Under A Periodic Inventory System When A Sale Is Made

The retail landscape relies on diverse inventory management systems, each influencing how businesses track and account for their goods. One such system, the periodic inventory system, requires a distinct approach when recording sales, impacting financial reporting and operational oversight. Understanding the mechanics of sales recording under this system is crucial for business owners, accountants, and anyone involved in financial analysis.
This article delves into the specifics of how a sale is handled under a periodic inventory system, examining the processes involved and the implications for a company's financial records. It will explore the differences between this method and the perpetual inventory system, highlighting the advantages and disadvantages of each.
Periodic Inventory: A Snapshot Approach
The periodic inventory system is characterized by its reliance on physical stocktaking at regular intervals, typically at the end of an accounting period. Instead of constantly updating inventory records with each sale, a business using this system determines the cost of goods sold (COGS) only at the end of the period. This contrasts sharply with the perpetual system which provides real-time inventory tracking.
The key difference lies in the frequency and method of inventory updates. Under a periodic system, the cost of goods sold is calculated indirectly, not at the point of sale.
Recording a Sale: What Happens and What Doesn't
When a sale occurs under the periodic inventory system, the immediate accounting entries are primarily focused on the revenue side of the transaction. The sale is recorded by debiting either cash (for cash sales) or accounts receivable (for credit sales). Simultaneously, sales revenue is credited, increasing the company's reported income.
Crucially, unlike the perpetual system, there's no immediate update to the inventory account or the cost of goods sold account when a sale is made. The physical inventory count and COGS calculation are deferred until the end of the accounting period.
This means the inventory account remains unchanged throughout the period, reflecting the initial value of inventory at the beginning of the period plus any purchases made during that time.
Calculating Cost of Goods Sold (COGS)
The process of determining COGS under a periodic system happens at the end of the accounting period. It involves a physical count of the remaining inventory and a calculation based on the following formula: Beginning Inventory + Purchases - Ending Inventory = Cost of Goods Sold.
The accuracy of the physical inventory count is paramount to ensure a reliable COGS figure. This count represents the ending inventory, which is then subtracted from the sum of the beginning inventory and any purchases made during the period.
The resulting COGS is then used to calculate gross profit (Sales Revenue - COGS), which is a critical component of the income statement.
Advantages and Disadvantages
The periodic inventory system is often favored by smaller businesses due to its simplicity and lower upfront costs. It requires less sophisticated technology and accounting software compared to the perpetual system.
However, this system offers less accurate and timely information about inventory levels. This lack of real-time data can lead to stockouts, overstocking, and difficulties in identifying shrinkage (loss of inventory due to theft or damage) promptly.
Because COGS is only calculated at the end of the period, businesses lack immediate insights into the profitability of individual sales or product lines.
Impact on Financial Reporting
The periodic inventory system influences the way a company's financial performance is presented. Because COGS is determined indirectly, the accuracy of the physical inventory count significantly impacts the reliability of the reported gross profit and net income.
Auditors often scrutinize the inventory counting process under a periodic system, paying close attention to the procedures used to ensure completeness and accuracy. Any material errors in the inventory count can distort the financial statements.
Furthermore, the lack of real-time inventory data can make it challenging to prepare timely and accurate financial reports, potentially hindering decision-making.
Example Scenario
Imagine a small retail store that sells clothing and uses a periodic inventory system. At the beginning of the month, the store's inventory was valued at $10,000. Throughout the month, the store purchased an additional $5,000 worth of clothing. At the end of the month, a physical inventory count reveals that the remaining inventory is worth $7,000.
Using the formula, the cost of goods sold is calculated as follows: $10,000 (Beginning Inventory) + $5,000 (Purchases) - $7,000 (Ending Inventory) = $8,000 (Cost of Goods Sold).
This $8,000 figure is then used to calculate the store's gross profit for the month.
The Future of Inventory Management
While the periodic inventory system remains a viable option for some businesses, the trend is towards more sophisticated inventory management solutions. Technological advancements have made perpetual inventory systems more accessible and affordable, even for smaller companies.
Cloud-based inventory management software, barcode scanners, and point-of-sale (POS) systems offer real-time inventory tracking and automation, providing businesses with greater control over their stock levels and improved decision-making capabilities. This allows for better inventory management.
As businesses grow and become more complex, the limitations of the periodic inventory system often outweigh its simplicity, making the transition to a perpetual system a strategic imperative.
In conclusion, understanding how sales are handled under a periodic inventory system is essential for anyone involved in accounting, finance, or business management. While it offers a simplified approach, its reliance on manual processes and lack of real-time data can present challenges for businesses seeking to optimize their inventory management and financial reporting. The ongoing evolution of technology continues to shape the future of inventory management, making it increasingly important for businesses to adopt solutions that provide accurate, timely, and actionable insights.
