Newport News Shipbuilding 3d Printing Manifold
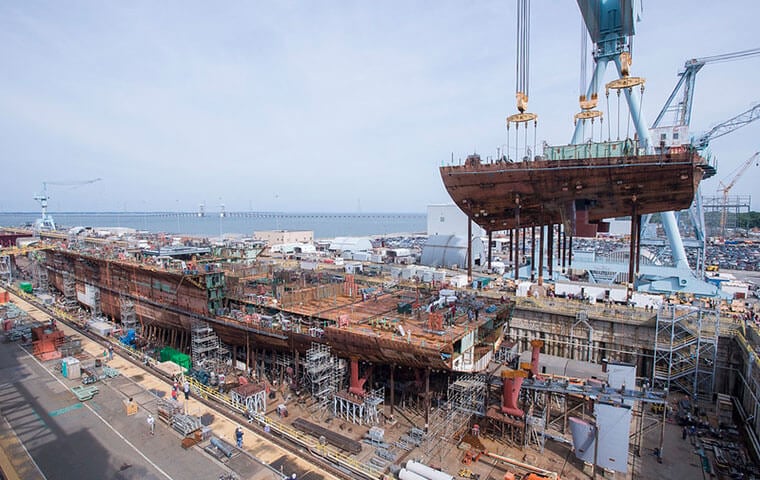
The future of shipbuilding is being forged in Newport News, Virginia, one layer of titanium at a time. Newport News Shipbuilding (NNS), a division of Huntington Ingalls Industries, has successfully 3D printed a critical component for the U.S. Navy: a complex manifold for a submarine.
This achievement marks a significant step towards integrating additive manufacturing, also known as 3D printing, into the core of naval vessel construction and maintenance. It promises faster production times, reduced costs, and potentially enhanced performance for the next generation of submarines.
The successful 3D printing of the manifold signals a pivotal shift in naval manufacturing. It offers a pathway to overcome traditional manufacturing limitations. It opens the door for highly customized and intricate components, leading to more efficient and resilient vessels.
Unlocking the Potential of Additive Manufacturing
At the heart of this breakthrough is the technology of 3D printing, or additive manufacturing. This process builds three-dimensional objects from a digital design. It does so by layering materials such as metals, plastics, ceramics, or composites.
NNS has invested heavily in research and development to harness the potential of additive manufacturing. The goal is to transform how submarines are built and maintained. This investment is paying off with the successful printing of the manifold.
The Manifold: A Complex Component
The manifold is a critical component in a submarine's fluid systems. It acts as a central distribution hub. It precisely controls the flow of liquids or gases throughout the vessel.
Traditionally, manifolds are manufactured using subtractive methods, such as machining and welding. These processes can be time-consuming, wasteful, and limit the design complexity.
3D printing offers a solution to these challenges. It allows for the creation of highly complex geometries with internal channels and optimized flow paths. This is often impossible to achieve using conventional methods.
Advantages of 3D Printing for Shipbuilding
The adoption of 3D printing in shipbuilding presents a multitude of advantages. It allows for the creation of complex geometries, reduced lead times, and decreased material waste. The benefits extend beyond simply replicating existing parts.
Reduced Lead Times: Traditional manufacturing processes for complex components can take months, or even years. 3D printing significantly reduces this timeframe, enabling faster production and deployment of vessels.
Cost Savings: While the initial investment in 3D printing technology can be substantial, the long-term cost savings are significant. Reduced material waste, streamlined production processes, and lower labor costs contribute to a lower overall cost per part.
Design Optimization: 3D printing allows engineers to design and manufacture components with optimized performance characteristics. This includes improved fluid flow, reduced weight, and enhanced structural integrity.
Supply Chain Resilience: By producing parts on-demand, 3D printing reduces reliance on traditional supply chains. It also mitigates the risk of delays due to material shortages or geopolitical instability.
Naval Sea Systems Command's Perspective
The Naval Sea Systems Command (NAVSEA) is actively supporting the integration of additive manufacturing into naval shipbuilding. They recognize its potential to revolutionize the way naval vessels are designed, built, and maintained.
“Additive manufacturing has the potential to transform naval shipbuilding by enabling faster production, reduced costs, and enhanced performance,” stated a NAVSEA spokesperson. They also highlighted the command's commitment to investing in research and development. The goal is to accelerate the adoption of this technology across the fleet.
NAVSEA is working closely with industry partners, such as Newport News Shipbuilding, to develop standards and certifications for 3D printed components. This ensures quality and reliability for critical applications.
Challenges and Future Directions
Despite the immense potential, there are challenges to overcome before 3D printing can be fully integrated into shipbuilding. These include material qualification, process control, and workforce development.
Material Qualification: Rigorous testing and certification are required to ensure that 3D printed materials meet the stringent performance requirements of naval applications. This involves characterizing the mechanical properties, corrosion resistance, and fatigue life of 3D printed components.
