Which Of The Following Statements About Dependent Demand Are True
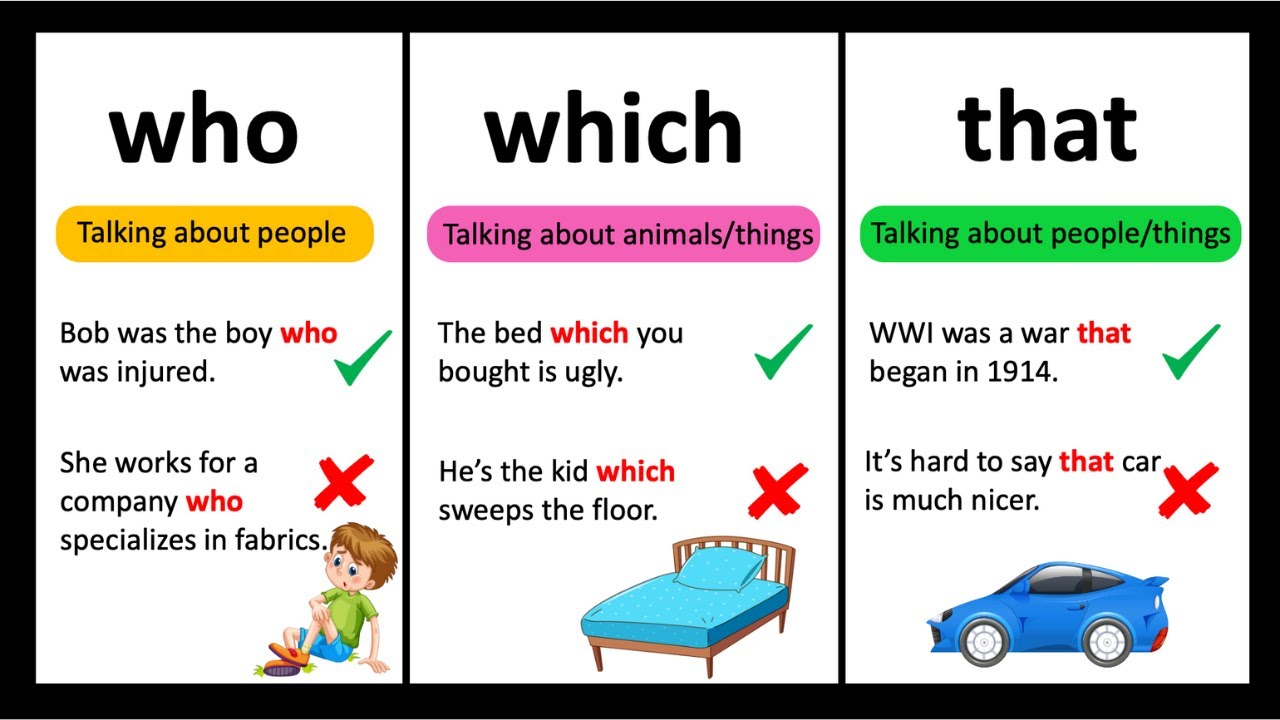
In the intricate world of supply chain management, the concept of dependent demand plays a pivotal role, influencing everything from inventory planning to production schedules. Misunderstanding its nuances can lead to significant inefficiencies, cost overruns, and ultimately, dissatisfied customers. Yet, pinpointing accurate statements about dependent demand often proves challenging, even for seasoned professionals.
This article aims to clarify the core principles of dependent demand, dissecting common misconceptions and highlighting verified truths. By examining the fundamental characteristics of this demand type, we seek to provide a comprehensive understanding for practitioners and students alike, leading to better decision-making in production and inventory control.
Understanding Dependent Demand: The Essentials
Dependent demand refers to the demand for a component part or subassembly that is derived directly from the demand for a parent item. Unlike independent demand, which is driven by market forces and customer orders, dependent demand is predictable and calculable.
It is crucial to grasp this distinction to optimize inventory management strategies.
Key Characteristics of Dependent Demand
One true statement about dependent demand is that it is directly related to the demand for another item. This relationship is often documented in a Bill of Materials (BOM), which outlines the components and quantities needed to produce a finished product.
For example, the demand for tires on a car assembly line is dependent on the number of cars being produced.
Another accurate assertion is that dependent demand can be calculated rather than forecasted. Using the BOM and a production schedule for the parent item, the exact quantity of each component needed can be determined.
