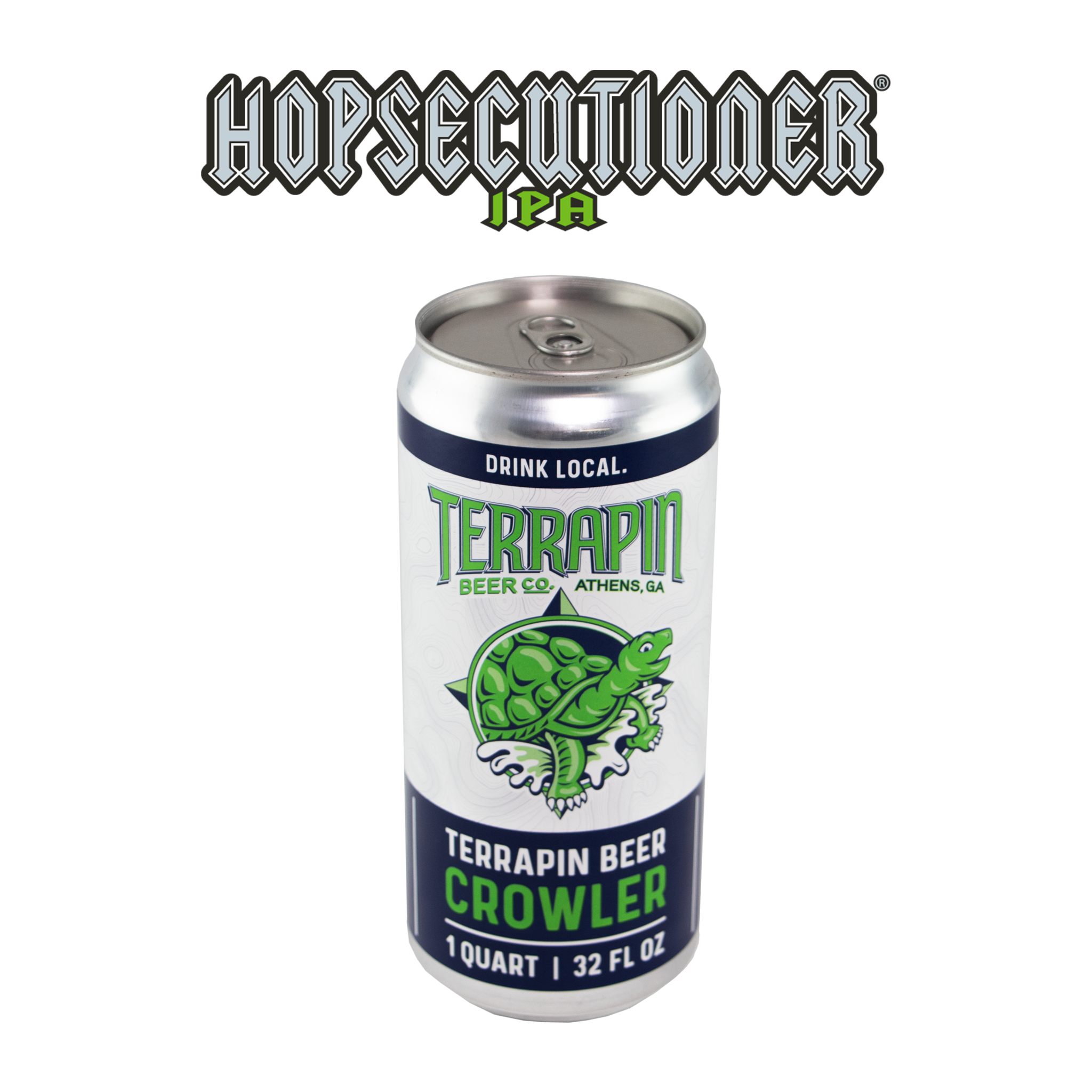