Process Control: Maintaining consistent quality in 3D printing requires precise control of the printing process. This includes monitoring temperature, humidity, and material flow. It also requires sophisticated software and hardware to ensure accurate layer deposition.
Workforce Development: A skilled workforce is essential for the successful implementation of 3D printing. This requires training engineers, technicians, and operators in the principles of additive manufacturing, design for additive manufacturing, and process control.
The Path Forward
Newport News Shipbuilding is continuing to invest in research and development to address these challenges. They are working closely with universities, government agencies, and industry partners. The goal is to advance the state of the art in additive manufacturing.
Expanding Applications: NNS plans to expand the use of 3D printing to other critical components. These include propulsion system parts, hull structures, and internal fixtures.
Integrating AI and Machine Learning: NNS is exploring the use of artificial intelligence (AI) and machine learning (ML) to optimize the 3D printing process. This can lead to improved quality, reduced waste, and faster production times.
A New Era for Naval Shipbuilding
The successful 3D printing of the manifold by Newport News Shipbuilding represents a major milestone. It marks a transition towards a new era of naval shipbuilding.
Additive manufacturing holds the key to unlocking greater efficiency, innovation, and resilience in the construction and maintenance of naval vessels. This capability is crucial for maintaining U.S. naval dominance in the 21st century.
