Which Of The Following Are Included In Raw Materials Inventory
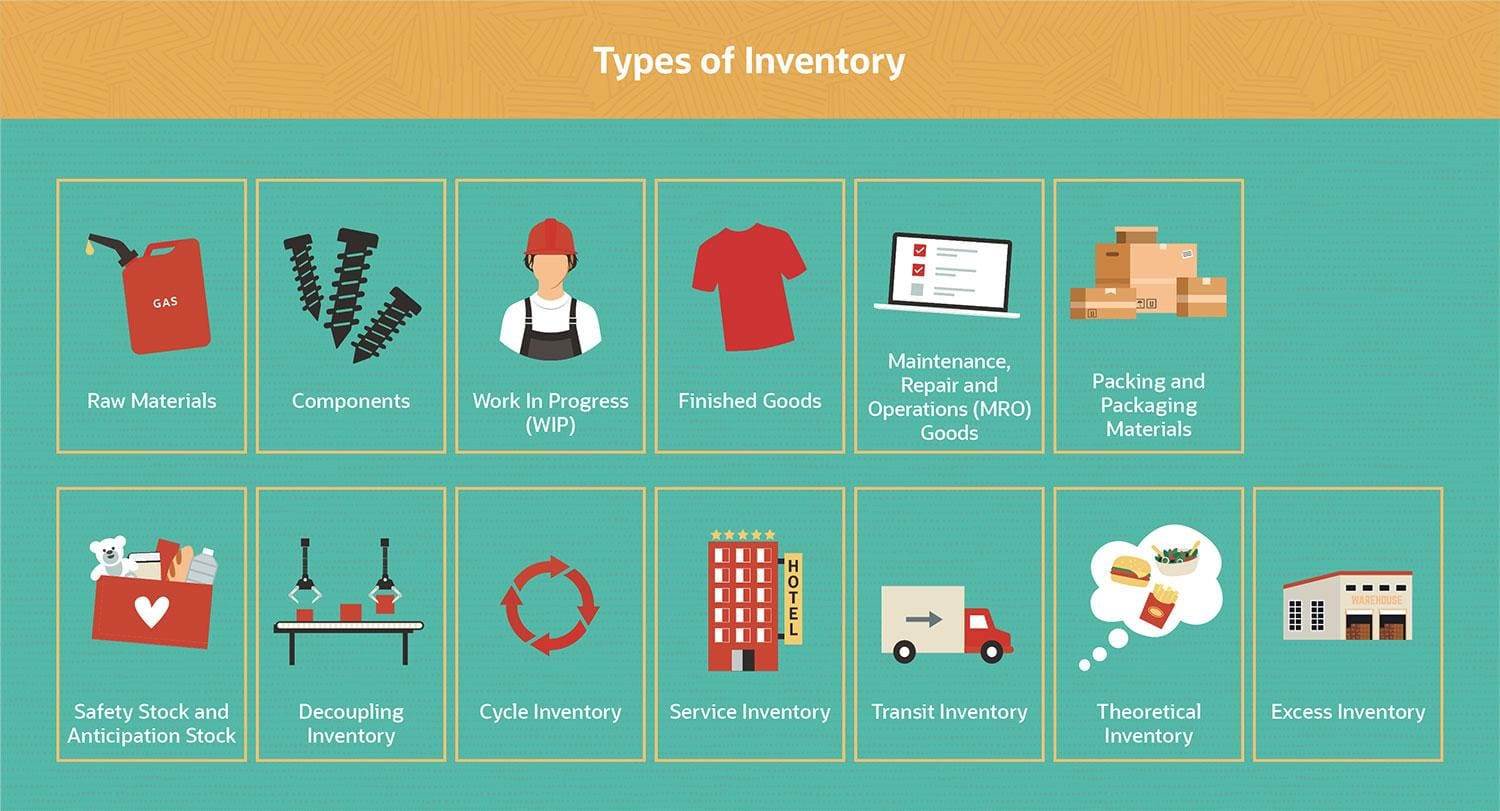
Understanding inventory management is crucial for businesses, especially when it comes to raw materials. Accurately identifying and classifying these materials directly impacts financial reporting, production planning, and overall operational efficiency. This article delves into the specific items included in raw materials inventory, clarifying what qualifies and why this classification is essential.
The classification of raw materials inventory can sometimes be complex, particularly in businesses dealing with diverse inputs or intricate supply chains. Getting it right is vital for accurate cost accounting and ensuring that resources are readily available for production processes.
What Qualifies as Raw Materials Inventory?
Raw materials inventory encompasses all the inputs a company acquires for use in its manufacturing or production processes. These are the basic components that will be transformed into finished goods. The key determinant is that these materials have not yet undergone any significant processing or transformation by the company itself.
Raw materials may include commodities, parts, and components purchased from external suppliers. They represent the foundational building blocks for the company’s products.
Common Examples of Raw Materials
Specific examples vary widely depending on the industry. However, some common categories illustrate the scope of raw materials inventory.
In manufacturing, this could be steel, lumber, or plastic resins. For a food processing company, it might include grains, fruits, vegetables, or spices.
A technology company might consider silicon wafers, microchips, or wiring as raw materials. Similarly, a clothing manufacturer would include fabrics, buttons, zippers, and thread.
