Which Of The Following Are Product Costs For A Manufacturer
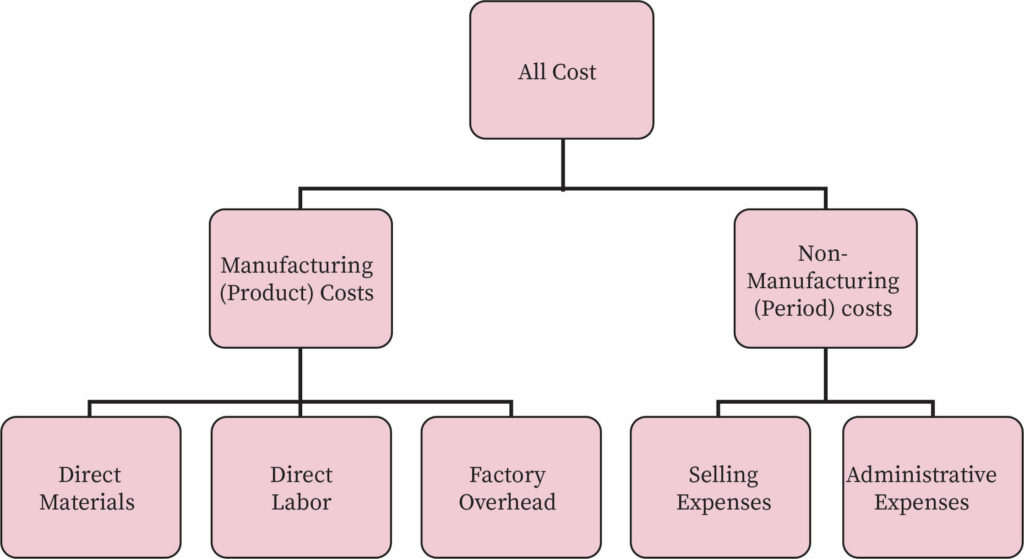
Imagine a bustling factory floor, the rhythmic hum of machinery a constant backdrop. Sparks fly as welders join metal, while in another corner, skilled artisans meticulously assemble intricate components. Raw materials transform into finished goods, ready to be shipped and sold. But behind this scene of creation lies a complex calculation: determining the true cost of each product.
The question of which expenses constitute a product's cost is fundamental to manufacturing, affecting everything from pricing strategy to profitability analysis. Understanding this is crucial for manufacturers to accurately assess their financial performance and make informed decisions about resource allocation.
Understanding Product Costs
Product costs, in the context of manufacturing, are those direct and indirect expenses incurred to bring a product to its saleable state. They are crucial for inventory valuation and determining the cost of goods sold (COGS). This directly impacts a company's bottom line and its ability to price its products competitively.
Direct Materials
Perhaps the most straightforward element of product cost is direct materials. These are the raw materials that become an integral part of the finished product and can be directly traced to it. Think of the wood used to build a chair, the fabric for a garment, or the steel in a car.
The cost of these materials includes the purchase price, freight, insurance during transit, and any other costs directly associated with acquiring them. Discounts and rebates received from suppliers are deducted from the cost of direct materials.
Direct Labor
Next comes direct labor, which represents the wages and benefits paid to workers who are directly involved in the manufacturing process. This includes the wages of machine operators, assemblers, and quality control inspectors.
Direct labor costs also extend to employer-paid payroll taxes, health insurance contributions, and retirement plan contributions for these workers. Accurately tracking direct labor hours and wages is essential for determining the cost of each product.
Manufacturing Overhead
The final category, and often the most complex, is manufacturing overhead. This encompasses all other costs incurred in the manufacturing process that are not direct materials or direct labor.
Manufacturing overhead includes a wide range of expenses. These expenses can be categorized as fixed or variable, adding another layer of complexity to cost accounting.
Examples include:
- Indirect materials (e.g., cleaning supplies, lubricants)
- Indirect labor (e.g., salaries of factory supervisors, maintenance personnel)
- Depreciation of factory equipment
- Rent or mortgage on the factory building
- Utilities (e.g., electricity, water) for the factory
- Property taxes on the factory
- Insurance on the factory and equipment
Allocating manufacturing overhead to individual products is a critical and sometimes challenging task. Different allocation methods, such as activity-based costing (ABC), can be used to more accurately assign overhead costs.
