How To Drill Hole In A Rock
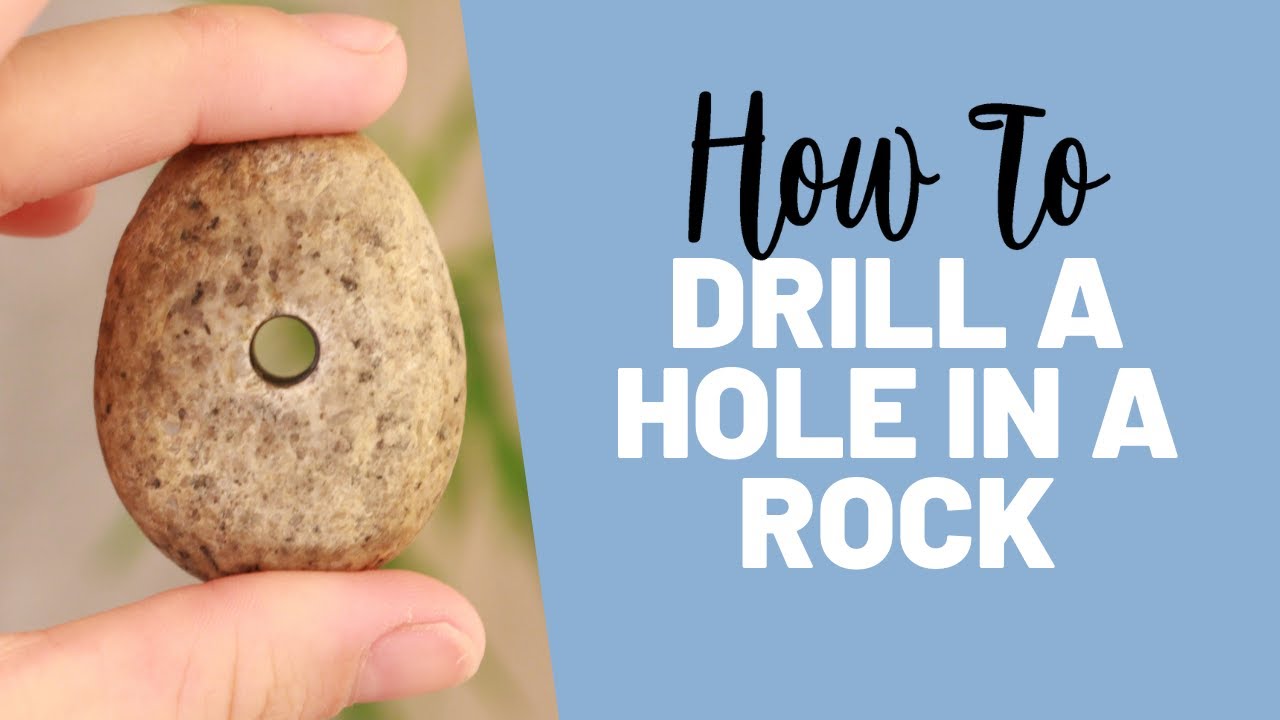
The earth beneath our feet, seemingly immutable, often requires penetration. From geological surveys uncovering the planet’s secrets to construction projects laying the foundations for modern infrastructure, the ability to create holes in rock is a fundamental skill. This process, however, is far from simple, demanding a blend of geological understanding, specialized equipment, and precise technique.
This article delves into the essential methods for drilling holes in rock, providing a comprehensive guide for professionals and enthusiasts alike. We will explore various drilling techniques, equipment considerations, safety precautions, and the geological factors influencing drilling success. Mastering these skills unlocks a wide range of possibilities, enabling exploration, construction, and resource extraction, shaping the world around us.
Understanding the Rock
Before initiating any drilling operation, a thorough understanding of the rock's properties is crucial. Different rock types possess varying hardness, density, and fracture patterns. Igneous rocks like granite, for instance, are typically very hard and require specialized drilling techniques.
Sedimentary rocks, such as sandstone or limestone, are often softer and easier to drill, but may be more prone to fracturing. Metamorphic rocks, like marble or slate, exhibit properties dependent on their formation process and composition. Consulting geological maps and conducting site-specific surveys is essential.
