What Two Adjustments Can Be Made To The Condenser
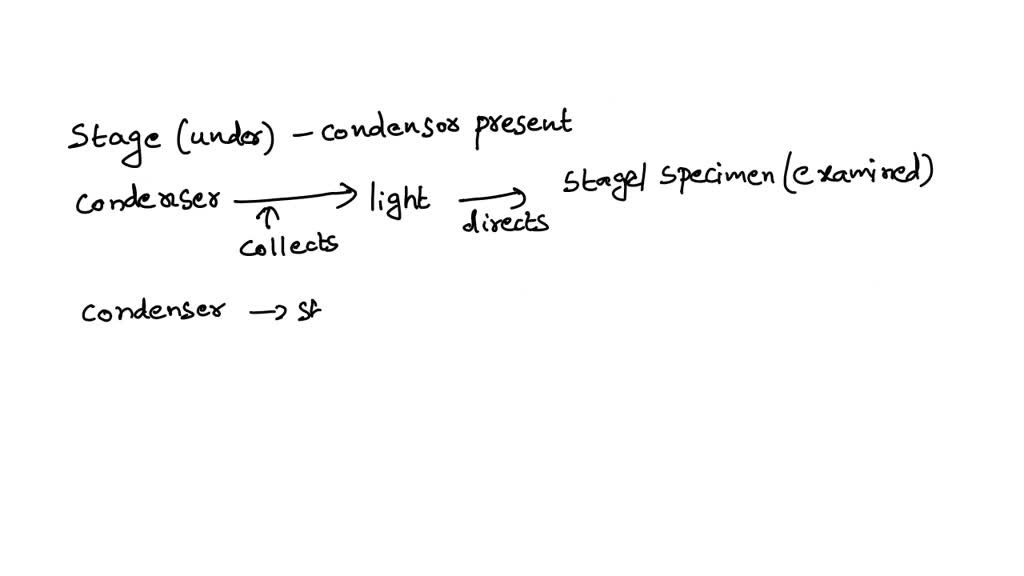
The air hangs thick and heavy, a muggy blanket draped over the bustling engine room. A rhythmic hum, the heartbeat of a power plant, vibrates through the steel deck. Rivulets of condensation trace paths down massive pipes, a testament to the relentless work happening within. The efficiency of this system, its ability to convert steam back into water, is paramount to keeping the lights on and the wheels turning.
At the heart of this vital process lies the condenser, a component often overlooked but absolutely crucial. While many perceive the condenser as a static piece of equipment, optimizing its performance can significantly impact overall system efficiency. This article explores two key adjustments that can be made to a condenser to enhance its operation: non-condensable gas removal and cooling water flow optimization.
The Unsung Hero: Understanding the Condenser
The condenser's primary function is to condense exhaust steam from a turbine or other process. This phase change creates a vacuum, which increases the efficiency of the turbine by maximizing the pressure difference across it.
Imagine blowing into a straw – the greater the difference between the pressure inside your mouth and the pressure at the end of the straw, the faster and more forcefully you can blow. The same principle applies to a turbine; a lower pressure on the exhaust side allows for more work to be extracted from the steam.
According to the U.S. Department of Energy, improving condenser performance directly translates to fuel savings and reduced emissions in power plants. Optimizing a condenser is not just about maintenance; it’s a strategic move towards energy efficiency and environmental responsibility.
Adjustment 1: The Silent Thief - Non-Condensable Gas Removal
Air and other non-condensable gases, like nitrogen and oxygen, can leak into the condenser system. These unwelcome guests interfere with the condensation process.
They create a barrier, inhibiting the steam from contacting the cooling surfaces and reducing heat transfer efficiency. Think of it like trying to cool a pot of boiling water with a layer of oil on top – the oil insulates the water and slows down the cooling process.
Effective removal of these gases is paramount. This is typically achieved through dedicated air ejectors or vacuum pumps. These systems draw out the non-condensables, maintaining the desired vacuum within the condenser.
