Minimum Requirements For 3d Printing

The 3D printing revolution, once confined to niche industrial applications, has exploded into mainstream consciousness. From hobbyists crafting personalized figurines to manufacturers prototyping complex parts, the technology's accessibility is undeniable. However, the ease of entry can be deceptive, masking a complex web of minimum requirements crucial for successful and safe 3D printing endeavors. Ignoring these foundational elements can lead to wasted materials, faulty prints, and even hazardous situations, prompting a closer look at the absolute necessities for participating in this transformative technology.
This article delves into the critical minimum requirements for engaging in 3D printing, examining hardware, software, materials, environmental considerations, and essential safety protocols. Understanding these core elements is paramount for anyone, from casual users to professional engineers, aiming to harness the power of additive manufacturing effectively and responsibly. We will explore both fused deposition modeling (FDM) and resin-based printing, highlighting the distinct requirements of each, while also considering the overarching prerequisites for success.
Hardware Essentials: The Foundation of Creation
At the heart of any 3D printing setup lies the printer itself. While a plethora of models exist, the fundamental requirements remain consistent: a stable build platform, a reliable extrusion or resin curing system, and precise motion control. For FDM printers, a heated bed is often indispensable, especially when working with materials like ABS that are prone to warping.
Resin printers, on the other hand, require a high-resolution screen, powerful UV light source, and a well-sealed enclosure to contain fumes. Calibration is absolutely essential across all 3D printer types. Without proper calibration, even the best printer will produce inaccurate and ultimately unusable parts.
Beyond the Printer: Essential Peripherals
The printer is not a standalone device. Essential peripherals include a computer with sufficient processing power to run slicing software, tools for removing prints (scrapers, spatulas), and storage solutions for filament or resin. Adequate ventilation is absolutely crucial, particularly when working with materials that emit fumes.
Software Requirements: Translating Ideas into Reality
Slicing software acts as the bridge between a digital design and the physical printer. These programs translate 3D models into a series of instructions (G-code) that the printer can understand. Cura, PrusaSlicer, and Simplify3D are popular options, each offering varying levels of control and customization.
Beyond slicing, access to 3D modeling software is typically necessary. While pre-designed models are readily available online, creating custom designs requires proficiency in programs like Tinkercad (for beginners), Fusion 360, or Blender. Understanding the software's capabilities and limitations is vital to ensure your models are printable.
Material Considerations: Choosing the Right Medium
The choice of material significantly impacts the final product's properties and the printing process itself. PLA, a biodegradable thermoplastic, is a popular choice for beginners due to its ease of use and relatively low printing temperature. However, it lacks the strength and heat resistance of materials like ABS or PETG.
Resin printing offers even greater material variety, with options ranging from standard resins to those designed for high strength, flexibility, or even dental applications. Understanding material properties like tensile strength, elongation at break, and glass transition temperature is crucial for selecting the appropriate material for a given application. Furthermore, certain resins, like those with specialized properties (e.g., biocompatible or castable resins), may require specialized printer settings and post-processing techniques.
Environmental Factors: Maintaining Optimal Conditions
Environmental conditions play a critical role in 3D printing success. Temperature fluctuations, humidity, and drafts can all negatively impact print quality. Maintaining a stable ambient temperature is especially important for FDM printing, as it helps to prevent warping and cracking.
Resin printing is particularly sensitive to light exposure. Resin should be stored in opaque containers and shielded from direct sunlight. Proper ventilation is also critical, as many resins emit volatile organic compounds (VOCs) that can be harmful if inhaled.
Safety First: Protecting Yourself and Your Environment
3D printing, while generally safe, presents certain hazards that must be addressed. FDM printers can reach high temperatures, posing a burn risk. Resin printing involves handling potentially toxic chemicals.
Always wear appropriate personal protective equipment (PPE), including gloves and eye protection, when handling resins. Ensure adequate ventilation in the printing area to minimize exposure to fumes. Dispose of waste materials properly, following local regulations.
According to the Environmental Protection Agency (EPA), improper disposal of certain 3D printing materials can lead to environmental contamination. It's crucial to research and adhere to best practices for material disposal.
Looking Ahead: The Future of 3D Printing Accessibility
As 3D printing technology continues to evolve, we can expect to see further simplification and increased accessibility. Manufacturers are developing more user-friendly software, printers with automated calibration systems, and materials with wider printing windows.