What's Excluded from Product Costs?
It's equally important to understand what is *not* included in product costs. These are generally classified as period costs.
Period costs are expenses that are not directly related to the production of goods and are expensed in the period in which they are incurred. These typically include:
- Selling expenses (e.g., advertising, sales commissions, marketing)
- Administrative expenses (e.g., salaries of office staff, rent for the administrative building)
- Research and development (R&D) costs
- Interest expense
These costs are not inventoried and are not included in the cost of goods sold. They are treated as expenses in the income statement for the period in which they occur.
Importance of Accurate Product Costing
Accurate product costing is vital for several reasons. It allows manufacturers to make informed decisions about pricing. It also facilitates inventory valuation, which is essential for financial reporting.
Moreover, it supports profitability analysis. By understanding the true cost of each product, manufacturers can identify areas for cost reduction and improve their overall efficiency.
According to a report by the Institute of Management Accountants (IMA), companies that implement effective cost accounting systems often experience significant improvements in profitability and operational efficiency. This highlights the strategic importance of accurate product costing in today's competitive business environment.
The Impact on Decision-Making
Consider a scenario where a furniture manufacturer underestimates the cost of its raw materials. This could lead to underpricing, resulting in lost profits on each sale.
Conversely, overestimating the cost of direct labor can lead to overpricing, potentially driving customers to competitors. Likewise, inaccurate overhead allocation can distort the perceived profitability of different product lines, leading to suboptimal resource allocation.
Therefore, a robust product costing system, often supported by sophisticated software solutions, is essential for data accuracy.
Navigating the Complexity
Determining product costs is not always straightforward, especially in complex manufacturing environments. Several factors can complicate the process, including:
- Multiple product lines
- Complex production processes
- Fluctuating material prices
- Changing labor costs
- Difficulty in allocating overhead costs
Manufacturers often rely on cost accountants and specialized software to navigate these complexities. Cost accountants utilize various techniques, such as standard costing and activity-based costing, to allocate costs accurately.
The Future of Product Costing
As technology advances, product costing is evolving. Cloud-based accounting software and data analytics tools are making it easier for manufacturers to track and analyze costs in real-time.
The integration of Internet of Things (IoT) devices on the factory floor also provides valuable data on machine performance and resource consumption, enabling more precise cost allocation. According to a recent Deloitte survey, manufacturers are increasingly adopting these technologies to improve their cost management practices.
The increasing complexity of supply chains and the growing importance of sustainability are also driving changes in product costing. Manufacturers are now incorporating environmental costs and social costs into their product cost calculations.
Conclusion
In the grand tapestry of manufacturing, understanding product costs is akin to understanding the threads that hold it all together. From the tangible raw materials to the intangible overhead, each element contributes to the final price tag.
By diligently tracking and analyzing these costs, manufacturers gain the insight needed to make smart decisions. Accurate product costing isn't just about crunching numbers; it's about understanding the value of every step in the creation process. It is also about fostering a culture of efficiency and innovation on the factory floor.
Ultimately, a deep understanding of product costs empowers manufacturers to thrive in a dynamic marketplace. Armed with knowledge, they can confidently navigate the challenges ahead and build a sustainable future.
