A Company's Inventory Position Is Defined As

Imagine walking into your favorite neighborhood bakery. The aroma of freshly baked bread fills the air, tempting you with golden croissants and decadent cakes. But behind the scenes, past the display cases brimming with delicious treats, lies a carefully managed system. This system ensures the bakery has enough flour, sugar, and eggs to meet the daily demand without letting ingredients spoil and go to waste. This balancing act, in essence, reflects the core concept of a company's inventory position.
At its heart, a company's inventory position is a comprehensive snapshot of all the goods a business owns and intends to sell. It encompasses everything from raw materials waiting to be transformed into finished products to the items sitting on store shelves ready for purchase. More than just a simple count, it's a dynamic indicator reflecting a company's ability to meet customer demand, manage costs, and ultimately, drive profitability. A strong inventory position allows a company to confidently navigate the complexities of the market, while a weak one can lead to lost sales, increased expenses, and a damaged reputation.
Understanding the Components of Inventory Position
To truly grasp the significance of a company's inventory position, it's essential to understand its key components. These elements work together to paint a complete picture of a company's resources and their potential for generating revenue.
Raw Materials: The Foundation
These are the basic inputs a company uses to create its products. For a baker, it's the flour, sugar, butter, and eggs. For a furniture manufacturer, it might be wood, fabric, and metal. Maintaining an adequate supply of raw materials is crucial to avoid production delays and ensure consistent product quality.
Work-in-Progress (WIP): The Transformation Stage
WIP refers to goods that are currently undergoing the manufacturing process. These are items that have been started but are not yet complete and ready for sale. Monitoring WIP levels allows companies to identify bottlenecks in their production processes and optimize efficiency.
Finished Goods: Ready for Sale
These are the completed products ready to be sold to customers. Maintaining an optimal level of finished goods inventory is a delicate balancing act. Too little inventory can lead to stockouts and lost sales, while too much can result in storage costs, obsolescence, and potential price reductions.
Maintenance, Repair, and Operations (MRO) Inventory
While not directly incorporated into the final product, MRO inventory includes items necessary to keep the production process running smoothly. This can range from spare parts for machinery to cleaning supplies for the factory floor. Ensuring the availability of MRO inventory minimizes downtime and prevents disruptions to operations.
The Significance of Inventory Management
Effectively managing a company's inventory position is not just about counting items; it's a strategic imperative that impacts nearly every aspect of the business. Proper inventory management can lead to increased profitability, improved customer satisfaction, and a stronger competitive advantage. Failing to manage inventory effectively, on the other hand, can have serious consequences.
Poor inventory management can result in stockouts, leading to frustrated customers and lost sales opportunities. Holding excess inventory ties up valuable capital, increasing storage costs and the risk of obsolescence, especially in industries with rapidly changing technology or fashion trends. Inefficient inventory processes can also lead to inaccurate forecasting, production inefficiencies, and higher operational costs. Data from a 2023 report by the Aberdeen Group highlights that companies with best-in-class inventory management practices experience a 15% reduction in inventory holding costs compared to their peers.
Strategies for Optimizing Inventory Position
Several strategies exist for optimizing a company's inventory position, each tailored to specific industry needs and business goals. The goal is to strike a balance between having enough inventory to meet customer demand and minimizing the costs associated with holding excess stock.
Just-in-Time (JIT) Inventory
This strategy involves receiving materials only when they are needed in the production process, minimizing inventory holding costs. JIT requires close coordination with suppliers and a reliable supply chain. This system, pioneered by Toyota, reduces waste and improves efficiency.
Economic Order Quantity (EOQ)
EOQ is a mathematical formula used to determine the optimal order quantity that minimizes total inventory costs, including ordering costs and holding costs. It helps companies determine the ideal quantity of inventory to order at a time.
ABC Analysis
This method categorizes inventory items based on their value and importance. "A" items are high-value items that require close monitoring, "B" items are medium-value, and "C" items are low-value. This allows companies to focus their resources on managing the most important inventory items.
Demand Forecasting
Accurate demand forecasting is essential for effective inventory management. By predicting future demand, companies can adjust their inventory levels accordingly. Tools like statistical analysis, machine learning, and market research can be used for demand forecasting.
"Effective inventory management is no longer just about tracking numbers; it's about leveraging data to make informed decisions and create a more agile and responsive supply chain," says Sarah Johnson, a supply chain management expert at Gartner.
Technology's Role in Modern Inventory Management
In today's fast-paced business environment, technology plays a crucial role in optimizing inventory positions. Sophisticated software systems and advanced analytics provide companies with real-time visibility into their inventory, enabling them to make data-driven decisions.
Enterprise Resource Planning (ERP) systems integrate all aspects of a company's operations, including inventory management, into a single system. This provides a comprehensive view of the entire supply chain. Warehouse Management Systems (WMS) help companies manage their warehouse operations more efficiently, improving inventory accuracy and reducing costs. Inventory optimization software uses advanced algorithms to analyze demand patterns and optimize inventory levels.
Examples of Inventory Position in Action
Consider a clothing retailer preparing for the holiday season. They carefully analyze historical sales data and current fashion trends to forecast demand for various clothing items. Based on this forecast, they adjust their inventory levels, ordering more of popular items and reducing orders for less popular ones. They might also implement a promotional campaign to clear out slow-moving inventory before the new year. If they do this correctly, they will be able to meet the demands of the holiday shoppers without being stuck with excessive inventory after the holidays. This proactive approach to inventory management helps maximize sales and minimize losses.