However, a foundational understanding of the core requirements discussed above will remain essential for anyone seeking to truly master this transformative technology. Continued education, responsible material handling, and a commitment to safety will pave the way for a future where 3D printing empowers individuals and industries alike to innovate and create without limits.
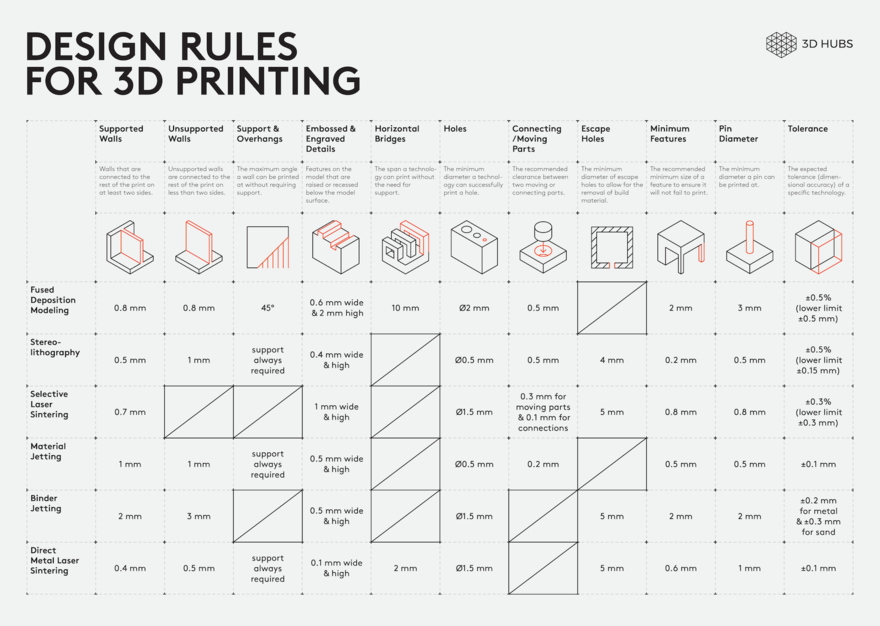

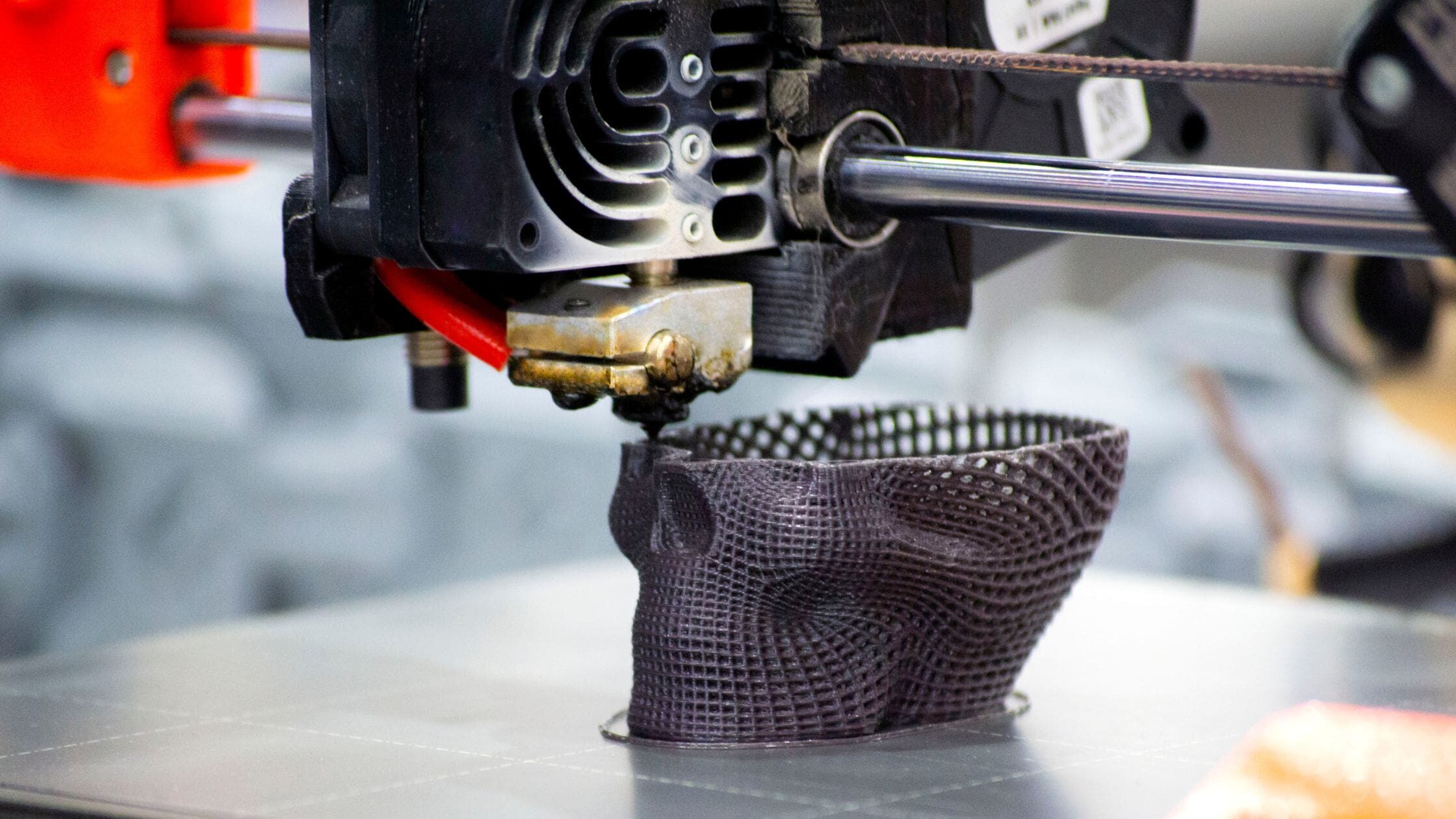