Drilling Techniques
Rotary Drilling
Rotary drilling is a common method, employing a rotating drill bit to grind away the rock. This technique is widely used in construction, mining, and geological exploration. The drill bit's material, usually tungsten carbide or diamond-impregnated, must be harder than the rock being drilled.
The process involves applying downward pressure and rotating the drill bit, creating cuttings that are flushed away by water, air, or drilling mud. Different types of rotary drilling exist, including tricone drilling, which uses a three-cone roller bit for crushing the rock.
Percussion Drilling
Percussion drilling utilizes a hammering action to fracture the rock. This method is particularly effective for hard and brittle rock formations. The drill bit is repeatedly struck against the rock, creating small fractures that eventually form a hole.
Pneumatic drills, often called jackhammers, are a common example of percussion drilling equipment. Hydraulic percussion drills offer increased power and control, making them suitable for demanding applications.
Diamond Core Drilling
Diamond core drilling is a specialized technique used to extract cylindrical rock samples, known as cores. This method is frequently employed in geological surveys and mineral exploration. The drill bit is a hollow cylinder with diamonds embedded in its cutting edge.
As the drill rotates, it cuts through the rock, leaving a solid core sample within the cylinder. This core provides valuable information about the rock's composition, structure, and properties.
Thermal Drilling
Thermal drilling utilizes intense heat to weaken or melt the rock. This technique is less common than mechanical drilling methods. However, it can be effective in certain situations.
Flame jet drilling uses a high-temperature flame to spall or fracture the rock surface. Laser drilling employs a focused laser beam to vaporize the rock material. Both methods offer potential advantages in specific geological conditions.
Equipment Considerations
Selecting the appropriate drilling equipment is crucial for success. The choice depends on the rock type, hole diameter, depth, and desired precision. Drill rigs vary in size and power, ranging from handheld drills to large, truck-mounted units.
The drill bit is the primary cutting tool, and its material and design must be carefully selected. Tungsten carbide bits are suitable for softer rocks, while diamond bits are necessary for harder formations. Drilling fluids, such as water, air, or drilling mud, play a vital role in cooling the drill bit, removing cuttings, and stabilizing the borehole.
Safety Precautions
Drilling operations can be hazardous, and safety should always be a top priority. Workers must wear appropriate personal protective equipment (PPE), including safety glasses, gloves, and hearing protection. Ensuring proper ventilation is crucial to prevent the build-up of dust and harmful gases.
Before drilling, a thorough site assessment should identify potential hazards, such as underground utilities or unstable rock formations. Regular equipment maintenance is essential to prevent malfunctions and accidents. Properly training personnel on safe drilling practices is paramount.
Geological Factors
The geological context significantly influences the drilling process. Rock strength, fracture density, and groundwater conditions can all impact drilling efficiency and stability. Highly fractured rock may require specialized techniques to prevent borehole collapse.
Groundwater infiltration can complicate drilling operations, requiring the use of drilling mud or other stabilization methods. Understanding the geological structure and potential hazards is crucial for planning a safe and effective drilling program.
Emerging Technologies
Advancements in drilling technology are continuously improving efficiency and precision. Automated drilling systems, controlled by computer programs, offer increased accuracy and reduced human error. Remote-controlled drilling rigs allow operators to work from a safe distance, minimizing exposure to hazards.
Sensor technology is being integrated into drilling equipment to monitor rock properties in real-time. This data can be used to optimize drilling parameters and improve overall performance.
Conclusion
Drilling holes in rock is a complex and multifaceted process, requiring a blend of geological knowledge, technical expertise, and a commitment to safety. By understanding the different drilling techniques, equipment considerations, and geological factors, professionals and enthusiasts can approach drilling projects with confidence. Continued innovation in drilling technology promises to further enhance efficiency and precision, unlocking new possibilities in exploration, construction, and resource extraction for years to come.