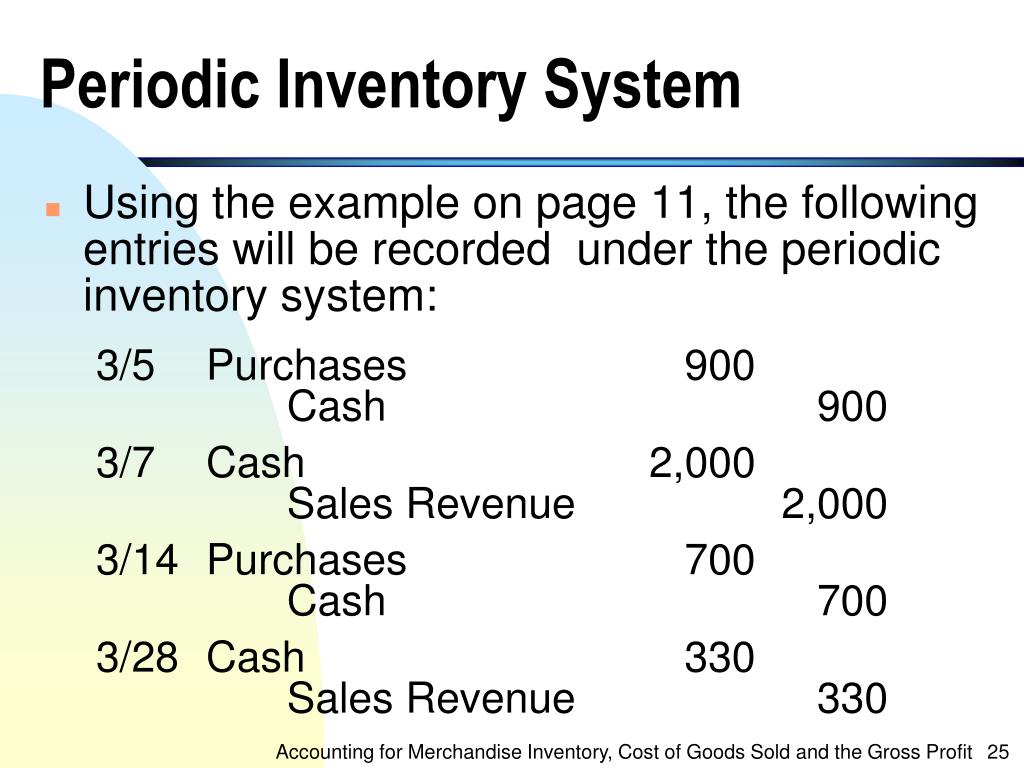

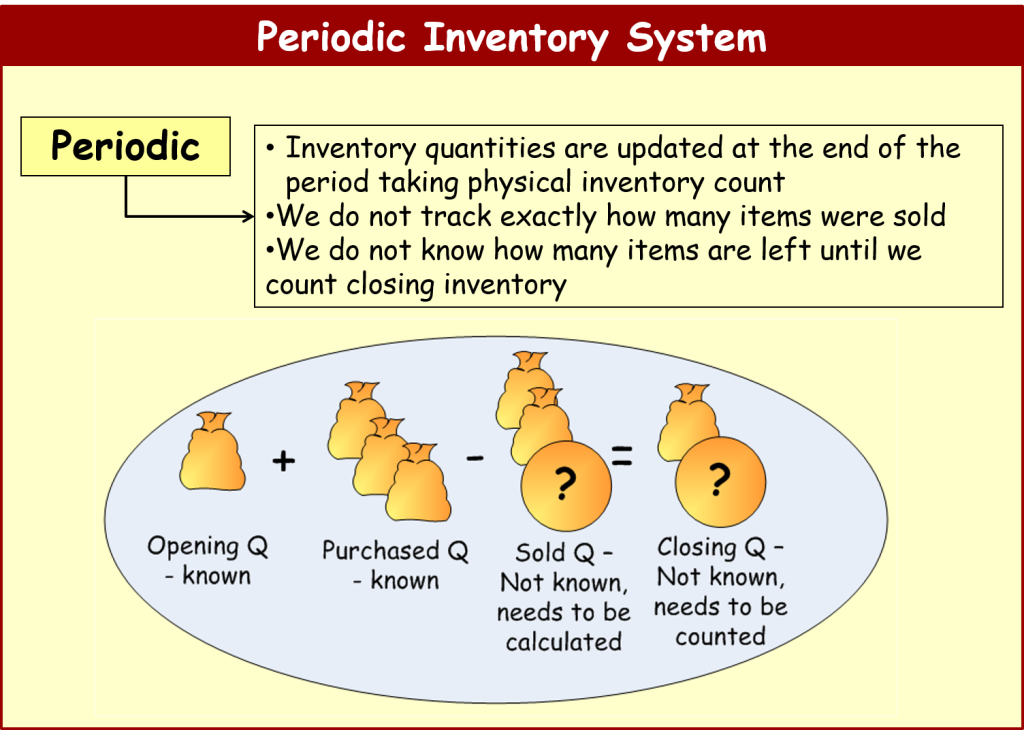