Methods of Removal
Air Ejectors: These use a high-velocity jet of steam to create a vacuum, drawing out the non-condensable gases. Regular inspection and maintenance of the steam nozzles are crucial for optimal performance.
Vacuum Pumps: These are mechanical pumps designed to remove gases and maintain a vacuum. They are often more energy-efficient than air ejectors but require careful monitoring and upkeep.
According to research from the Electric Power Research Institute (EPRI), regularly checking and maintaining these systems can improve condenser vacuum by as much as 0.5 inches of mercury, which can translate into a noticeable increase in turbine efficiency.
Furthermore, consider implementing continuous online monitoring of the condenser vacuum and non-condensable gas levels. This provides real-time insights, allowing for prompt identification and correction of any issues.
Adjustment 2: Finding the Sweet Spot - Cooling Water Flow Optimization
The condenser relies on a steady flow of cooling water to absorb the heat released during condensation. However, simply maximizing the flow is not always the best approach.
Too much cooling water can lead to increased pumping costs and potentially erode the internal surfaces of the condenser tubes. Too little cooling water and the vacuum suffers, reducing turbine efficiency.
The key lies in finding the optimal flow rate. This is the point where the benefits of increased heat transfer outweigh the costs associated with increased pumping power.
The Balancing Act
Optimizing cooling water flow often involves adjusting the speed of the cooling water pumps. Some systems utilize variable frequency drives (VFDs) to precisely control the pump speed and flow rate.
Another approach involves carefully monitoring the cooling water temperature differential – the difference between the inlet and outlet temperatures. A large temperature differential may indicate insufficient flow, while a small differential may suggest excessive flow.
By analyzing these parameters, operators can fine-tune the cooling water flow to achieve the best balance between efficiency and cost. Data from various engineering handbooks suggests that optimizing cooling water flow can lead to significant reductions in parasitic power consumption.
Regularly cleaning the condenser tubes is also crucial for maintaining optimal heat transfer. Fouling, scaling, and corrosion can significantly reduce the effectiveness of the cooling water system. Techniques like tube brushing or chemical cleaning can help remove these deposits and restore performance.
Looking Ahead: The Importance of Continuous Improvement
Optimizing condenser performance is not a one-time fix but rather an ongoing process. Regular monitoring, data analysis, and proactive maintenance are essential for sustaining efficiency gains.
Emerging technologies, such as advanced heat transfer coatings and automated tube cleaning systems, offer promising avenues for further improvement. By embracing these innovations, industries can continue to push the boundaries of energy efficiency and reduce their environmental footprint.
Ultimately, the condenser, though often hidden from sight, plays a critical role in the overall efficiency of many power generation and industrial processes. By focusing on simple yet effective adjustments like non-condensable gas removal and cooling water flow optimization, we can unlock significant energy savings and contribute to a more sustainable future.
