Average Cost Of Soda 2 Liter
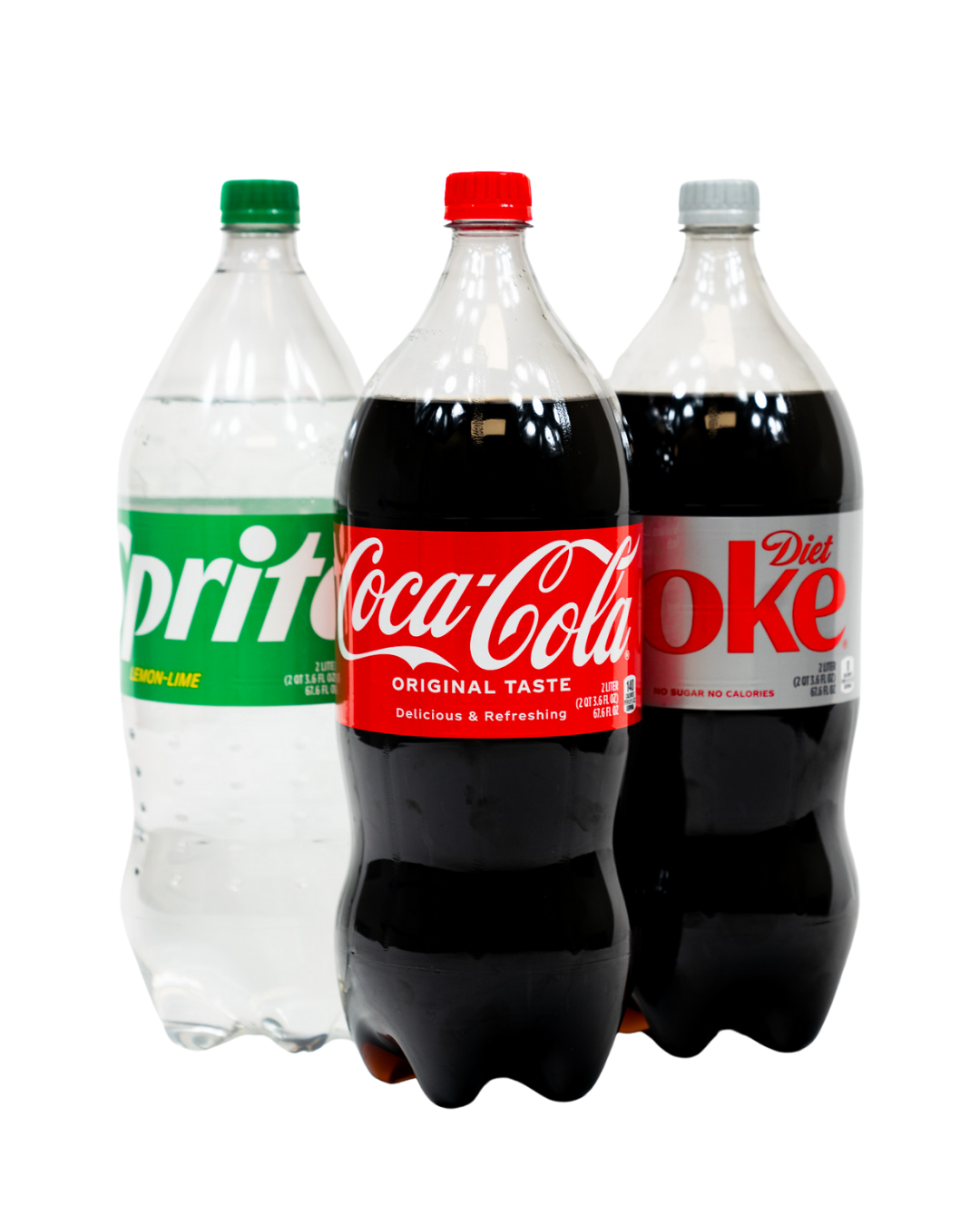
The simple pleasure of sharing a 2-liter bottle of soda with friends and family is increasingly impacted by rising costs. From the corner store to major supermarkets, consumers are noticing a significant shift in the price they pay for this ubiquitous beverage. This seemingly small increase reflects a larger economic story impacting the entire food and beverage industry.
The average cost of a 2-liter bottle of soda has been steadily climbing, influenced by factors ranging from supply chain disruptions to inflation. Understanding these underlying drivers is crucial for consumers trying to manage their budgets and for businesses adapting to the evolving economic landscape. This article delves into the multifaceted forces affecting soda prices and explores the potential implications for the future.
Decoding the Nut Graf: Soda Prices Under Pressure
The average national price for a 2-liter bottle of soda currently hovers around $2.00 - $2.50, depending on brand, flavor, and location. This represents an increase of approximately 15-25% compared to prices seen just a few years ago. Several key factors are contributing to this upward trend, including rising ingredient costs, increased transportation expenses, and packaging material shortages.
Supply chain bottlenecks, exacerbated by global events, play a significant role. The price of high fructose corn syrup (HFCS), a primary ingredient in many sodas, has fluctuated dramatically. This volatility directly translates into higher production costs for soda manufacturers.
Furthermore, aluminum, used for both cans and bottling equipment, has also experienced price surges. These compounding factors create a challenging environment for soda producers, who ultimately must pass some of these costs onto consumers.