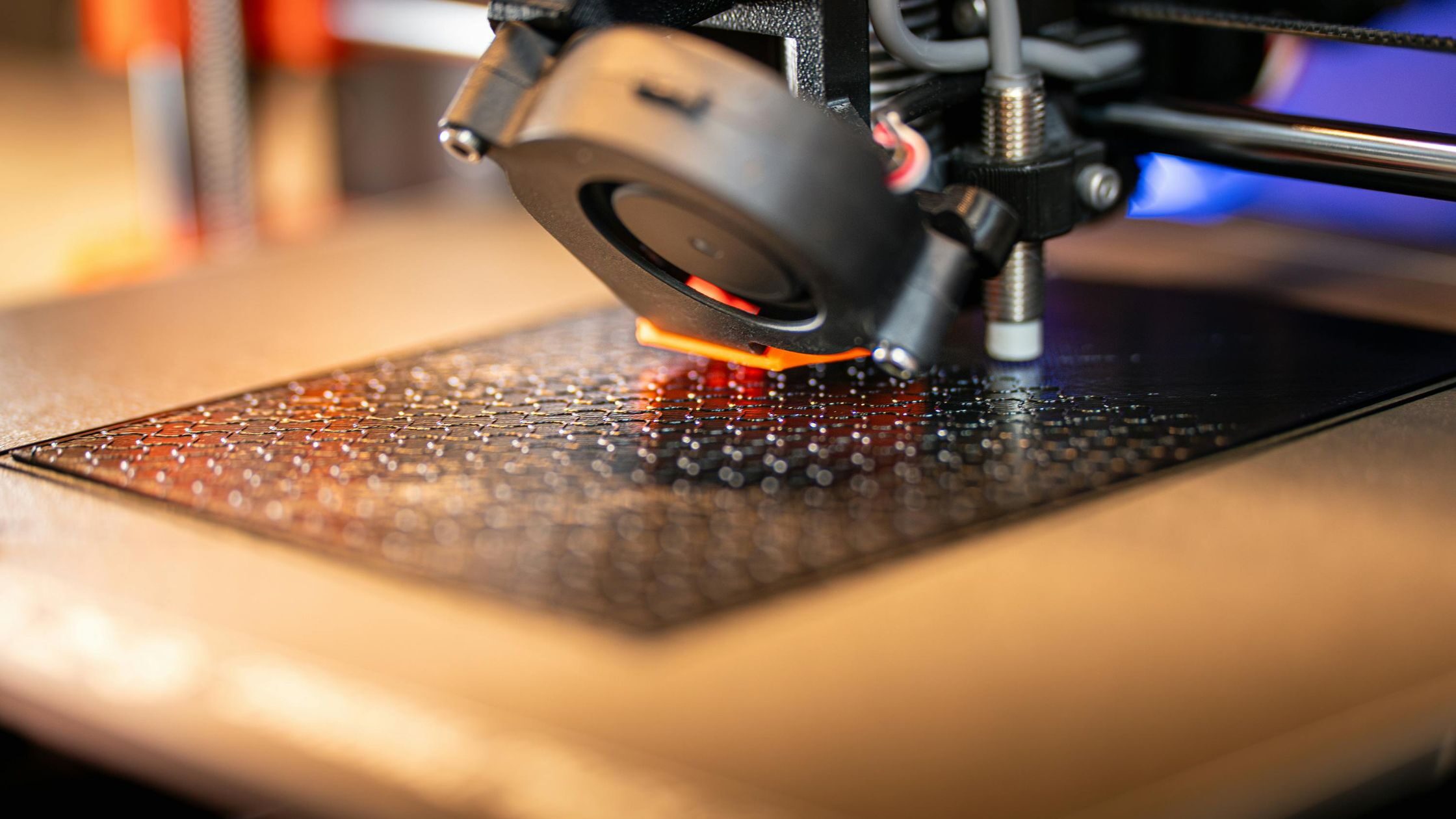
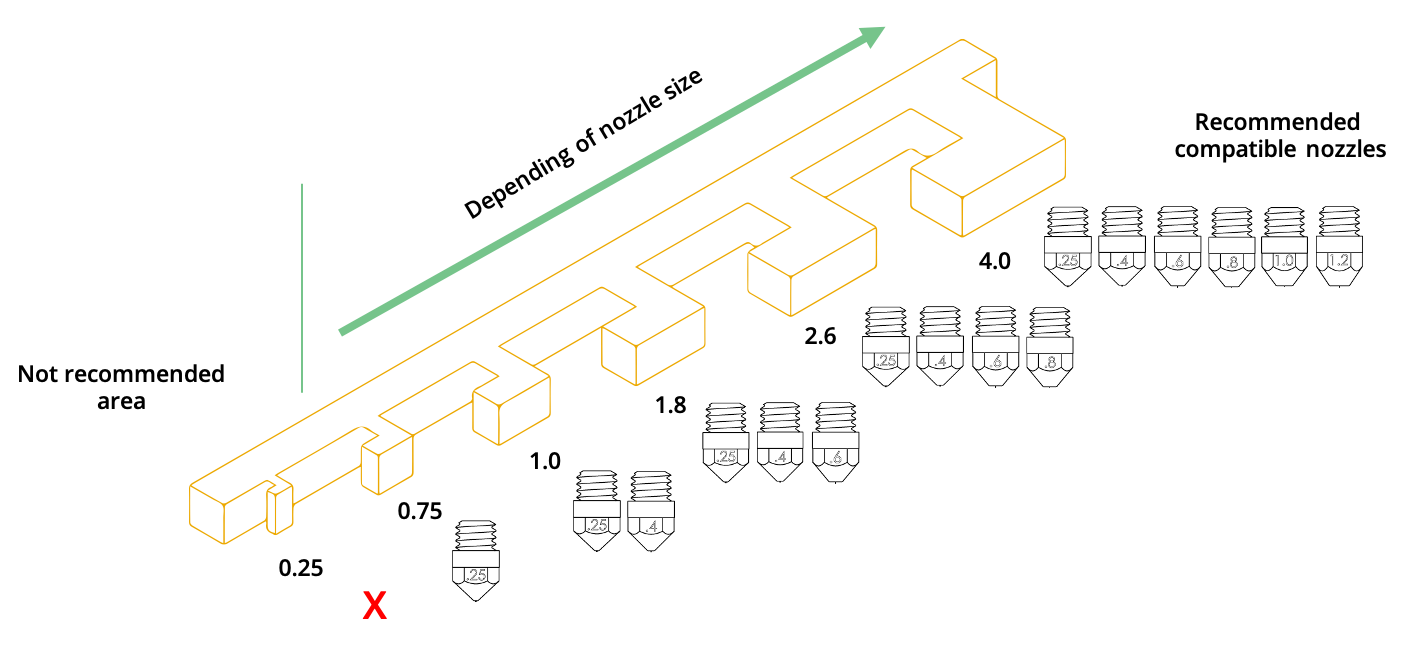



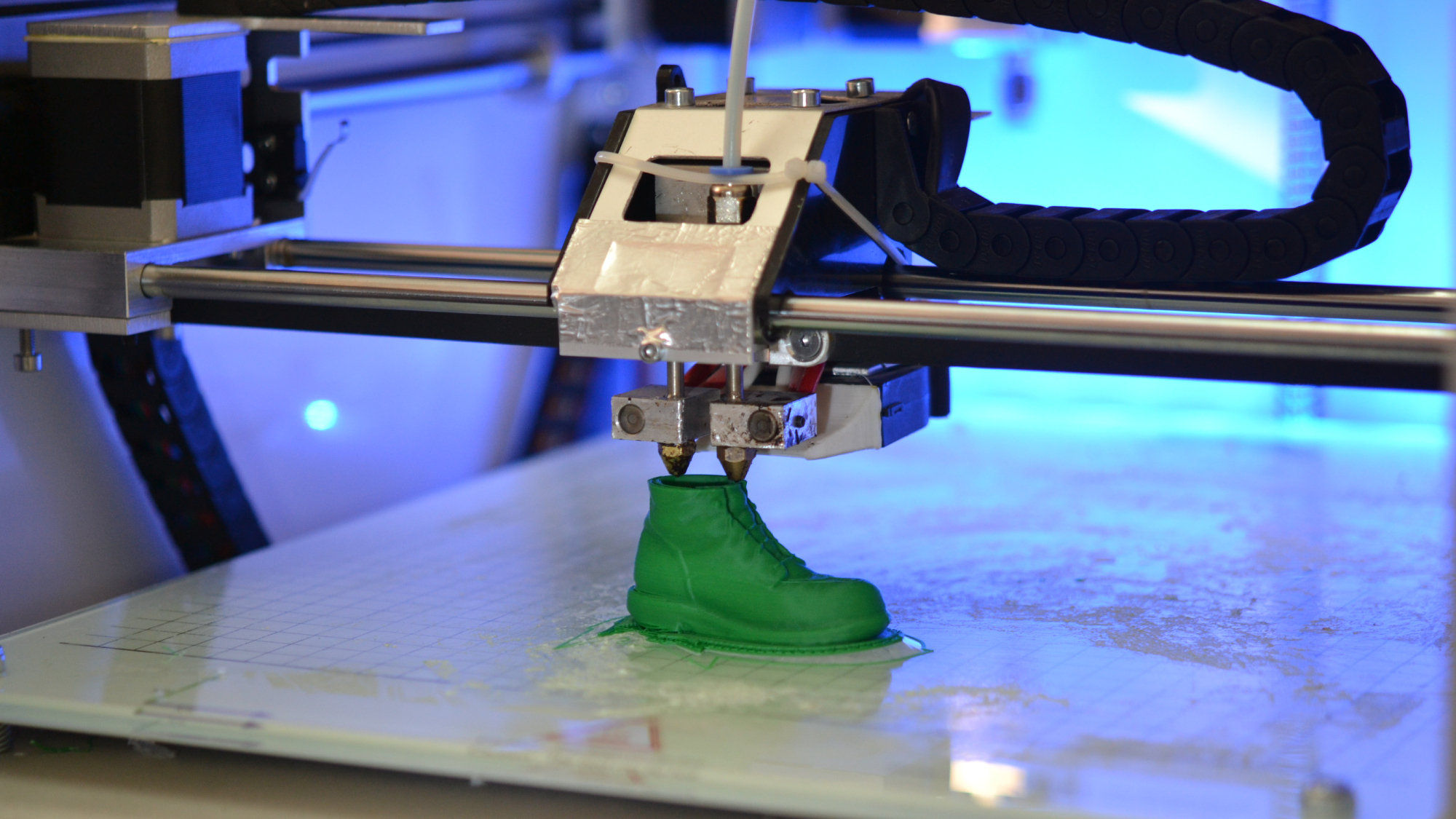