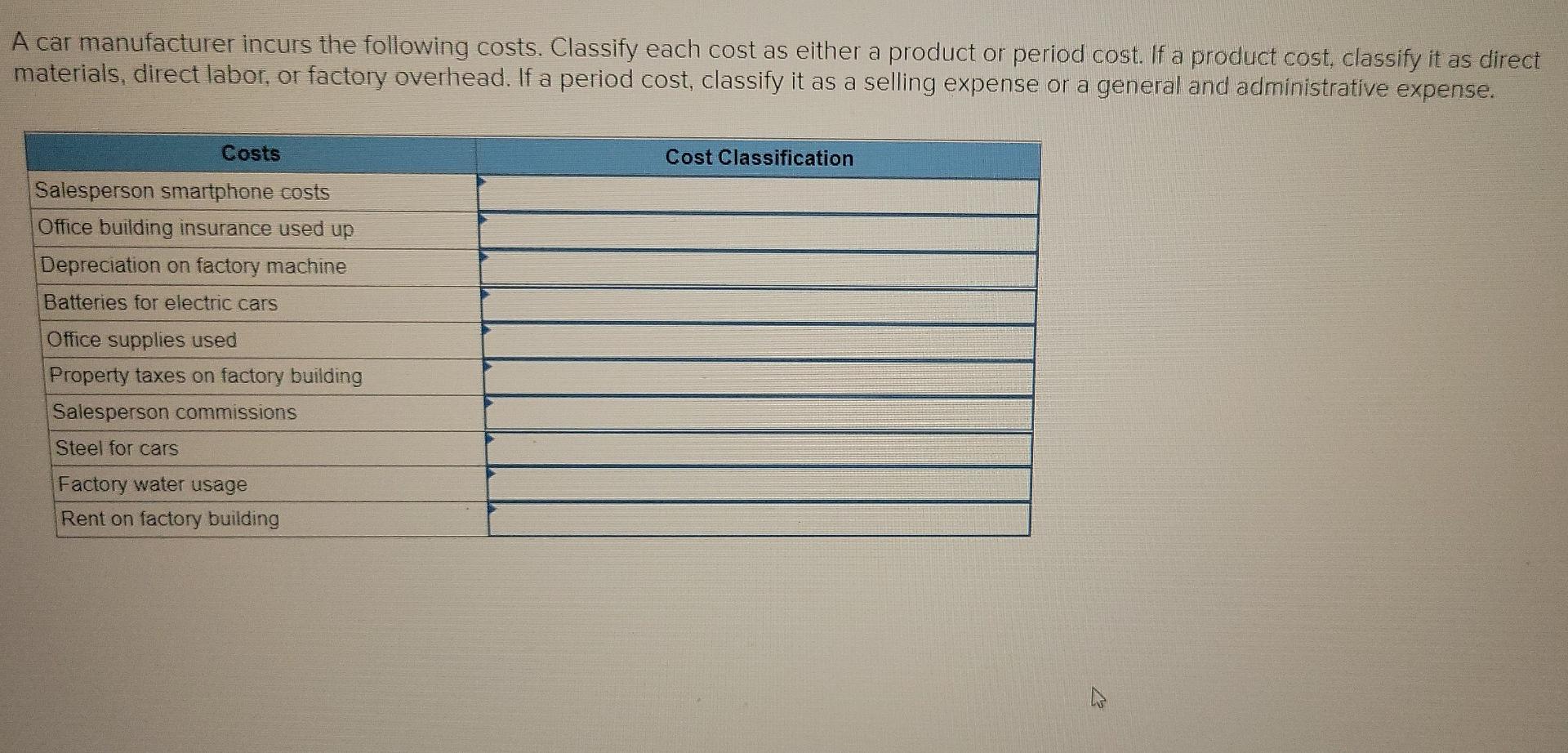
