Difference Between An Agitator And Impeller
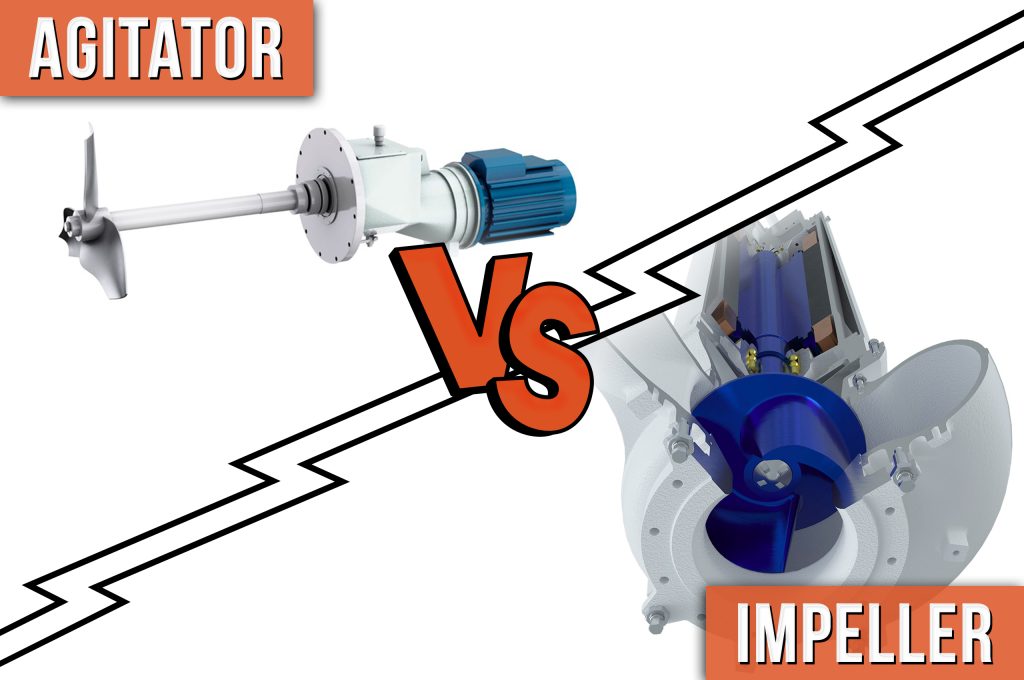
In the world of industrial mixing and processing, the terms agitator and impeller are often used interchangeably, leading to confusion. While both play crucial roles in blending and homogenizing materials, understanding their distinct functions and applications is vital for optimizing processes across various industries, from pharmaceuticals to wastewater treatment.
This article will delve into the core differences between agitators and impellers, clarifying their individual contributions to mixing processes. We will examine their design, application, and impact on efficiency and effectiveness, providing a comprehensive overview for engineers, technicians, and anyone seeking a clearer understanding of these critical components.
Key Distinctions: Agitator vs. Impeller
At the heart of the distinction lies the scope of the term. An agitator is the complete mixing apparatus, the entire system responsible for creating motion and blending materials within a vessel. Think of it as the whole package.
An impeller, on the other hand, is just one component of the agitator. It's the rotating element, the specifically designed blade or set of blades that directly imparts mechanical energy into the fluid, creating flow and promoting mixing.
Essentially, the impeller is the workhorse inside the agitator system. It’s responsible for the actual physical act of moving the fluid.
Anatomy of an Agitator
A typical agitator system comprises several key components. This includes the impeller itself, a shaft that connects the impeller to a motor, a motor that provides the rotational force, and sometimes, supporting structures like baffles within the mixing vessel.
The motor's speed and power are critical factors in determining the intensity of mixing. The shaft's length and material must be selected to withstand the torque and stress generated during operation.
Baffles, strategically placed within the tank, prevent swirling and promote more effective top-to-bottom mixing.
Impeller Types and Their Applications
Impellers come in a diverse range of designs, each tailored for specific mixing tasks. Radial flow impellers, like turbine impellers, generate flow outwards towards the walls of the vessel.