Distinguishing Raw Materials from Other Inventory Types
It is essential to differentiate raw materials from other types of inventory. These include work-in-progress (WIP) and finished goods.
WIP inventory refers to materials that have entered the production process but are not yet complete. Finished goods are the completed products ready for sale.
The distinction lies in the stage of processing. Items are classified as raw materials until they are actively being converted into another form through labor or machinery.
Components Included in Raw Materials Inventory
The following items are typically included when classifying raw materials inventory:
- Direct Materials: These are the materials that become an integral part of the finished product and can be easily traced to it. For instance, the wood used to build a chair.
- Indirect Materials: While not directly part of the finished product, these are necessary for the production process. Examples include lubricants for machinery or cleaning supplies used in the factory. They can be included if their value is significant.
- Purchased Parts and Components: Items acquired from suppliers that will be directly incorporated into the final product without further modification. Think of semiconductors for electronics.
- Commodities: Basic goods used as input. These could be agricultural products, minerals, or metals.
Items Typically Excluded
Certain items are typically excluded from raw materials inventory. These usually include:
Supplies not Directly Incorporated: Office supplies, janitorial supplies, and similar items generally do not qualify. They are typically expensed in the period they are used.
Capital Equipment: Machinery, tools, and other equipment used in the production process are classified as fixed assets. They are not raw materials.
Finished Goods and Work-in-Progress: As mentioned previously, these belong to separate inventory categories.
Why Proper Classification Matters
The accurate classification of raw materials inventory is fundamental for several reasons. It directly impacts financial reporting and costing.
Incorrect classification can distort the balance sheet and income statement. This leads to flawed financial analysis and potentially misleading investment decisions.