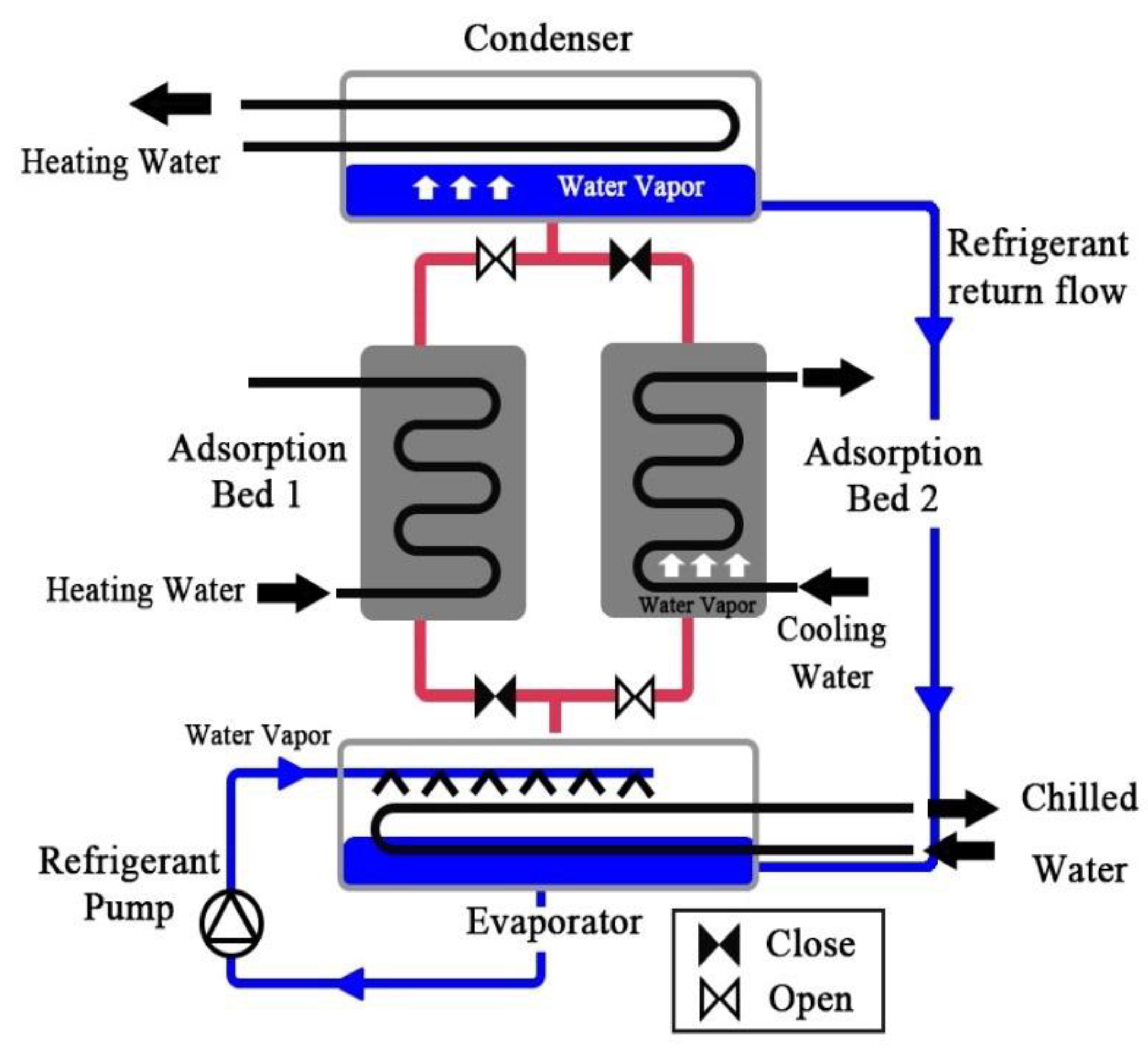