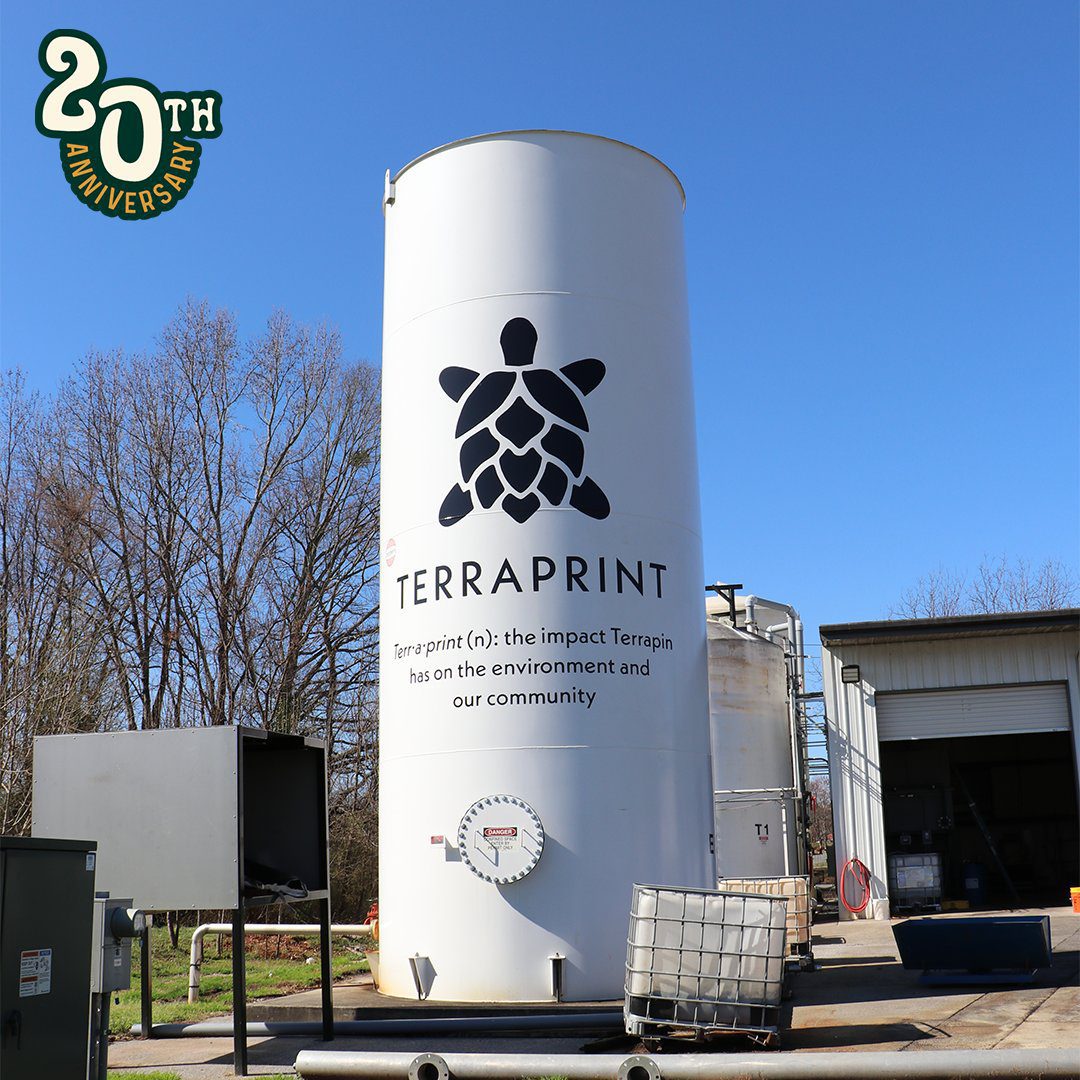
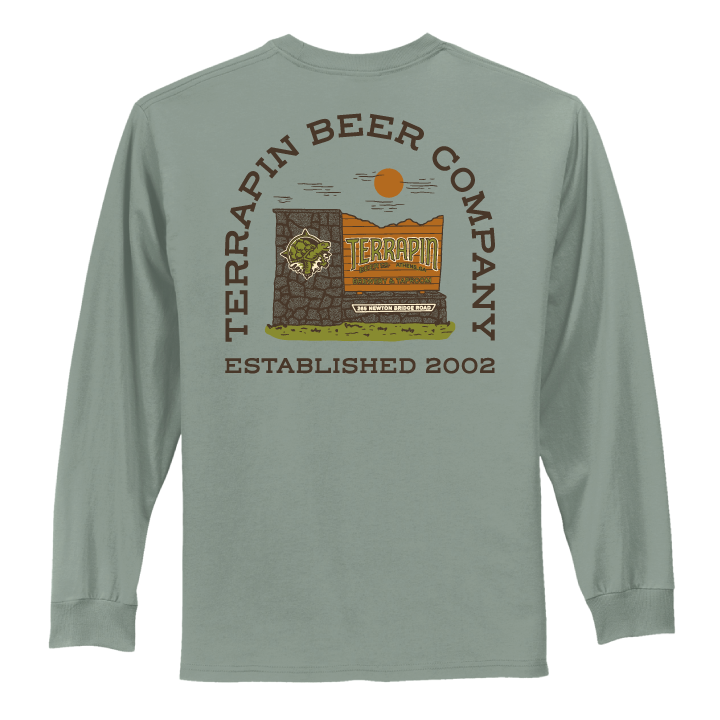