Within The Relevant Range Variable Costs Can Be Expected To
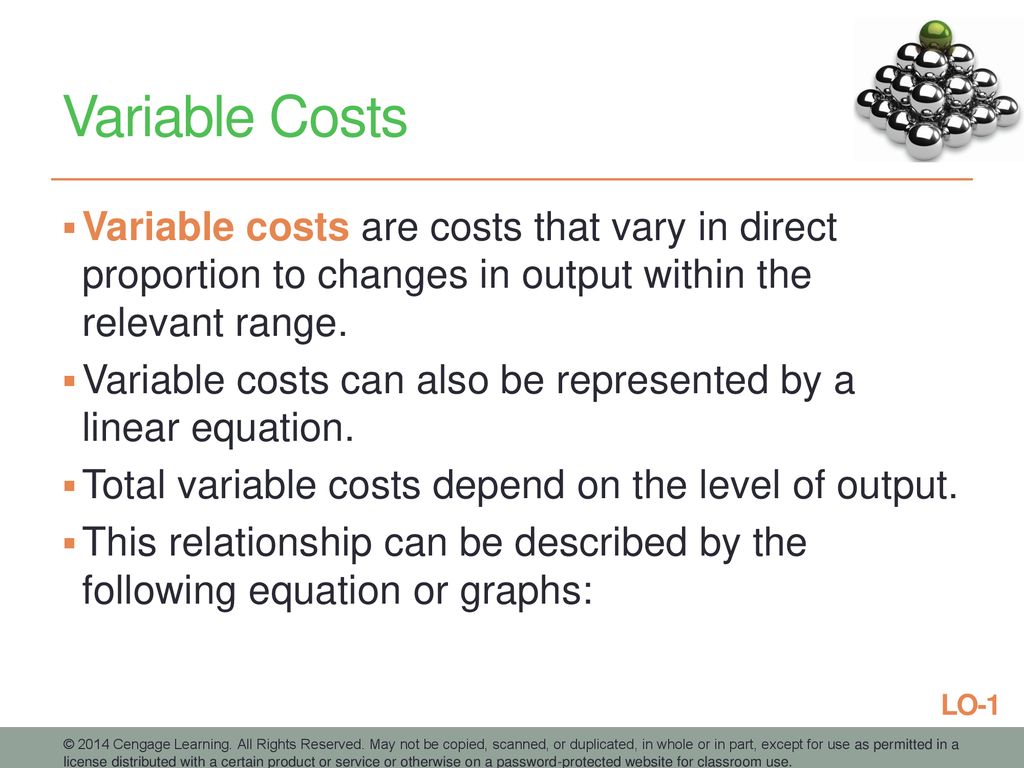
The relentless churn of economic forces keeps businesses walking a tightrope, balancing costs and revenue to survive and thrive. One fundamental concept guiding these decisions is the understanding of cost behavior, particularly how variable costs react within defined operational parameters. A misjudgment here can spell disaster, leading to inaccurate pricing, flawed budgeting, and ultimately, financial instability.
At the heart of effective cost management lies the concept of the relevant range. This range represents the specific activity level within which a business expects to operate, and where cost behavior patterns remain predictable. Specifically, within the relevant range, variable costs are *expected* to maintain a direct and proportional relationship with activity levels, a cornerstone principle for cost accounting and managerial decision-making.
Understanding the Relevant Range
The relevant range is not an unlimited expanse. It is defined by the capacity and operational constraints of a business. For example, a factory might have a relevant range of production between 5,000 and 15,000 units per month.
Beyond this range, costs may no longer behave in a predictable, linear fashion. This is due to factors like the need for additional equipment, hiring more staff at different pay scales, or facing bulk purchase discounts on materials.
Variable Costs: The Proportional Dance
Variable costs are those that change in direct proportion to the level of activity. Raw materials, direct labor (if paid on an hourly basis), and sales commissions are classic examples.