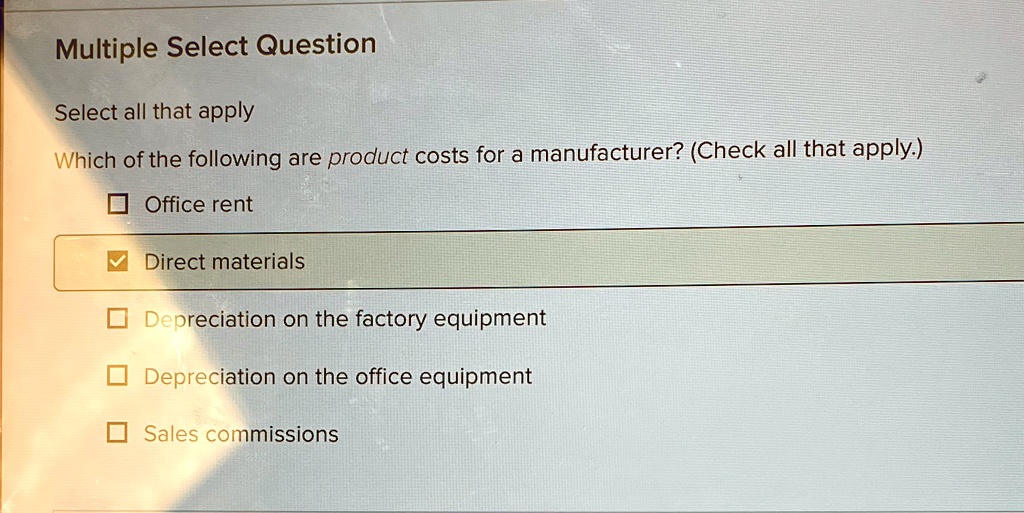
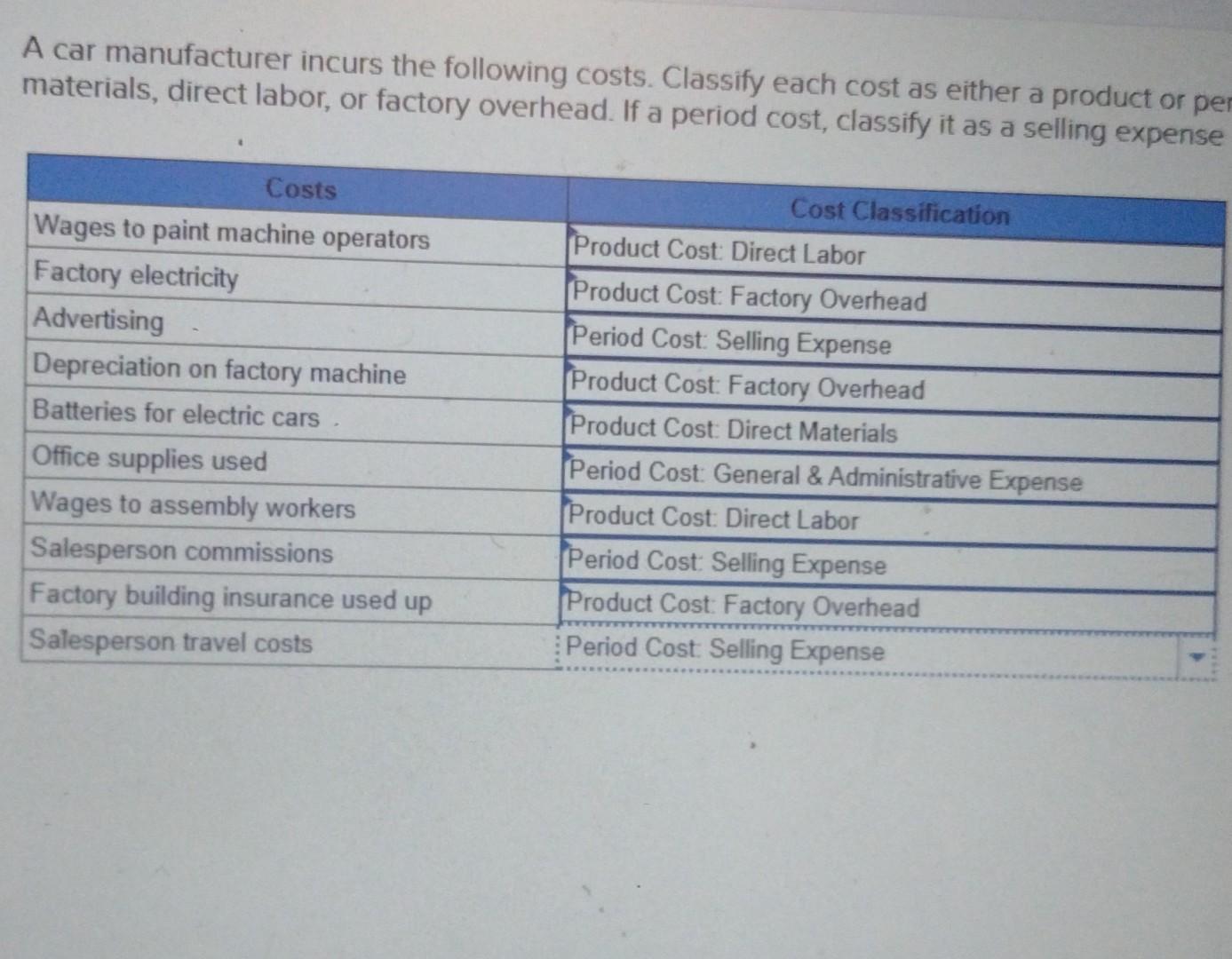
