Product Costs That Have Become Expenses Can Be Found In:
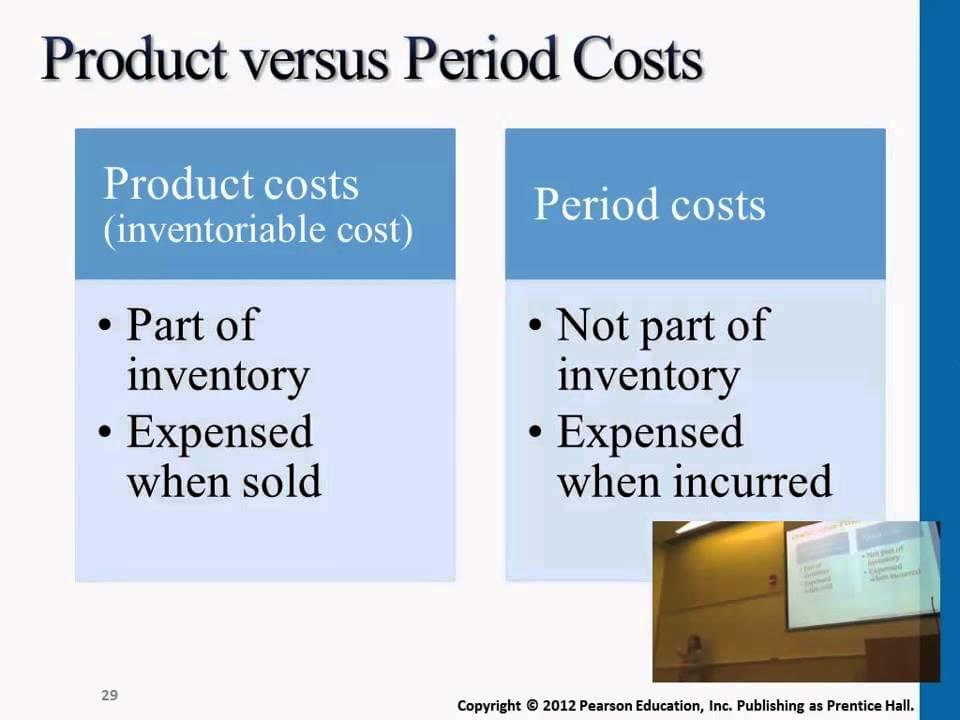
The creeping erosion of profitability continues to plague businesses across sectors, forcing a relentless hunt for cost efficiencies. One key battleground in this struggle lies within the often-murky waters of accounting practices, specifically the identification and proper categorization of expenses. The incorrect classification of product costs as period expenses, instead of inventory assets, can silently bleed a company dry.
This article delves into the crucial question: Where can one find product costs that have been erroneously treated as expenses? We will examine the areas within financial statements and operational workflows where these misclassifications often hide, highlighting the implications for accuracy in financial reporting and ultimately, the bottom line. This analysis draws upon accounting standards, expert insights, and real-world examples to provide a comprehensive understanding of this critical issue.
The Income Statement: A Primary Hunting Ground
The income statement, also known as the profit and loss (P&L) statement, is often the first place to look. Here, expenses are directly matched against revenues to determine a company’s profitability over a specific period.
An inflated expense line, particularly within Cost of Goods Sold (COGS) or operating expenses, should raise red flags. This is because COGS should ideally only reflect the direct costs associated with producing goods or services.
For instance, consider a manufacturing company that prematurely expenses the cost of raw materials before they are actually used in production. These costs are erroneously included in COGS, artificially deflating the gross profit.
Scrutinizing COGS Components
A closer examination of the components of COGS is essential. This involves dissecting the direct materials, direct labor, and manufacturing overhead that constitute this significant expense category.
Are labor costs directly tied to the production process being properly allocated to inventory? Similarly, is depreciation on manufacturing equipment being treated as a product cost and included in overhead? Incorrect assignment of these costs directly impacts COGS and net income.
Specifically, look for: raw materials expensed prematurely, direct labor inaccurately classified or timed, and manufacturing overhead including period costs.
The Balance Sheet: Unveiling Inventory Discrepancies
The balance sheet, a snapshot of a company’s assets, liabilities, and equity at a specific point in time, is another crucial source of information. Inventory, a key asset for many businesses, should reflect all product costs incurred up to the point of sale.
A suspiciously low inventory balance, especially when compared to production volumes and sales figures, can indicate that product costs are being expensed too early. Investigate the methods the company uses to determine the value of ending inventory.