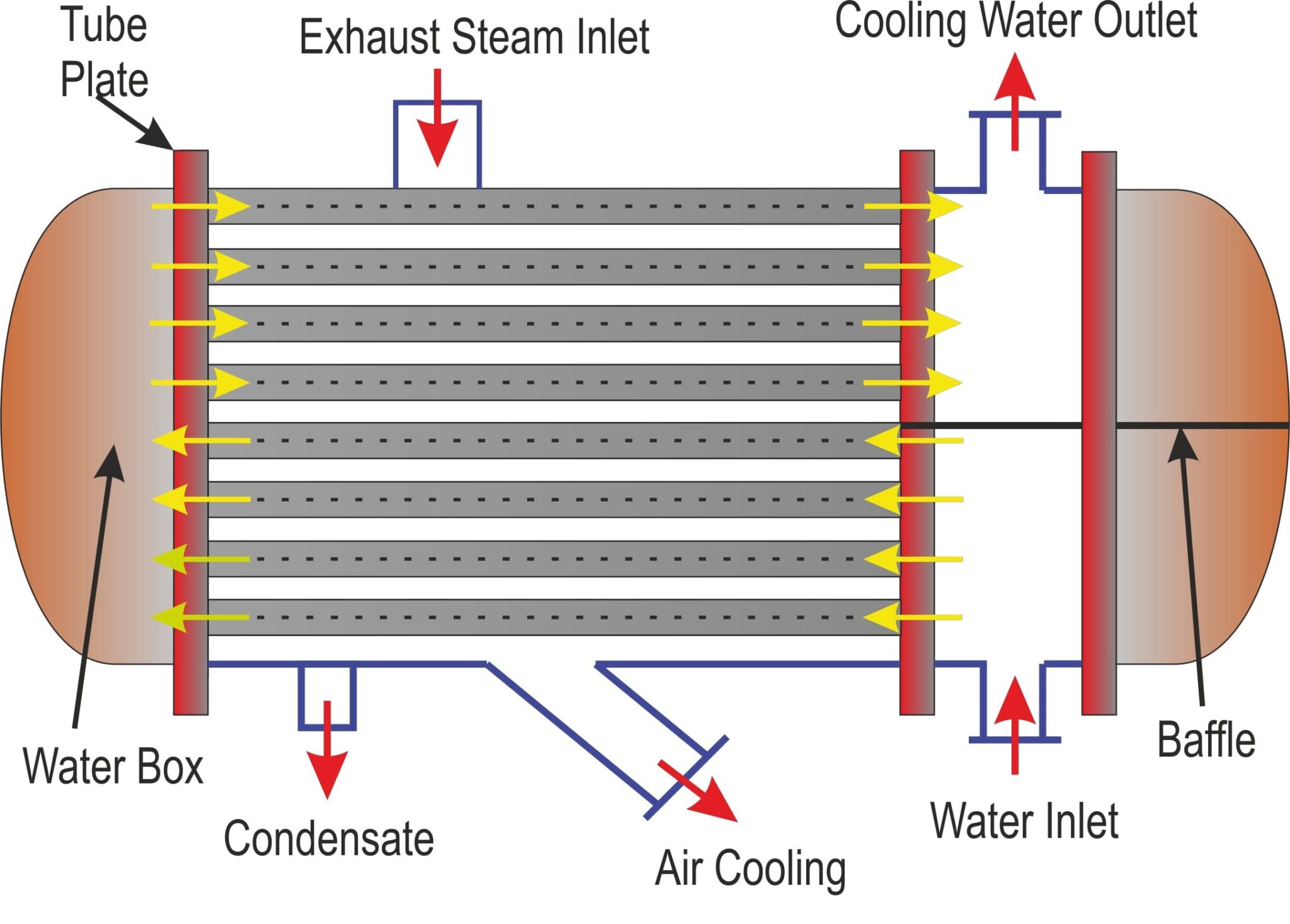
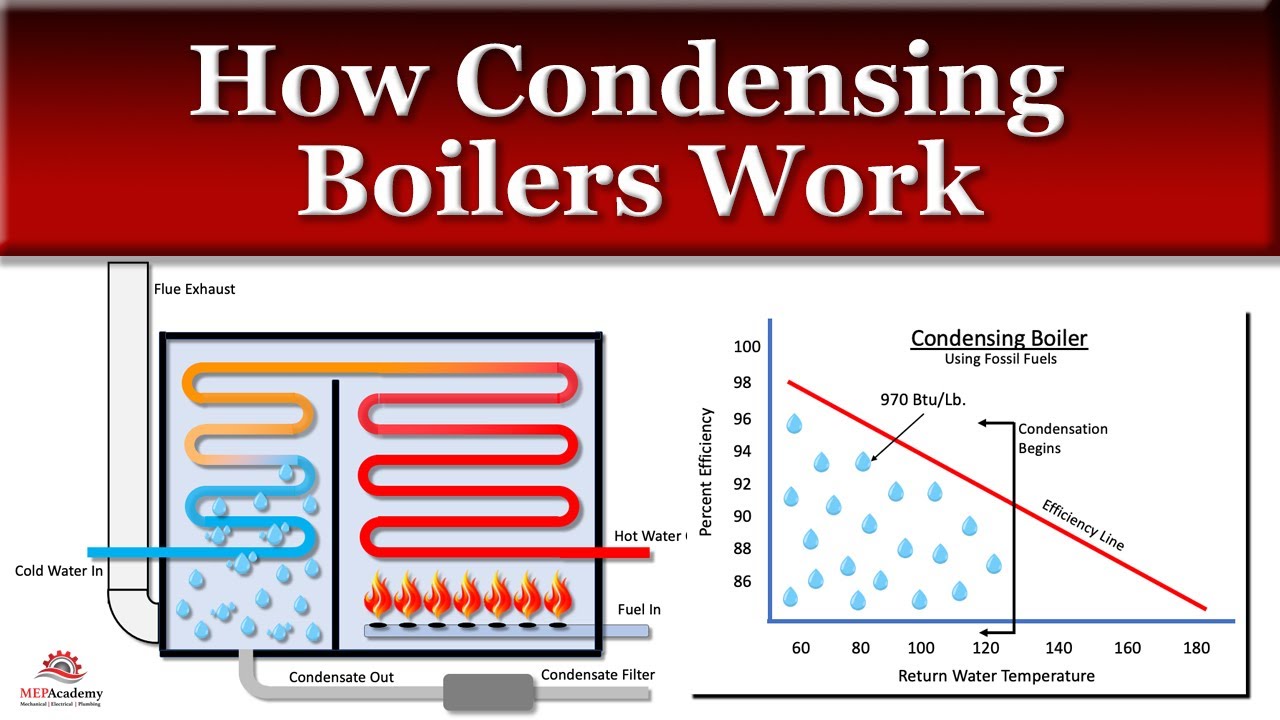