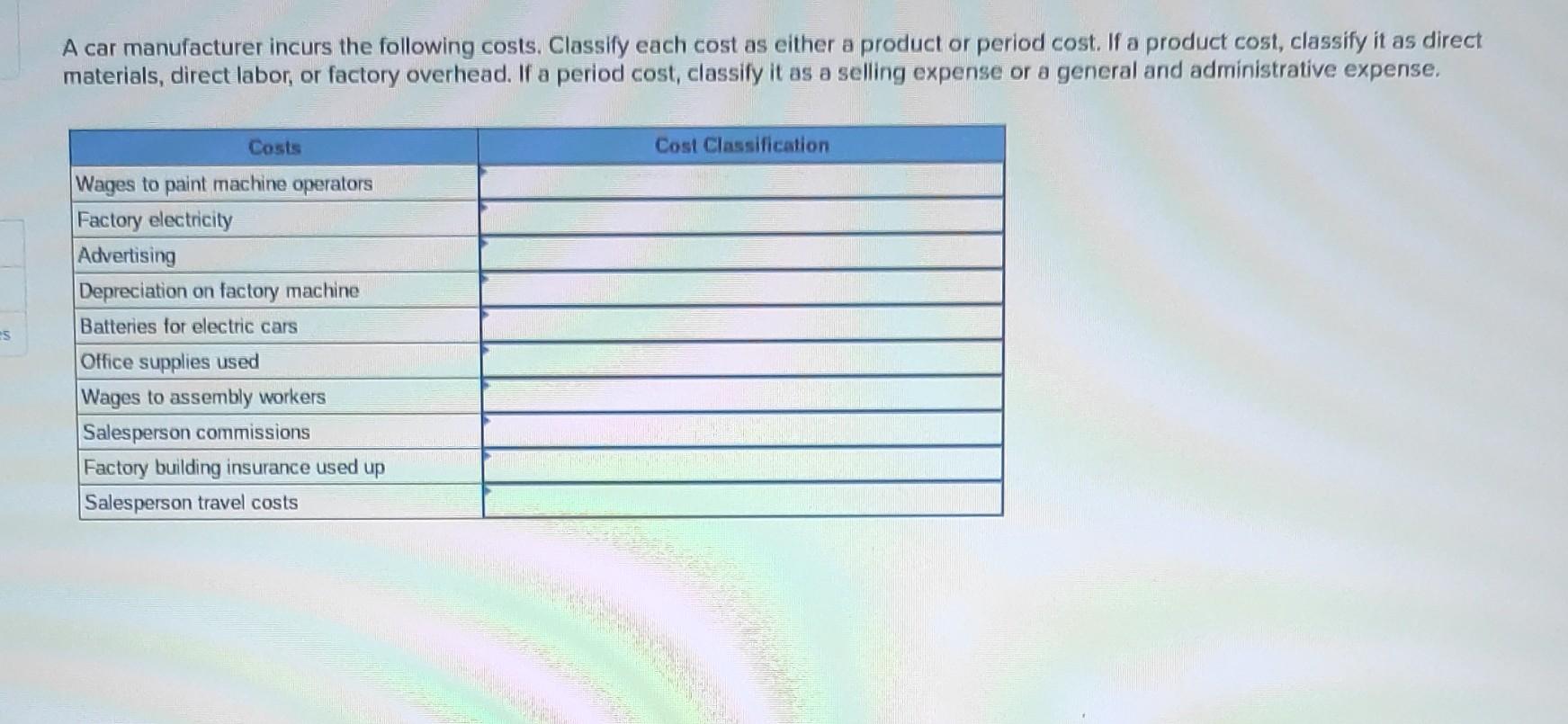