It is also critical for effective production planning and supply chain management. Knowing the exact quantity and value of raw materials on hand is essential for avoiding stockouts and optimizing production schedules.
Impact on Businesses and the Economy
Effective raw materials inventory management has broad implications. It contributes to a company’s profitability and competitiveness.
Companies with well-managed raw materials inventories can respond quickly to changing market demands. They are able to avoid production delays and minimize waste.
On a macroeconomic level, efficient inventory management contributes to overall economic stability. This minimizes supply chain disruptions and promotes steady economic growth.
The process of determining what qualifies as raw materials is important for all companies. Ensuring appropriate identification and classification directly affect financial reporting, operational planning, and supply chain resilience.
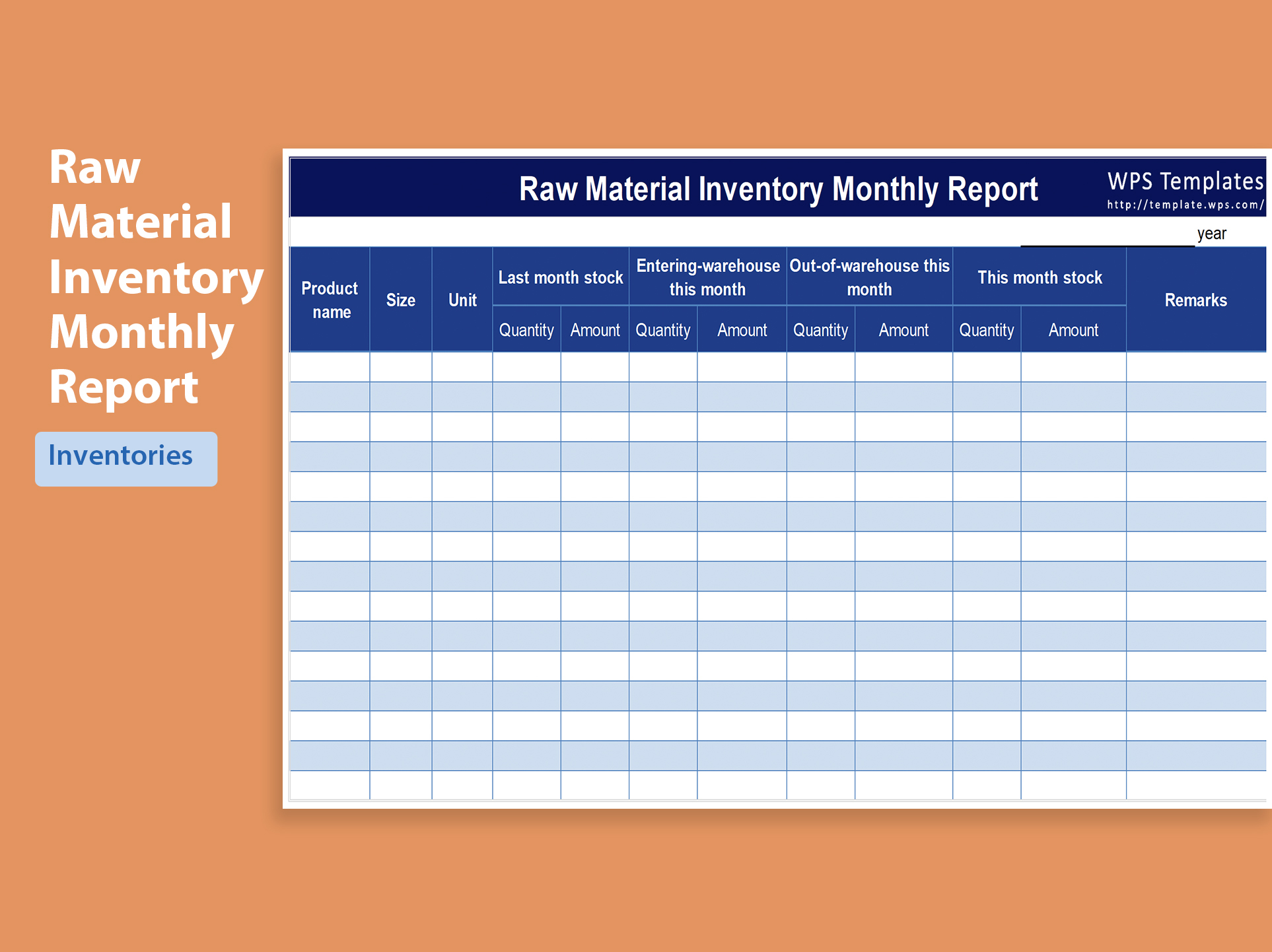
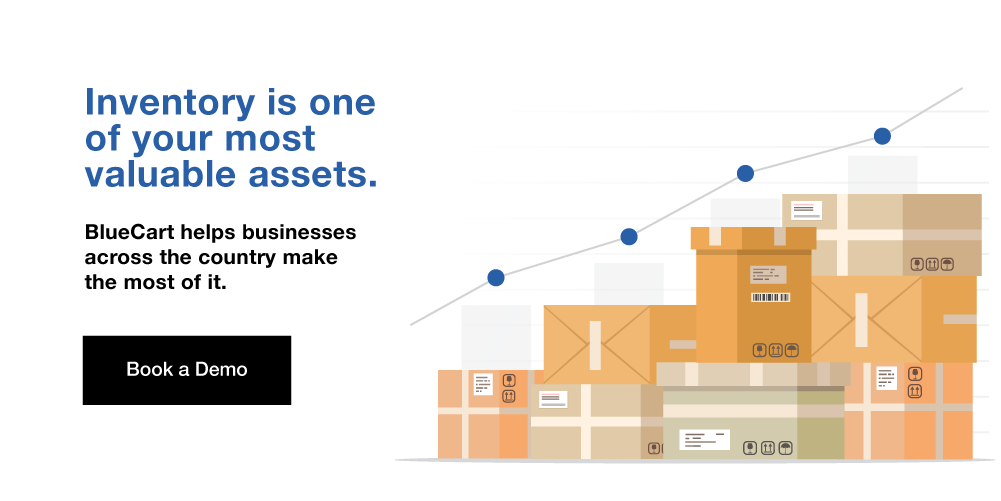
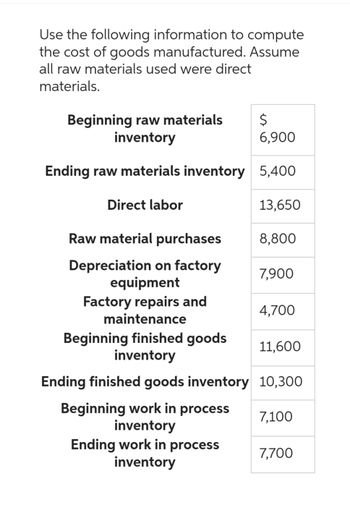