Axial flow impellers, such as propellers and hydrofoils, create flow predominantly downwards or upwards along the axis of the impeller. This type of impeller is often used for suspending solids in liquids.
Each type offers different strengths in terms of shear rate, flow pattern, and power consumption, impacting the overall efficiency of the mixing process.
Impact on Industrial Processes
The appropriate selection of an agitator and impeller is critical for optimizing a wide array of industrial processes. In the pharmaceutical industry, precise mixing is essential for creating homogenous drug formulations.
In the food and beverage industry, agitators and impellers ensure uniform blending of ingredients, preventing separation and maintaining product quality. Wastewater treatment plants rely on agitators to suspend solids and promote biological reactions.
The efficiency of these processes depends heavily on choosing the right impeller type, agitator design, and operating parameters.
Expert Perspectives
According to a leading engineer at MixPro Technologies, a company specializing in mixing solutions, “Understanding the nuanced differences between agitators and impellers allows for precise control over mixing outcomes. It prevents over- or under-mixing, ensures optimal energy efficiency, and improves product quality."
She further stated, "Choosing the wrong impeller can lead to inadequate suspension of solids, poor heat transfer, and increased operating costs. It is essential to carefully consider fluid properties, tank geometry, and desired mixing outcome.”
Data from the American Institute of Chemical Engineers (AIChE) suggests that optimizing mixing processes through proper agitator and impeller selection can lead to significant energy savings and reduced waste in various industries.