Or, consider a high-tech manufacturer producing smartphones. They rely on a complex global supply chain to source components from various suppliers. To ensure timely production, they need to carefully manage their inventory of components, such as processors, screens, and batteries. They may use a JIT system to receive components just in time for production, reducing inventory holding costs. They also need to monitor the quality of components to prevent defects and ensure the smooth flow of production.
The Future of Inventory Management
The future of inventory management is likely to be driven by further advancements in technology and increasing complexity in global supply chains. Artificial intelligence (AI) and machine learning (ML) will play an increasingly important role in demand forecasting, inventory optimization, and supply chain management. Businesses will need to increasingly consider sustainability and ethical sourcing in their inventory management decisions.
Technologies such as blockchain can enhance supply chain transparency and traceability, improving inventory accuracy and reducing the risk of counterfeiting. Businesses will need to adopt a more agile and responsive approach to inventory management, adapting to changing market conditions and customer demands. As stated in a recent report by Deloitte, "The future of supply chain lies in resilience, agility, and a relentless focus on customer needs, all underpinned by data-driven decision-making."
Ultimately, a company's inventory position is more than just a number; it is a reflection of its operational efficiency, its understanding of the market, and its commitment to meeting customer needs. It's a story told in raw materials, work in progress, and finished goods, a story that, when managed well, leads to success and sustainability. As we leave the bakery with our freshly baked goods, we can appreciate the careful dance of inventory management that made it all possible – a lesson applicable far beyond the realm of croissants and cakes.

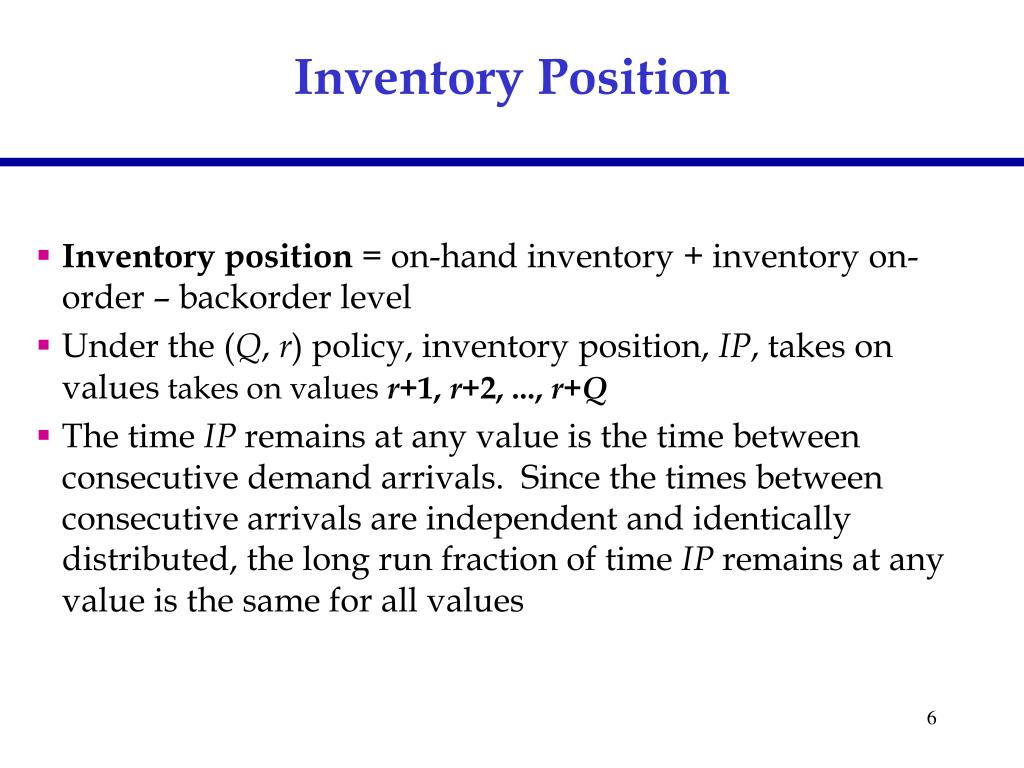
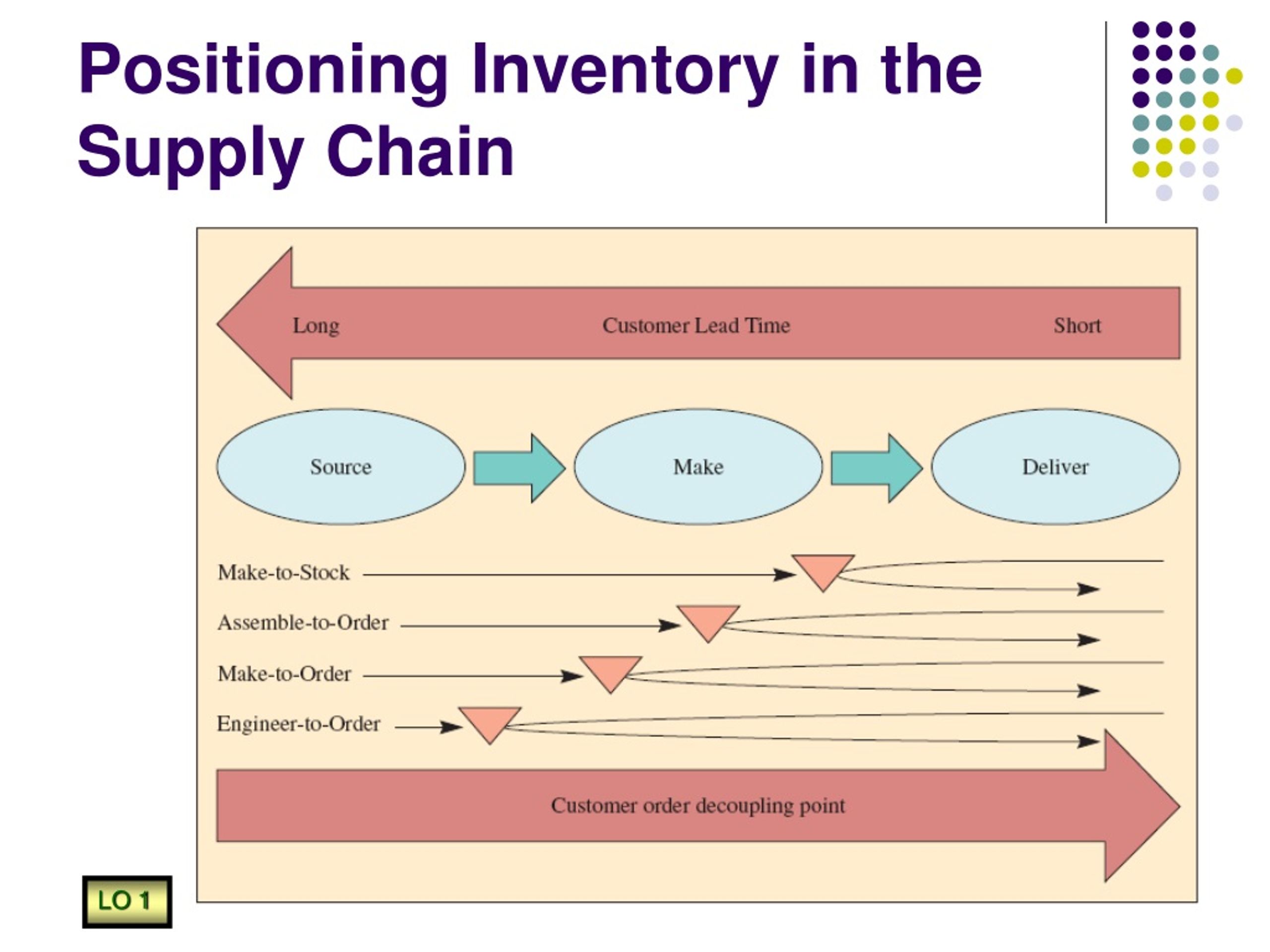
