A Product-focused Process Is Commonly Used To Produce
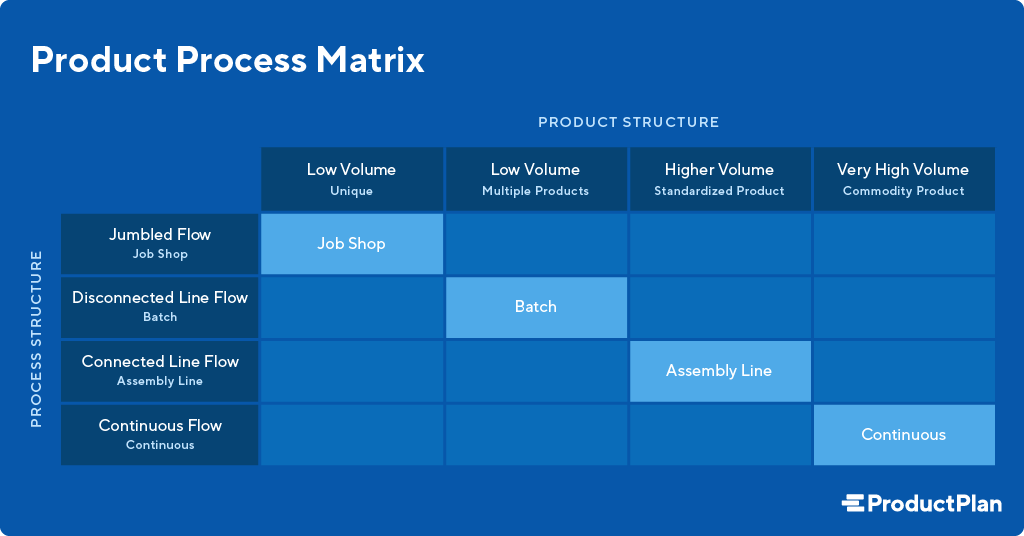
Massive production delays are plaguing industries worldwide, all stemming from a singular source: the pervasive reliance on product-focused processes. This entrenched system, prioritizing individual product features over holistic efficiency, is now buckling under unprecedented global demand.
The product-focused process, designed to optimize individual product characteristics, has inadvertently created bottlenecks across supply chains, manufacturing, and distribution, hindering overall production capacity and driving up costs. Experts warn of escalating economic repercussions if industries fail to adapt.
The Breakdown: How Product Focus Cripples Production
The product-focused process dictates that resources, machinery, and personnel are organized around individual products or product lines. This means separate departments often handle specific features or components, leading to a fragmented production flow and a lack of streamlined efficiency.
For example, a car manufacturer might have separate teams dedicated to engine assembly, chassis construction, and interior design. Each team optimizes its specific area, but the integration between them can be cumbersome and time-consuming.
According to a recent report by the Manufacturing Institute, companies using product-focused processes experience an average of 20% longer lead times compared to those employing process-focused methodologies. This delay is exacerbated by the current global supply chain crisis.
Supply Chain Vulnerabilities Exposed
The product-focused approach intensifies the impact of supply chain disruptions. When components are specific to a single product line, shortages in one area can halt the entire production of that line, even if other components are readily available.
John Peterson, a supply chain analyst at Gartner, stated, "The over-specialization inherent in product-focused processes creates single points of failure. A shortage of a specific chip, unique to one product, can cripple an entire company's output."
This vulnerability contrasts sharply with process-focused systems where resources are more adaptable and can be easily reallocated to different product lines as needed. Flexibility is key, but this system doesn't provide flexibility.
Increased Costs and Reduced Output
The inefficiency of the product-focused process translates directly into higher production costs. Redundant equipment, specialized training for each product line, and increased inventory holding costs all contribute to a significant financial burden.
A study by the Boston Consulting Group found that companies using product-focused processes spend an average of 15% more on production costs compared to companies with process-focused systems.
Furthermore, the lack of integrated workflows leads to reduced overall output. The Manufacturing Productivity Coalition estimates that product-focused processes result in a 10-15% decrease in overall production volume.
Industries Under Pressure: Automotive, Electronics, and Apparel
Several key industries are particularly affected by the shortcomings of the product-focused process. The automotive industry, with its complex supply chains and highly specialized components, is facing significant production slowdowns.
Electronic manufacturers are struggling to meet demand for smartphones, laptops, and other devices due to chip shortages and disruptions in the assembly process. The apparel industry is grappling with increased lead times and rising costs due to the fragmented nature of its supply chain.
Specifically, General Motors reported a 25% decrease in production in the last quarter, citing component shortages and inefficient production workflows. Apple has delayed the launch of several new products due to similar issues.
The Path Forward: Shifting to Process-Focused Systems
Experts are urging companies to transition to process-focused systems to improve efficiency and resilience. This involves reorganizing resources around core processes, such as cutting, assembly, or packaging, rather than individual products.
This shift requires significant investment in technology, employee training, and process optimization. However, the long-term benefits, including increased output, reduced costs, and greater adaptability, outweigh the initial investment.
The National Association of Manufacturers is hosting a series of workshops to help companies understand and implement process-focused methodologies. Early adopters are already seeing significant improvements in their production efficiency and overall profitability. The future is now, and adaptation is critical.

