Which Of The Following Is Not A Manufacturing Cost Category
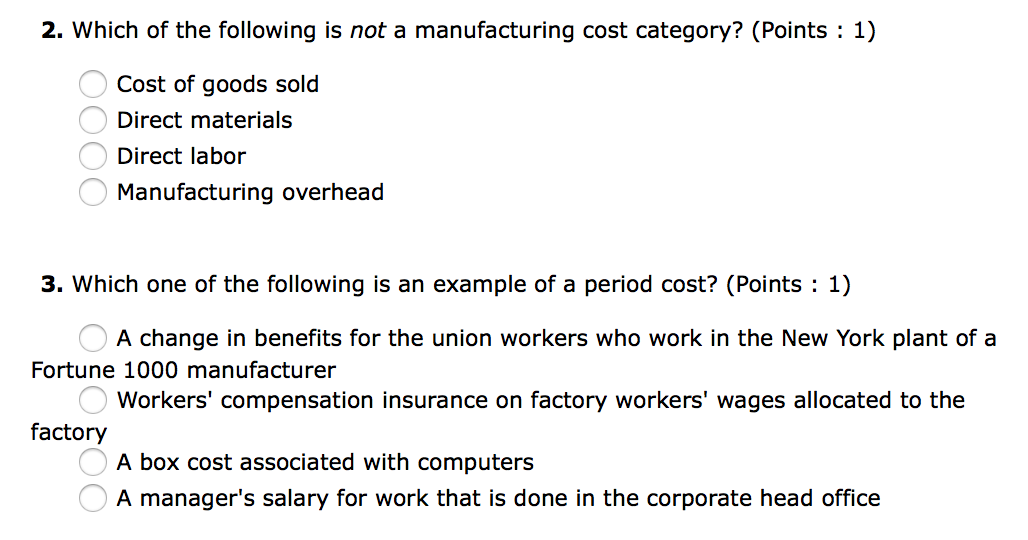
Imagine walking through a bustling factory floor, the rhythmic hum of machinery a constant soundtrack. Sparks fly from welding stations, and the air is thick with the scent of oil and freshly cut metal. Workers in hard hats move with practiced efficiency, each contributing to the complex dance of turning raw materials into finished goods. But behind the scenes, far from the shop floor, a team of accountants meticulously tracks every penny spent, categorizing costs to ensure profitability and efficiency. In this intricate accounting landscape, understanding the different categories of manufacturing costs is crucial.
The question "Which of the following is not a manufacturing cost category?" often pops up in business discussions and exams. This deceptively simple question highlights a fundamental concept: differentiating between costs directly associated with production and those that fall outside this realm. Recognizing this distinction is pivotal for accurate financial reporting and informed decision-making.
Decoding Manufacturing Costs: The Core Components
Manufacturing costs are generally categorized into three primary components: direct materials, direct labor, and manufacturing overhead. Each category plays a vital role in determining the total cost of producing goods. Understanding these categories is the bedrock of cost accounting.
Direct Materials: The Foundation of Production
Direct materials are the raw materials that become an integral part of the finished product. These are the tangible components that can be easily traced back to the final item. For example, the wood used to build a chair, the fabric in a garment, or the steel in a car are all considered direct materials.
The cost of direct materials includes the purchase price, freight charges, and any other expenses incurred to get the materials ready for use in production. However, it doesn't include indirect materials like cleaning supplies or lubricants used on machinery.
Direct Labor: The Human Element
Direct labor represents the wages paid to employees who are directly involved in the manufacturing process. These are the workers who physically transform raw materials into finished goods. Think of the assembly line workers in a car factory or the seamstresses in a clothing factory.
Direct labor costs include not only hourly wages but also benefits like health insurance and retirement contributions for these specific employees. It excludes the salaries of supervisors or quality control personnel, as these are considered indirect labor and fall under manufacturing overhead.
Manufacturing Overhead: The Umbrella Category
Manufacturing overhead encompasses all other costs incurred in the manufacturing process that are not direct materials or direct labor. This is a broad category that includes a wide range of expenses. Examples include indirect materials, indirect labor, factory rent, utilities, depreciation on factory equipment, and factory insurance.
Indirect materials, such as sandpaper used in woodworking or cleaning supplies used to maintain the factory, are included in manufacturing overhead. Similarly, indirect labor, like the salaries of factory supervisors, maintenance staff, and security personnel, is also part of this category.