:max_bytes(150000):strip_icc()/TermDefinitions_Inventory_finalv2-174a95eaeac3409d971256da7ecb164b.jpg)
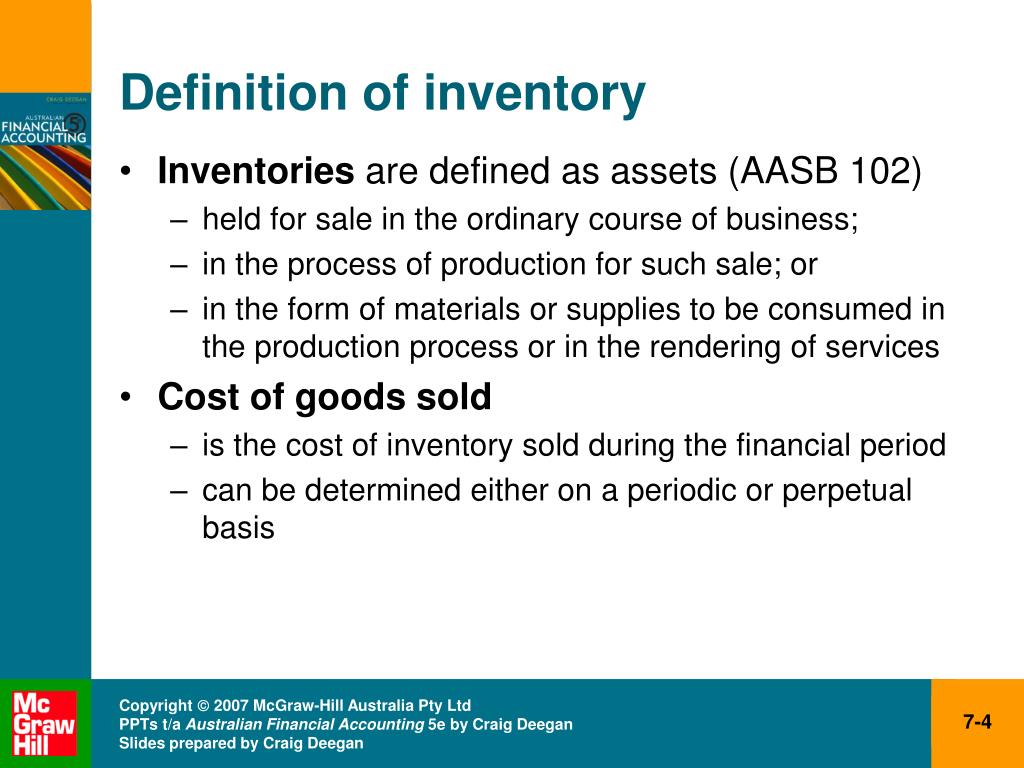

![A Company's Inventory Position Is Defined As Easy Inventory Position Definition [+3 Step Formula]](https://b3979894.smushcdn.com/3979894/wp-content/uploads/2024/07/Secrets-behind-inventory-position-2-1024x640.jpg?lossy=2&strip=1&webp=1)

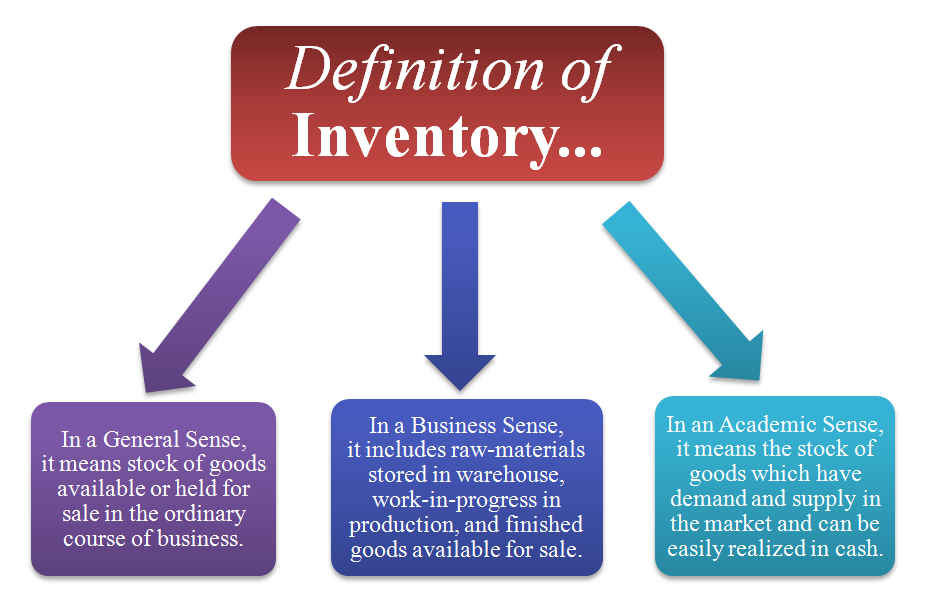