This allows for precise material requirements planning (MRP), minimizing the need for safety stock.
Common Misconceptions and Clarifications
A frequent misunderstanding is that dependent demand always applies to raw materials. While raw materials can be subject to dependent demand, it more commonly refers to components and subassemblies used in manufacturing.
Consider the demand for microchips in the production of smartphones; this is a clear example of dependent demand at the component level.
Another misconception is that dependent demand is always stable and predictable. While generally more predictable than independent demand, changes in the parent item's production schedule can significantly impact dependent demand.
A sudden surge in demand for finished goods will cascade down the supply chain, affecting the demand for all dependent components.
The Role of MRP in Managing Dependent Demand
Material Requirements Planning (MRP) systems are specifically designed to manage dependent demand. These systems use the BOM, production schedule, and inventory data to calculate the quantity and timing of materials needed.
This allows businesses to procure materials just in time, reducing inventory holding costs and minimizing the risk of obsolescence.
MRP systems also help identify potential bottlenecks in the supply chain. By tracking lead times for each component, MRP can highlight potential delays and allow for proactive problem-solving.
This proactive approach ensures that production schedules are met and customer orders are fulfilled on time.
Benefits of Accurate Dependent Demand Management
Effective management of dependent demand translates to several significant advantages. Reduced inventory costs are a primary benefit. By accurately calculating material requirements, companies can minimize the amount of inventory held, freeing up capital for other investments.
Improved production efficiency is another key outcome. Knowing exactly when and what materials are needed allows for smoother production runs and fewer disruptions.
Finally, better customer service results from effective dependent demand management. Meeting production schedules consistently leads to on-time delivery of finished goods, increasing customer satisfaction.
Challenges and Future Trends
Despite the benefits, managing dependent demand is not without its challenges. Data accuracy is crucial for effective MRP, and inaccurate BOMs or inventory records can lead to significant errors. Implementing and maintaining an MRP system requires significant investment in software, training, and ongoing maintenance.
Demand variability, even for dependent items, can also pose a challenge. Unexpected disruptions in the supply chain or sudden changes in customer demand can throw off production schedules and material requirements.
Looking ahead, several trends are shaping the future of dependent demand management. The increasing adoption of cloud-based MRP systems is making these tools more accessible to smaller businesses.
The use of advanced analytics and machine learning is also improving demand forecasting and optimizing inventory levels. Furthermore, the integration of MRP with other enterprise systems, such as ERP and CRM, is creating a more seamless and integrated supply chain.
These advancements are enabling businesses to manage dependent demand more effectively than ever before, leading to greater efficiency, reduced costs, and improved customer service.
Conclusion
Understanding the nuances of dependent demand is critical for success in today's competitive business environment. By recognizing the key characteristics of this demand type and leveraging the power of MRP systems, companies can optimize their supply chains and achieve significant improvements in efficiency and profitability.
While challenges remain, ongoing advancements in technology and data analytics are making dependent demand management more sophisticated and effective. Embracing these advancements will be essential for businesses looking to stay ahead of the curve and thrive in the years to come.
Ultimately, a firm grasp of dependent demand principles empowers organizations to make informed decisions, streamline operations, and deliver exceptional value to their customers.