Identifying Non-Manufacturing Costs
Now that we have established the core categories of manufacturing costs, let's consider what falls outside this scope. These are generally classified as period costs, meaning they are expensed in the period they are incurred, rather than being included in the cost of goods sold. Period costs are crucial for running a business but aren't directly linked to the production process itself.
Selling, General, and Administrative (SG&A) Expenses
Selling, General, and Administrative (SG&A) expenses are a major category of non-manufacturing costs. These expenses relate to activities that support the overall business but are not directly involved in production. Examples include marketing and advertising expenses, sales commissions, salaries of administrative staff, rent for office buildings, and legal fees.
SG&A costs are essential for generating revenue and managing the company, but they are not considered part of the cost of producing goods. For instance, the cost of a television commercial promoting a product would be classified as a selling expense, not a manufacturing cost.
Research and Development (R&D) Expenses
Research and Development (R&D) expenses are another significant category of non-manufacturing costs. These expenses relate to the activities involved in creating new products or improving existing ones. This includes the salaries of research scientists, the cost of laboratory equipment, and the expenses associated with conducting experiments.
R&D is vital for innovation and long-term growth, but it is not directly tied to the current production process. While the results of R&D may eventually lead to new products or processes that impact manufacturing costs, the R&D expenses themselves are treated as period costs.
Interest Expense
Interest expense, the cost of borrowing money, is also considered a non-manufacturing cost. Companies often take out loans to finance various aspects of their business, including manufacturing operations. However, the interest paid on these loans is treated as a financing cost, not a manufacturing cost.
Although the borrowed funds may be used to purchase factory equipment or raw materials, the interest expense is a separate item that is not directly related to the production process itself. It is typically reported as a non-operating expense on the income statement.