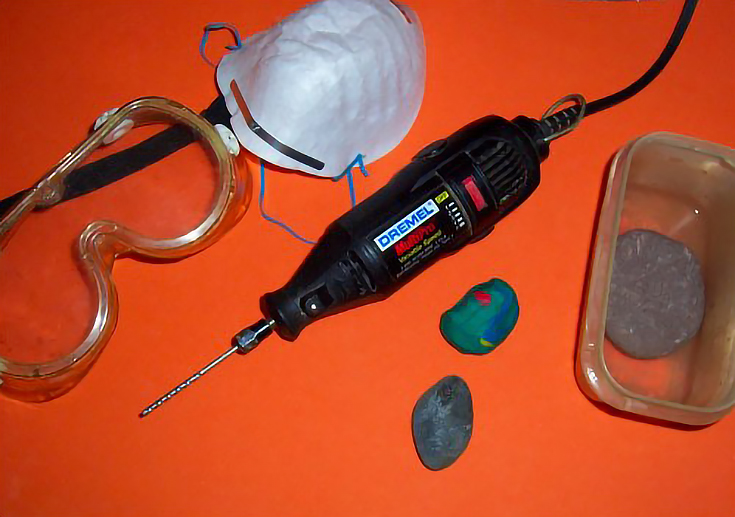
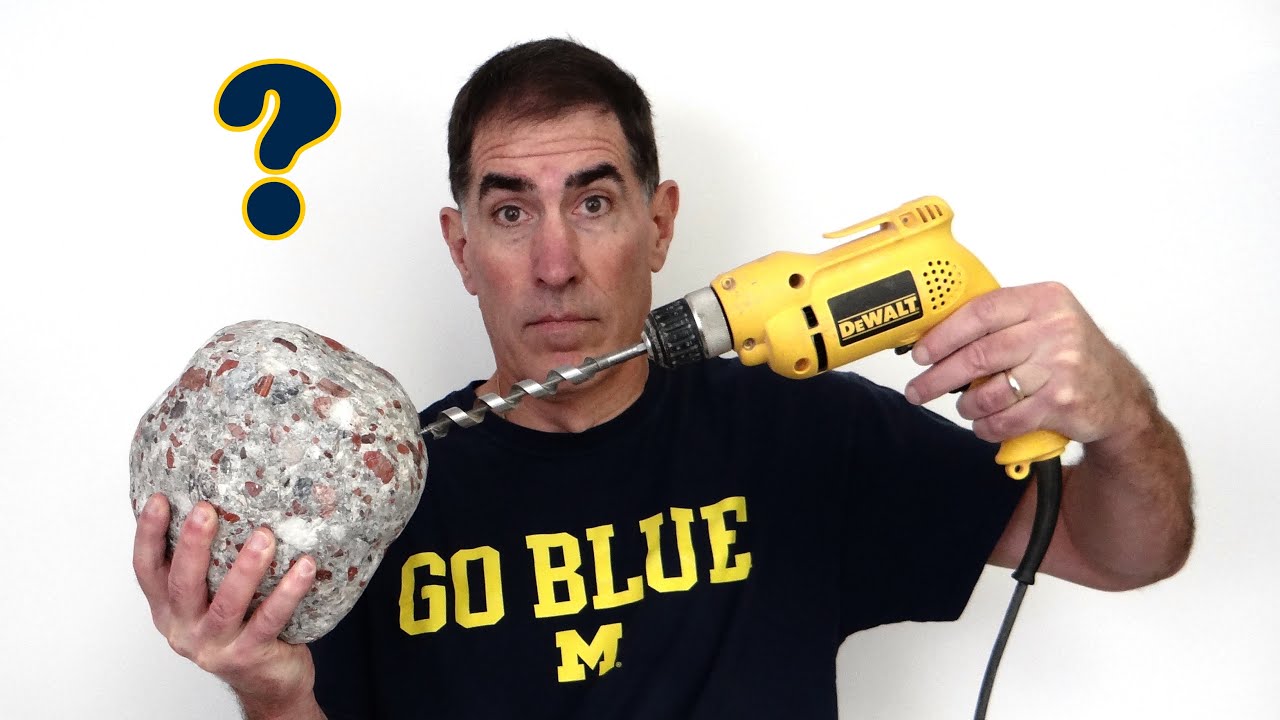