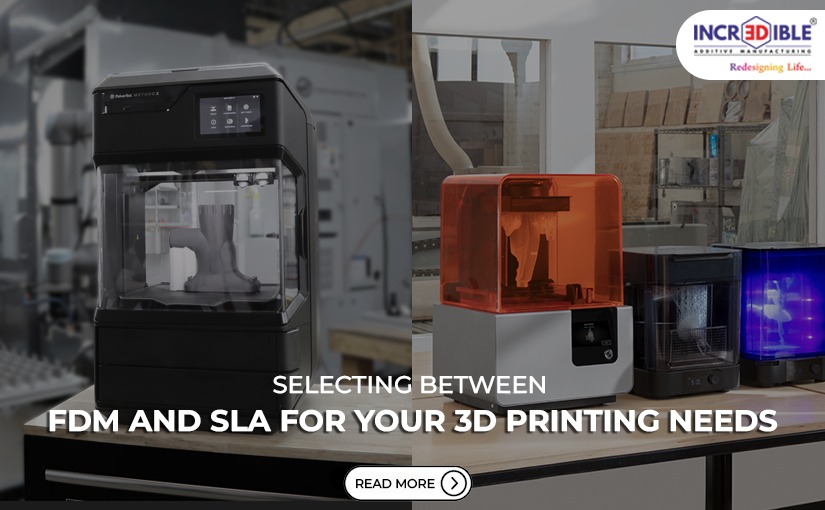
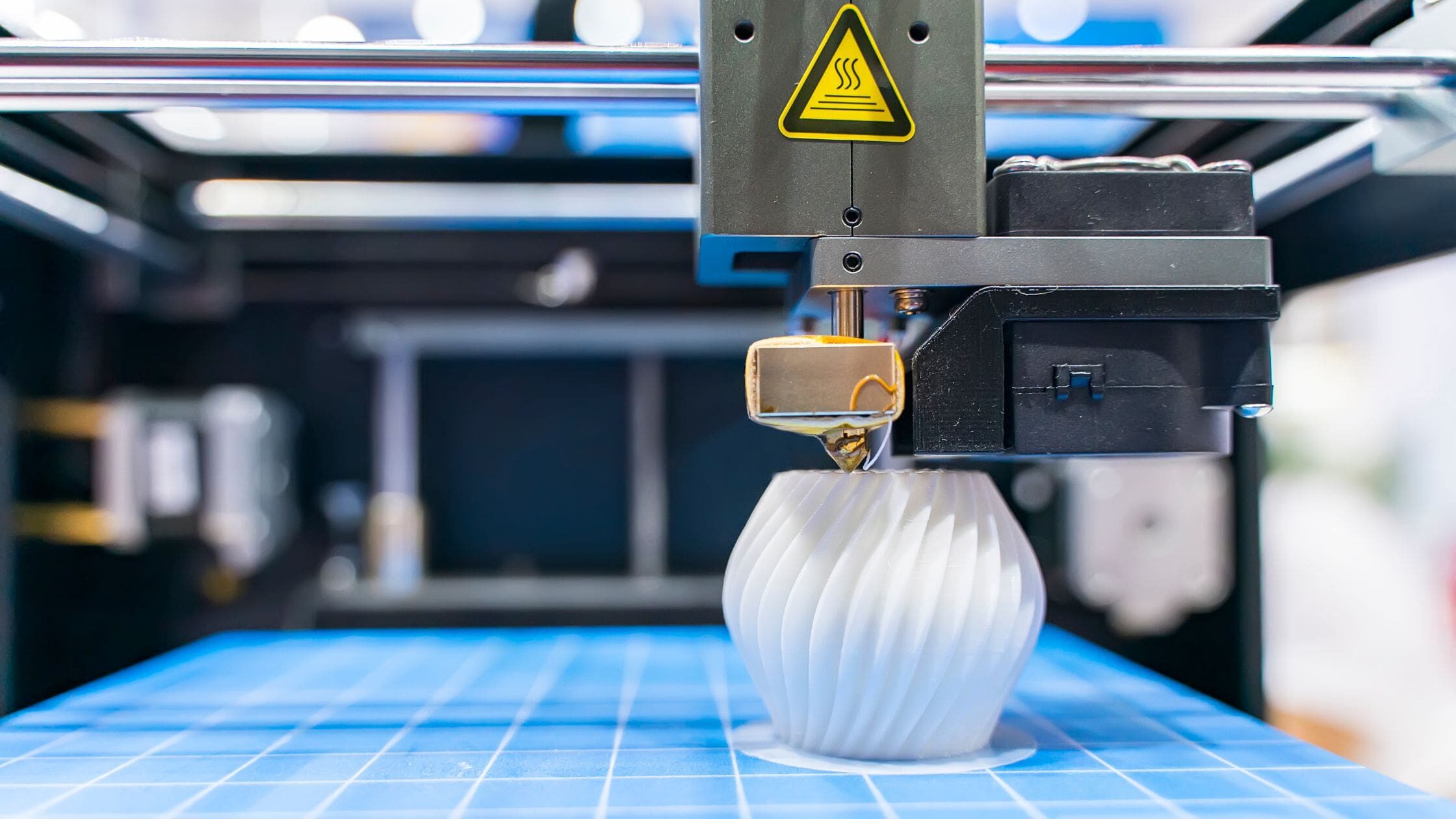