Why This Matters: The Significance of Cost Classification
Accurately classifying costs is essential for several reasons. It directly impacts the accuracy of financial statements, including the income statement and balance sheet. It also affects the calculation of key profitability metrics, such as gross profit and net income.
Furthermore, proper cost classification is crucial for making informed business decisions. By understanding the true cost of producing goods, companies can set appropriate prices, manage expenses effectively, and identify areas for improvement. Ignoring these principles can lead to misinformed pricing strategies and ultimately, financial instability.
For example, if a company incorrectly classifies selling expenses as manufacturing overhead, it may overestimate the cost of goods sold and underestimate its gross profit. This could lead to setting prices that are too high, potentially losing sales to competitors.
Conclusion: Beyond the Bottom Line
The distinction between manufacturing and non-manufacturing costs might seem like a dry accounting exercise, but it's a crucial element in the complex equation of business success. It's about understanding where resources are being allocated and making informed decisions to optimize efficiency and profitability. By correctly identifying and categorizing costs, businesses can gain a clearer picture of their financial health and navigate the ever-changing economic landscape with greater confidence.
Ultimately, the ability to differentiate manufacturing costs from non-manufacturing expenses empowers businesses to operate more effectively, innovate more strategically, and build a sustainable future. It’s a testament to the power of sound financial management in driving long-term success.


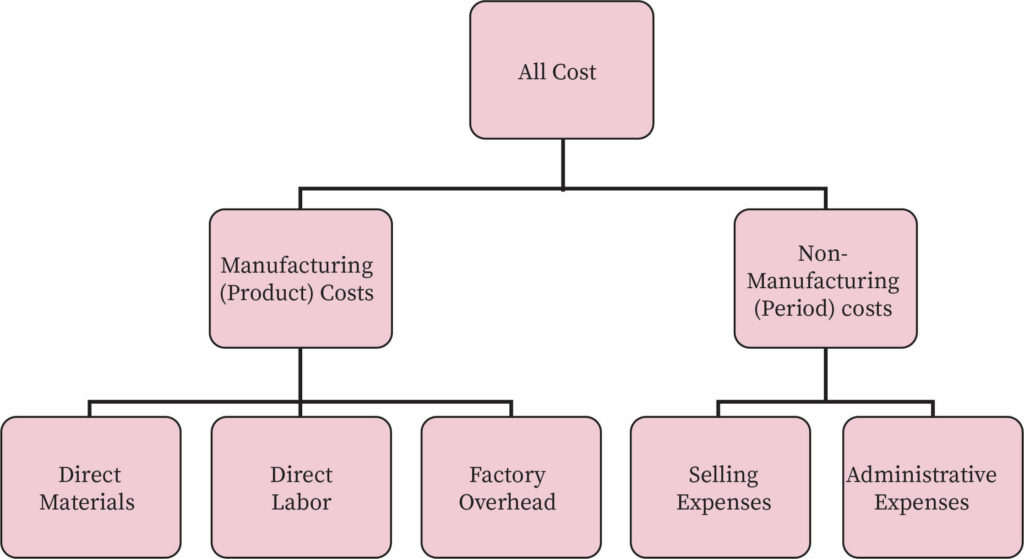
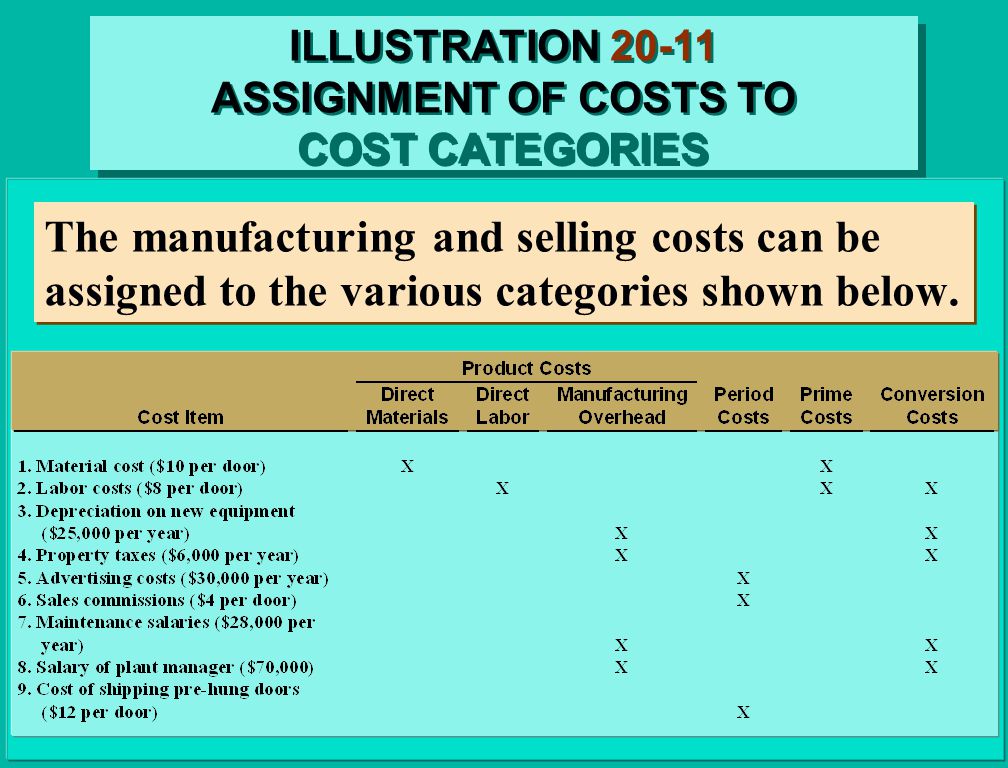
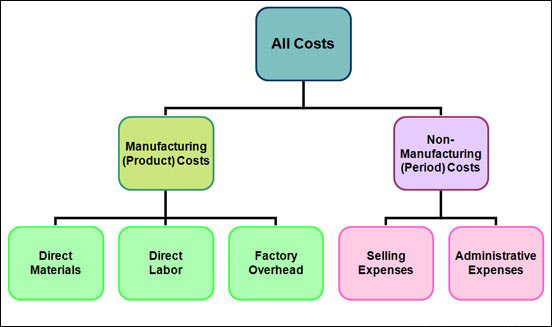

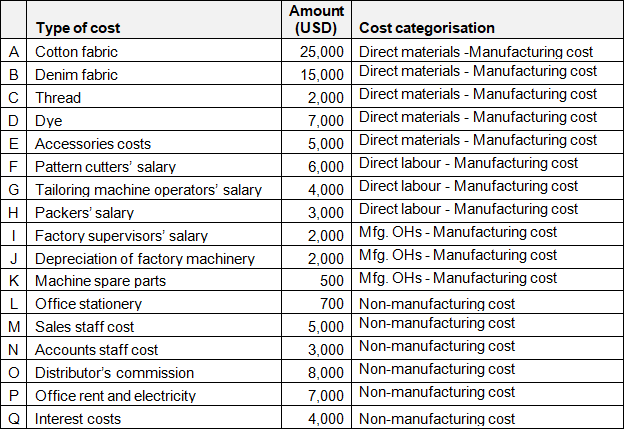
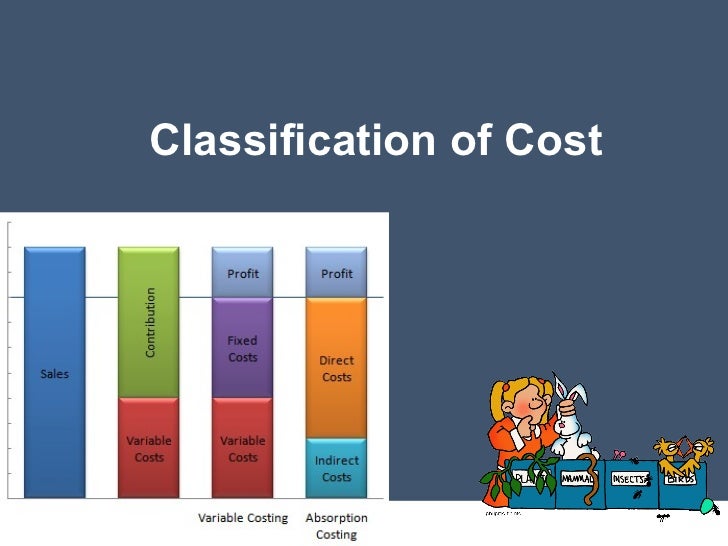
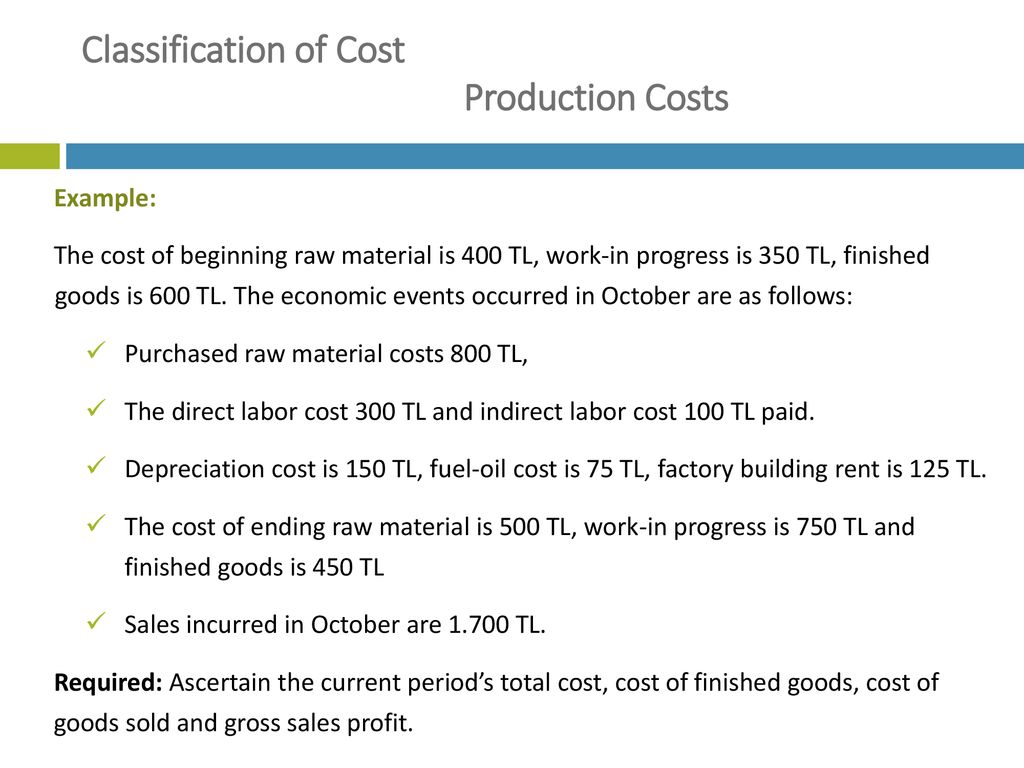
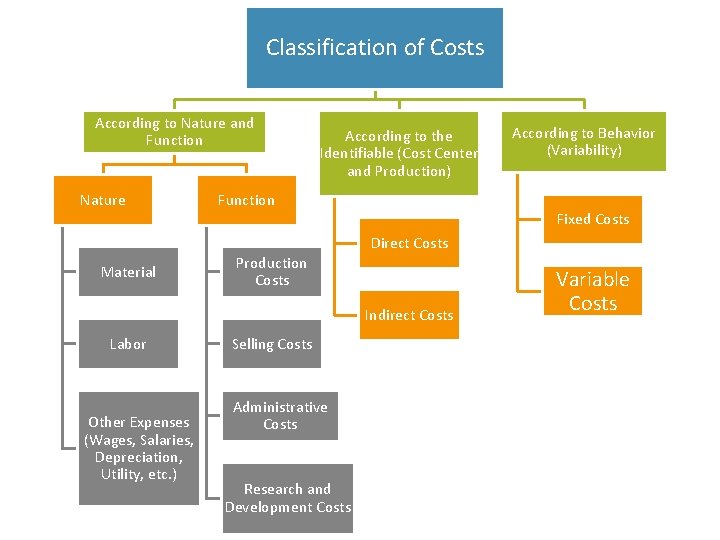
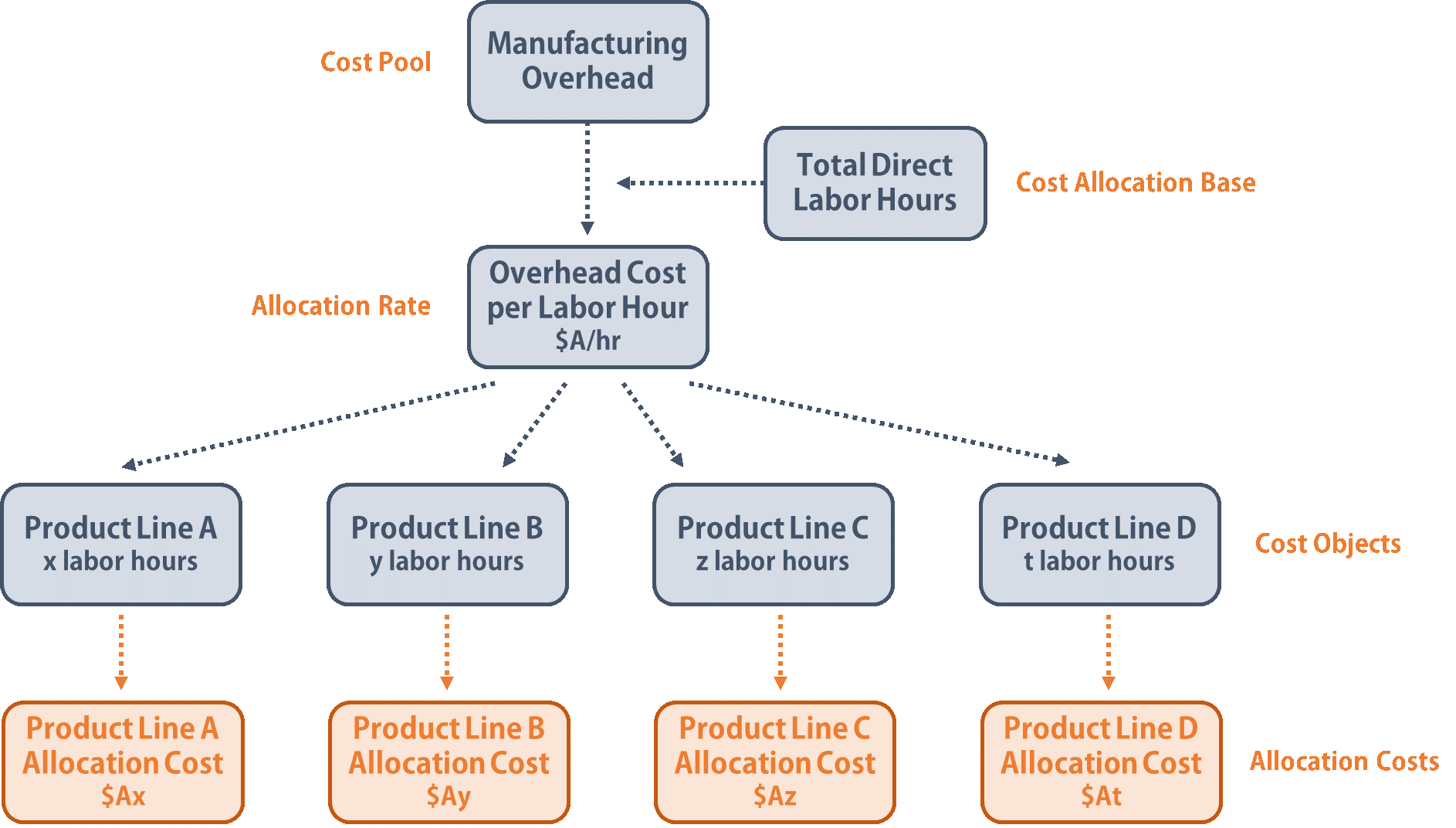

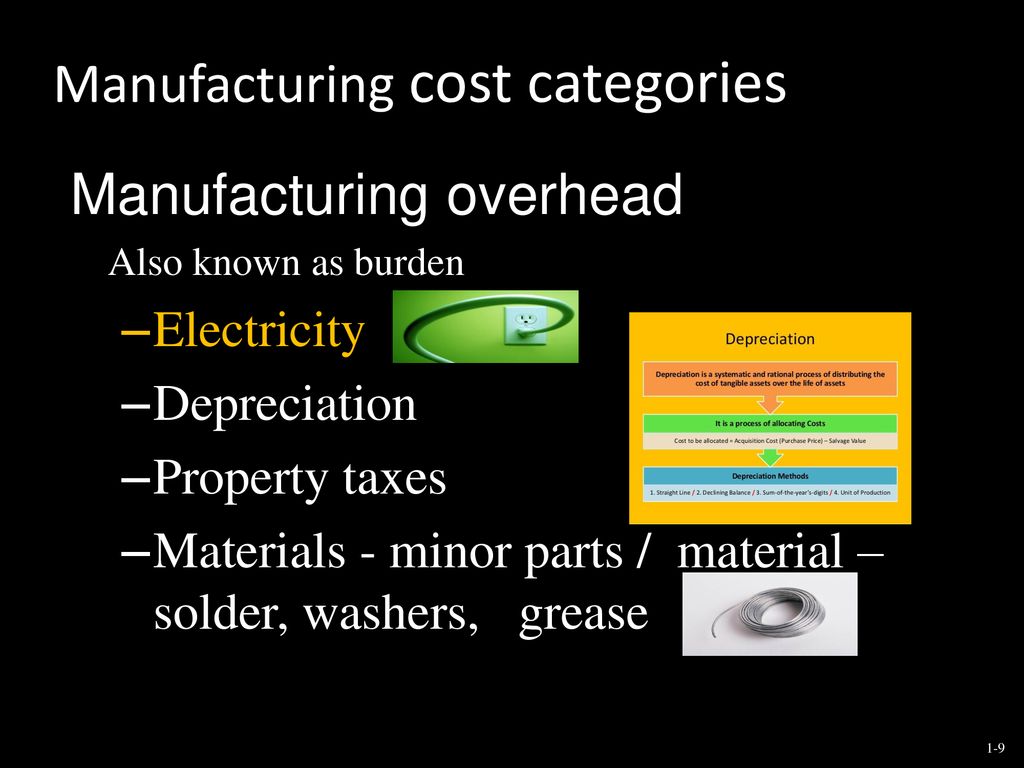

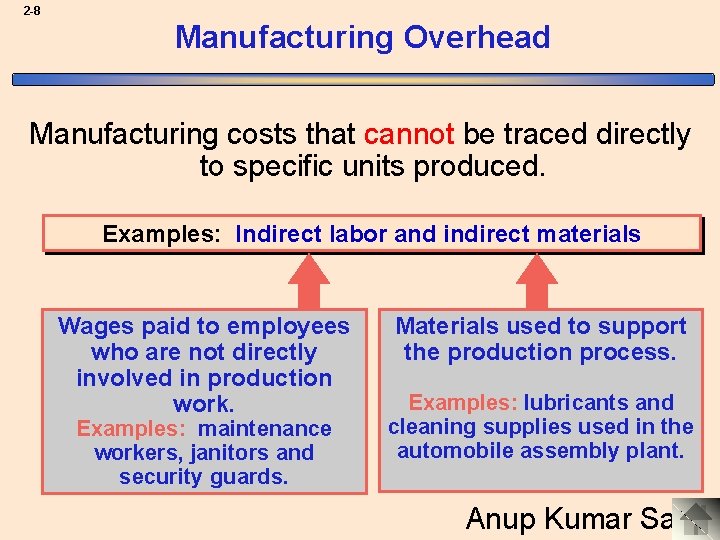

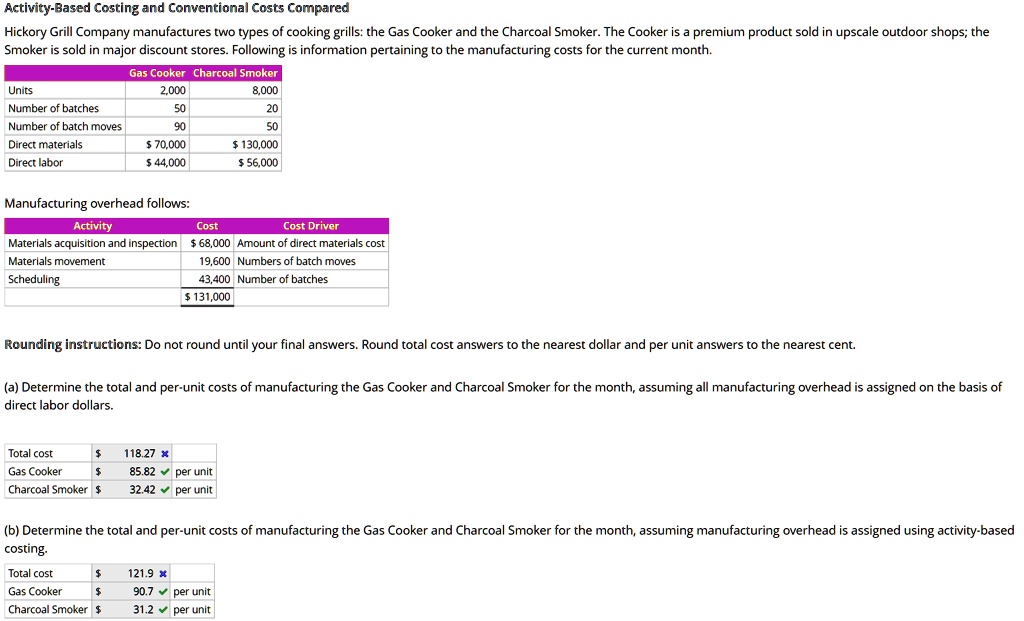
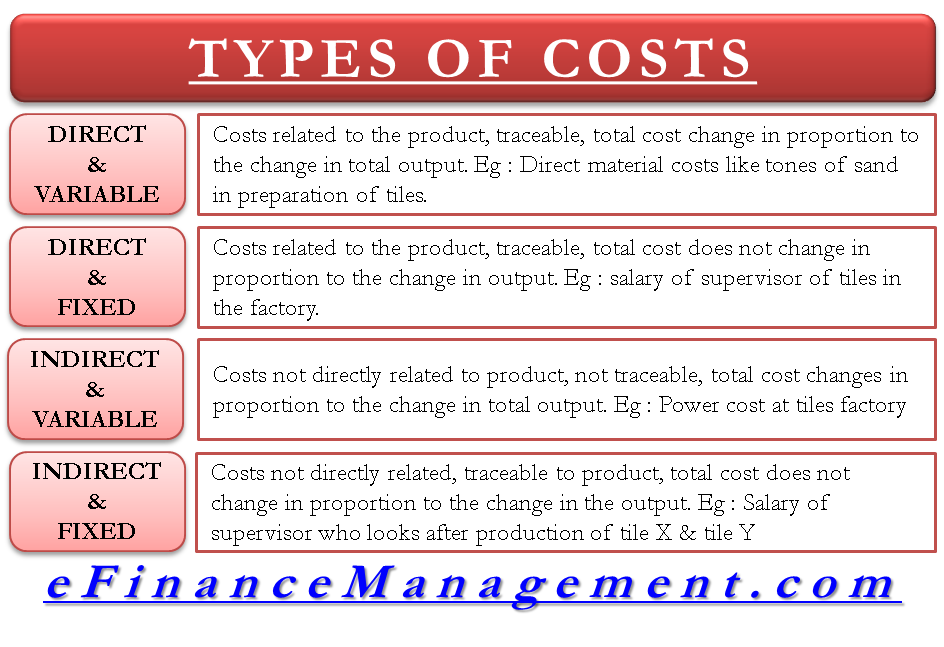