Inventory valuation methods such as FIFO (First-In, First-Out) or Weighted-Average can also mask inconsistencies. Ensure that the chosen method is consistently applied and accurately reflects the flow of goods.
Analyzing Inventory Sub-Ledgers
Deeper analysis requires scrutinizing inventory sub-ledgers. These detailed records provide a breakdown of inventory quantities and costs for each item.
Discrepancies between physical inventory counts and recorded inventory balances often point to errors in cost allocation. This also indicates the potential for unrecorded obsolescence or spoilage that should have been written off as an expense.
Moreover, pay close attention to work-in-progress (WIP) inventory. Accurately capturing the labor and overhead applied to partially completed goods is crucial.
Operational Workflows and Internal Controls
The root cause of product cost misclassifications often lies within a company’s operational workflows and internal controls. Weaknesses in these areas can lead to systematic errors in cost allocation.
Examine the processes for tracking raw materials from procurement to production. Look for gaps in documentation that might allow materials to be expensed before they are used.
Robust internal controls, including segregation of duties and regular reconciliations, are essential to prevent and detect errors. Deficiencies in these controls significantly increase the risk of misclassification.
Supplier Contracts and Invoicing
Review supplier contracts and invoices for inconsistencies in pricing or terms. Hidden financing costs or inflated prices can be erroneously expensed instead of being capitalized as part of the product cost.
Consider purchase price variances. Unfavorable variances (paying more than expected for materials) require careful investigation.
Are these variances being properly allocated to inventory, or are they being written off as a period expense?
Beyond the Financial Statements: External Audits and Management Discussions