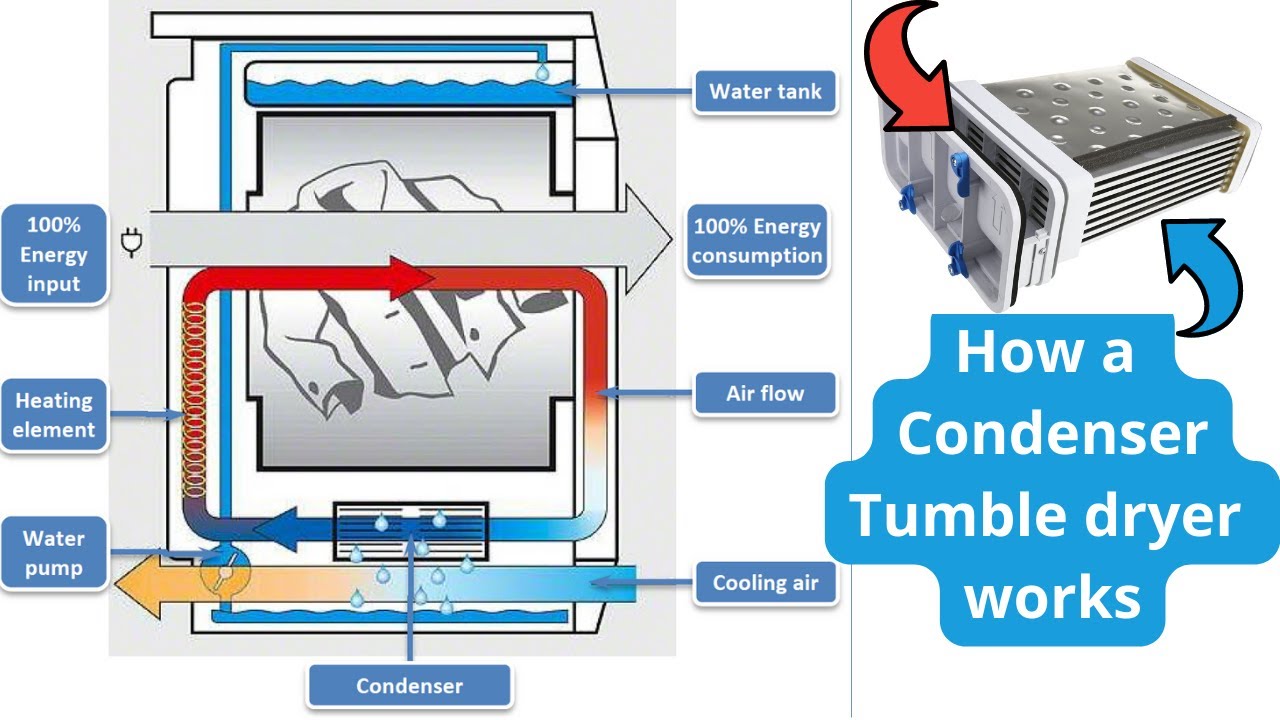

