A Company's Distribution And Warehouse Expenses

Imagine a bustling warehouse, a symphony of forklifts humming, packages gliding along conveyor belts, and the steady rhythm of workers ensuring everything finds its way to its destination. This intricate dance, repeated countless times each day, is the lifeblood of modern commerce. It's a dance powered by strategy, technology, and, of course, substantial financial investment in distribution and warehouse expenses.
Understanding these expenses is crucial for businesses striving to optimize their supply chains and remain competitive in today's dynamic market. This article delves into the world of distribution and warehouse costs, exploring their components, challenges, and the innovative strategies companies are employing to navigate this vital aspect of their operations.
The Foundation: Understanding Distribution and Warehouse Expenses
Distribution and warehouse expenses encompass all costs associated with storing, handling, and moving goods from the point of origin to the end consumer. These costs are a significant portion of a company's overall operating expenses, directly impacting profitability and customer satisfaction.
The efficient management of these expenses is not merely about cutting costs; it's about optimizing the entire process to ensure timely delivery, minimize waste, and enhance the overall customer experience. Let's examine the key elements that contribute to these expenses.
Key Components of Distribution and Warehouse Expenses
Several factors contribute to the overall distribution and warehouse expenses. These include rent or mortgage payments for warehouse space, utilities (electricity, water, heating/cooling), and property taxes.
Labor costs associated with warehouse staff, including salaries, wages, benefits, and training, constitute another significant expense. Then, there are the costs associated with warehouse equipment, such as forklifts, conveyor belts, racking systems, and maintenance and repair expenses.
Transportation costs involve moving goods from warehouses to distribution centers or directly to customers, encompassing fuel, vehicle maintenance, and driver salaries. Inventory holding costs include the cost of capital tied up in inventory, storage fees, insurance, and obsolescence costs.
Packaging materials, such as boxes, tape, and protective wrapping, are essential for protecting goods during transit. And, finally, technology infrastructure includes warehouse management systems (WMS), transportation management systems (TMS), and other software solutions.
The Shifting Landscape: Challenges in Managing Expenses
Several factors are making the management of distribution and warehouse expenses increasingly complex. One challenge is the rising transportation costs, driven by fluctuating fuel prices, driver shortages, and increased demand for faster delivery times.
Another challenge is the increasing demand for faster delivery times. E-commerce has heightened customer expectations, requiring companies to invest in faster and more efficient distribution networks. The complexities of global supply chains create challenges related to managing inventory across multiple locations, dealing with customs regulations, and mitigating risks associated with disruptions such as natural disasters or geopolitical events.
Labor shortages, particularly in the warehousing and transportation sectors, can drive up labor costs and hinder operational efficiency. Finally, the rapid pace of technological change requires continuous investment in new technologies and training to remain competitive.
Strategies for Optimization: Cutting Costs and Improving Efficiency
Companies are implementing various strategies to optimize their distribution and warehouse operations and reduce expenses. One popular approach is implementing warehouse management systems (WMS). A WMS can optimize warehouse layout, inventory management, and order fulfillment processes, reducing waste and improving efficiency.
Another strategy involves automating warehouse processes. Automation technologies, such as automated guided vehicles (AGVs), robotic picking systems, and automated sorting systems, can reduce labor costs, improve accuracy, and accelerate order fulfillment.
Companies are also optimizing their transportation networks by consolidating shipments, using more efficient routes, and negotiating favorable rates with carriers. Efficient inventory management is critical to minimizing holding costs and reducing the risk of obsolescence. Techniques such as Just-in-Time (JIT) inventory and demand forecasting can help optimize inventory levels.
Negotiating favorable leases or contracts with landlords and suppliers can help reduce expenses. Embracing sustainable practices, such as using energy-efficient lighting and equipment, reducing packaging waste, and optimizing transportation routes, can lower operating costs and enhance a company's environmental footprint.
Data analytics plays a crucial role in identifying areas for improvement and optimizing distribution and warehouse operations. By analyzing data related to inventory levels, order fulfillment times, and transportation costs, companies can gain valuable insights into their operations and identify opportunities for cost savings.