While financial statements provide a starting point, additional insights can be gleaned from other sources. External audit reports often highlight weaknesses in internal controls and accounting practices.
Pay attention to management’s discussion and analysis (MD&A) section of the annual report. Here, management often provides explanations for significant changes in financial performance.
Look for discussions regarding cost management initiatives or changes in accounting policies that might impact product cost classification. If there are sudden fluctuations, a deeper dive is needed.
The Importance of Proper Classification and Looking Ahead
The accurate classification of product costs as inventory assets is not merely an accounting exercise. It has significant implications for financial reporting, tax compliance, and managerial decision-making.
Incorrect classification can lead to inaccurate financial statements. This distorts profitability metrics, and ultimately, misleads investors and stakeholders.
As businesses face increasing pressure to optimize performance, a renewed focus on cost accounting principles is essential. This involves implementing robust internal controls, providing adequate training for accounting personnel, and regularly reviewing accounting policies to ensure compliance with accounting standards.
By diligently searching for product costs that have become expenses in the wrong places, businesses can achieve greater transparency, improve financial performance, and build a stronger foundation for sustainable growth.
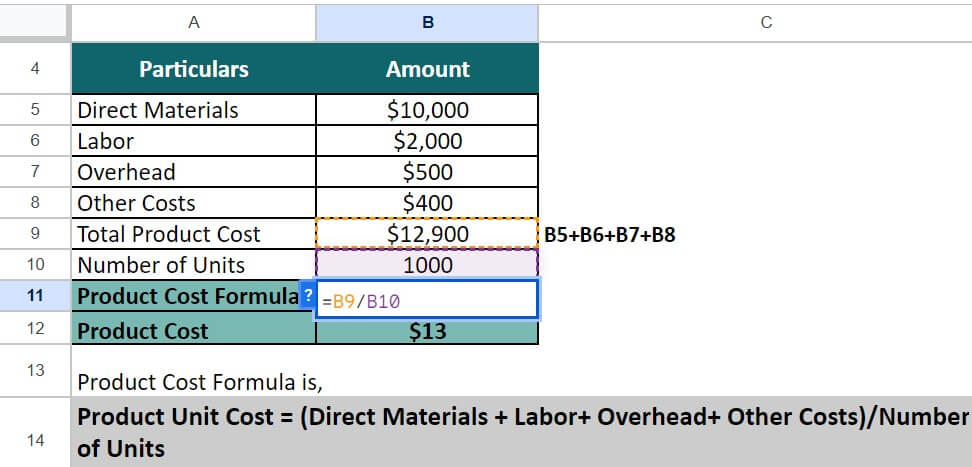
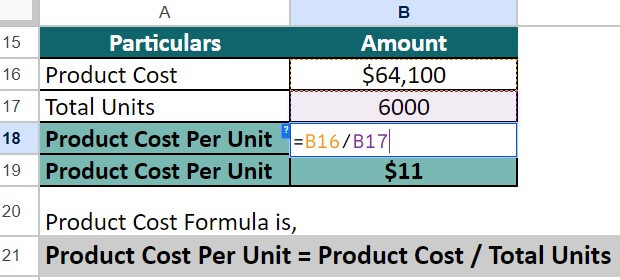
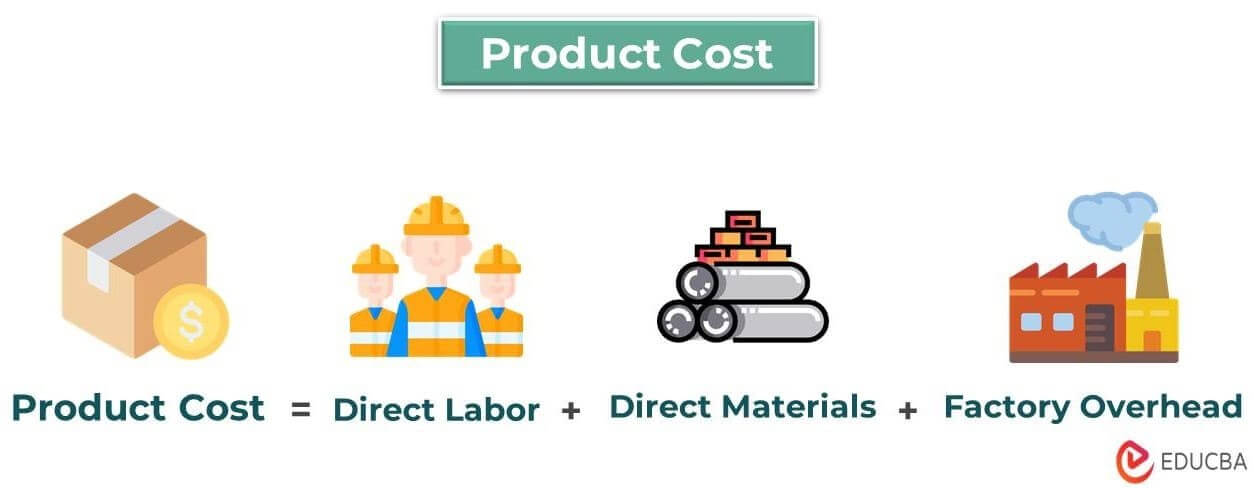


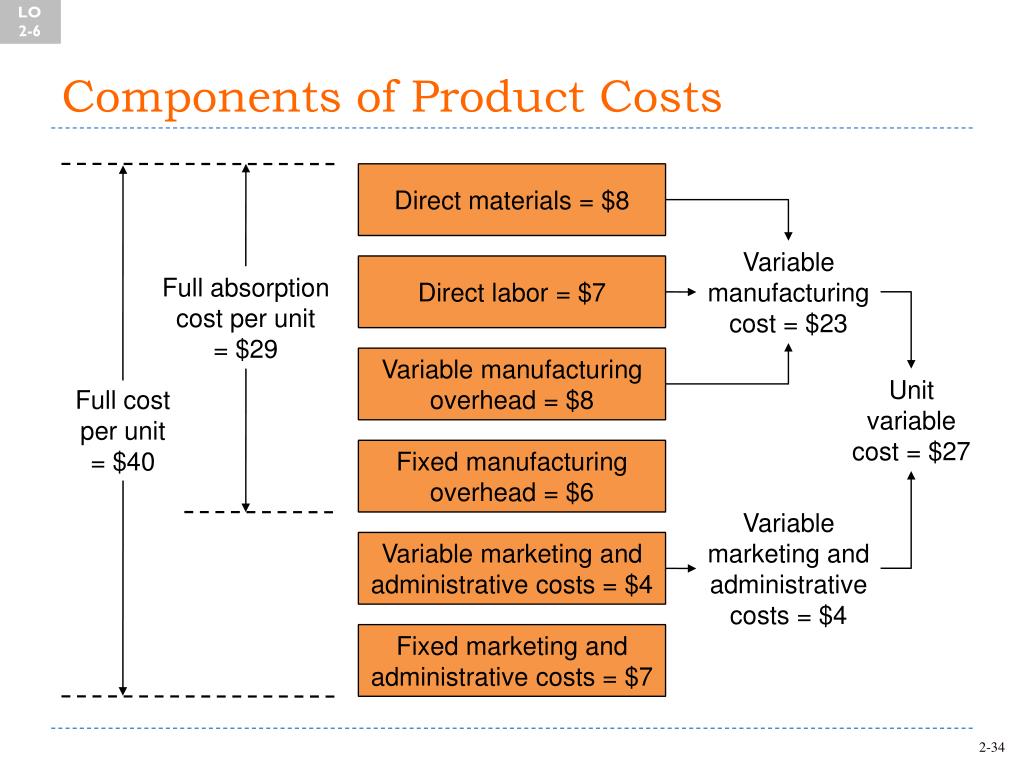

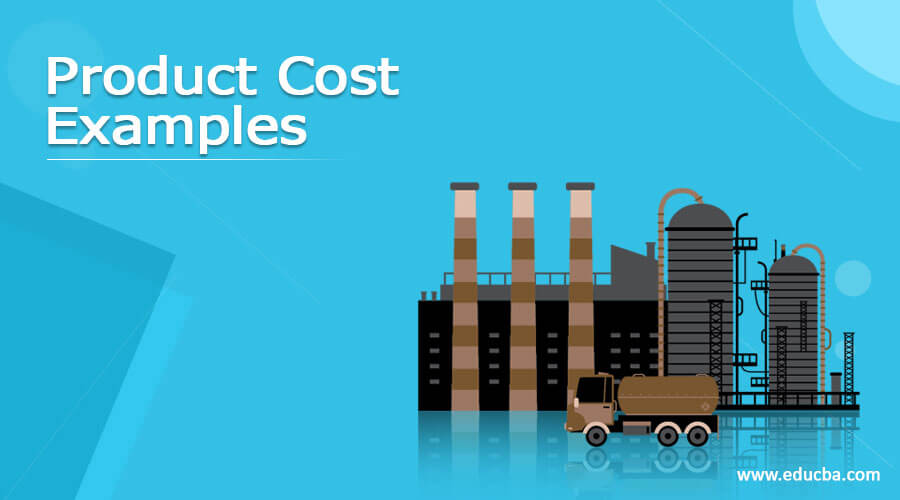

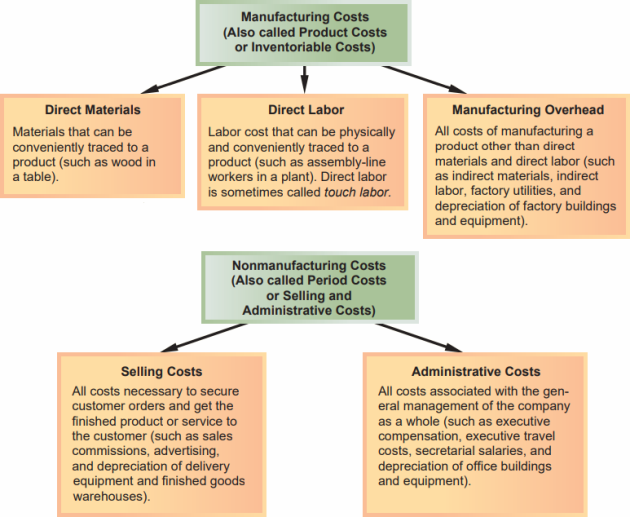
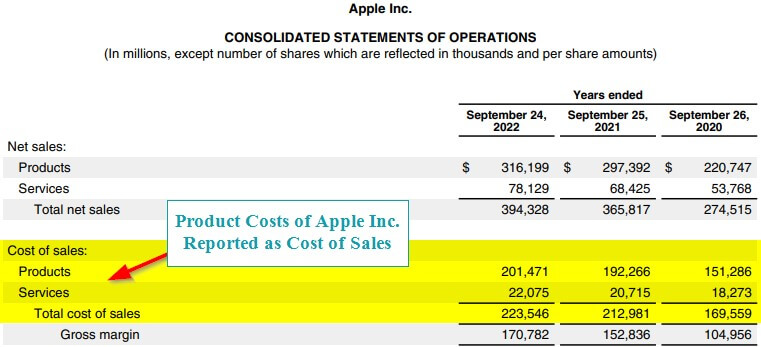
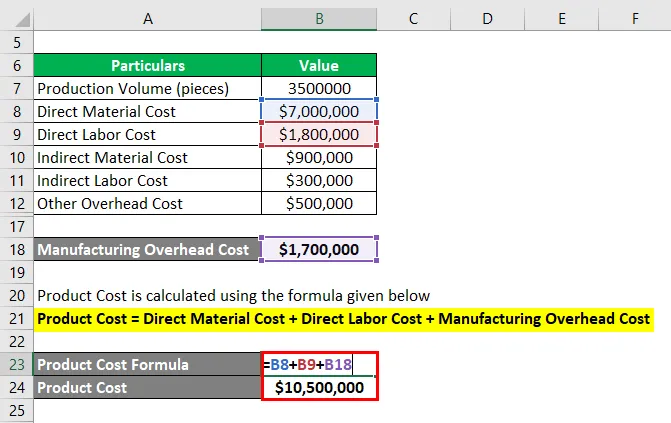
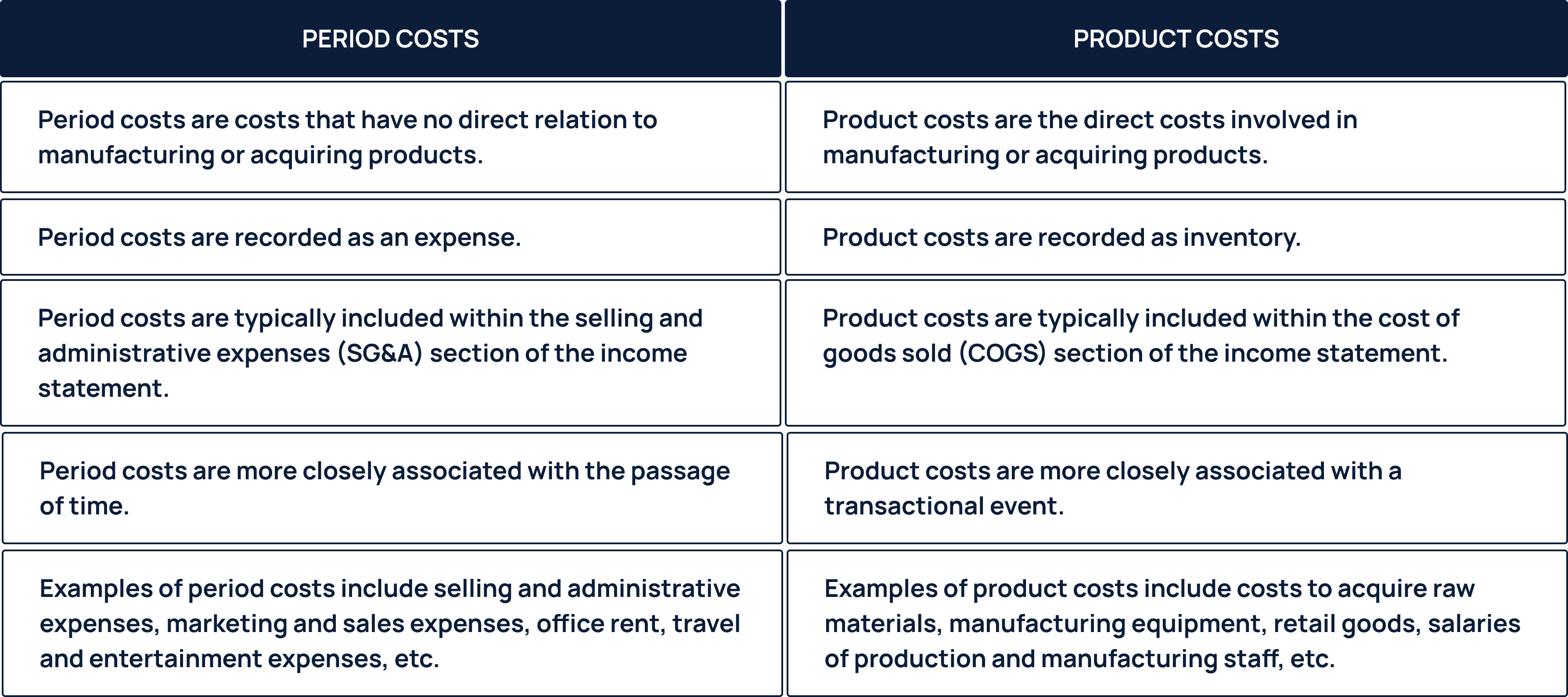
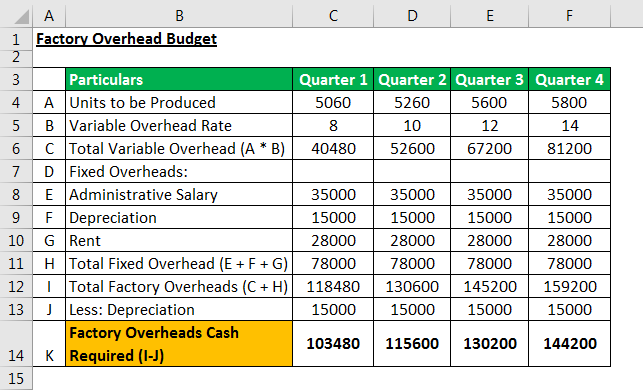