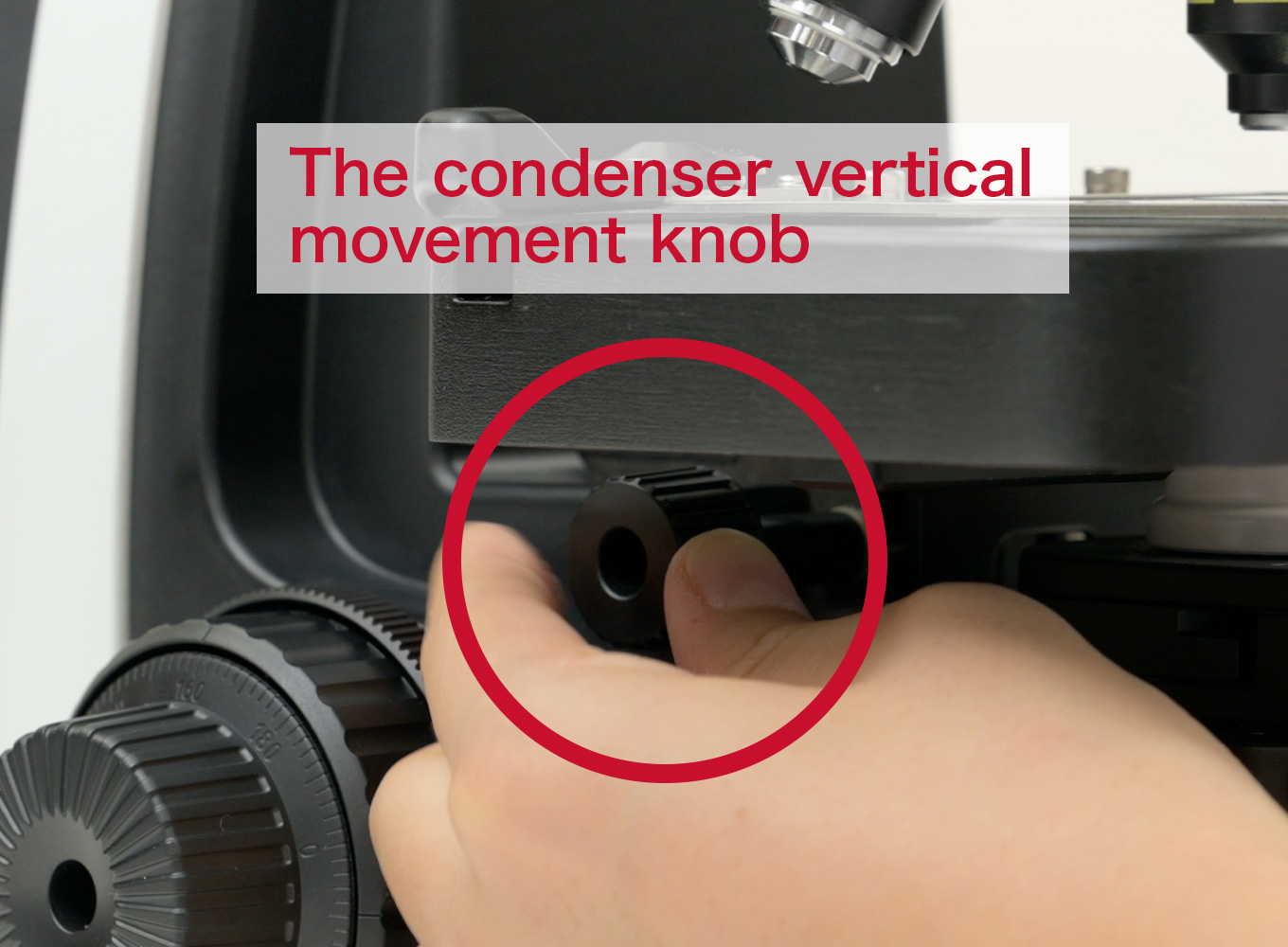