Within the relevant range, if production doubles, the total variable cost is expected to double as well. This predictable relationship allows businesses to accurately forecast expenses based on anticipated sales volume, facilitating informed pricing decisions and profitability analysis.
The Crucial "Expected To" Caveat
The phrase "expected to" is essential because it acknowledges that real-world conditions are rarely perfectly aligned with theoretical models. External factors can disrupt the anticipated linear relationship between activity and variable costs.
Supply chain disruptions, for instance, can drive up the price of raw materials, increasing the variable cost per unit even within the relevant range. Similarly, unexpected increases in energy costs can impact production expenses.
Real-World Examples and Industry Perspectives
Consider a small bakery producing artisan bread. Within its relevant range, each loaf requires a consistent amount of flour, water, and labor, making these variable costs directly proportional to production volume.
However, if the bakery exceeds its oven's capacity, forcing it to purchase a second oven, its fixed costs increase, shifting the entire cost structure. Similarly, a sudden wheat shortage would increase the cost per loaf, disrupting the expected variable cost behavior.
Dr. Anya Sharma, a professor of accounting at the University of California, Berkeley, emphasizes the practical limitations of the relevant range. "While a valuable tool for budgeting and forecasting, managers must remain vigilant about external factors that can influence cost behavior," she notes. "Regular monitoring and adjustments to cost models are crucial for maintaining accuracy."
According to data from the Bureau of Labor Statistics (BLS), fluctuations in commodity prices are a consistent challenge for businesses trying to predict variable costs. The BLS reports on changes in the Producer Price Index (PPI), which reflects the average change over time in the selling prices received by domestic producers for their output.