Real-World Examples: Success Stories in Expense Optimization
Several companies have successfully implemented strategies to optimize their distribution and warehouse expenses. Amazon, for example, has invested heavily in automation and robotics to streamline its warehouse operations and reduce labor costs. The company uses a sophisticated WMS to optimize inventory management and order fulfillment.
Walmart has optimized its transportation network by using a combination of its own fleet and third-party carriers. The company uses data analytics to identify the most efficient routes and consolidate shipments. *Zara*, known for its fast-fashion model, uses a highly efficient supply chain to quickly deliver new products to its stores. The company relies on a network of strategically located distribution centers and a sophisticated logistics system.
These examples highlight the importance of investing in technology, optimizing processes, and leveraging data to achieve significant cost savings and improve efficiency in distribution and warehouse operations. The Council of Supply Chain Management Professionals (CSCMP) consistently publishes research and case studies highlighting best practices in the field.
Looking Ahead: The Future of Distribution and Warehouse Management
The future of distribution and warehouse management will be shaped by several key trends. Artificial intelligence (AI) and machine learning will play an increasingly important role in optimizing warehouse operations, predicting demand, and improving decision-making. The Internet of Things (IoT) will enable real-time monitoring of inventory, equipment, and transportation, providing valuable insights and improving operational efficiency.
Blockchain technology can enhance supply chain transparency and security, reducing the risk of fraud and counterfeiting. The rise of e-commerce will continue to drive demand for faster and more efficient distribution networks. And, finally, sustainability will become an increasingly important consideration, with companies seeking to reduce their environmental footprint and adopt more eco-friendly practices.