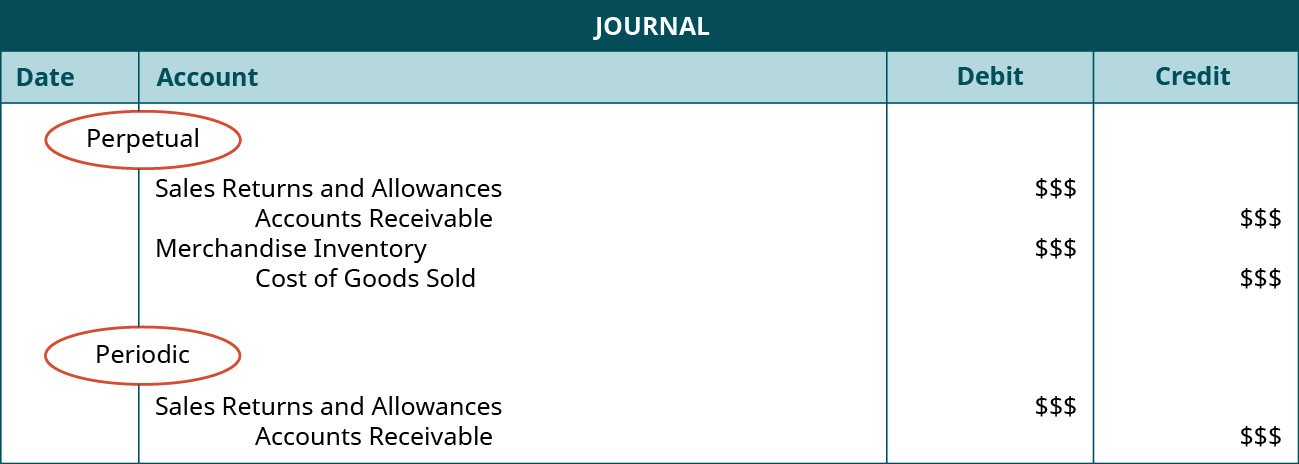




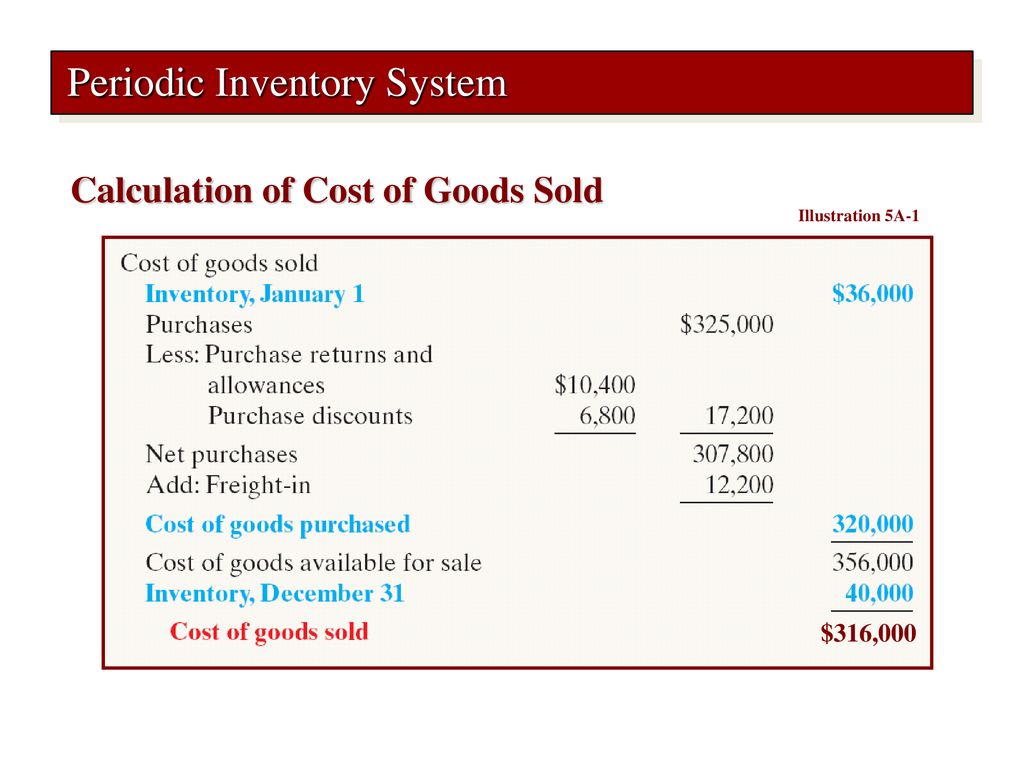