Ingredient Inflation: A Bitter Pill for Soda Makers
The cost of raw materials is a primary driver of the increasing price of 2-liter soda bottles. High fructose corn syrup (HFCS), the sweetener of choice for many major brands, is heavily influenced by corn prices.
Weather patterns, geopolitical events impacting global grain markets, and government subsidies all impact the price of corn. This creates a ripple effect that significantly alters the production cost for soda manufacturers.
Beyond HFCS, other ingredients such as carbon dioxide (CO2), used for carbonation, have also seen price increases. Production disruptions and increased demand from various industries have created shortages and driven up the cost of CO2. This adds another layer of complexity and expense to the soda production process.
Transportation Troubles: Fuel Costs and Logistics
The journey from factory to store shelf is a complex and expensive process. Rising fuel costs have a direct impact on the transportation expenses associated with delivering 2-liter bottles of soda.
Trucking companies, faced with higher diesel prices, are forced to increase their rates. These increased transportation costs are inevitably passed on to consumers. This is especially true in areas geographically distant from major soda production facilities.
Labor shortages within the trucking industry further compound these issues. The scarcity of drivers contributes to delays and increased competition, driving up transportation expenses even further.
Packaging Pressures: Aluminum and Plastic Shortages
Packaging plays a critical role in the soda industry. Shortages and price increases of both aluminum and plastic have put additional pressure on manufacturers. The demand for aluminum, particularly for cans, has surged in recent years.