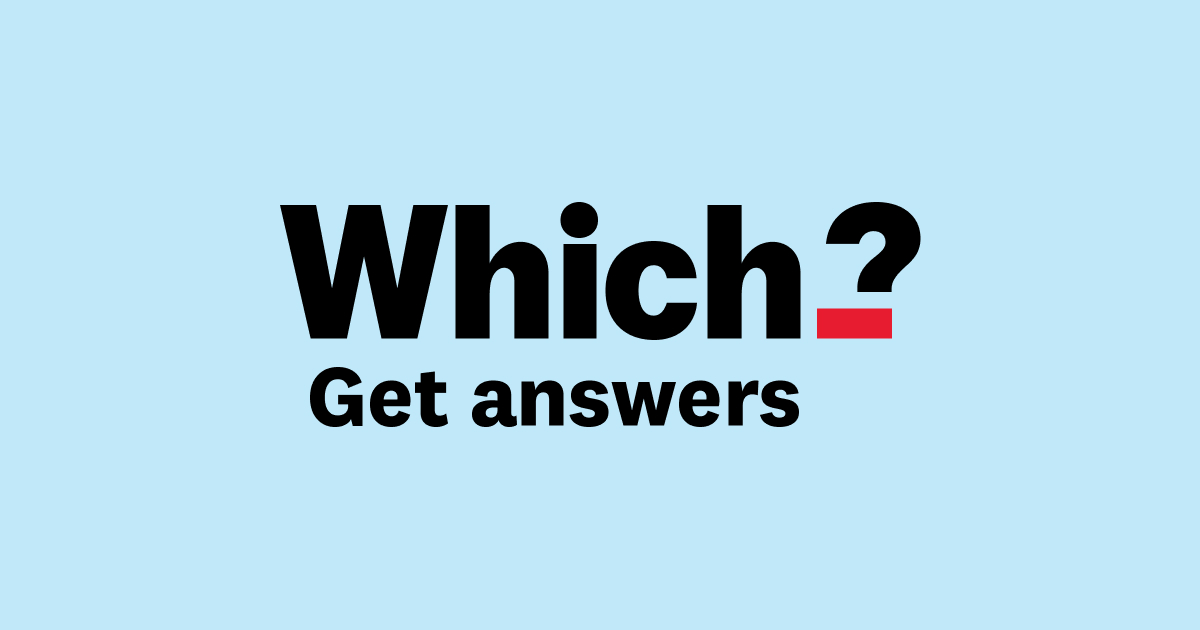
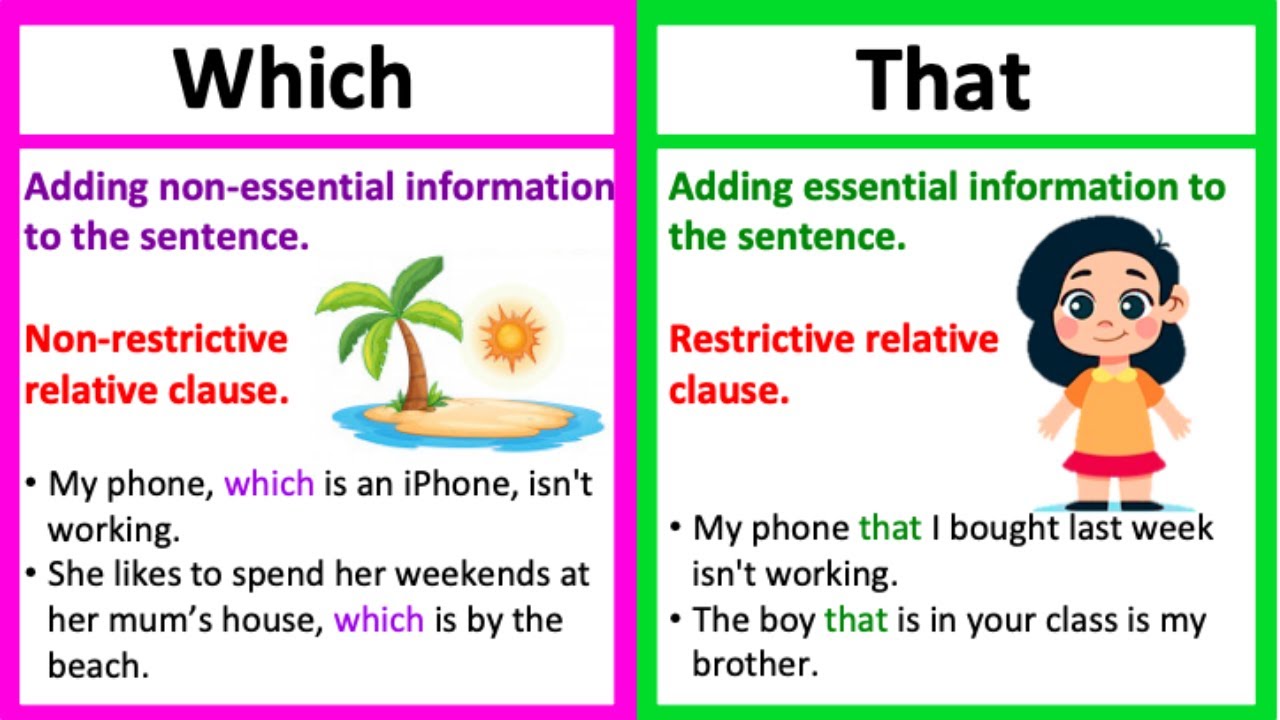