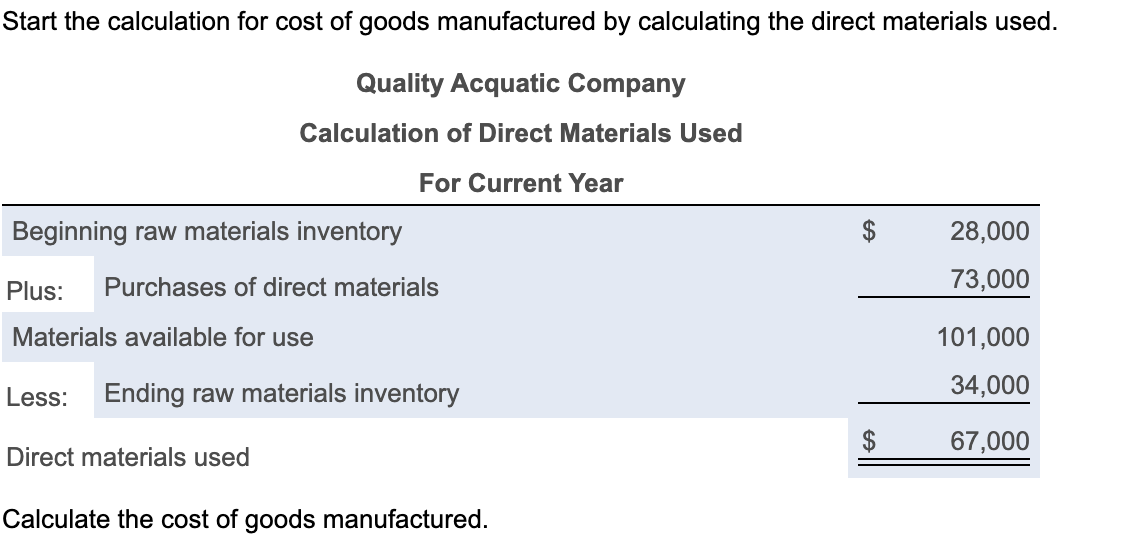
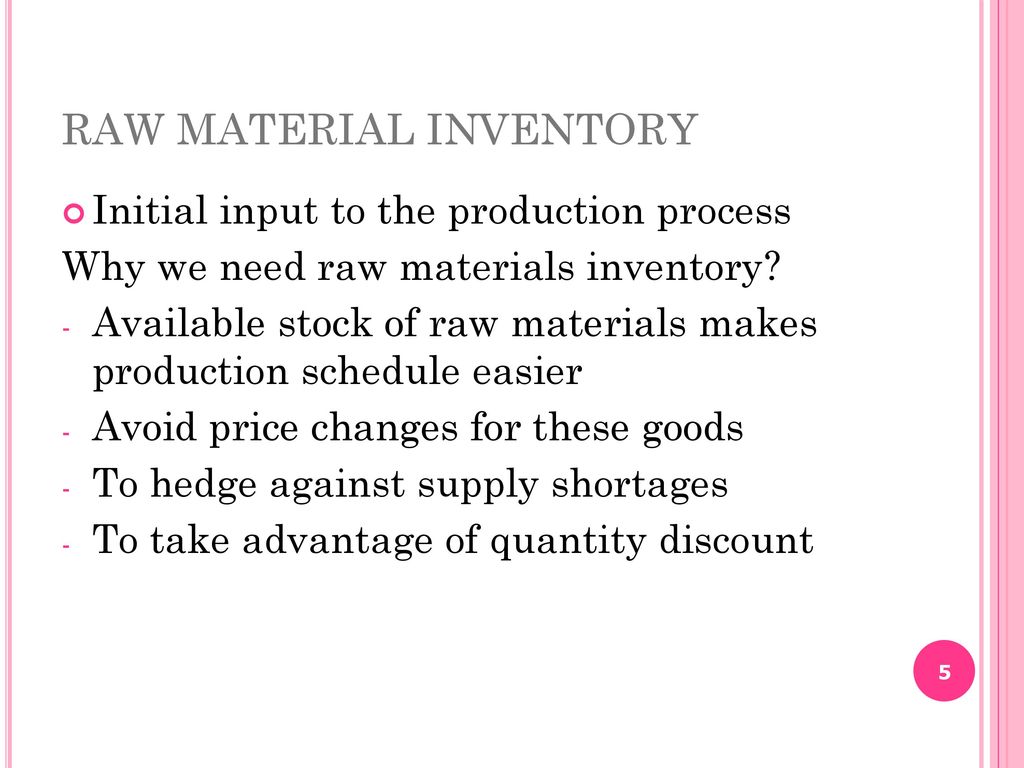
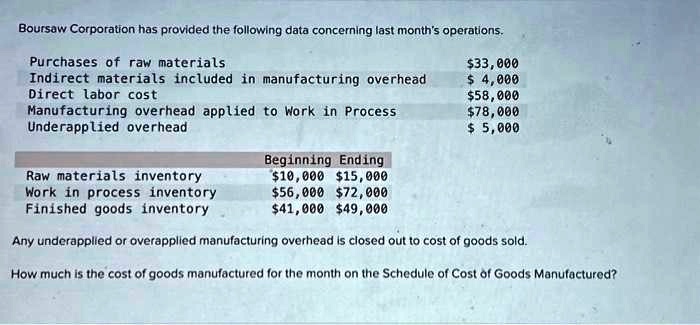
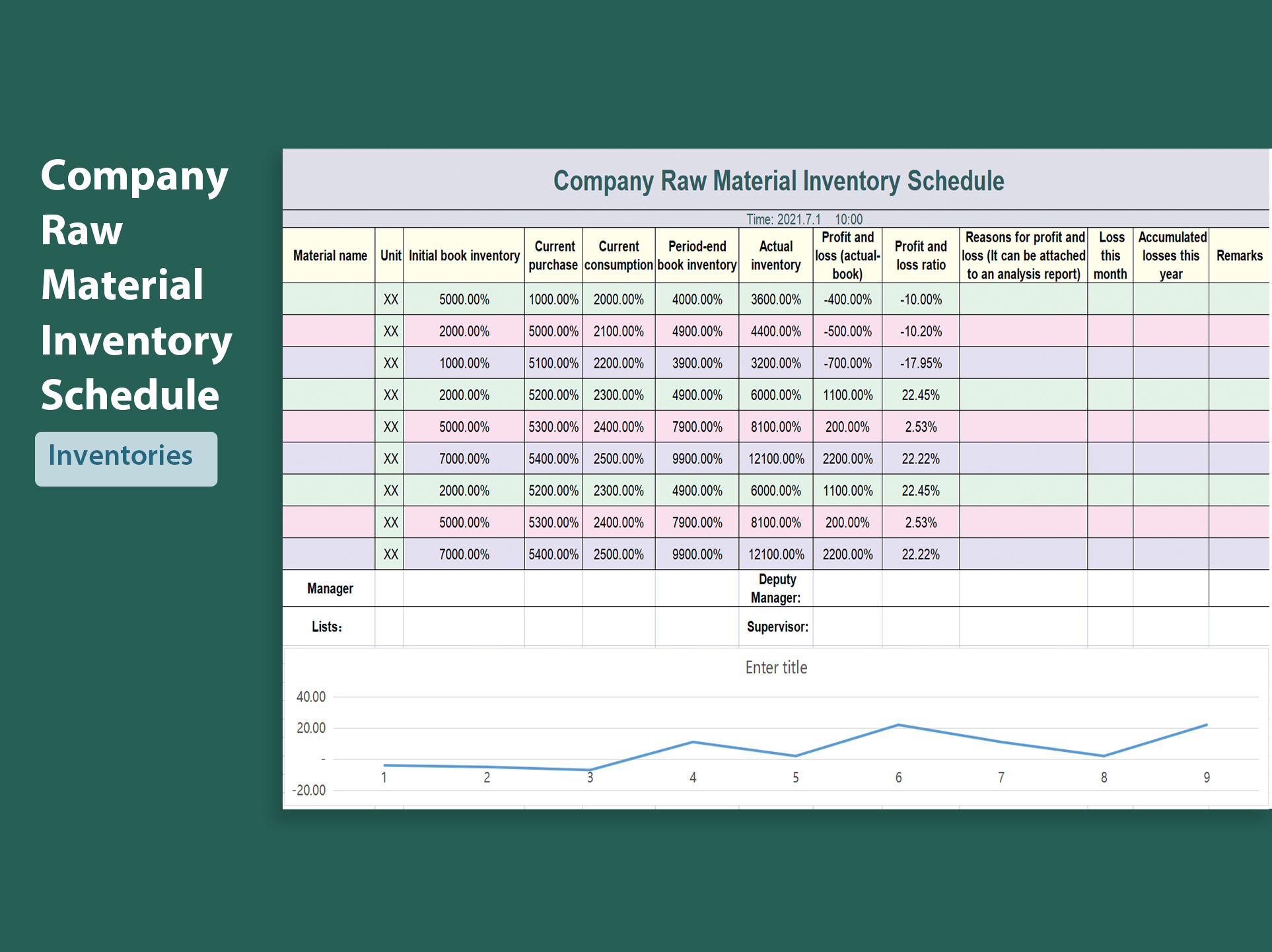
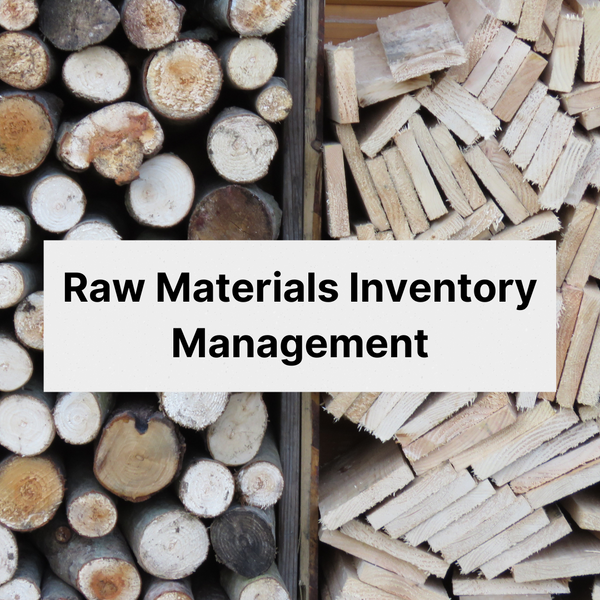
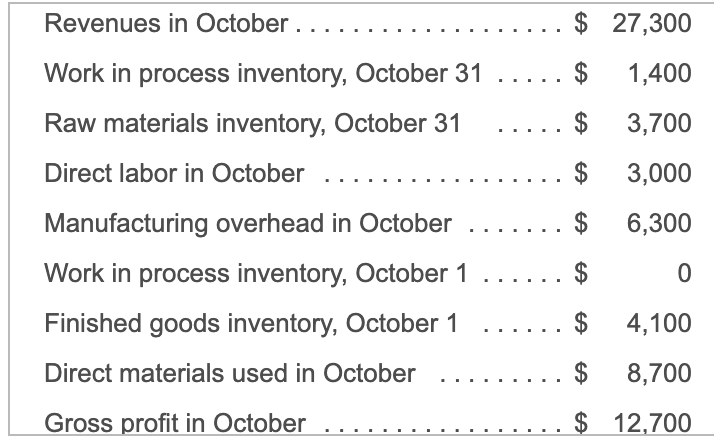
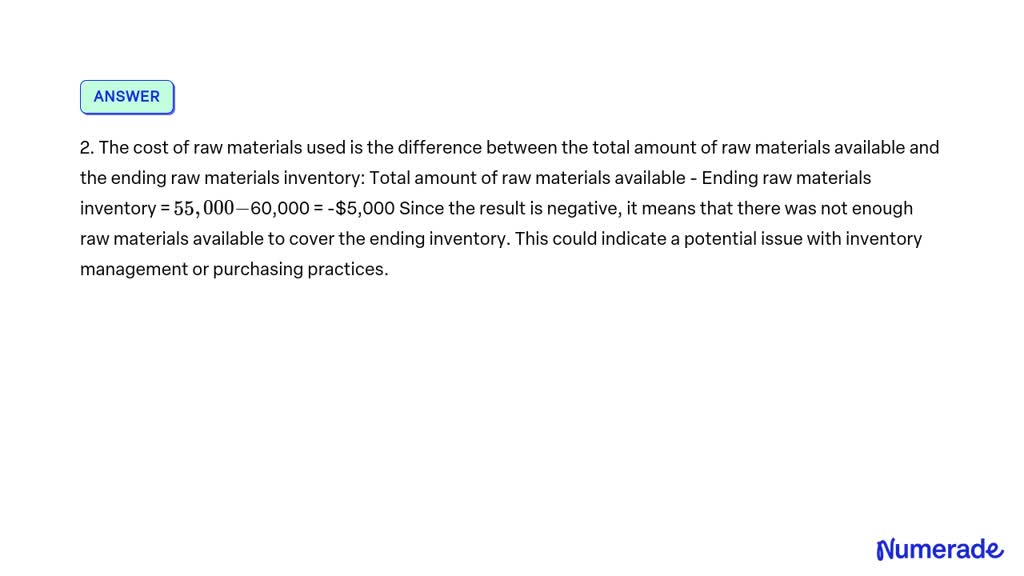
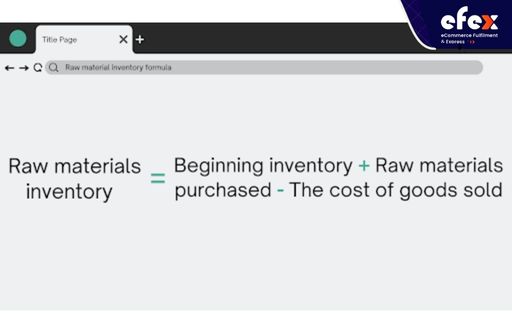
.png?auto=compress%2Cformat&fit=max&w=3840&q=75)

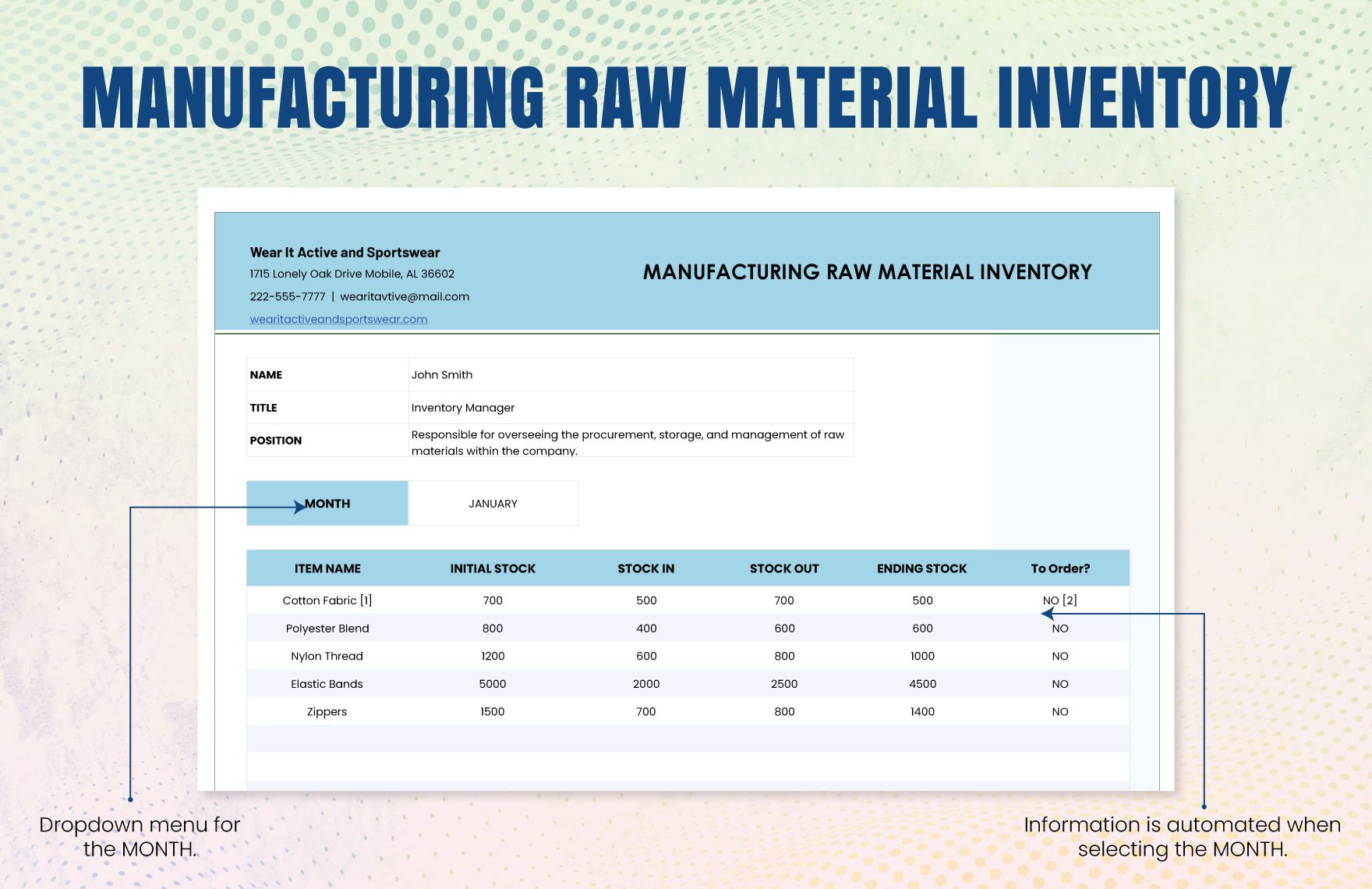
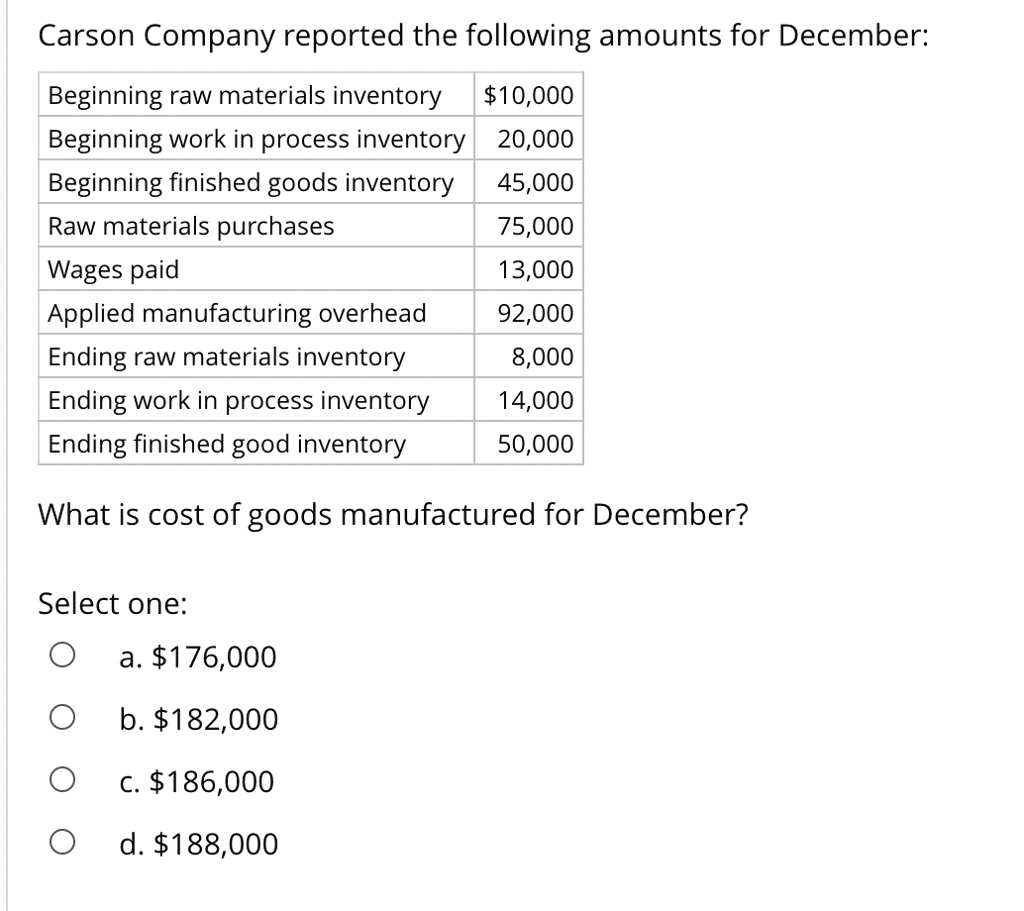
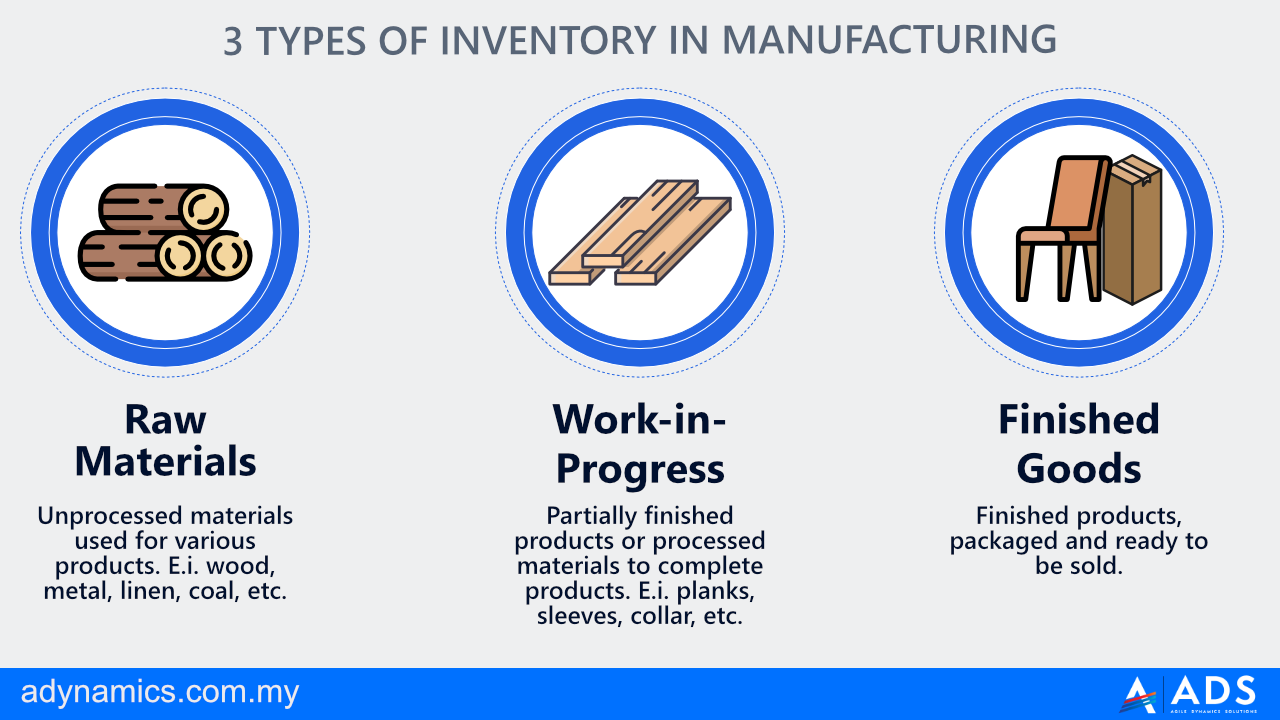
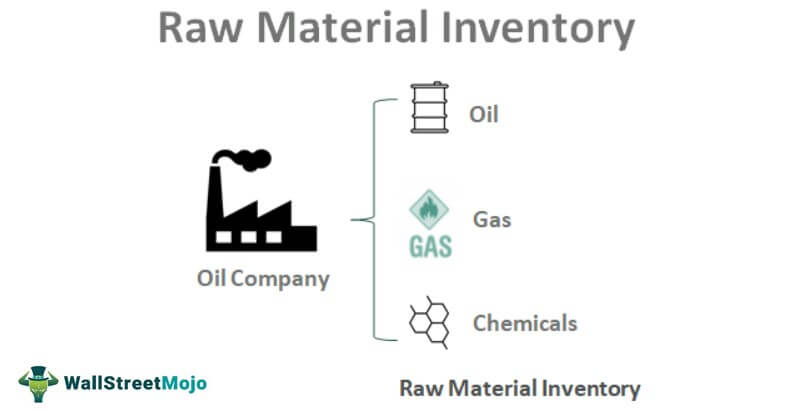
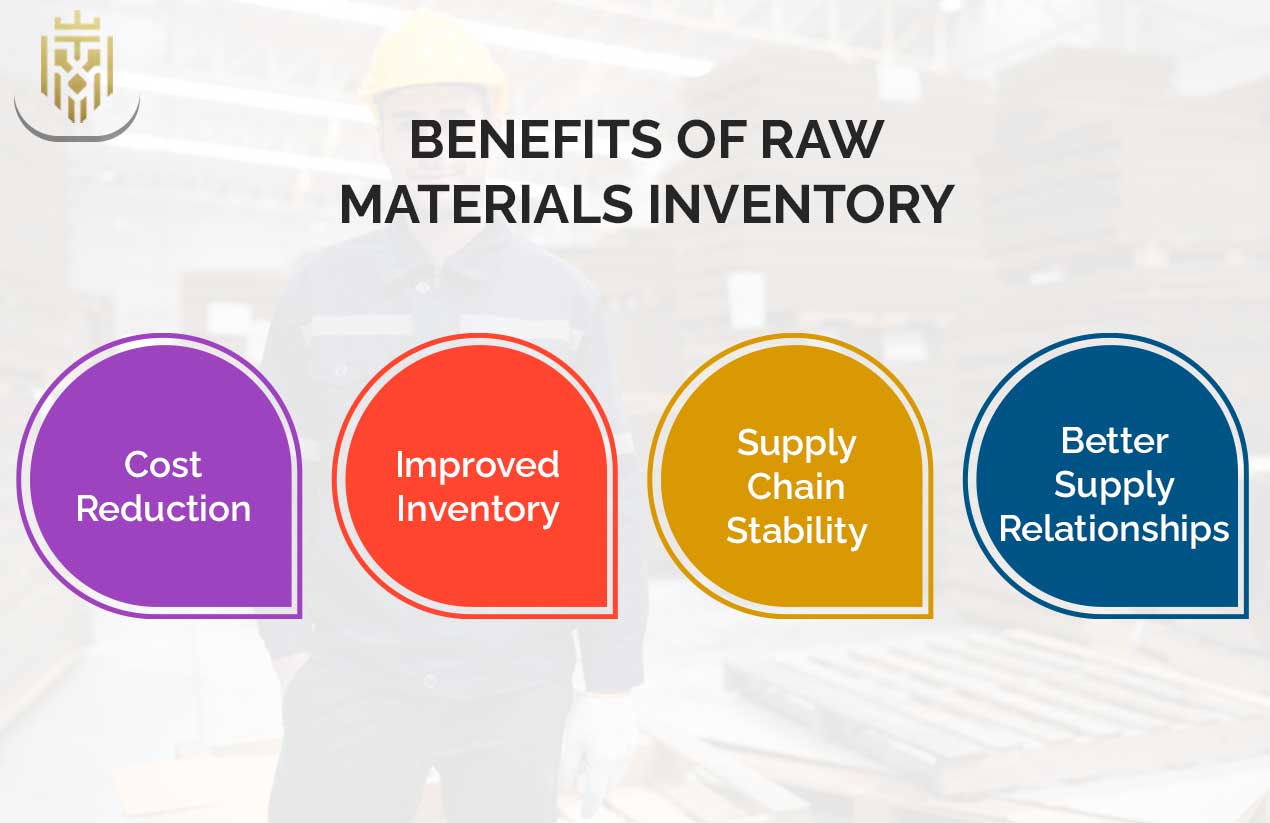