Successfully navigating the complexities of distribution and warehouse expenses requires a strategic approach that focuses on continuous improvement and innovation. By embracing technology, optimizing processes, and leveraging data, companies can achieve significant cost savings, enhance customer satisfaction, and gain a competitive edge in today's dynamic market.
The hum of the warehouse, the glide of packages, the intricate dance – it's a constant evolution, a pursuit of efficiency and excellence that drives commerce forward. The companies that master this dance will be the ones leading the way.

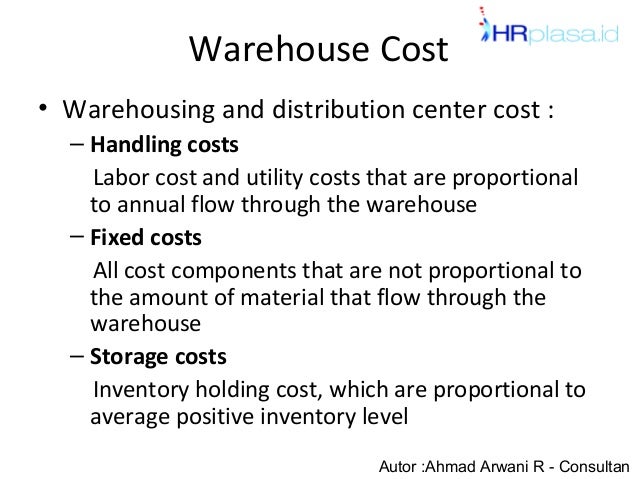

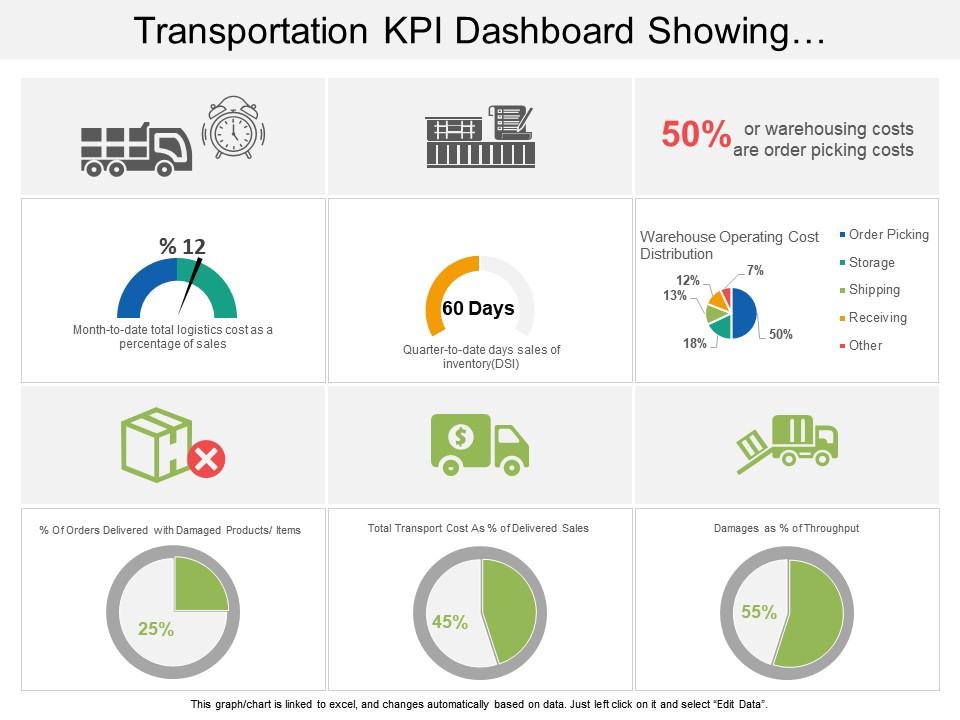

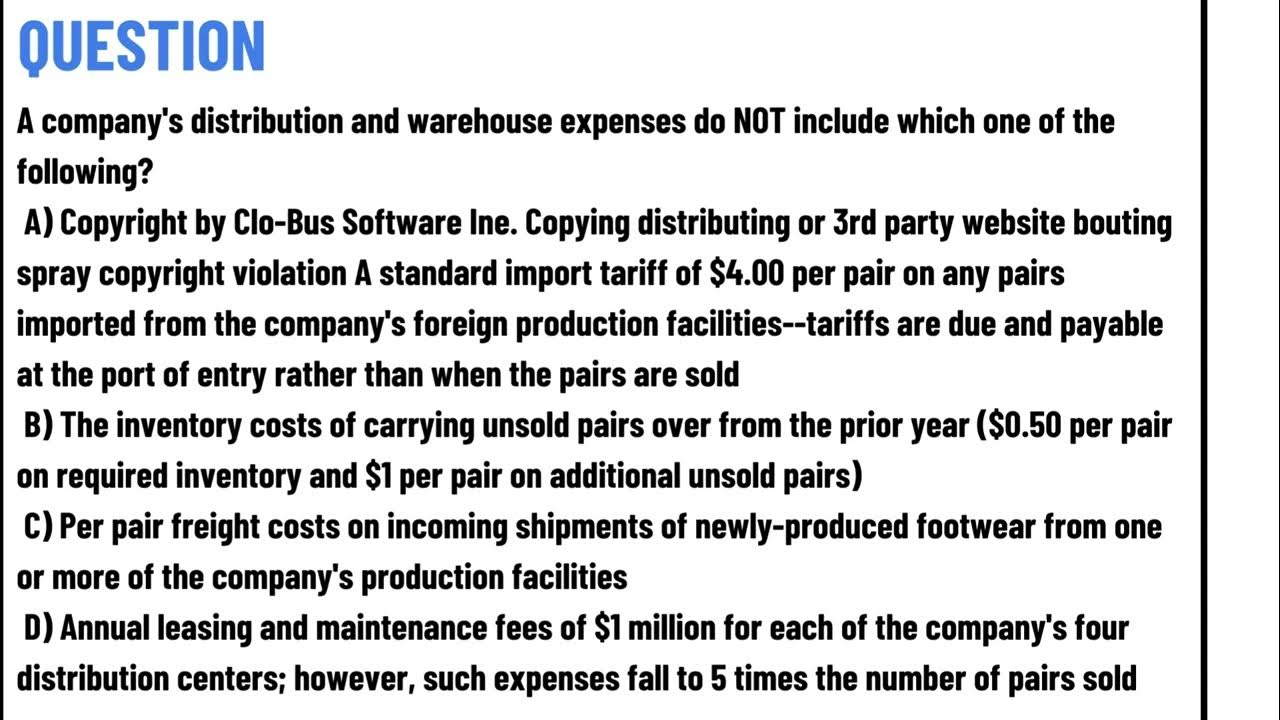
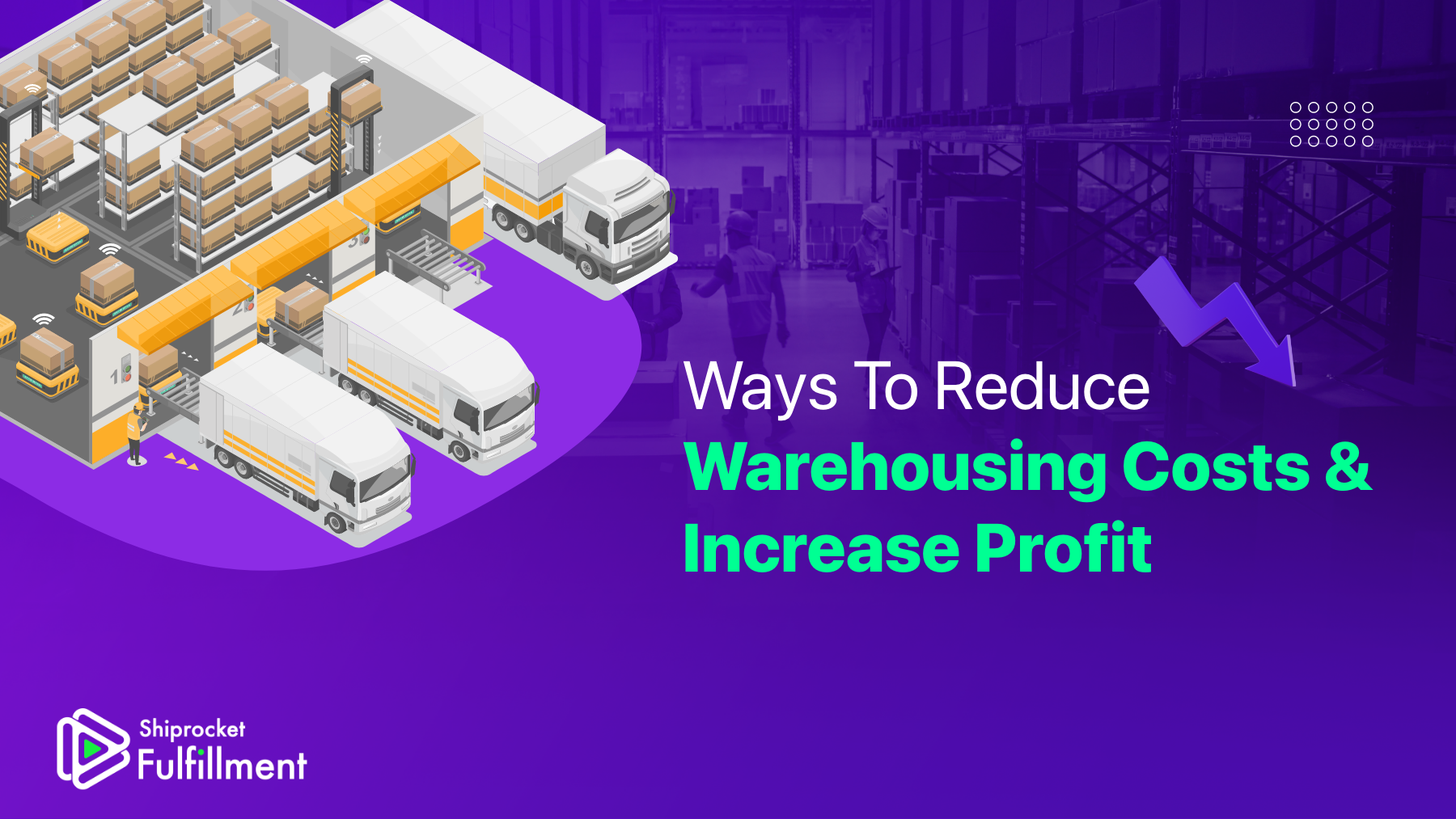
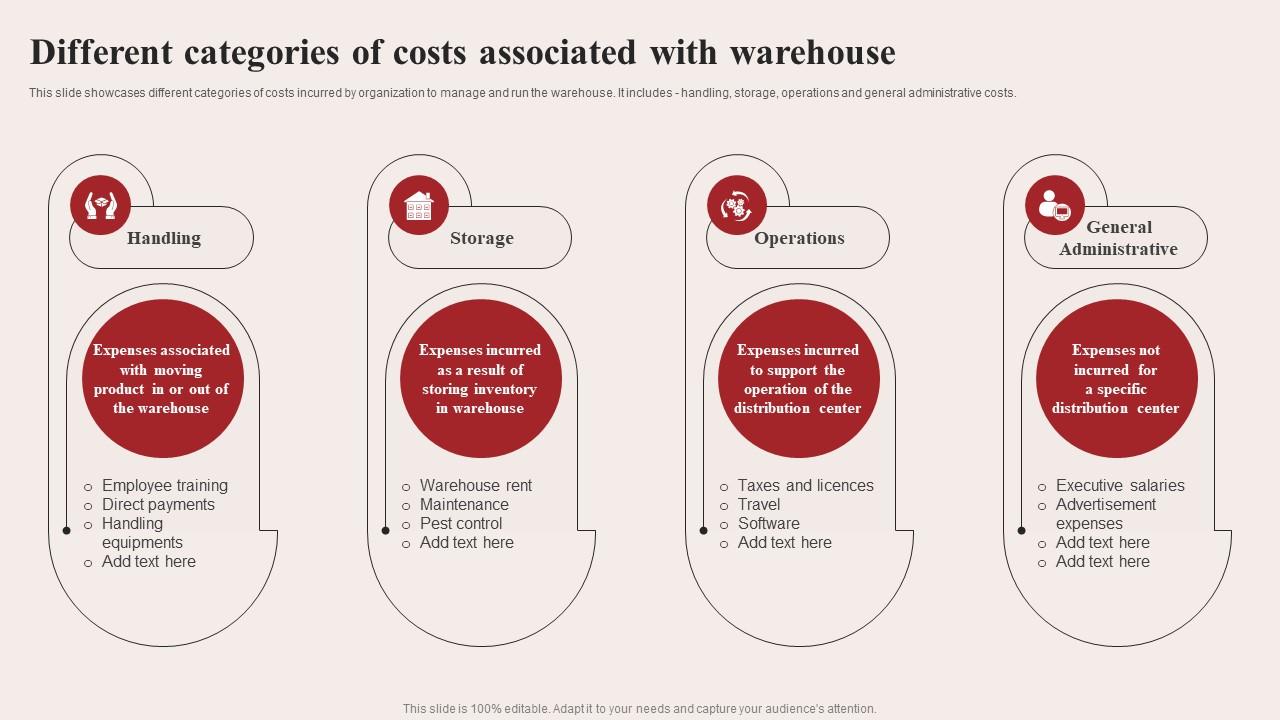
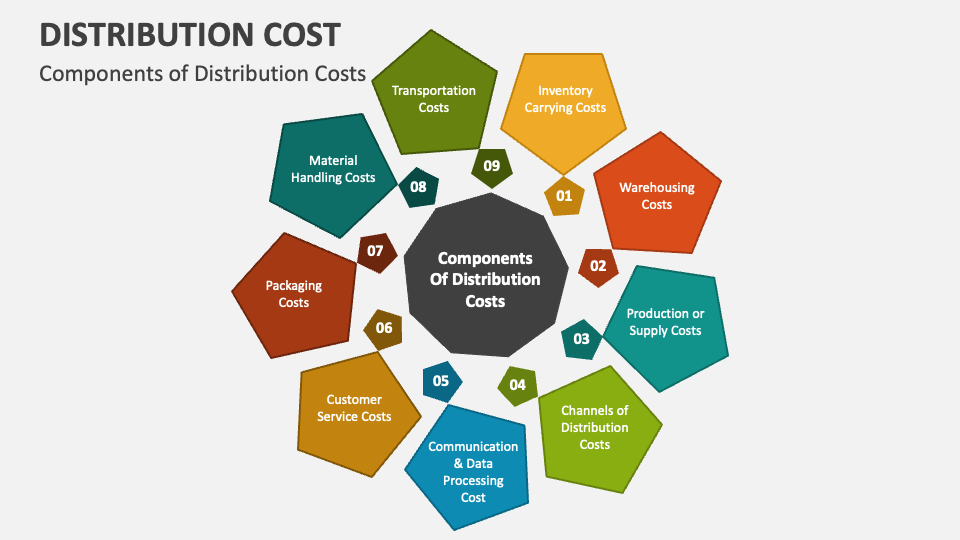

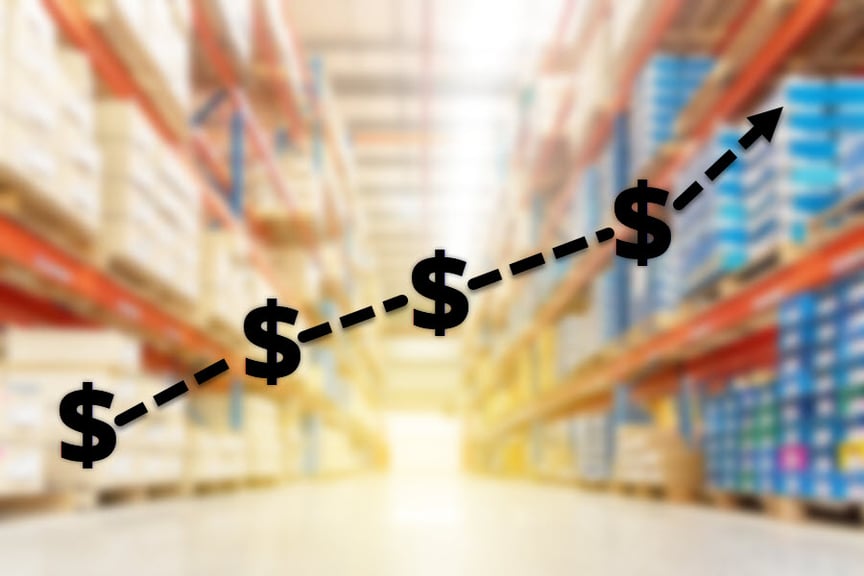

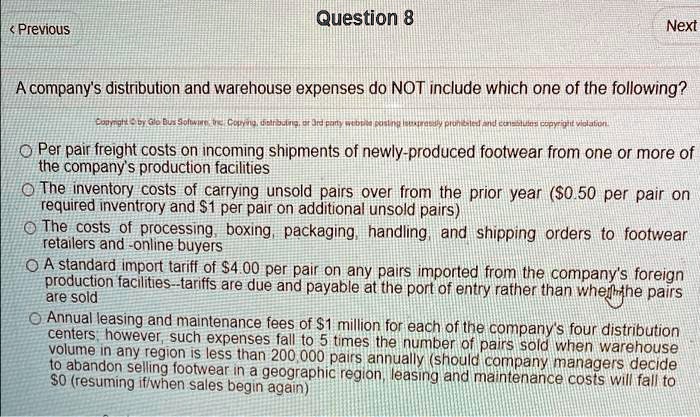
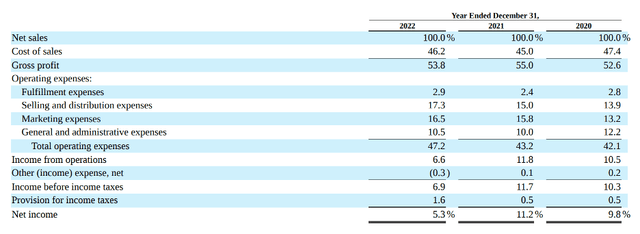



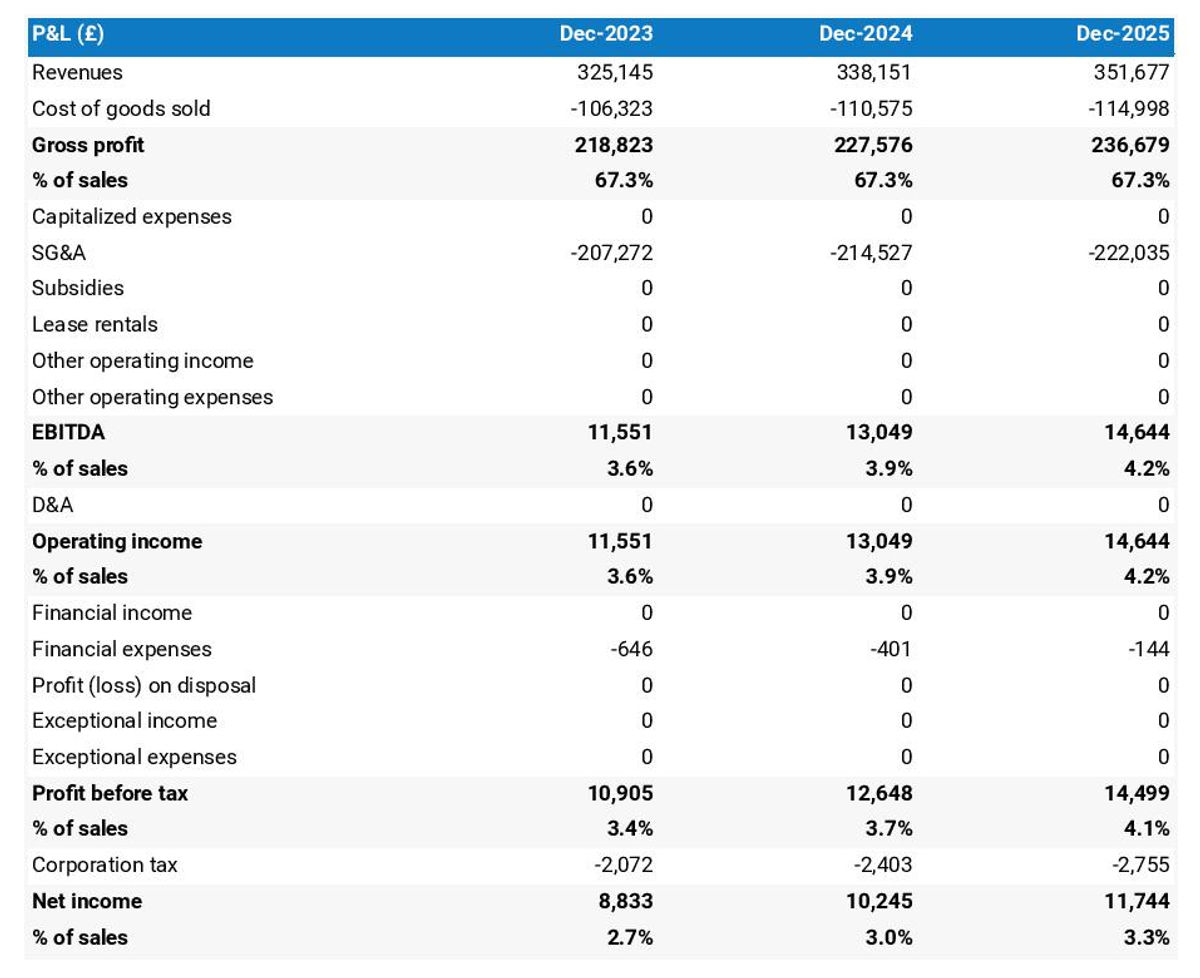