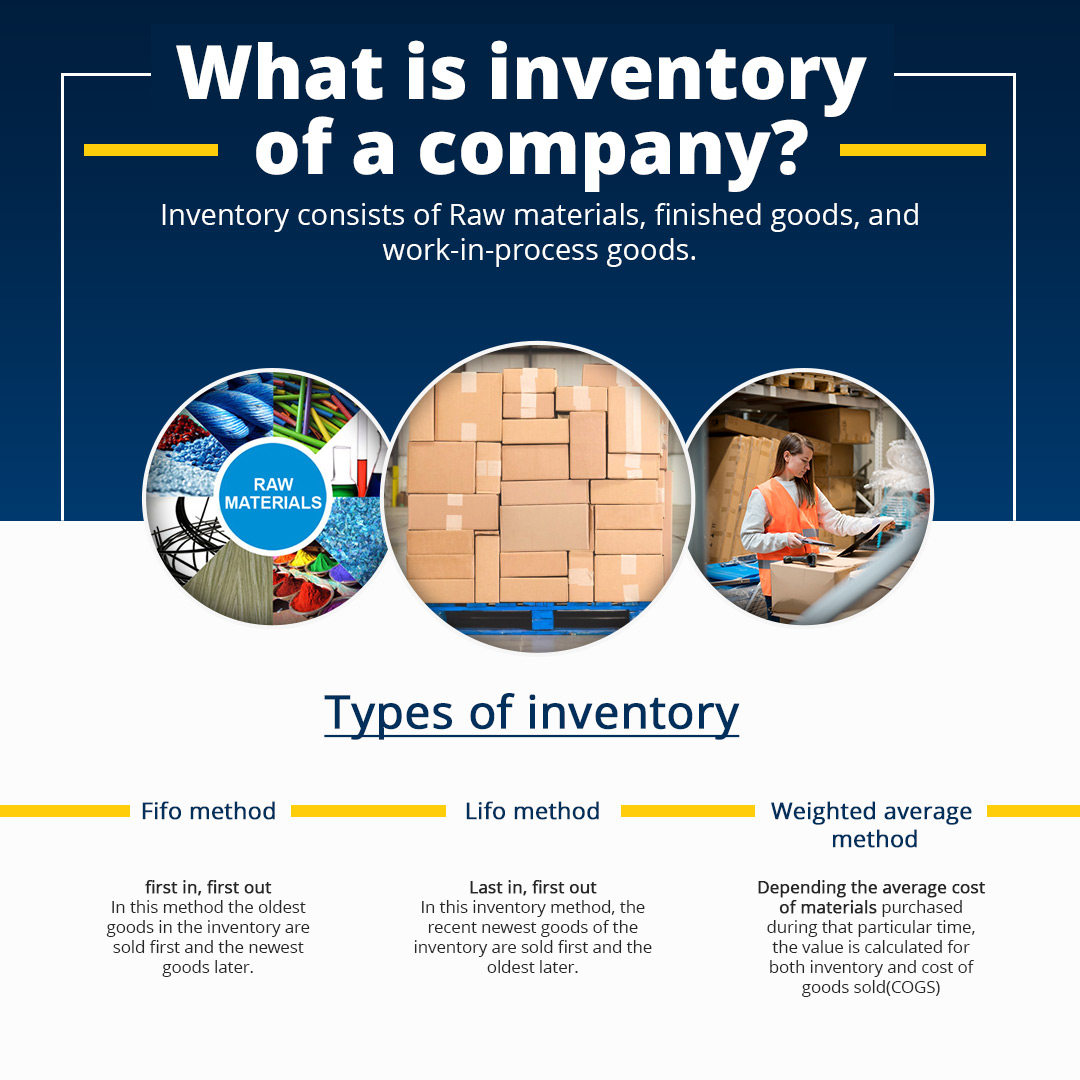
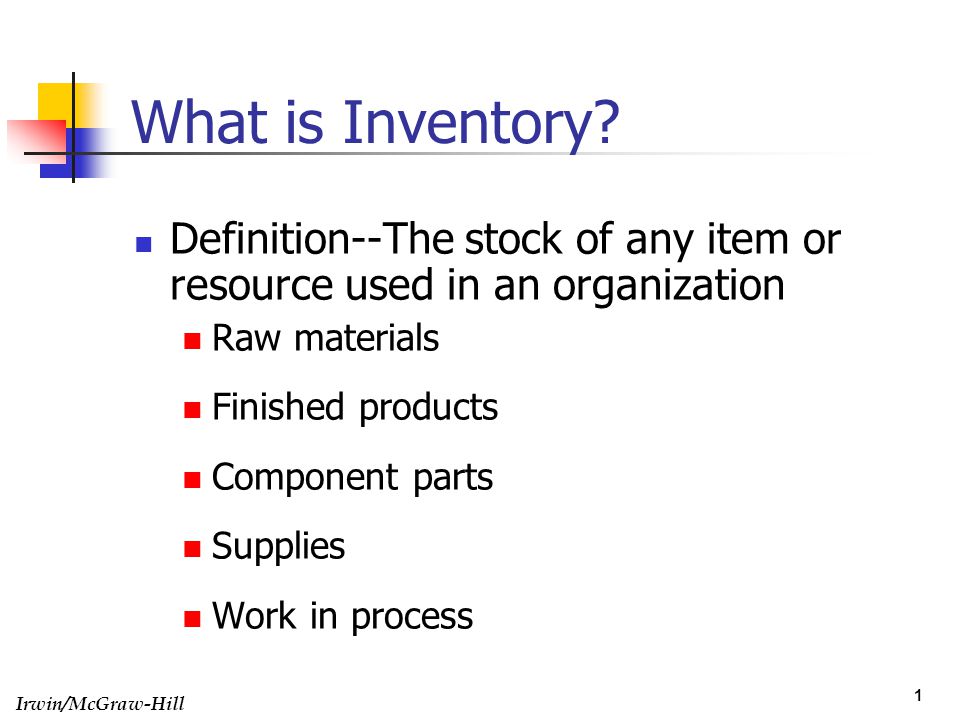
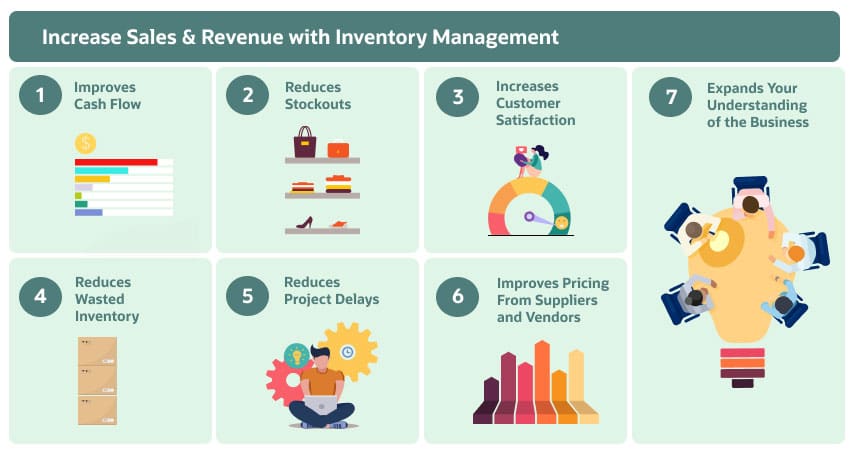
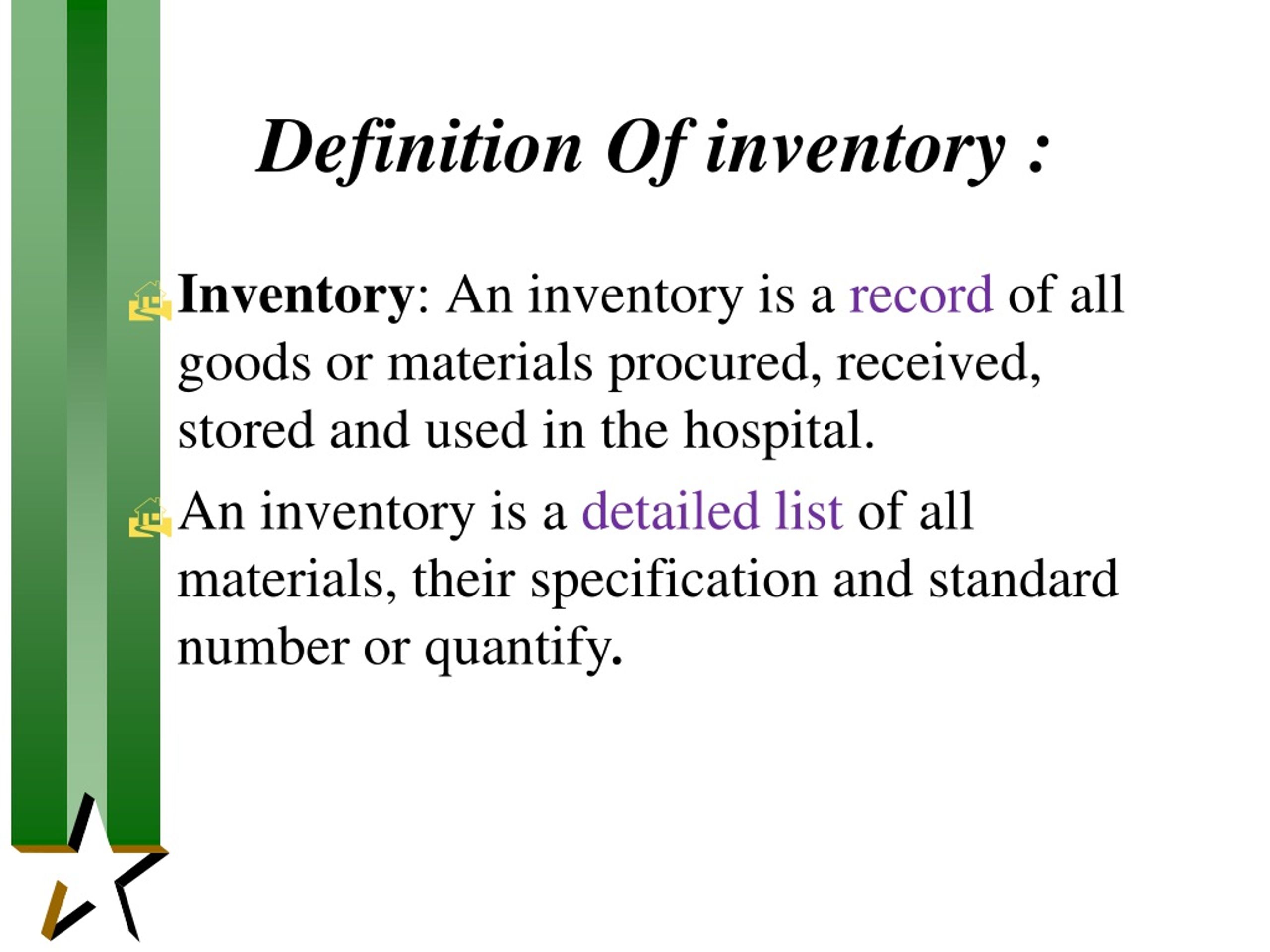
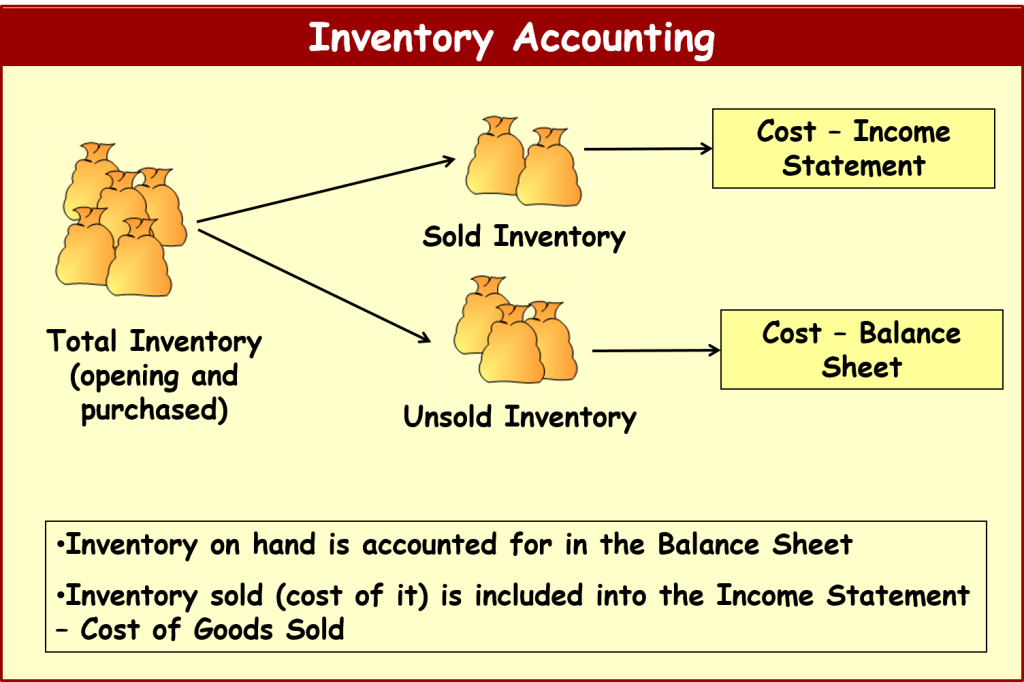
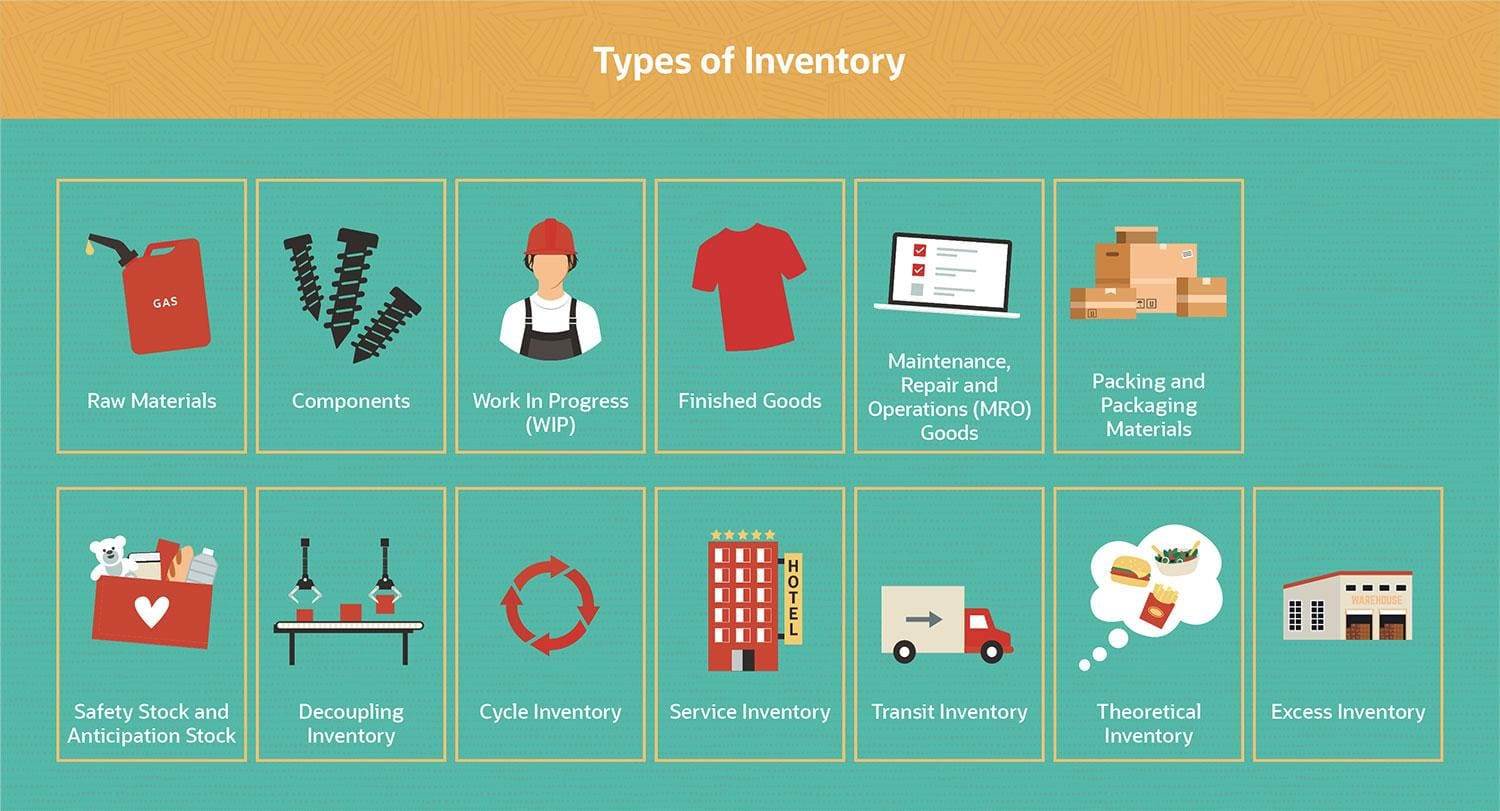
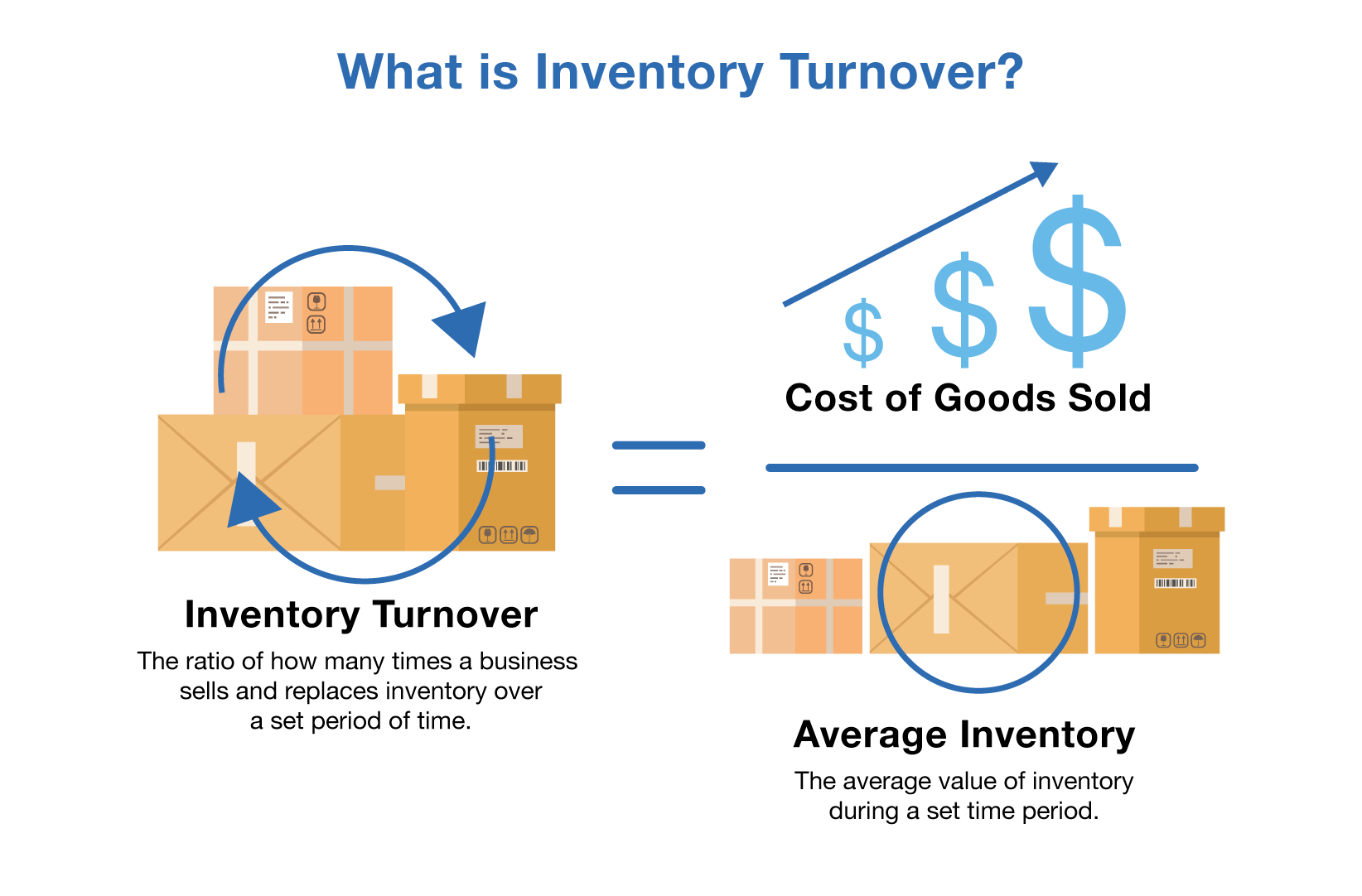
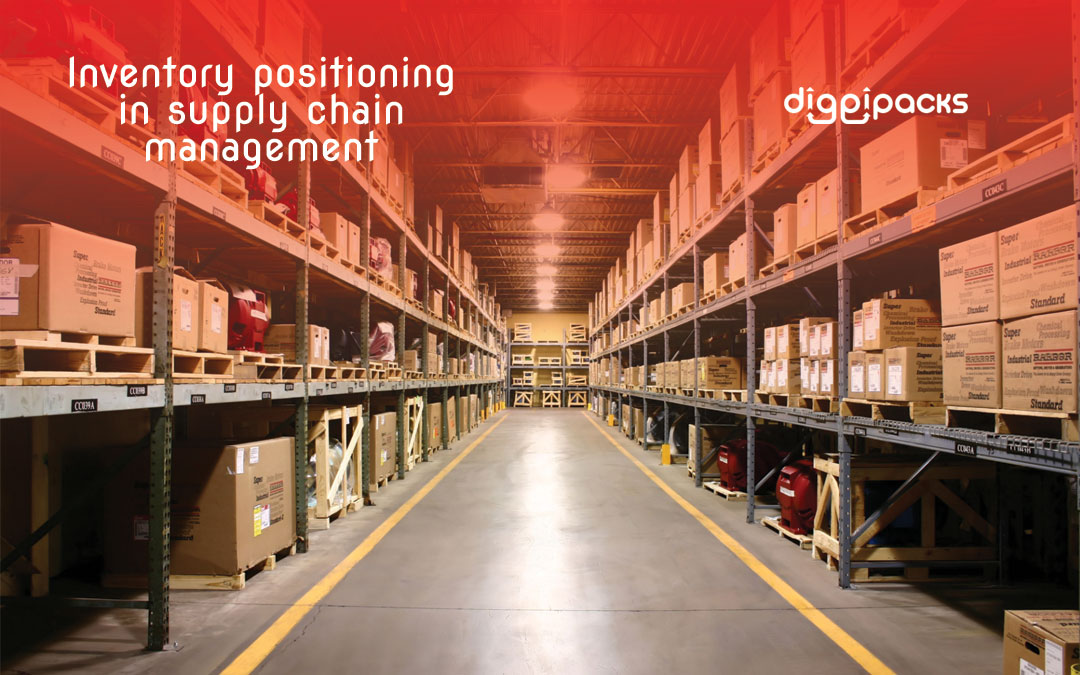
:max_bytes(150000):strip_icc()/inventory-management-8595e839c2884128997ca77f00a8da2b.jpg)