This demand is driven by factors such as increased consumption of canned beverages and a global shift towards more sustainable packaging options. However, production capacity has not kept pace with this increased demand, leading to shortages and price increases. Recycled polyethylene terephthalate (rPET), used to create soda bottles, is also facing increasing demand, affecting overall costs.
Plastic resin production has also been affected by global events. This causes fluctuations and limitations within the industry.
Consumer Reaction and Market Dynamics
Consumers are increasingly aware of the rising cost of everyday items, including soda. Some are opting for cheaper alternatives, such as store-brand sodas or flavored water. This shift in consumer behavior has implications for major soda brands.
Retailers are also responding by adjusting their pricing strategies and promotional offers. They are trying to balance profitability with maintaining customer loyalty. Some retailers may choose to absorb some of the cost increases to remain competitive, while others will pass them on to consumers.
This creates a dynamic market where consumers are constantly seeking the best value for their money. Brand loyalty is being tested as consumers become more price-sensitive.
Looking Ahead: Forecasting the Future of Soda Prices
Predicting the future trajectory of soda prices is challenging. Ongoing global economic instability and supply chain uncertainties make accurate forecasting difficult.
However, several trends suggest that prices are unlikely to decrease significantly in the near future. Continued inflationary pressures and supply chain disruptions are expected to persist. Furthermore, manufacturers are investing in more sustainable packaging options.
These options often come with a higher initial cost. Ultimately, the future cost of a 2-liter bottle of soda will depend on a complex interplay of economic