As 3D printing technology continues to advance, its impact on naval shipbuilding will only grow. The future of the U.S. Navy is being built, one layer at a time, in Newport News.

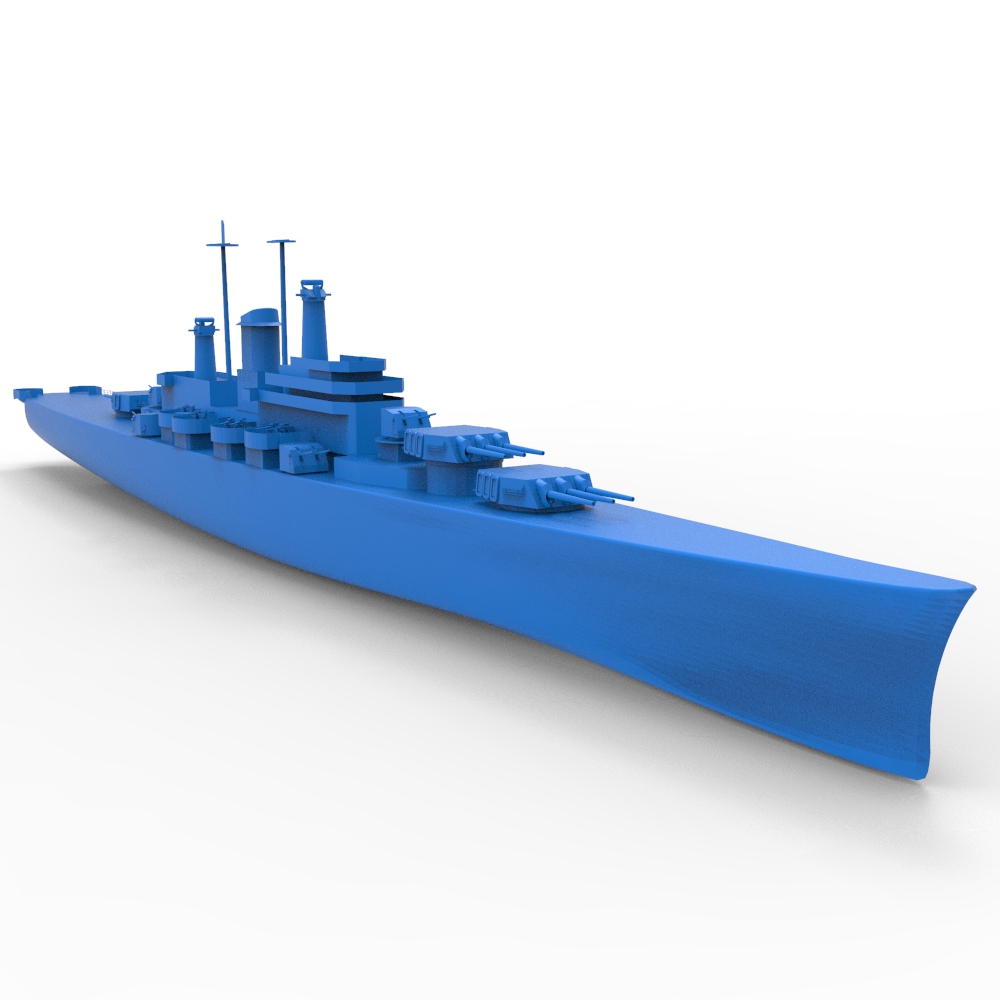

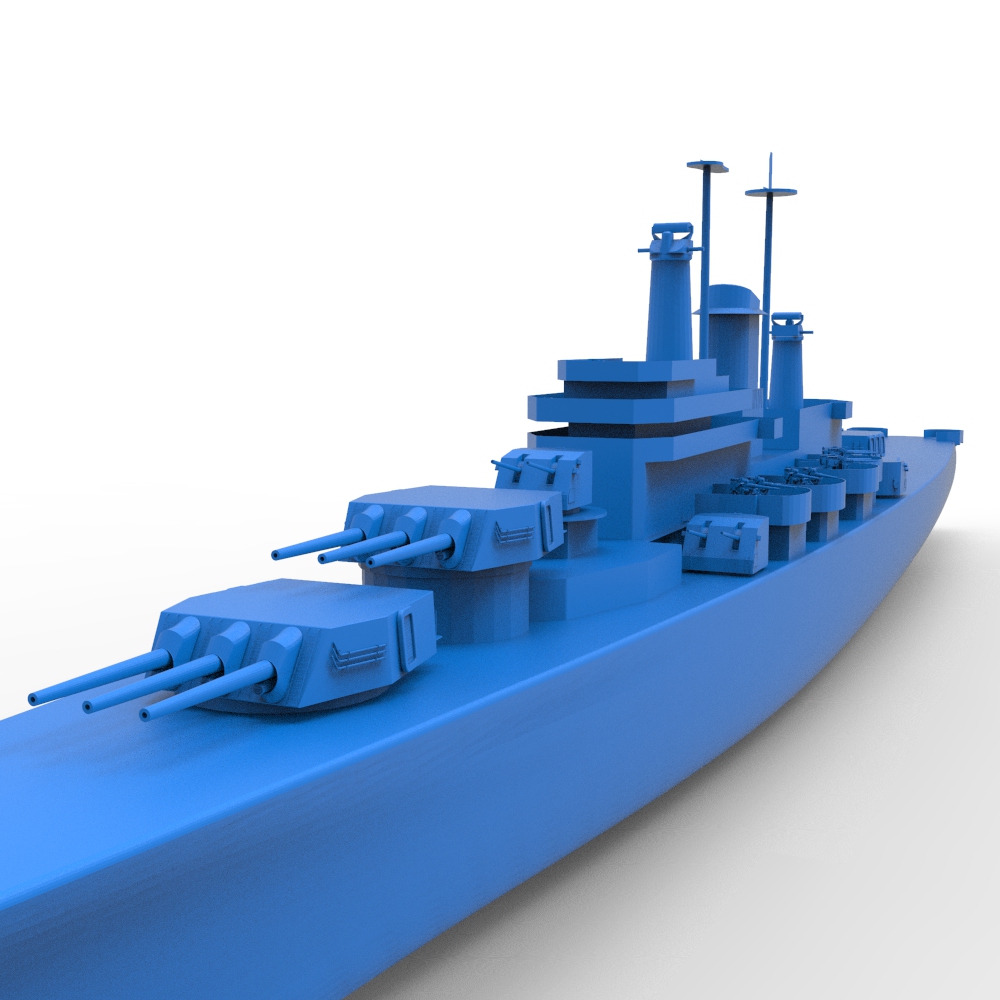
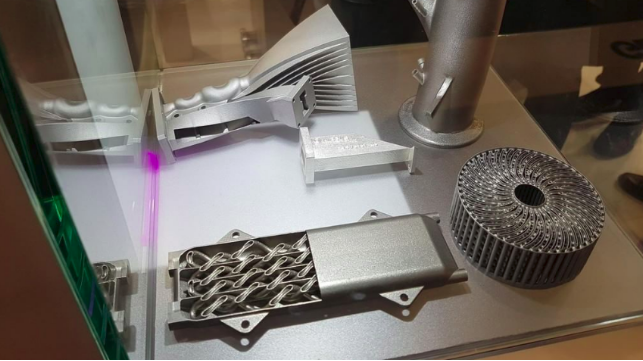


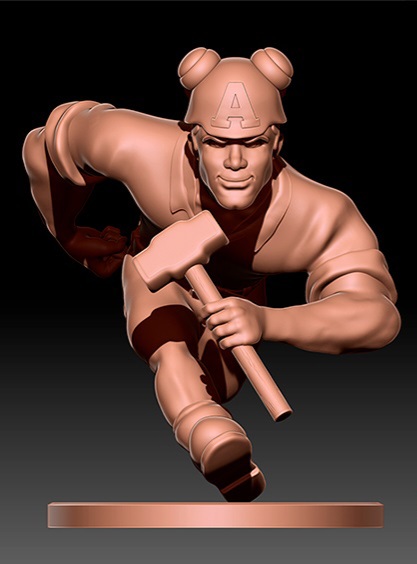