Conclusion
While the terms agitator and impeller are often conflated, recognizing their distinct roles is crucial for effective mixing and blending. An agitator is the complete mixing system, while an impeller is the rotating component that imparts energy into the fluid.
Careful consideration of impeller type, agitator design, and operating parameters is essential for optimizing industrial processes, improving product quality, and minimizing energy consumption. The knowledge presented in this article provides a solid foundation for making informed decisions regarding mixing equipment in diverse applications.
By embracing a deeper understanding of these fundamental concepts, industries can unlock new levels of efficiency and effectiveness in their mixing processes, ultimately driving innovation and improving outcomes.


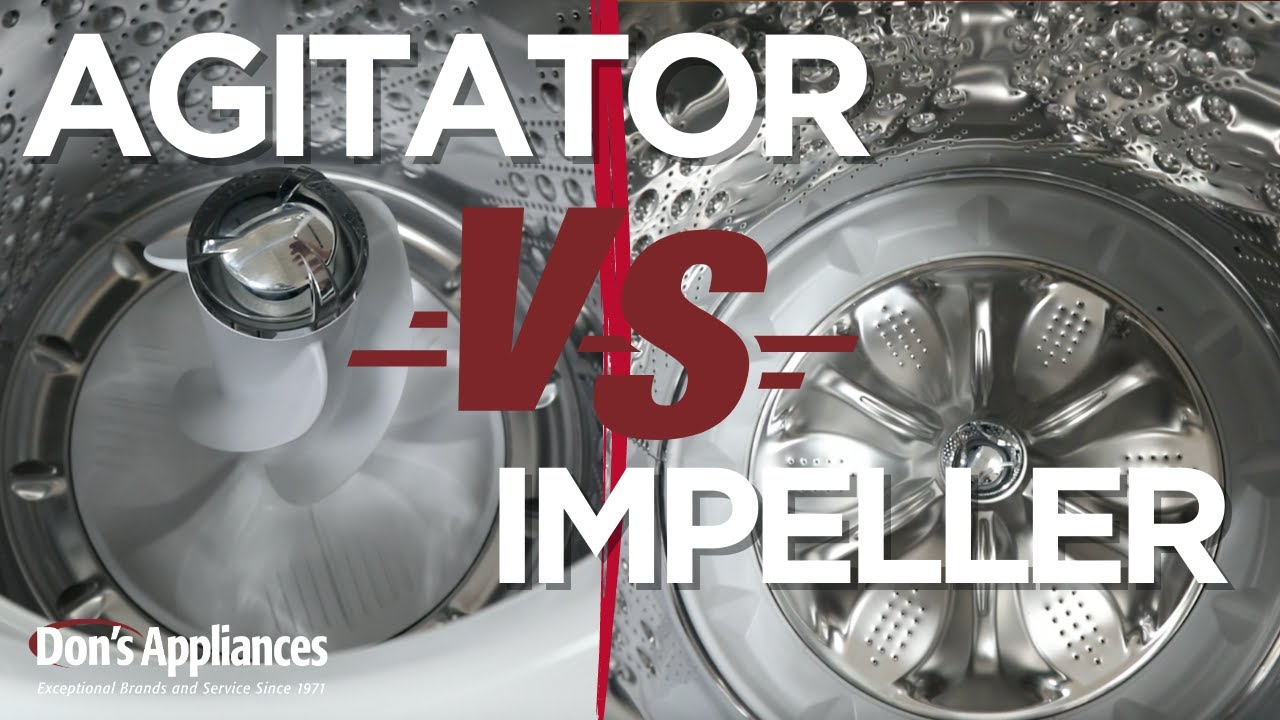
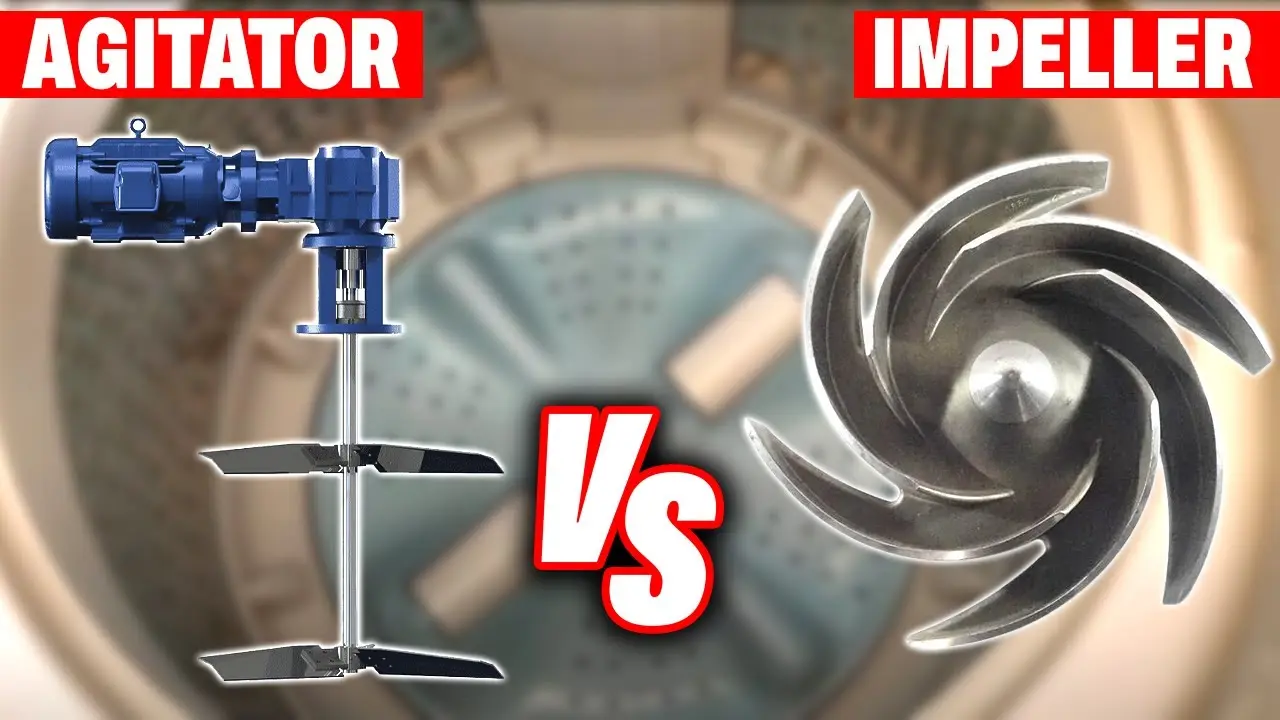



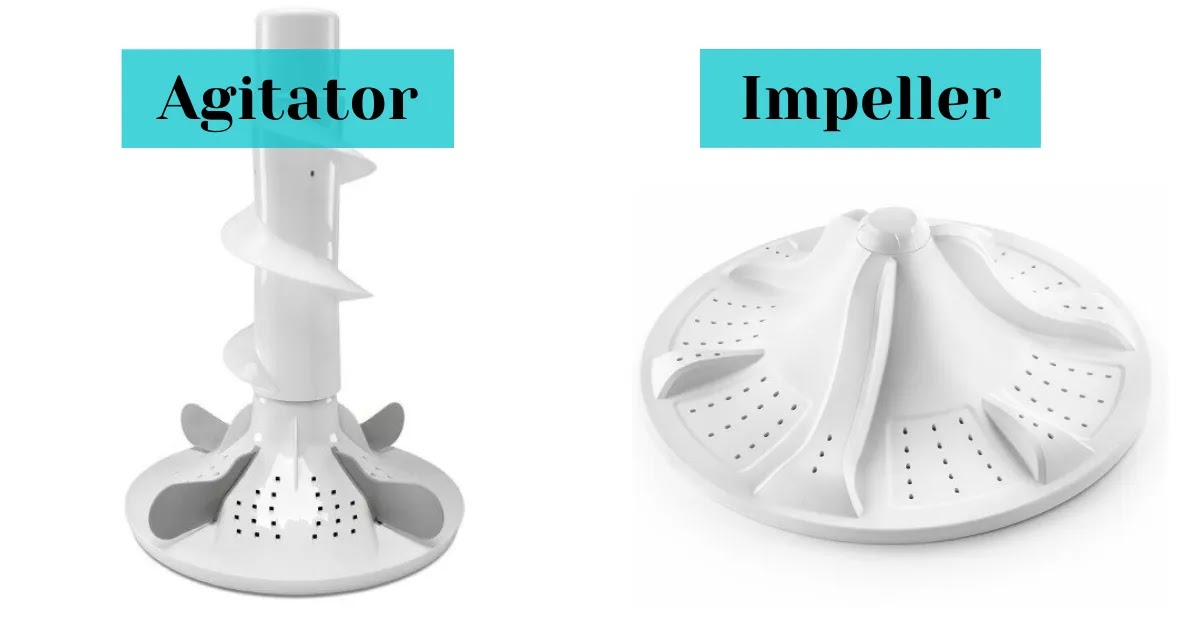
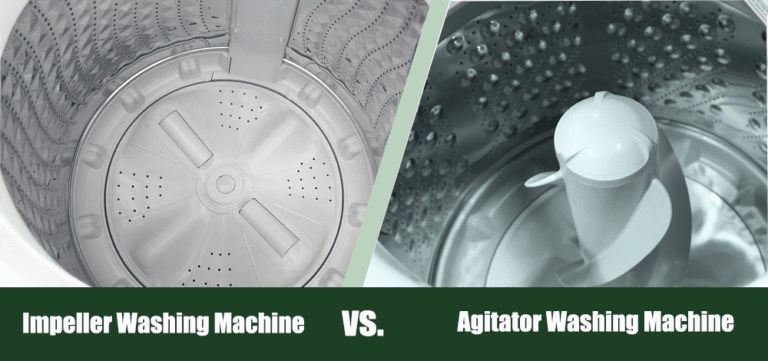
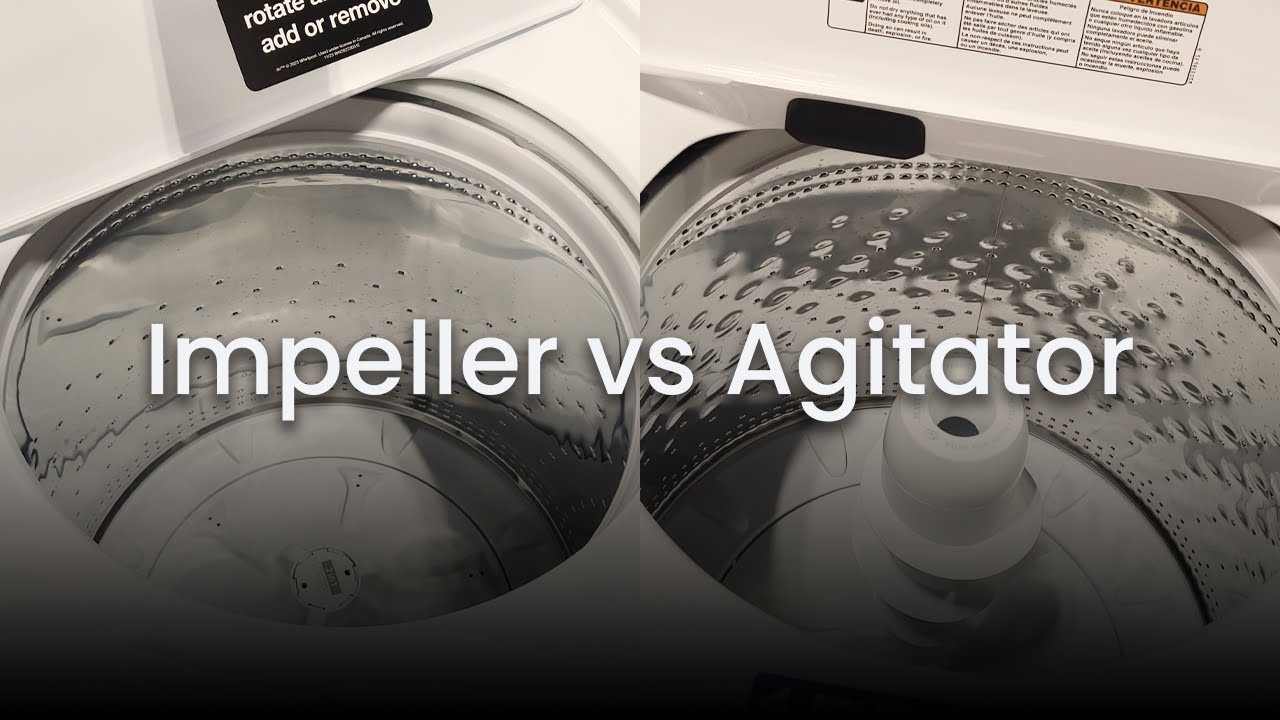

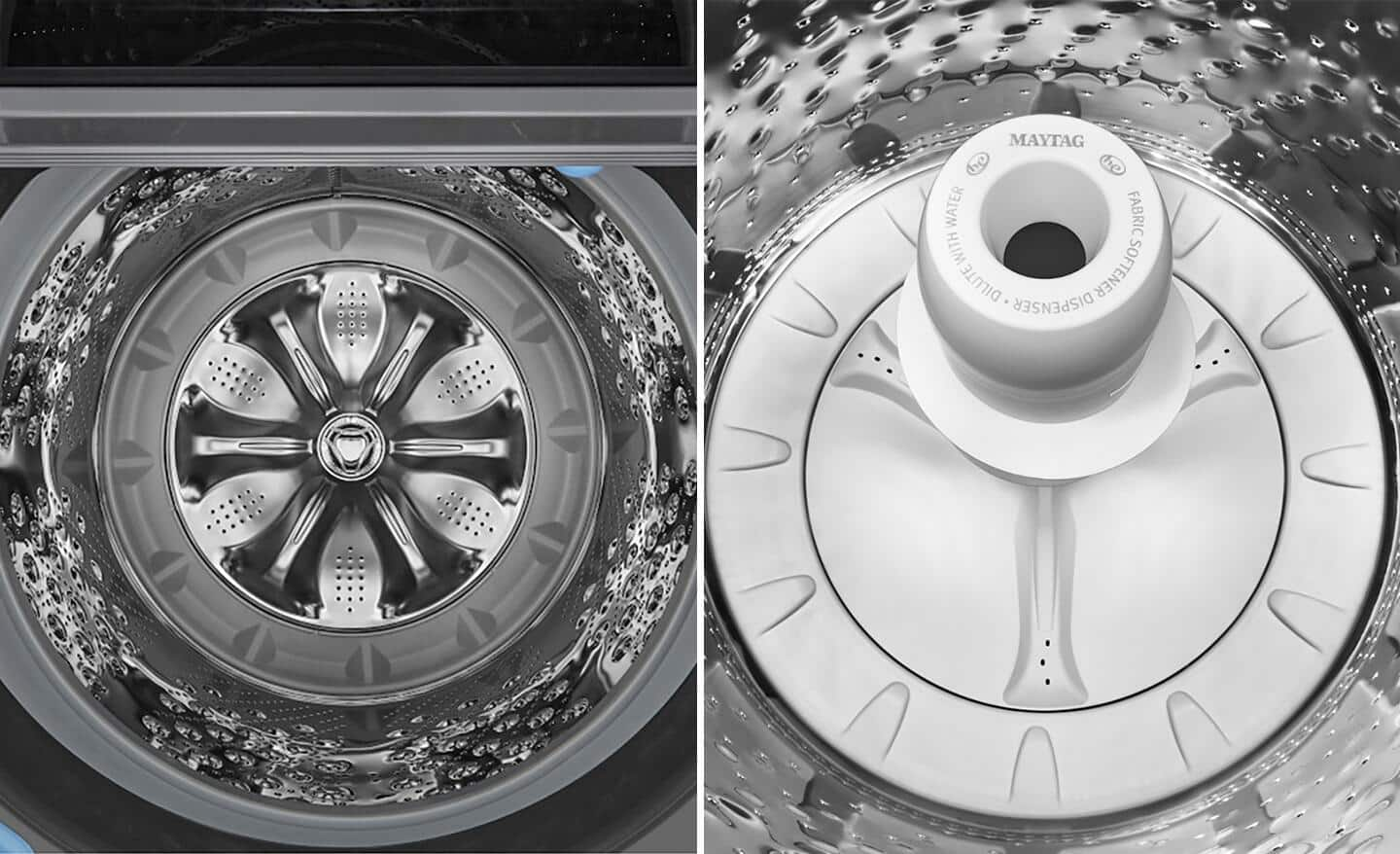

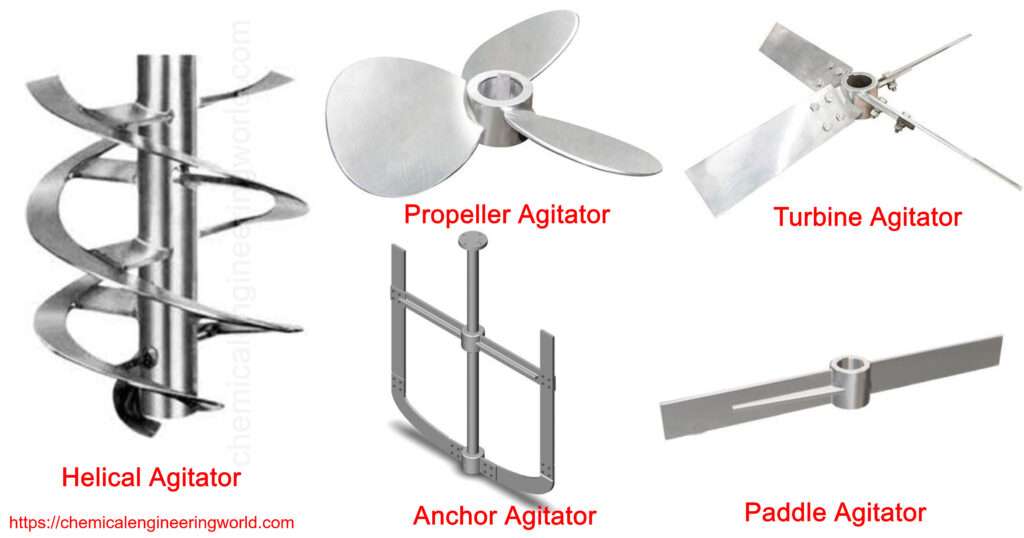
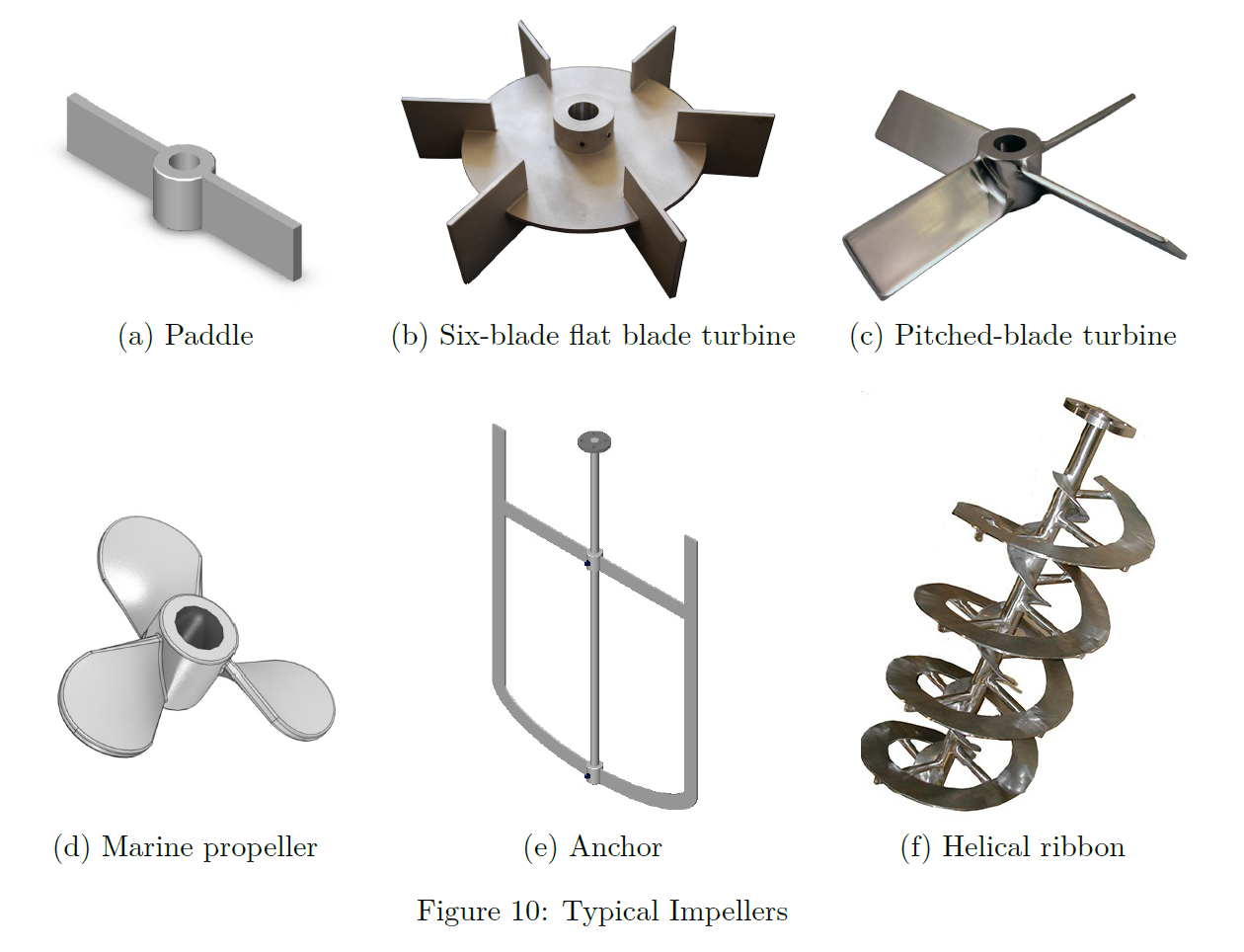
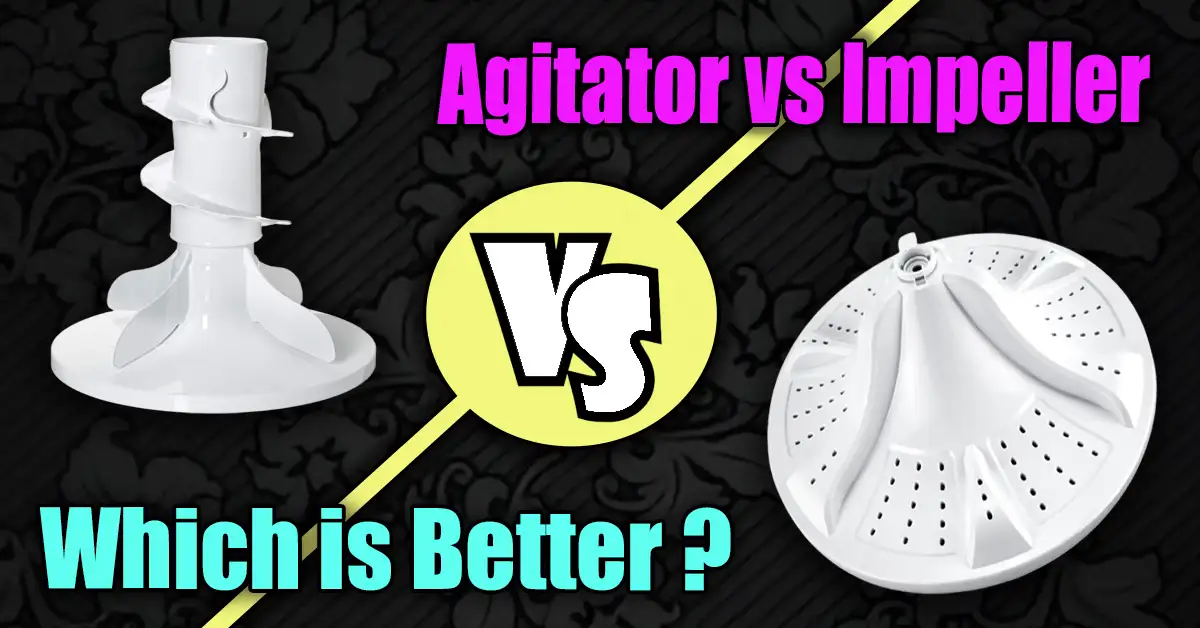
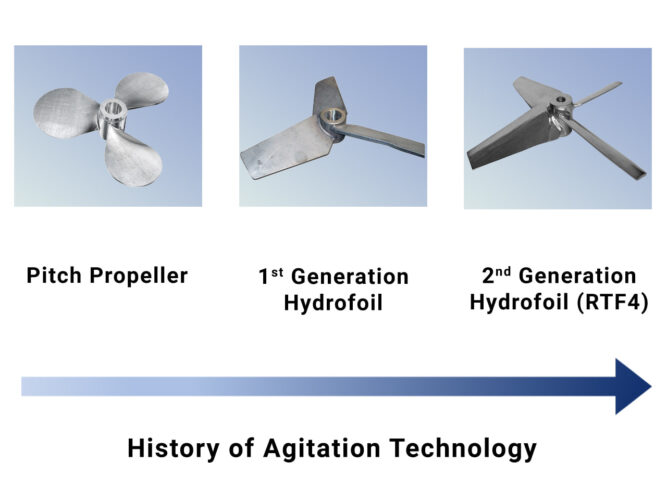