factors, consumer behavior, and industry innovation. Consumers must remain informed and adaptable in this evolving marketplace.
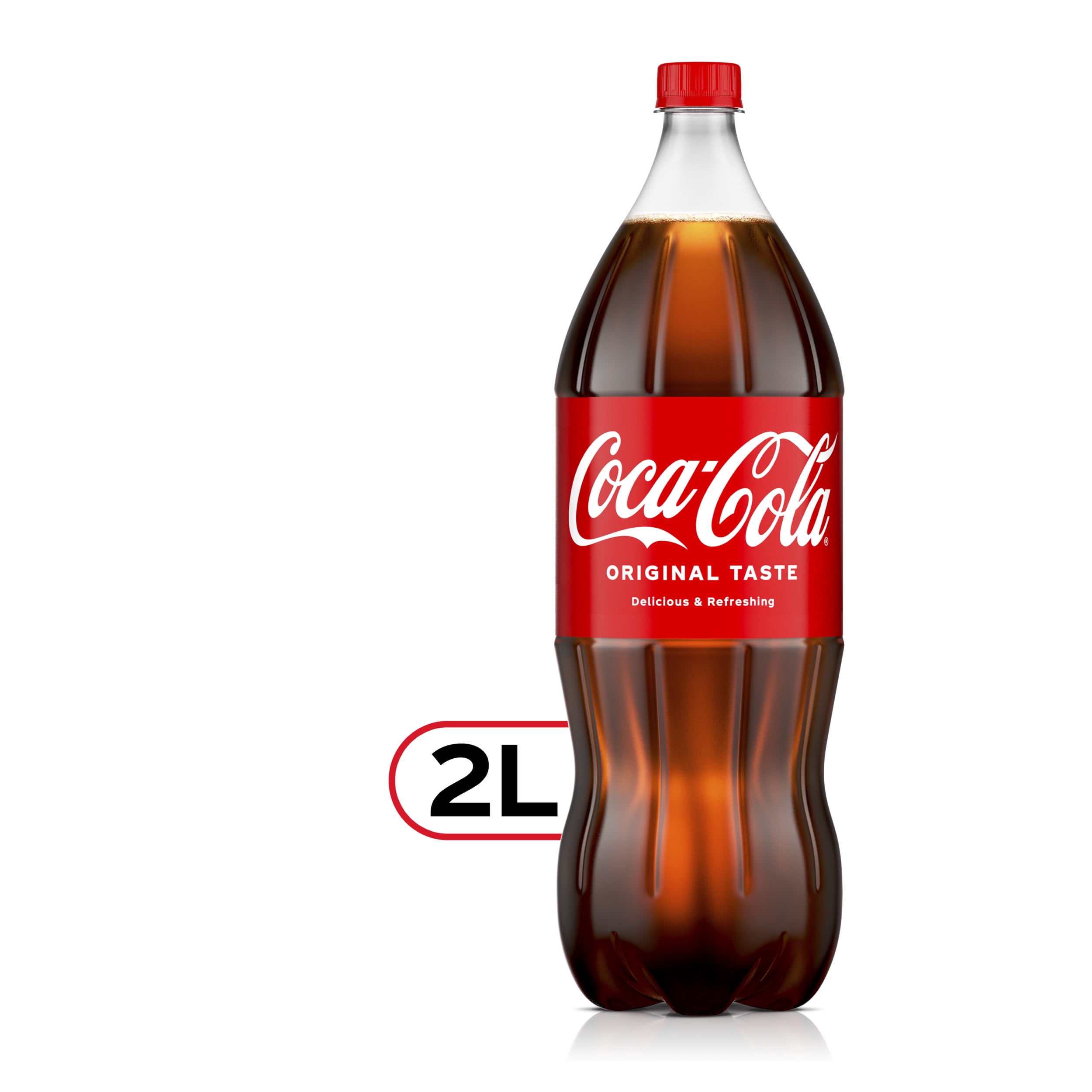


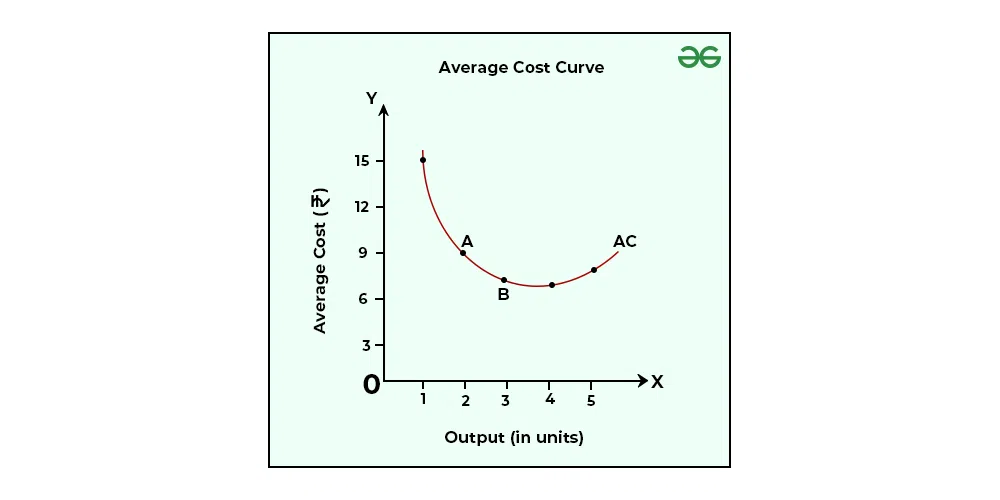
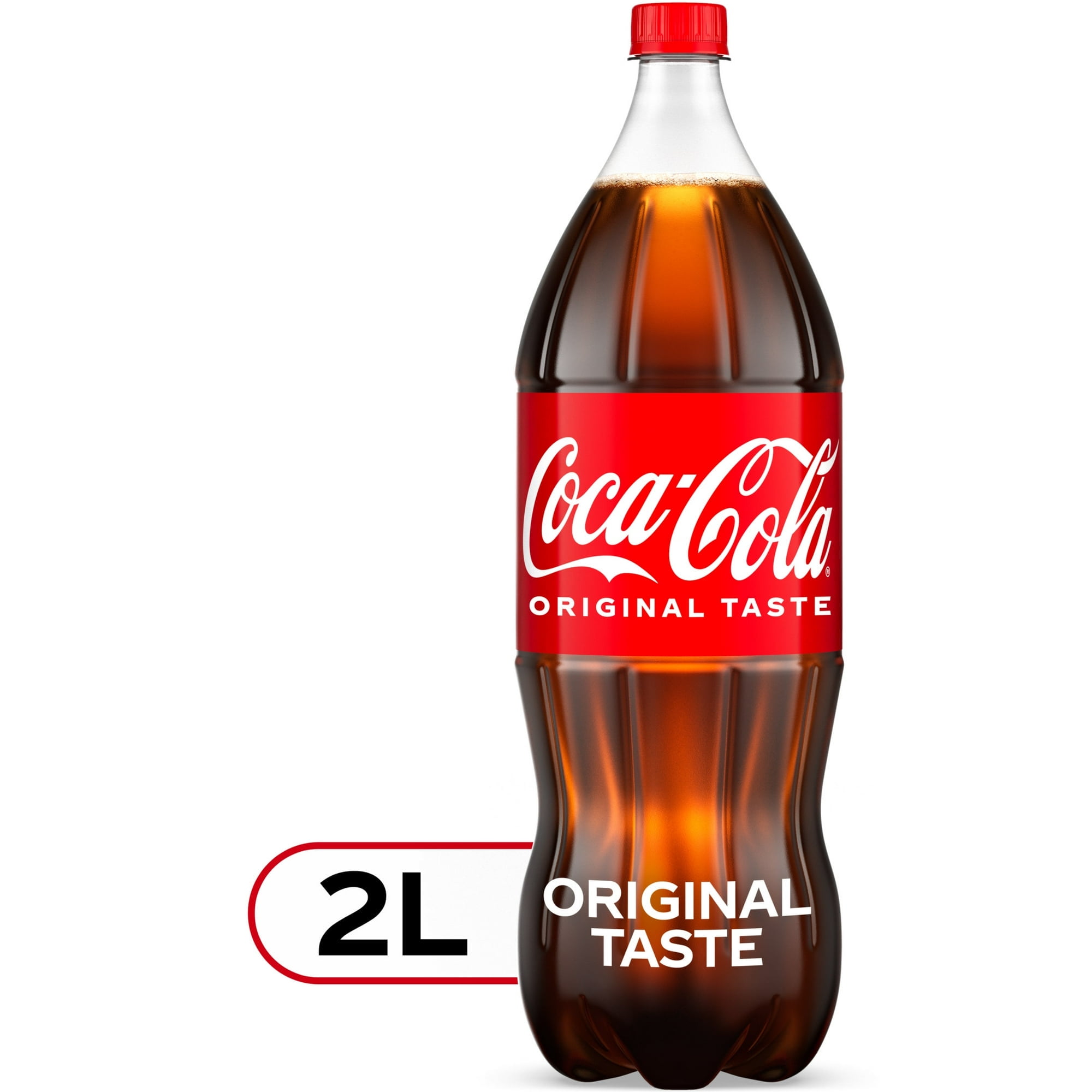
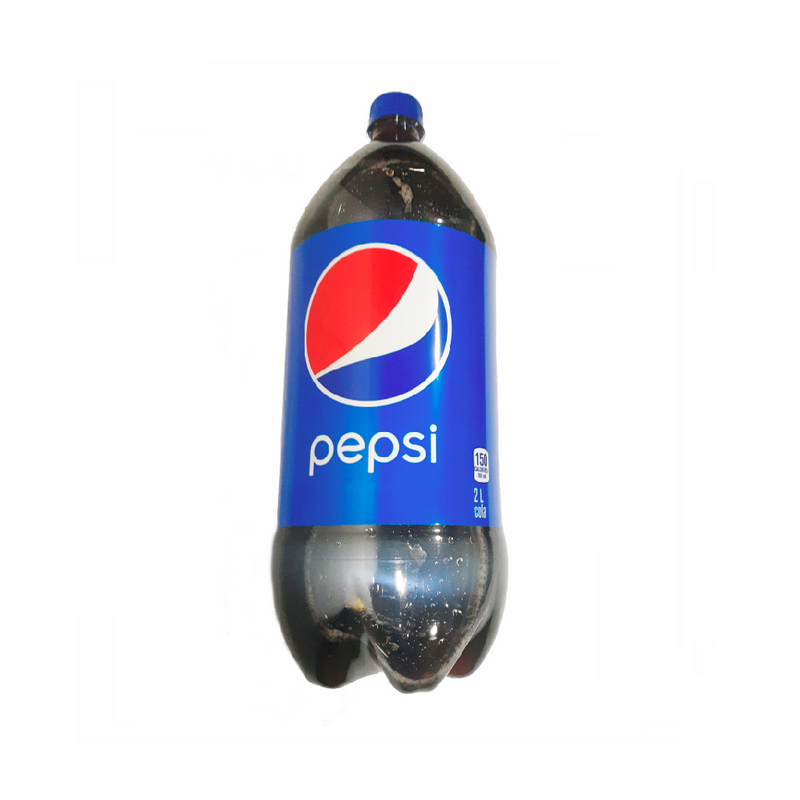
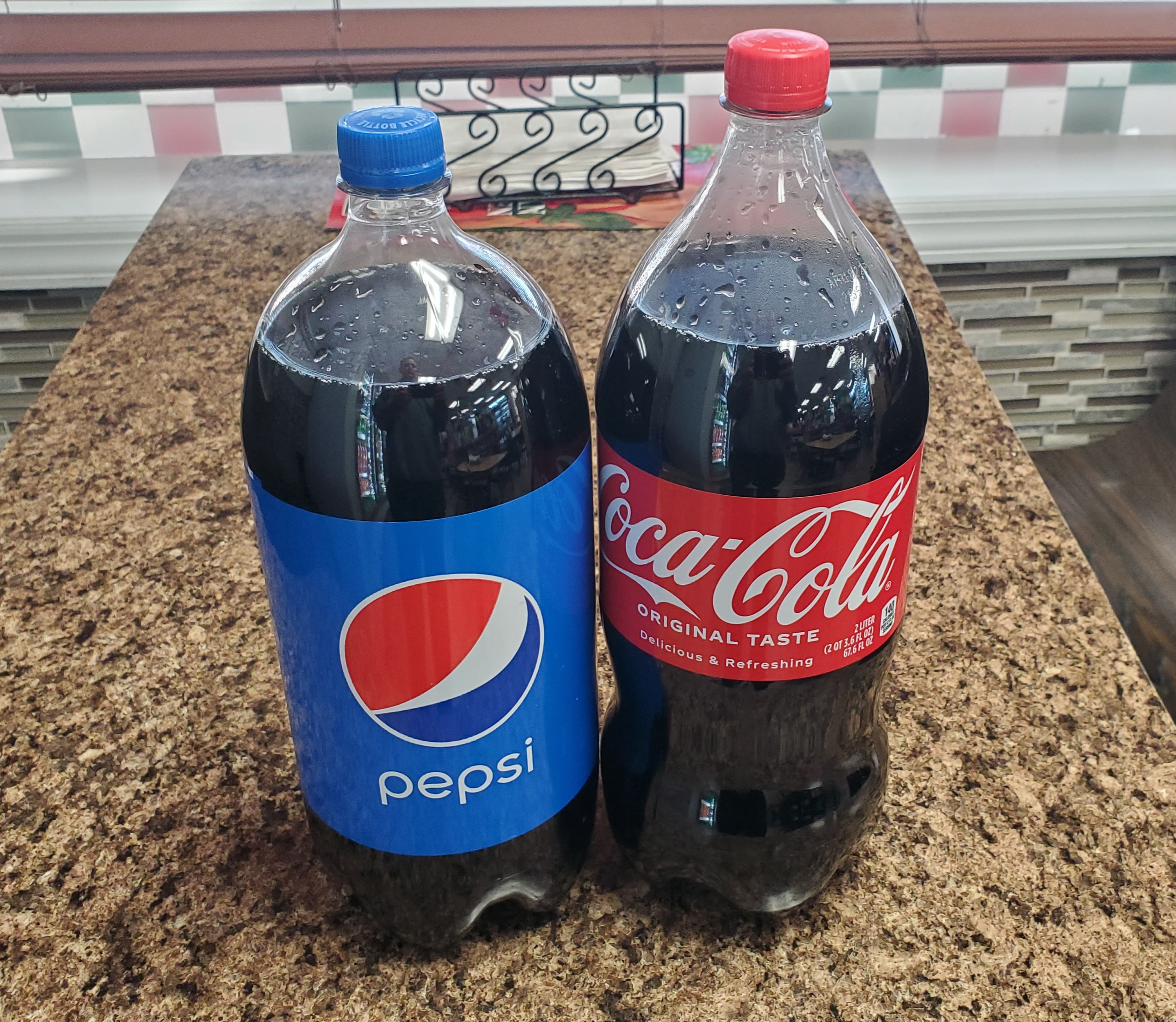

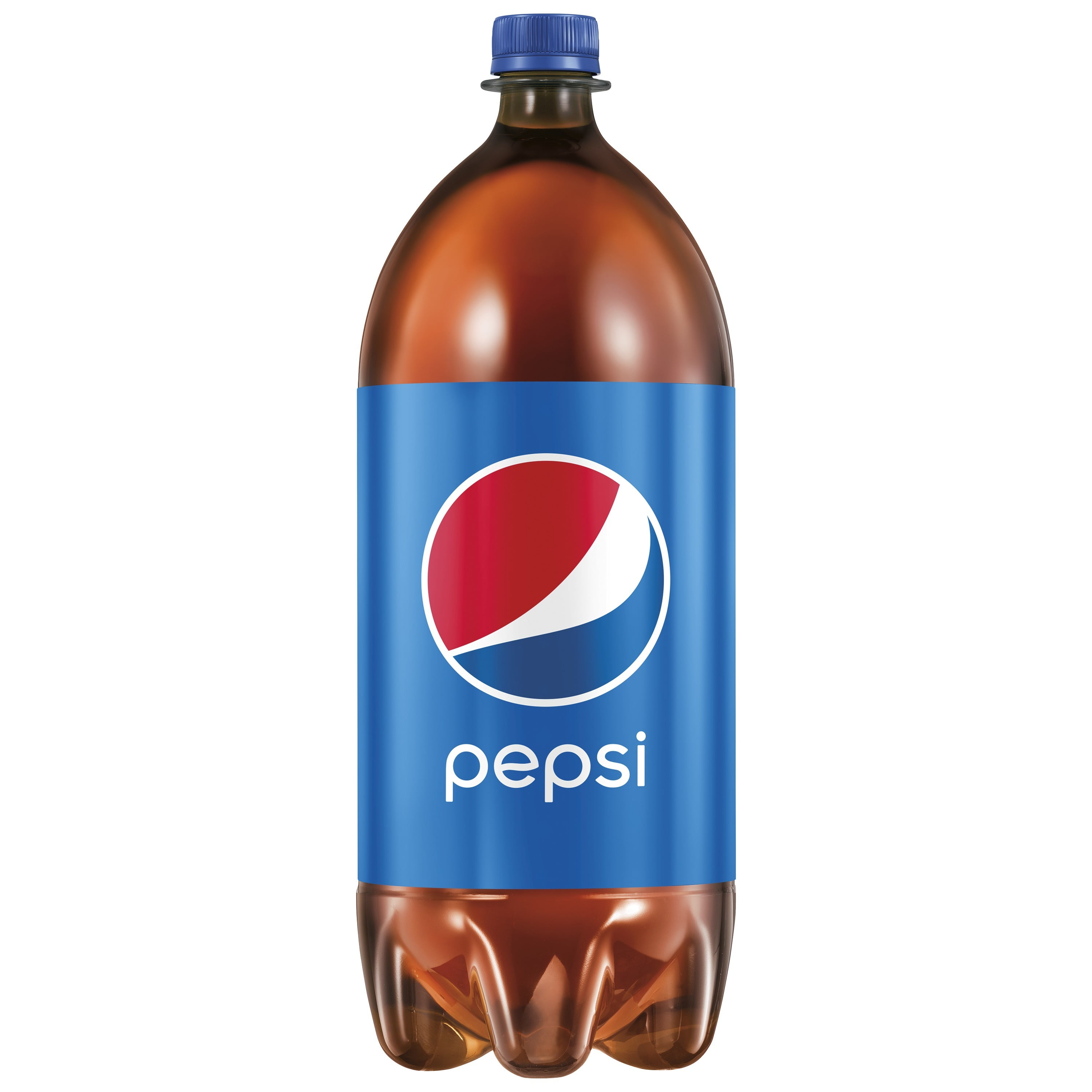

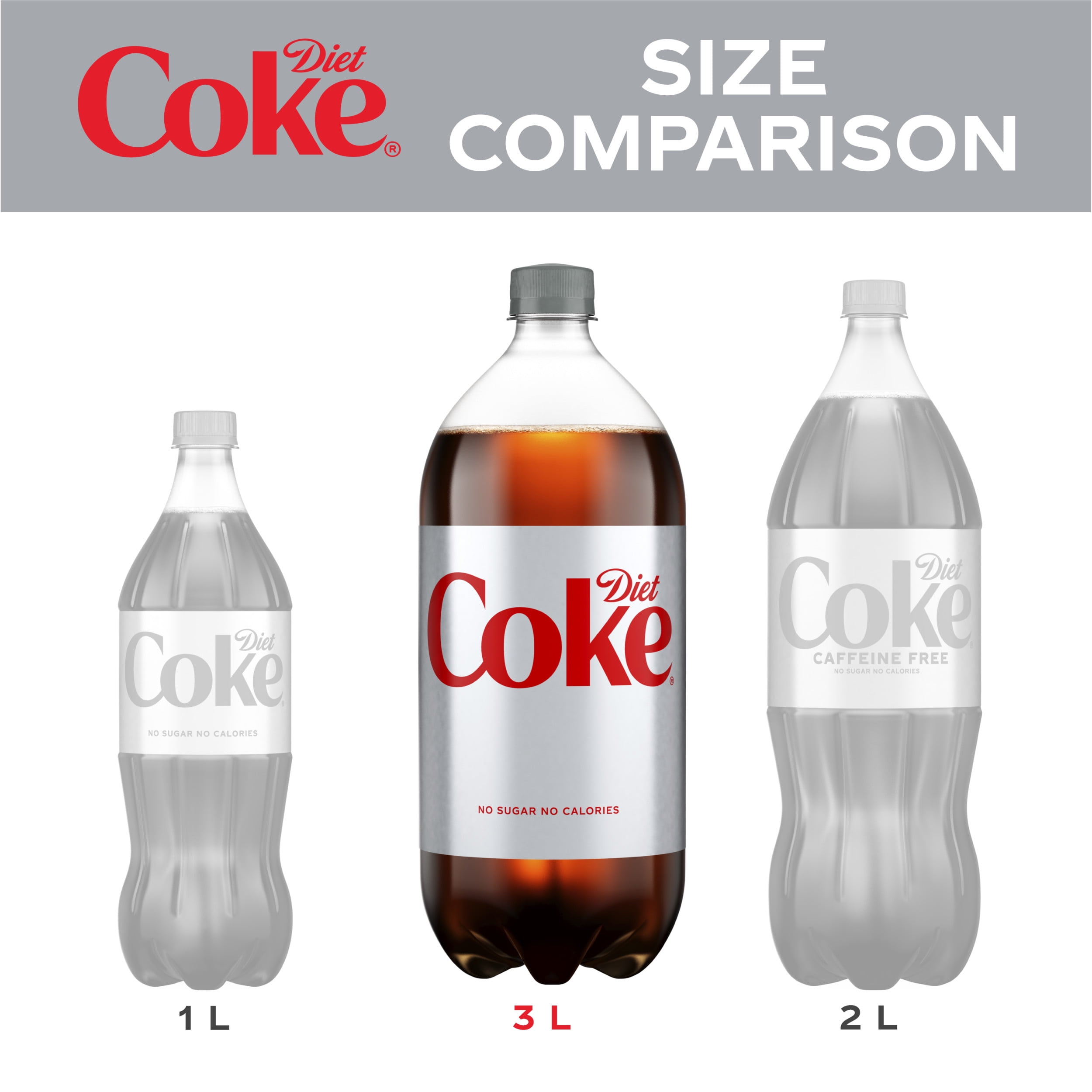


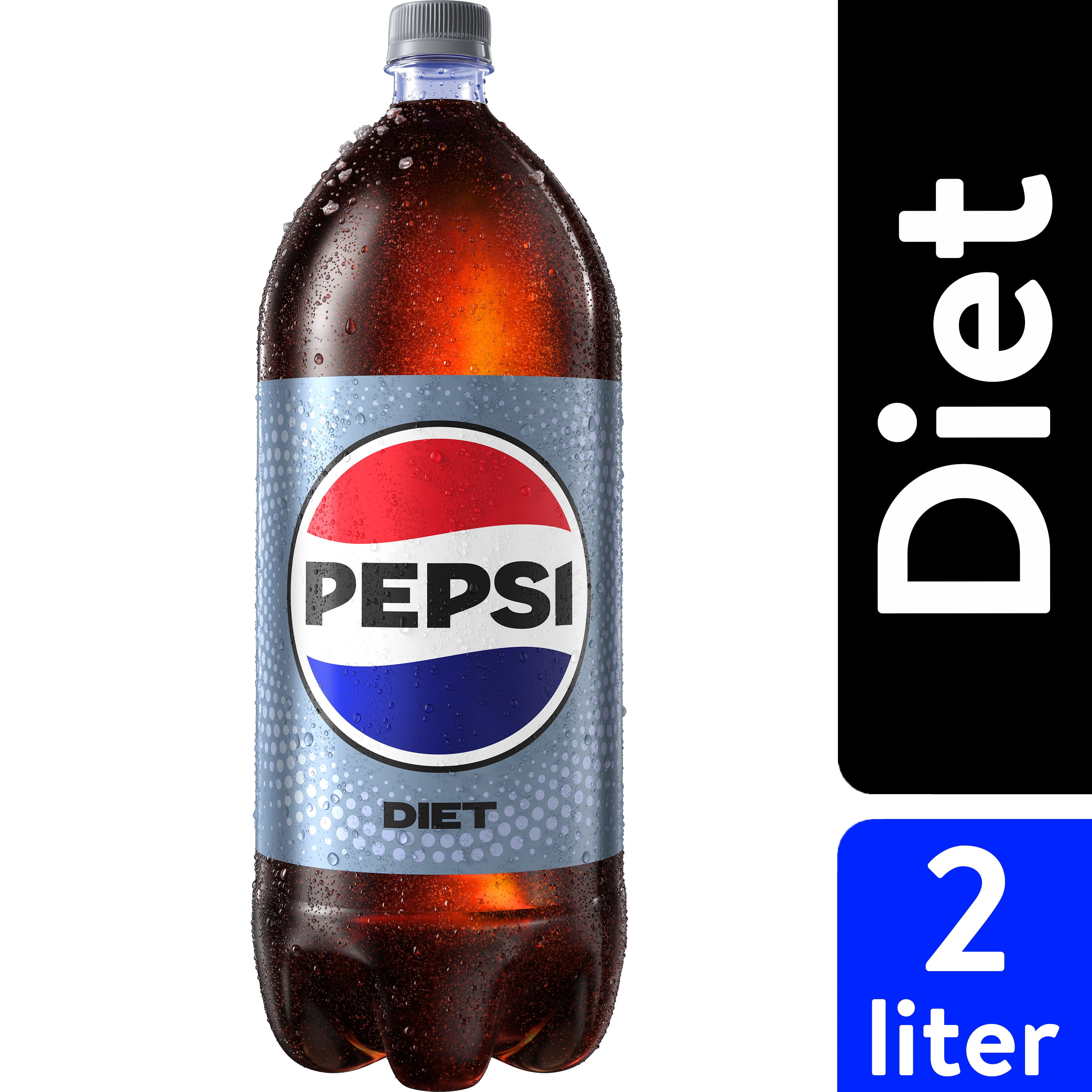
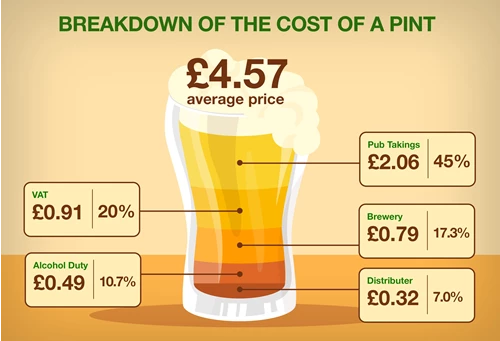
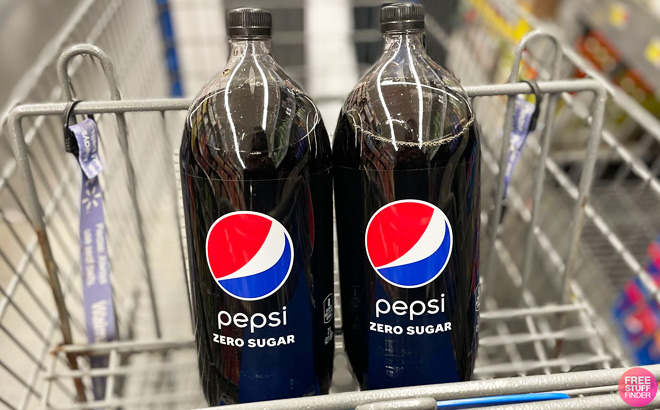
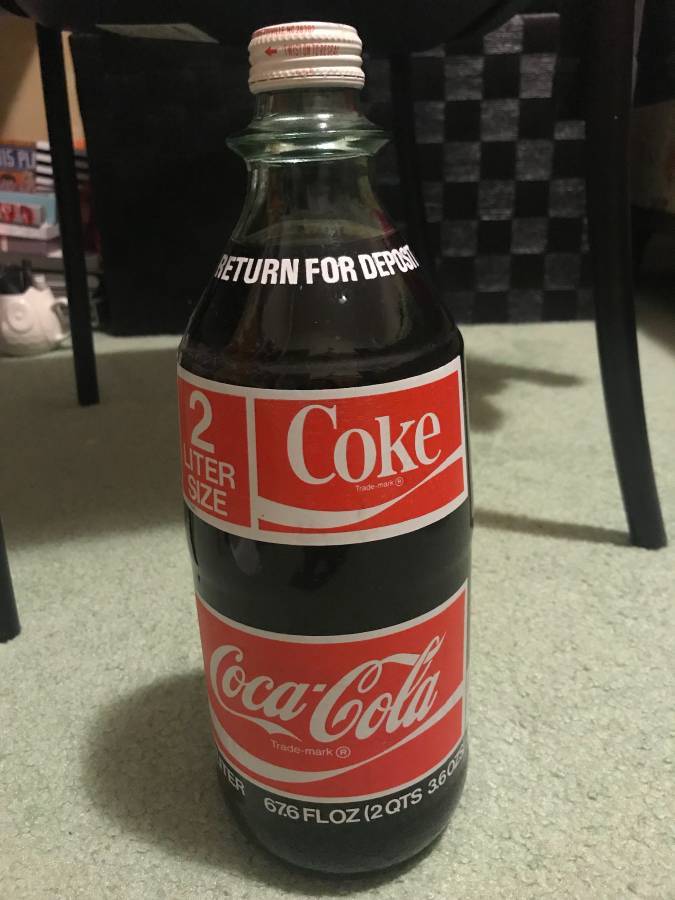
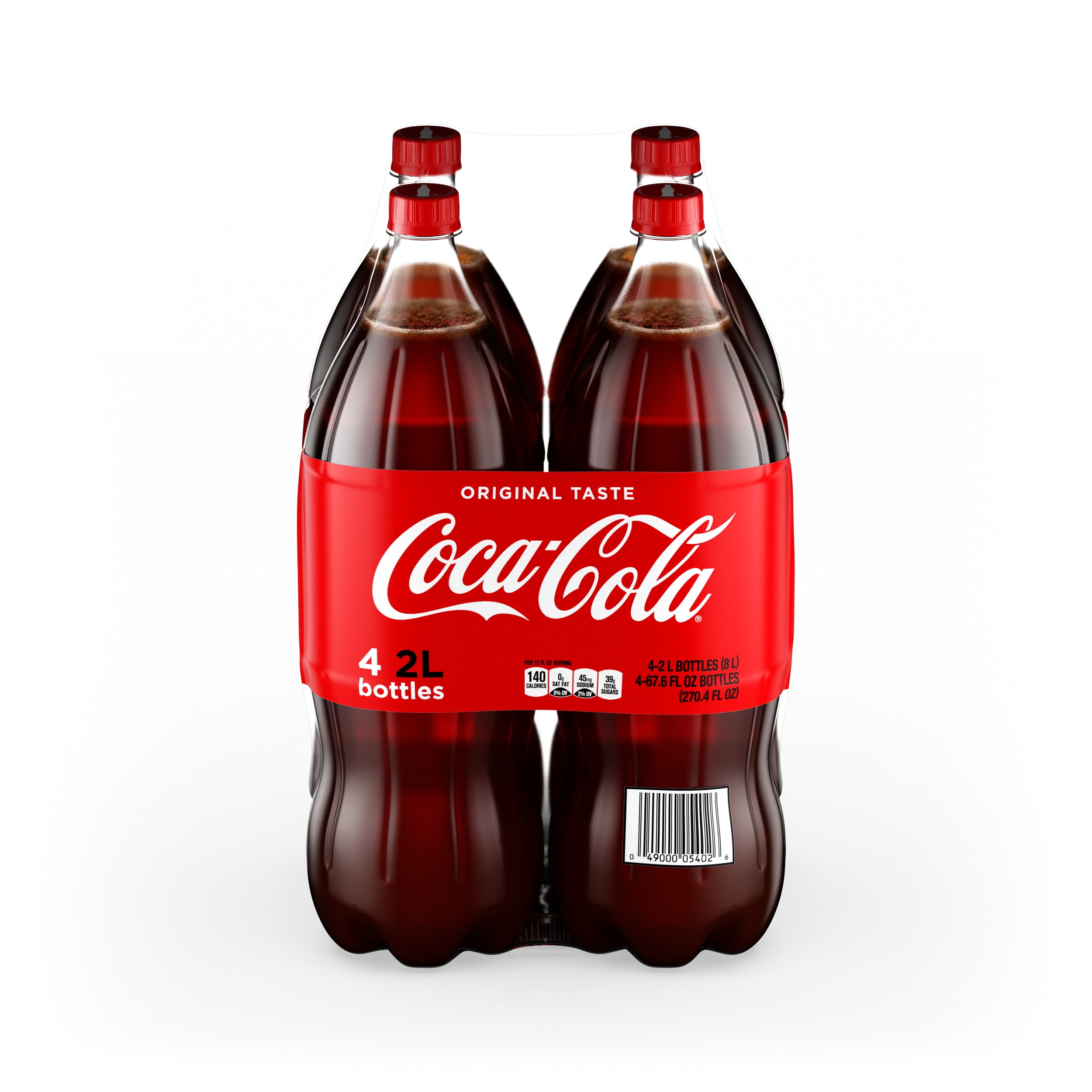