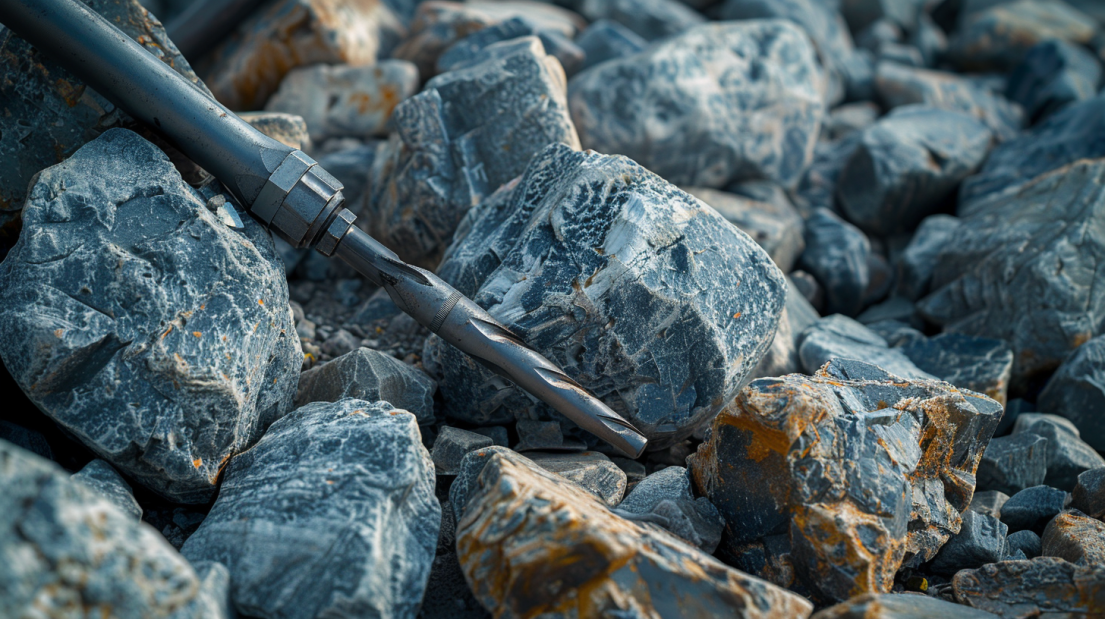