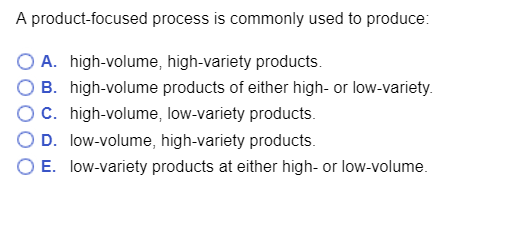


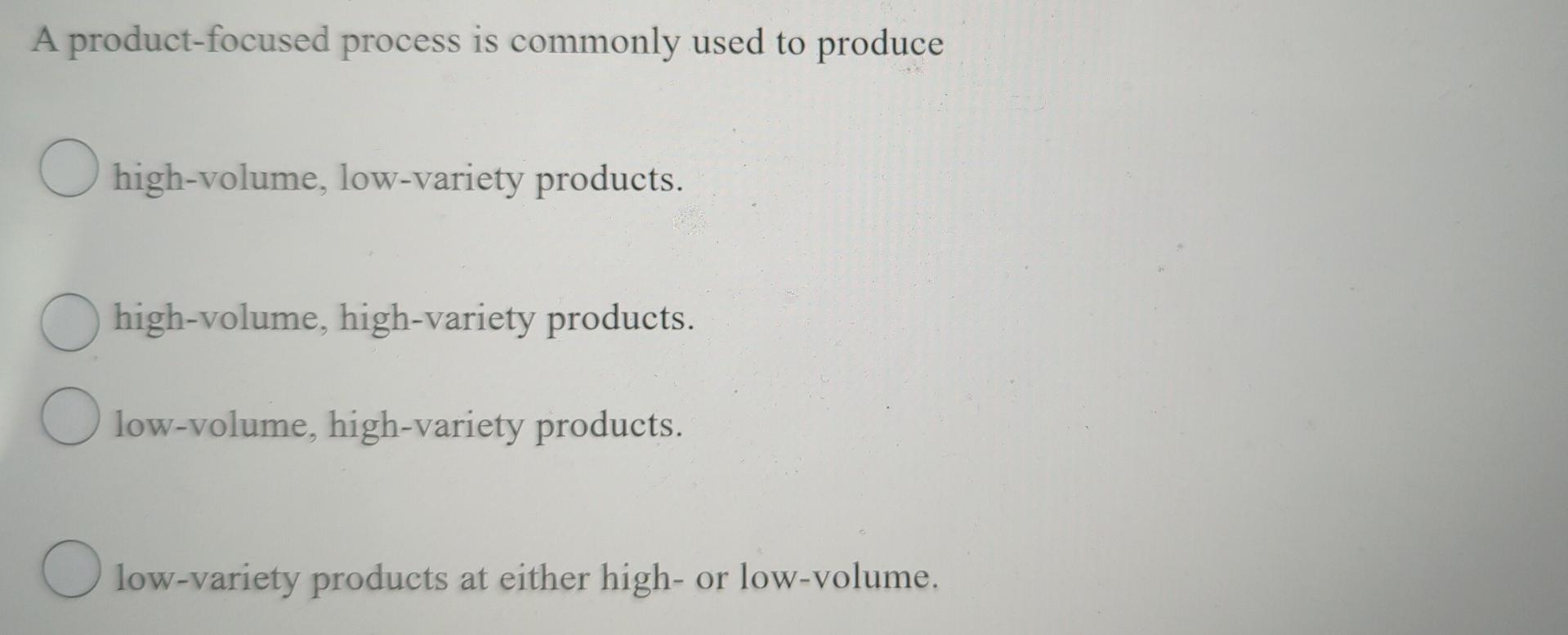

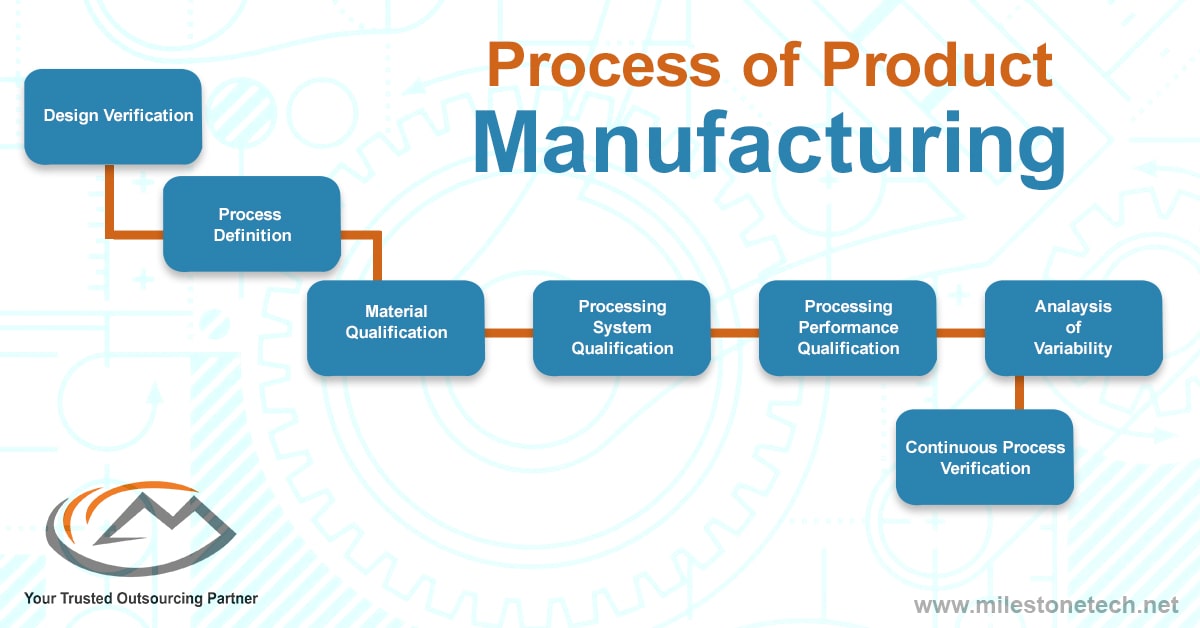
![A Product-focused Process Is Commonly Used To Produce [Solved] 22) A product-focused process is commonly | SolutionInn](https://dsd5zvtm8ll6.cloudfront.net/si.experts.images/questions/2022/12/6393d59d10a5d_8606393d59ccdb64.jpg)

+are+arranged+based+on+the+sequence+of+operations+required+to+produce+a+product+or+provide+a+service..jpg)

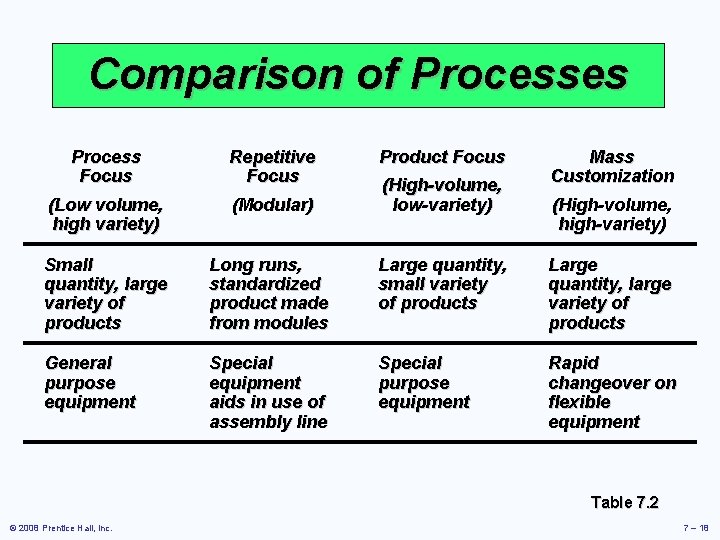