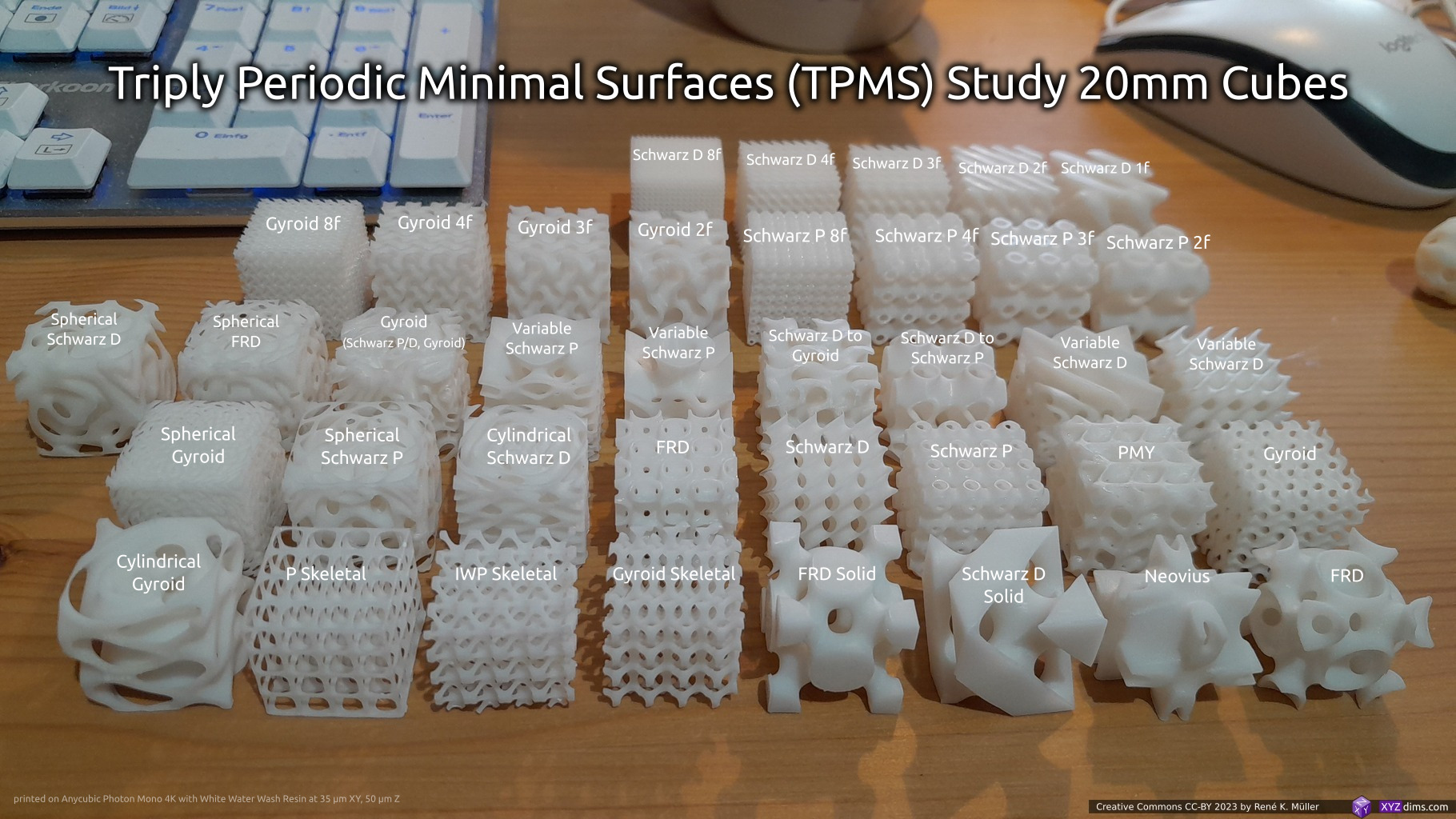
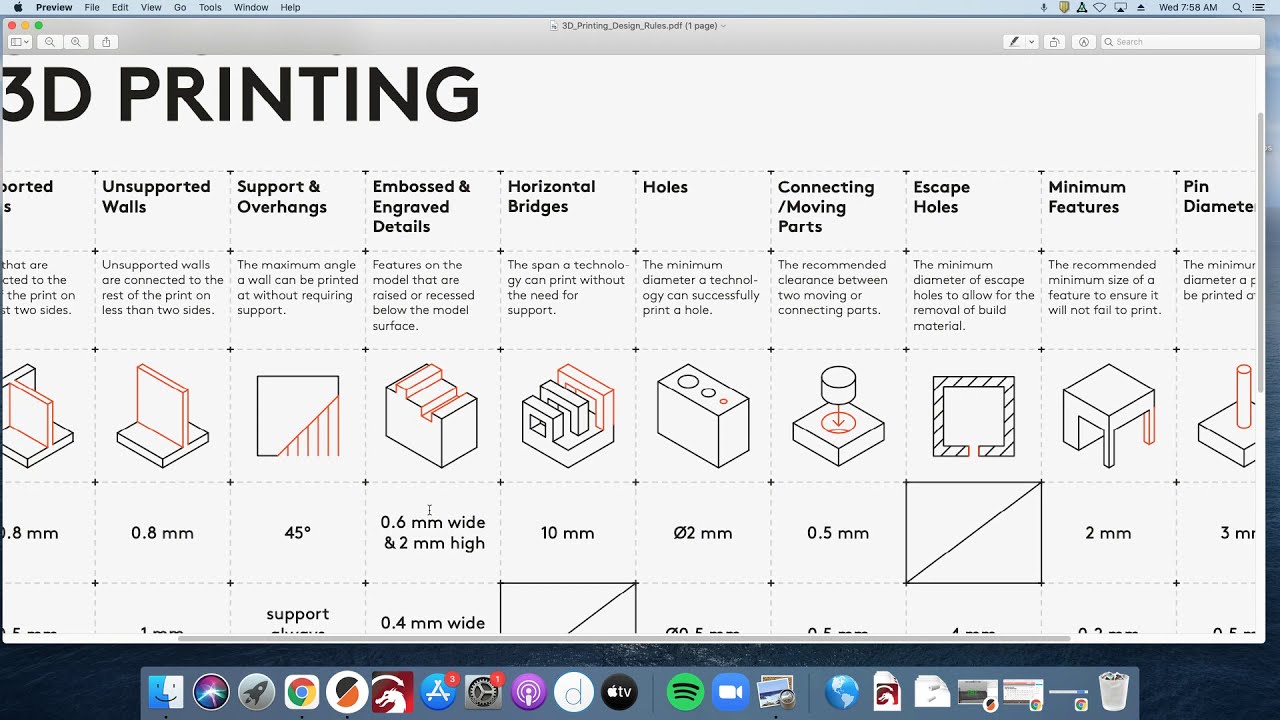

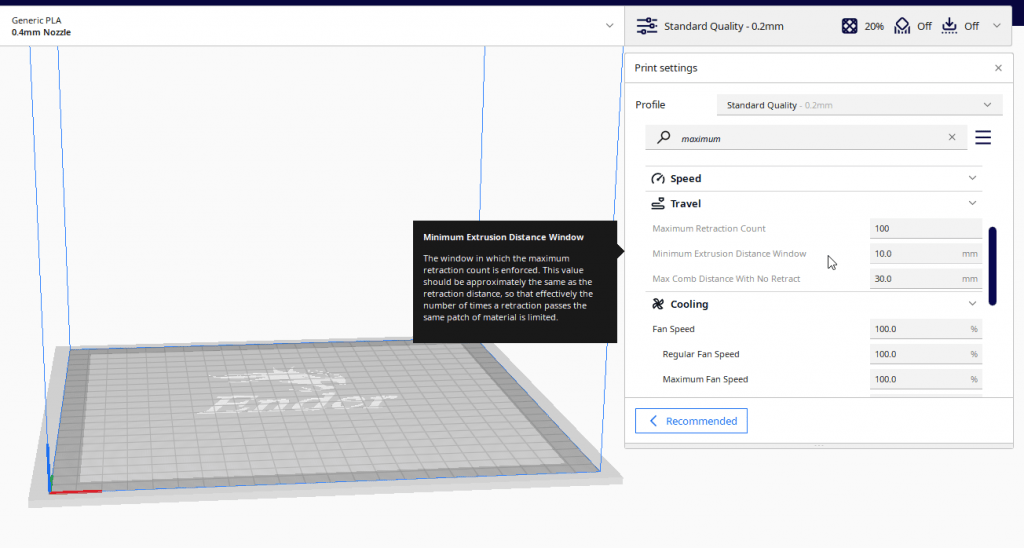