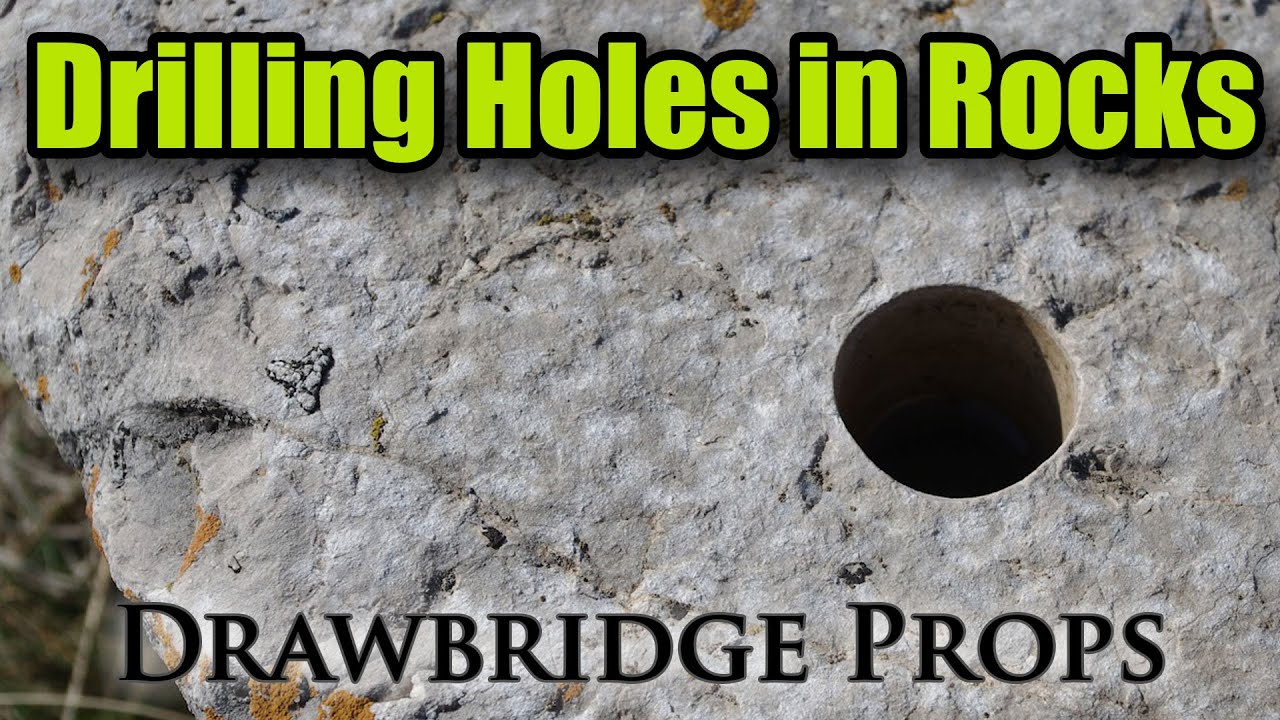






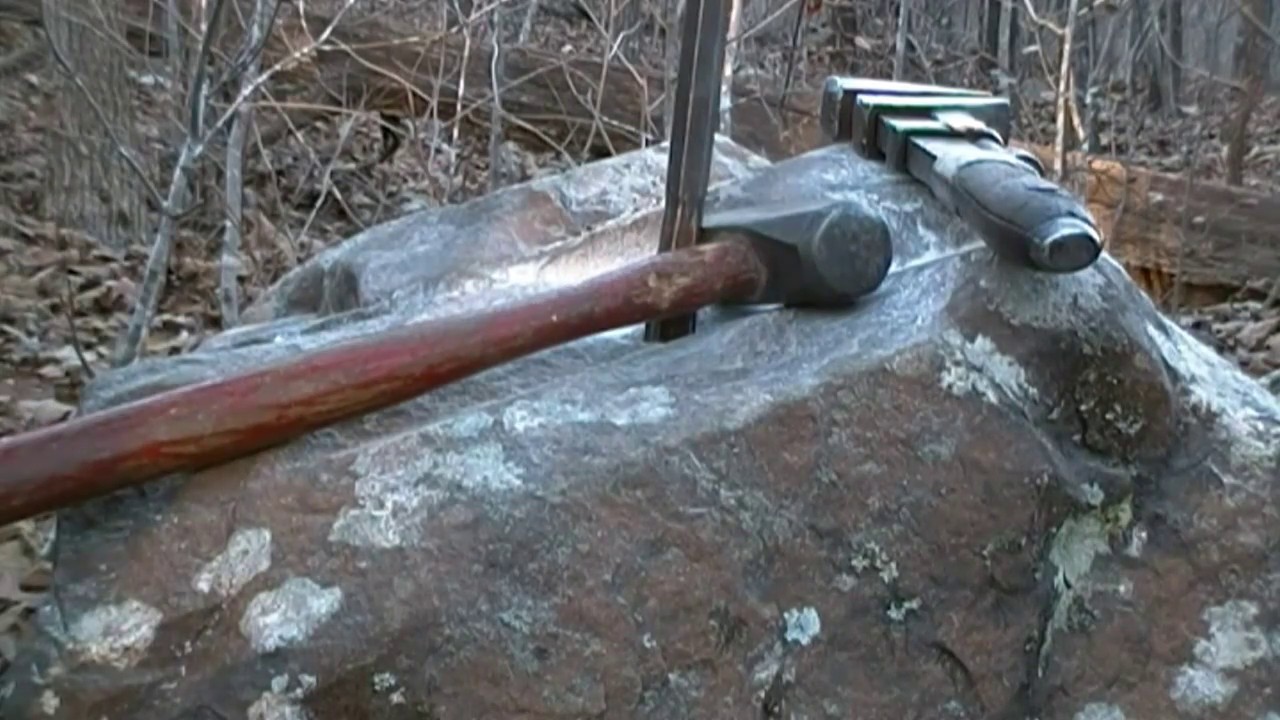