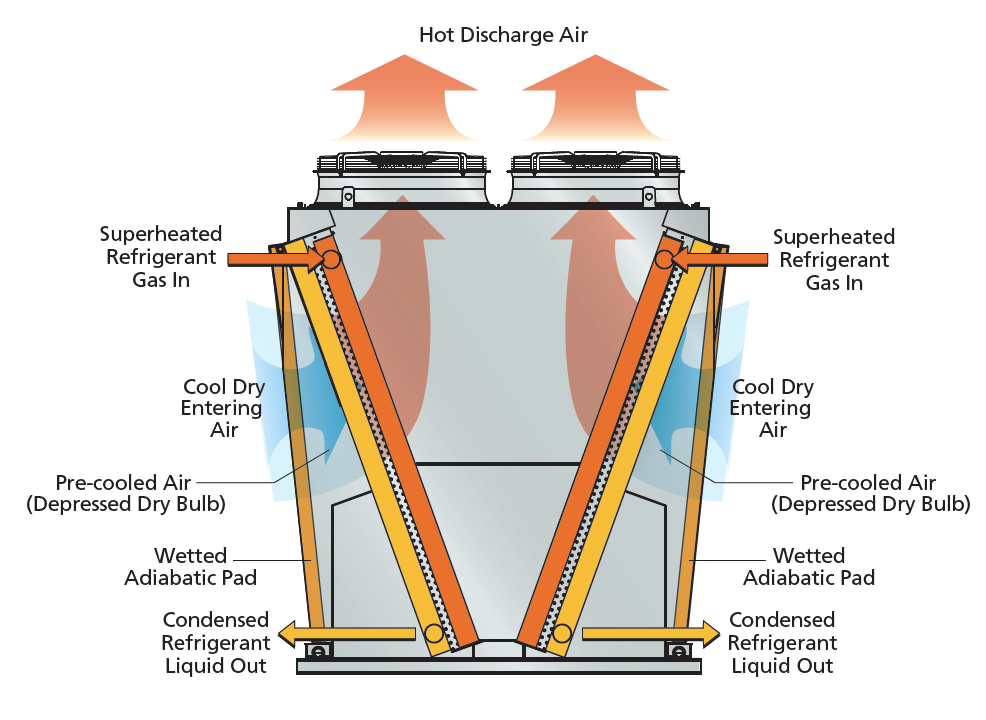







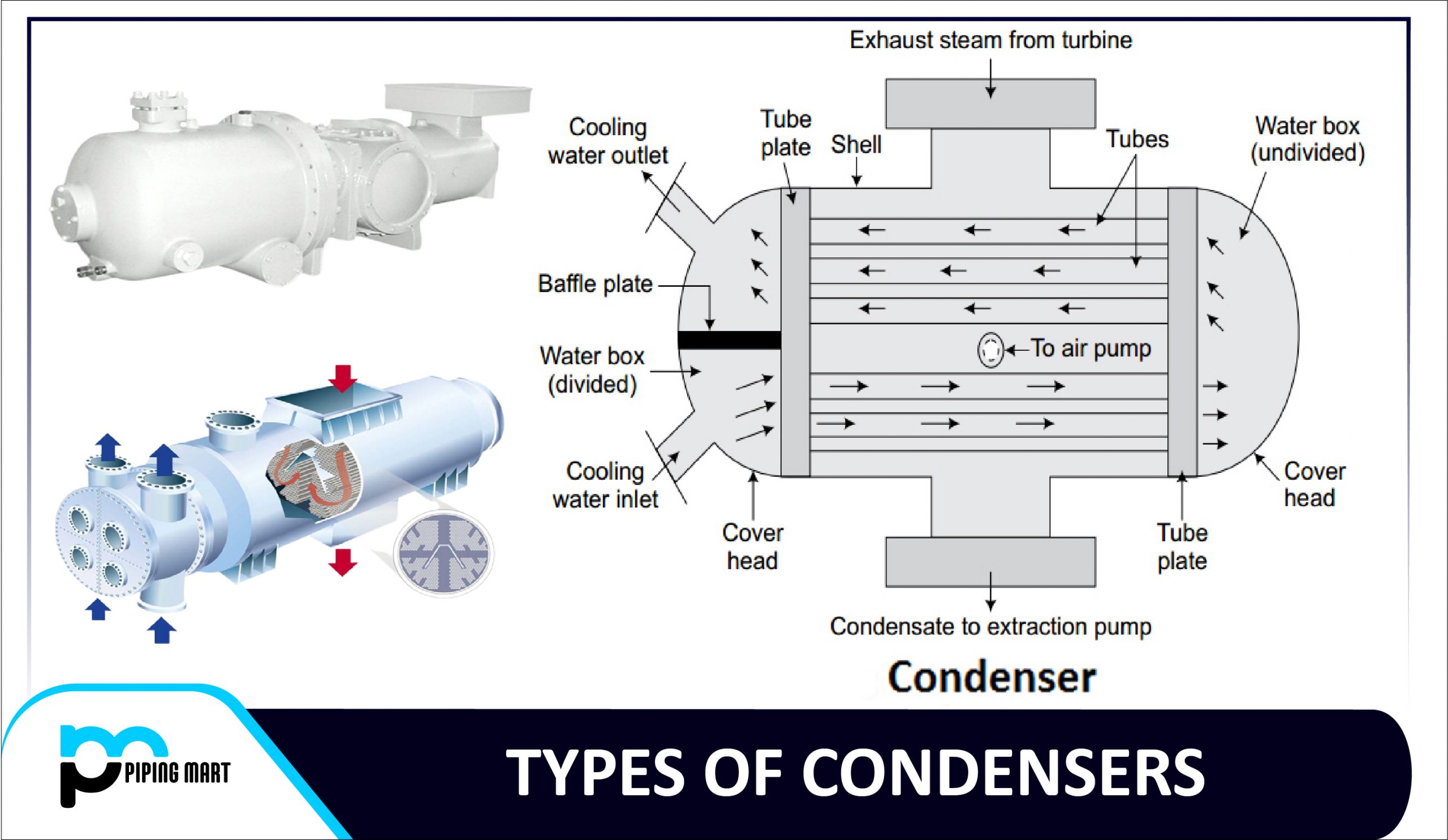

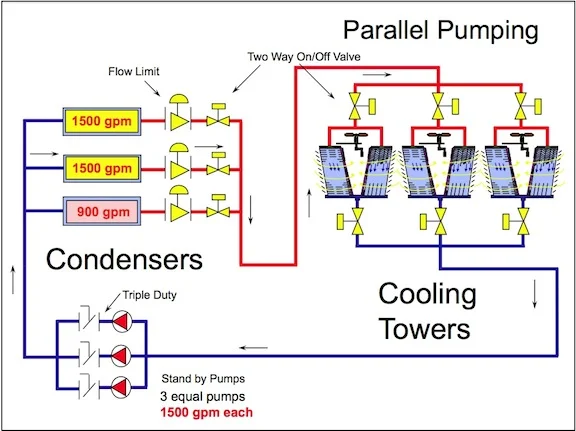