Analyzing PPI data provides businesses with insights into potential shifts in raw material costs. This allows for proactive adjustments to pricing and production strategies.
Breaking the Range: What Happens?
Operating outside the relevant range forces businesses to re-evaluate their cost assumptions. Fixed costs may jump in increments, creating a step-fixed cost structure.
Variable costs might exhibit economies of scale, decreasing per unit as production volume increases, or diseconomies of scale, increasing per unit due to inefficiencies and resource constraints.
A manufacturing plant might need to invest in new machinery or rent additional space to increase production beyond the existing range. This dramatically changes the cost landscape and requires a completely new set of analyses and strategies.
The Future of Cost Management
Advanced data analytics and machine learning are playing an increasingly important role in cost management. These technologies allow businesses to develop more sophisticated cost models that can adapt to changing market conditions and predict cost behavior with greater accuracy.
AI-powered systems can analyze vast amounts of data, including market trends, supplier information, and internal operational data, to identify potential cost fluctuations and optimize resource allocation.
The future of cost management lies in leveraging these technologies to enhance the understanding of the relevant range and to create more resilient and adaptable business strategies. This will ultimately improve decision making within the organization to achieve better outcome.




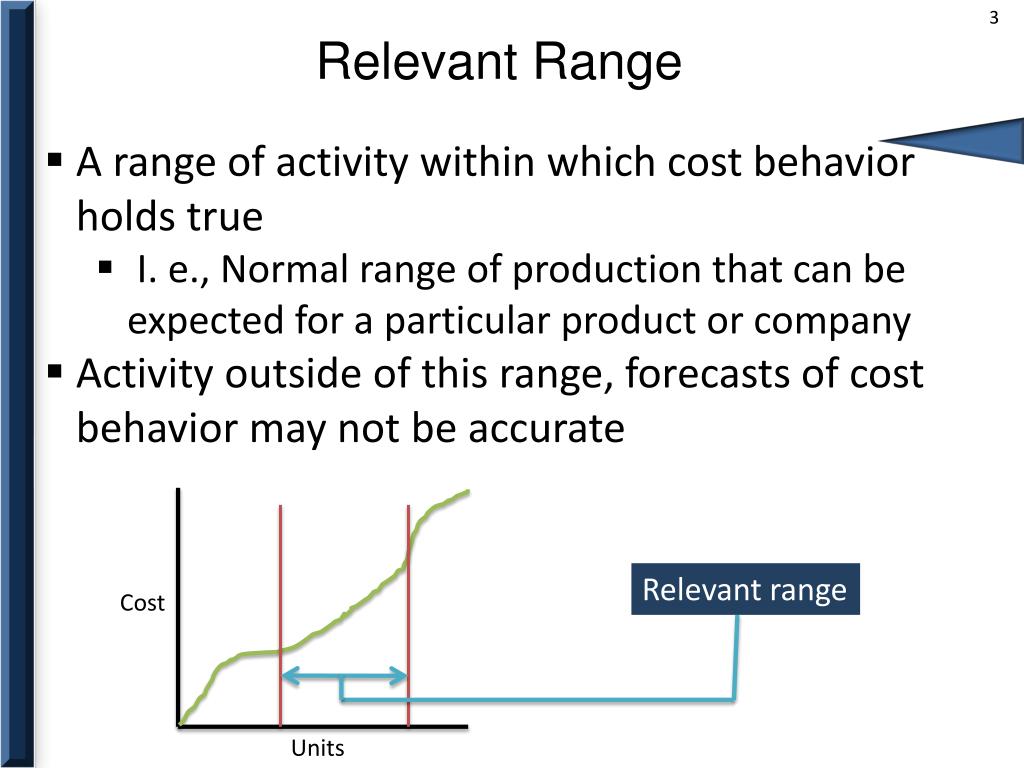

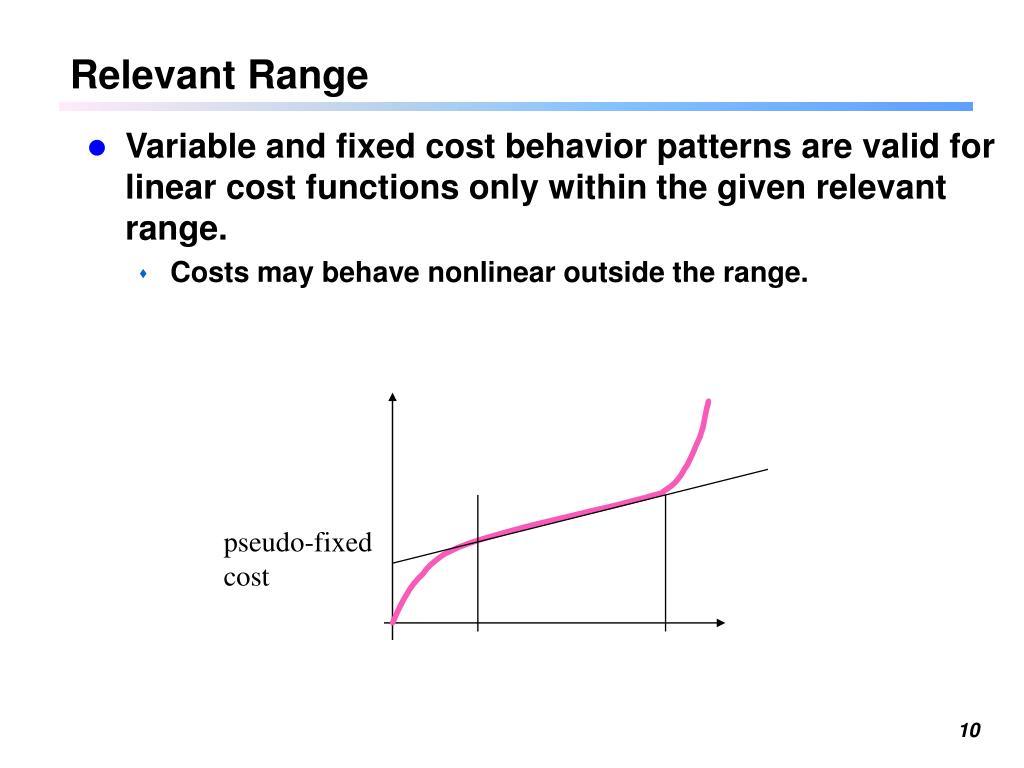
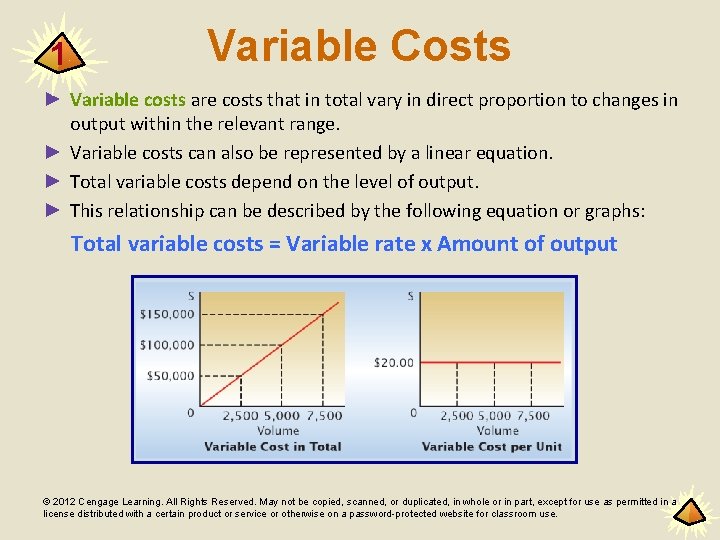


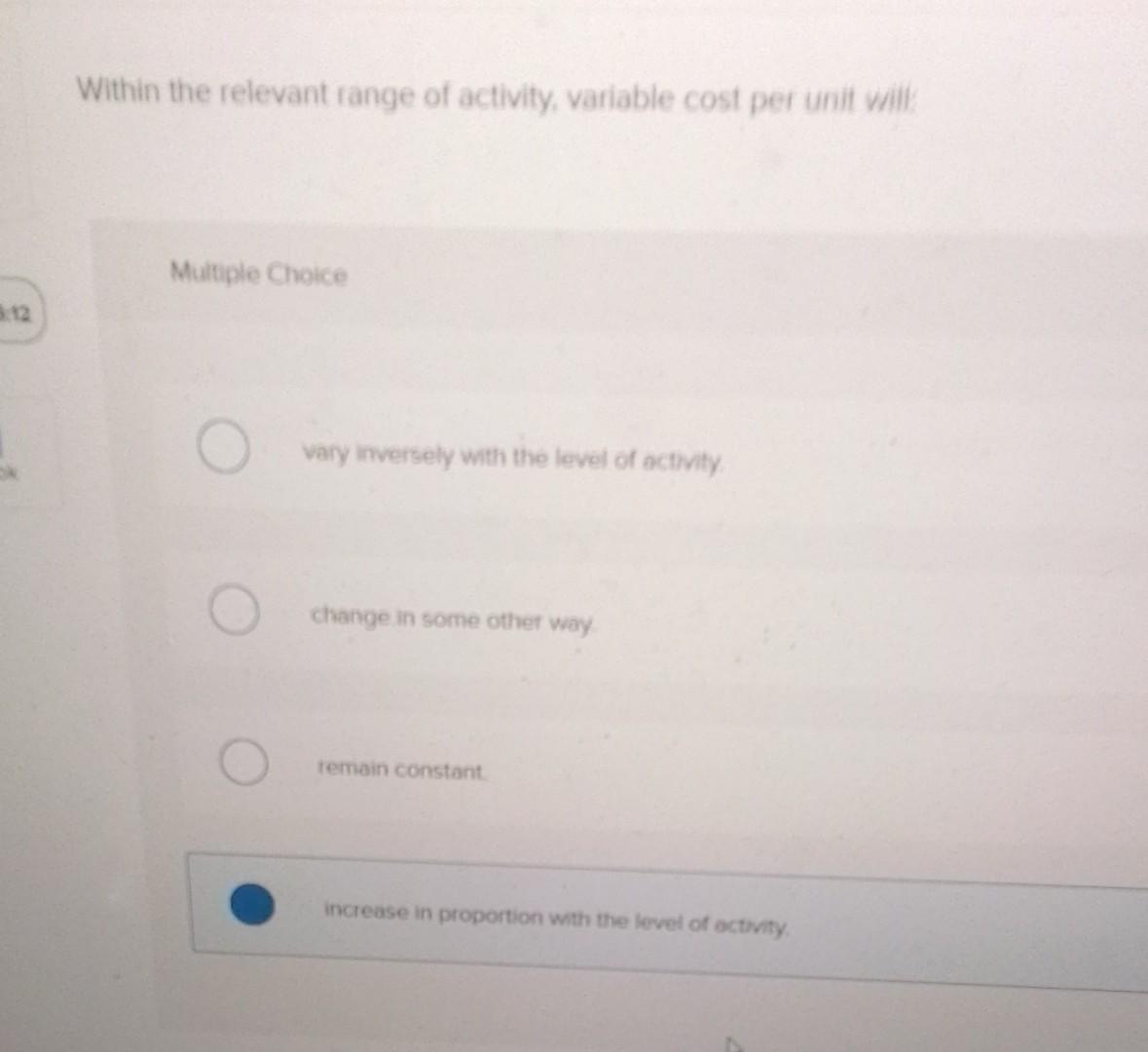

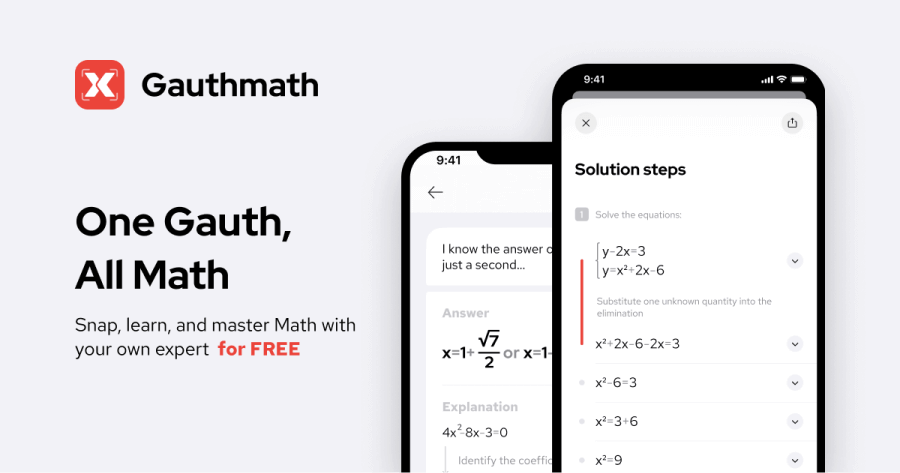
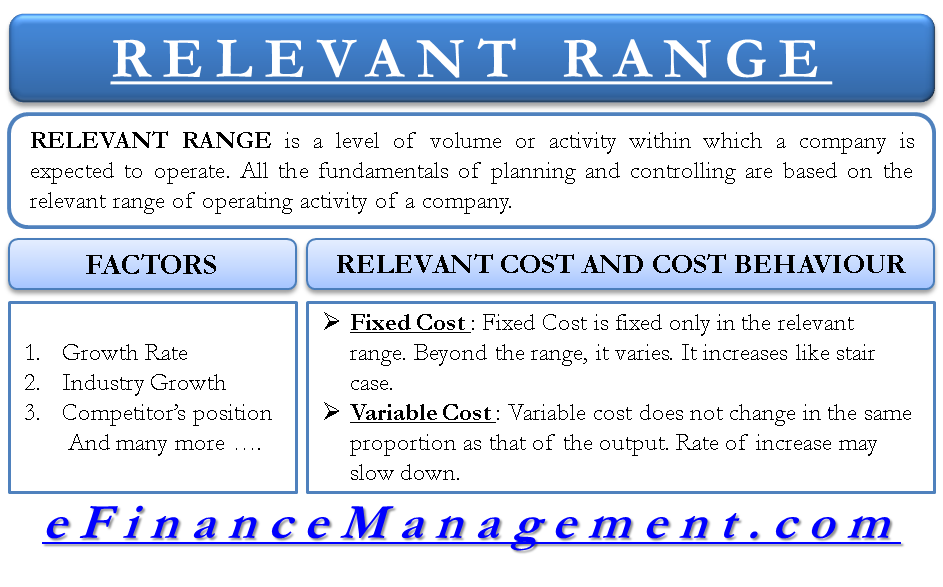
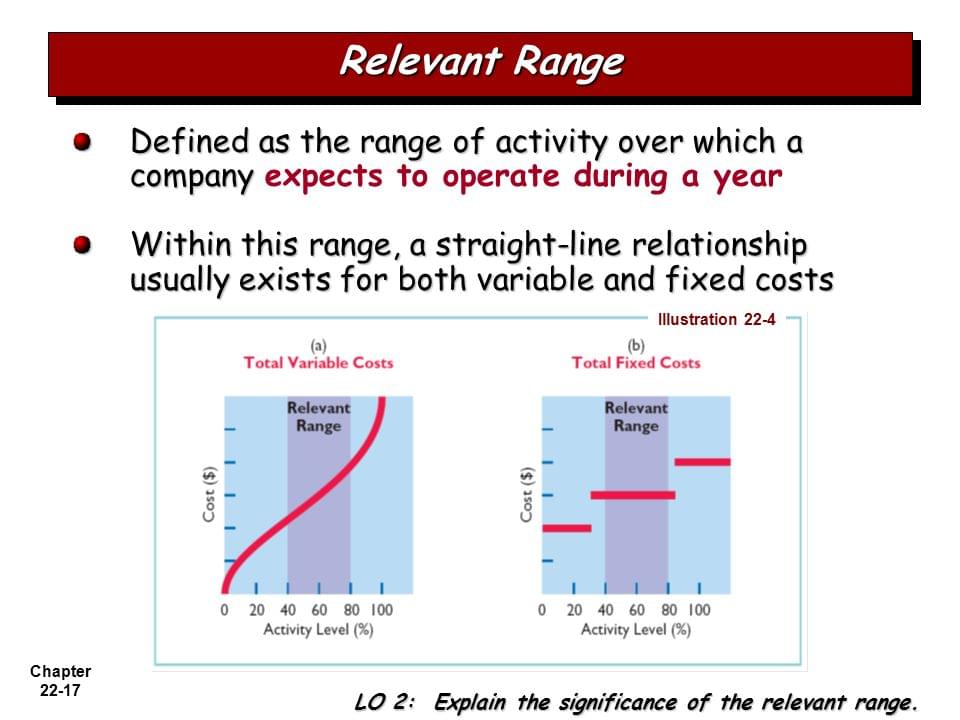
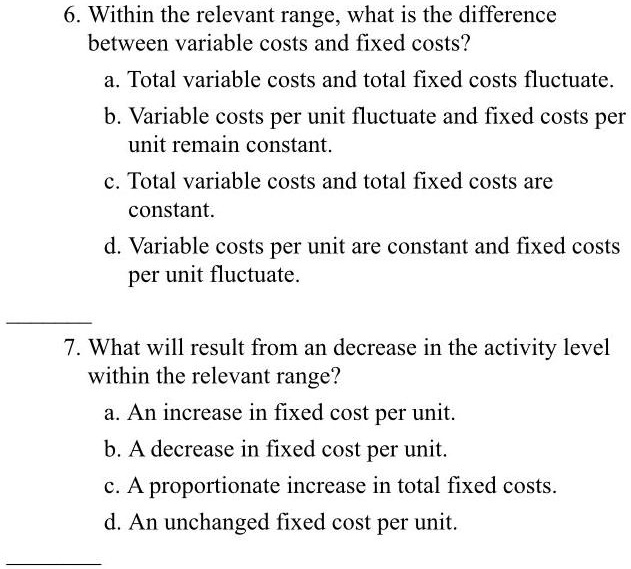
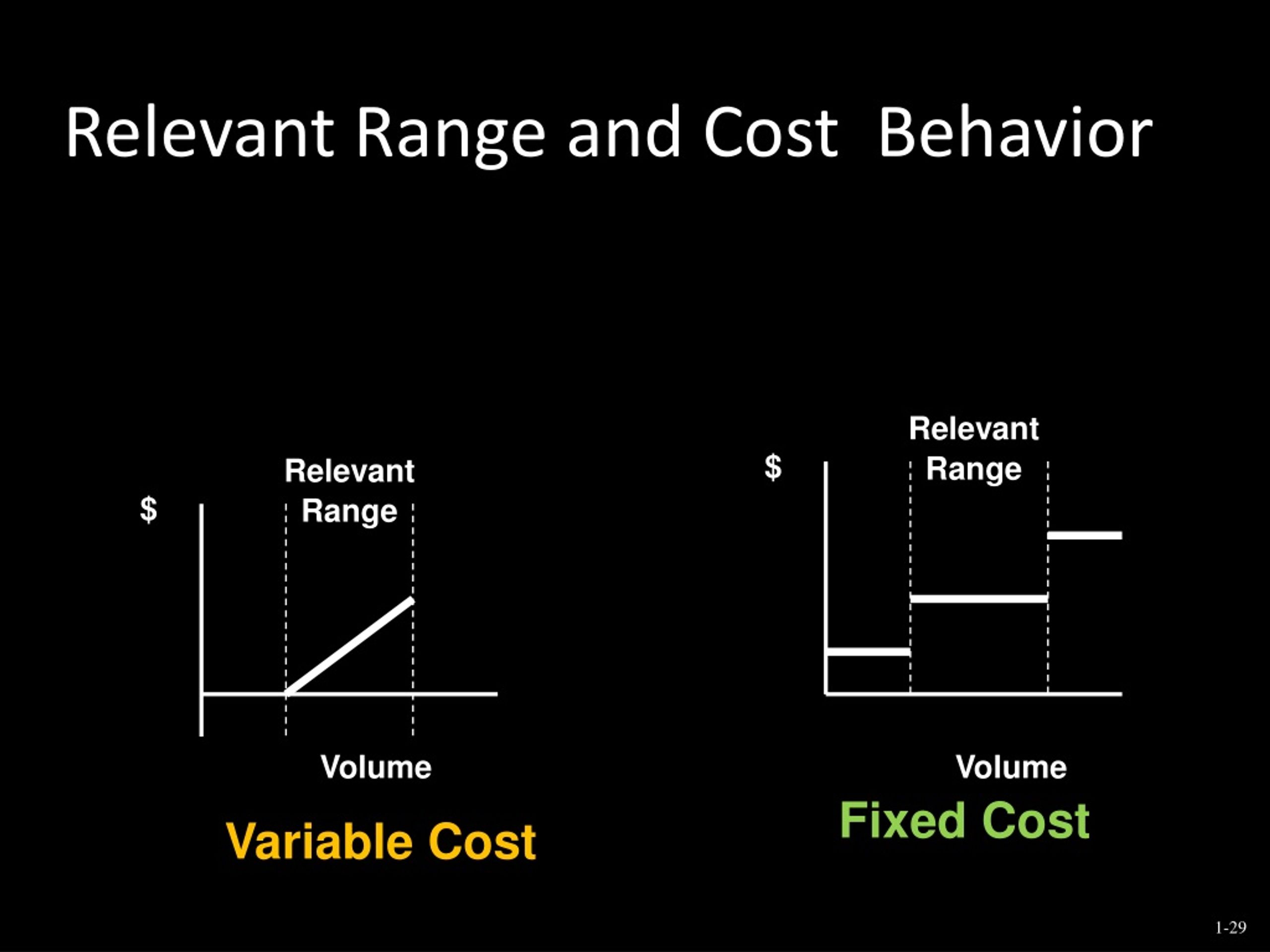