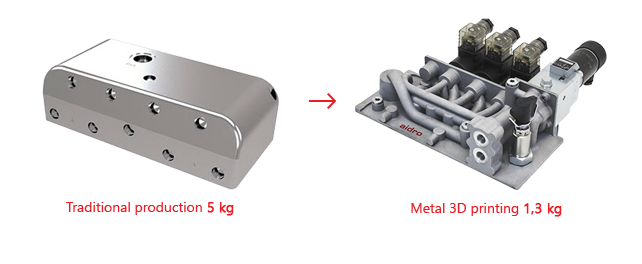
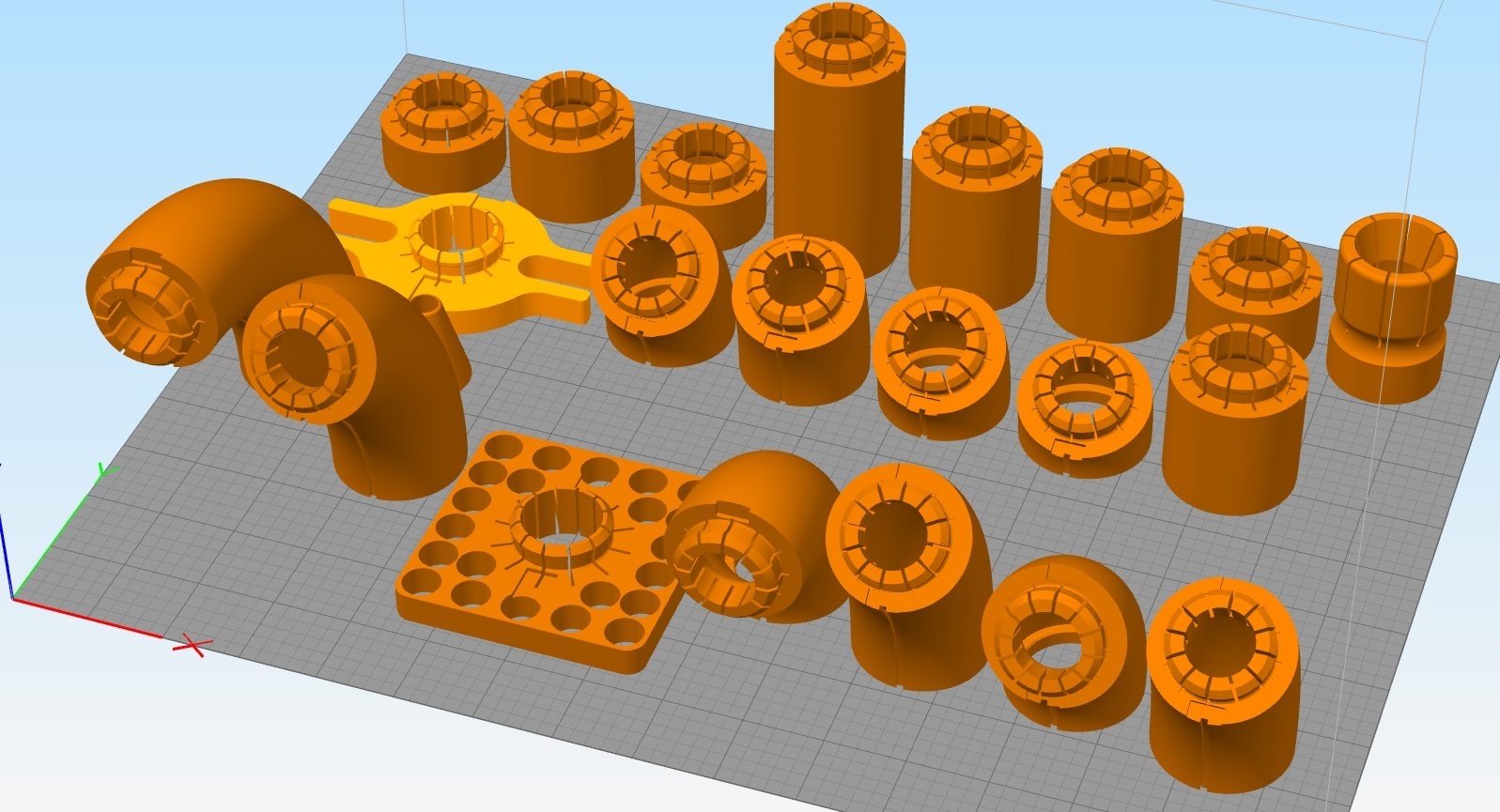
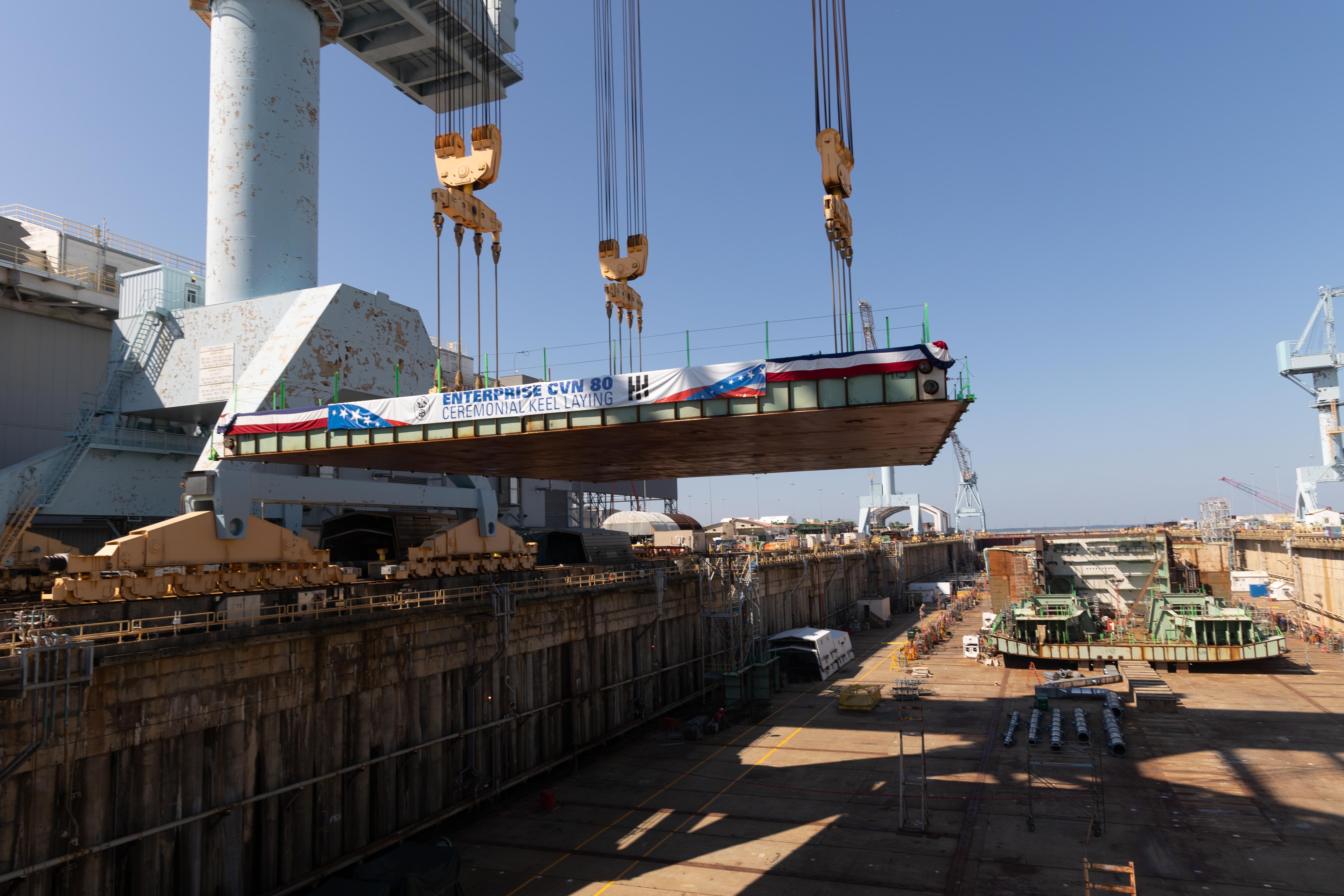


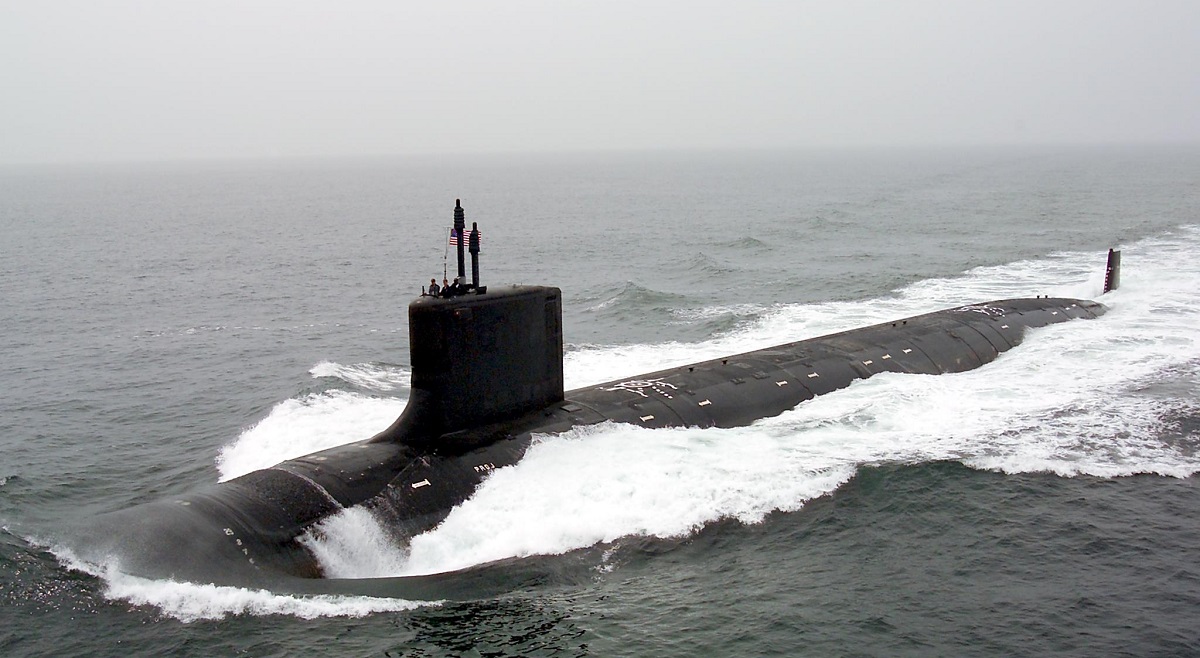
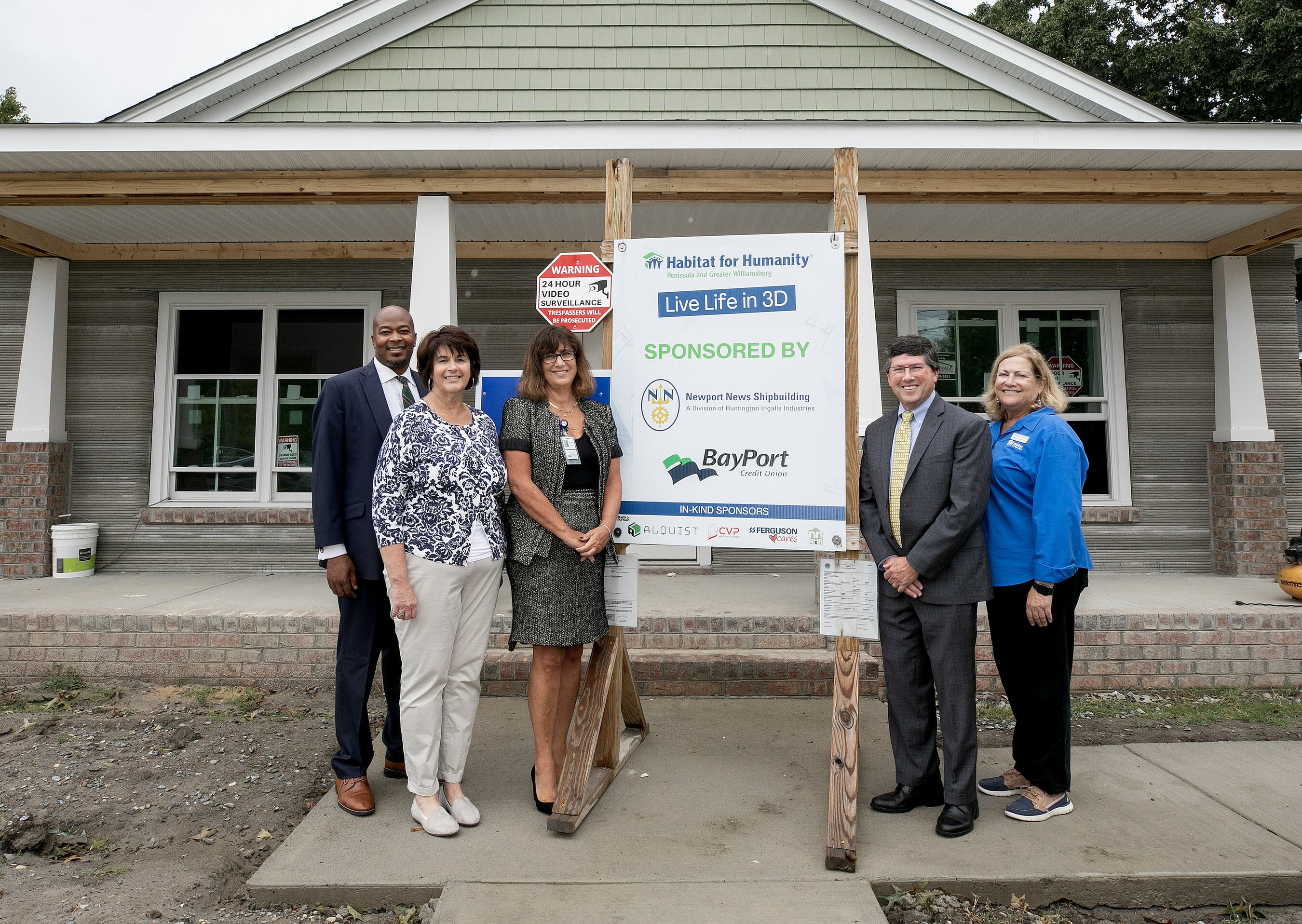
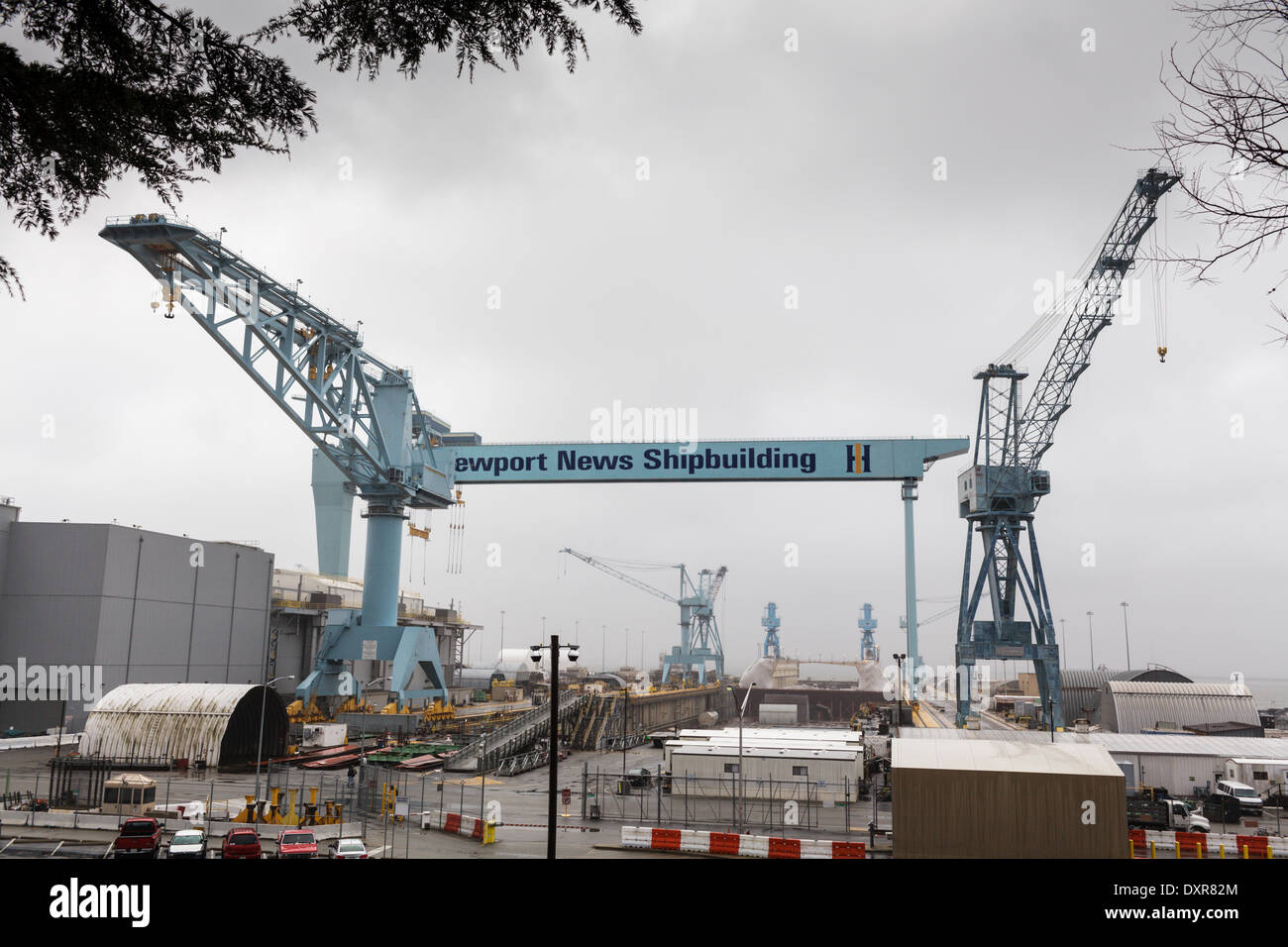
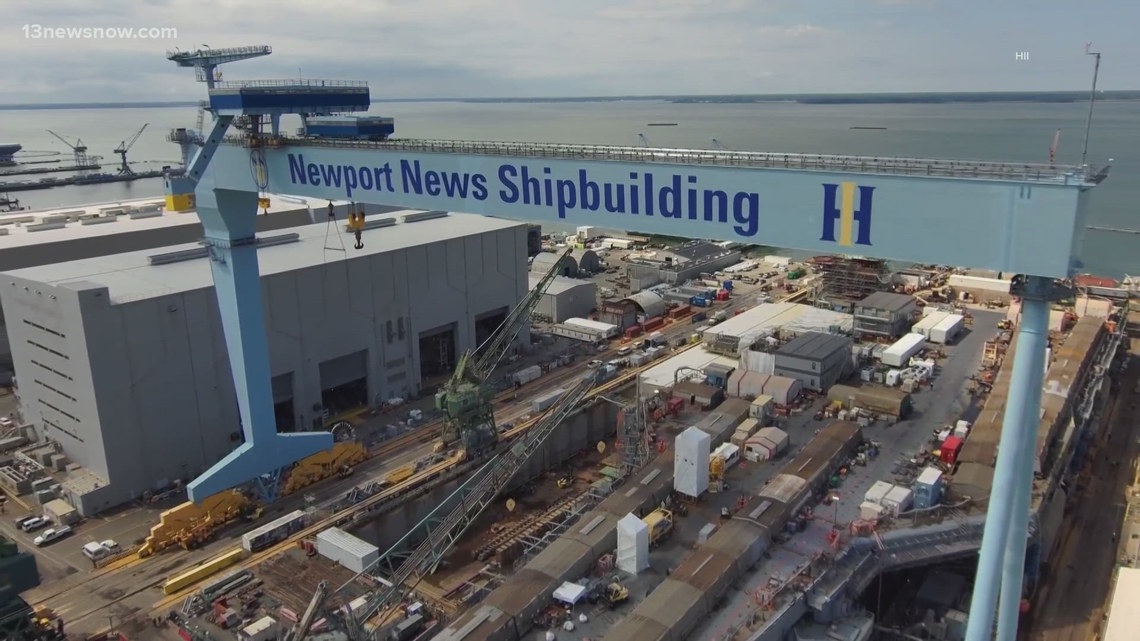
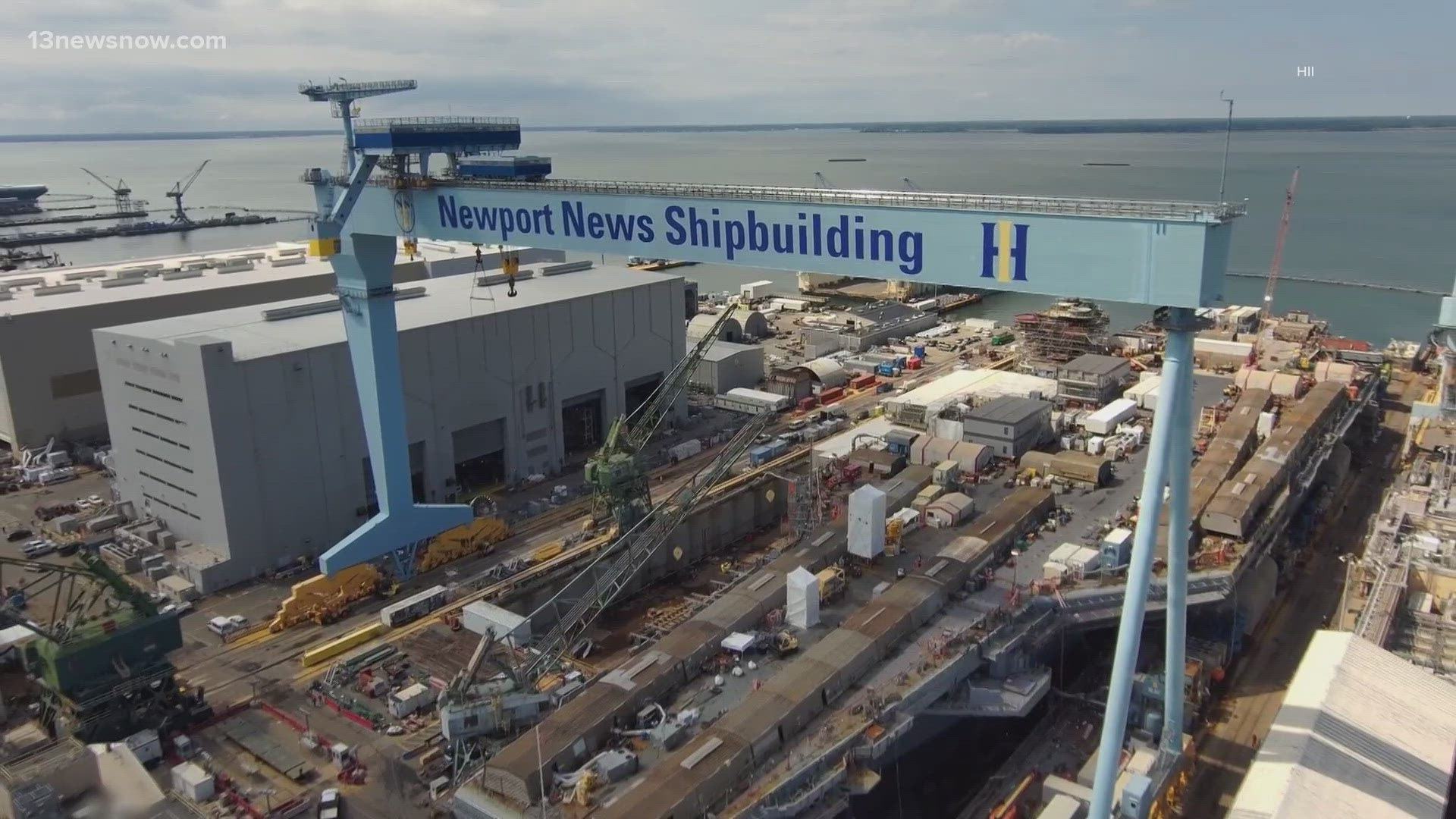