How Is Gas Made From Crude Oil

Global energy demands are surging, and the process behind producing gasoline from crude oil remains a critical, yet often misunderstood, cornerstone of modern society. This article cuts through the complexity to deliver a clear, concise explanation of how this essential fuel is derived from its raw source.
At its heart, the transformation of crude oil into gasoline hinges on a sophisticated process called fractional distillation, followed by several refining steps. These operations are primarily conducted in massive industrial complexes known as oil refineries around the globe.
Fractional Distillation: Separating the Components
Crude oil, as extracted from the earth, is a complex mixture of hydrocarbons. These hydrocarbons vary significantly in molecular size and boiling points.
The first crucial step, fractional distillation, leverages these differences to separate the crude oil into various fractions. This separation occurs in a distillation column, a tall tower heated to progressively higher temperatures from bottom to top.
Crude oil is heated to extremely high temperatures, often exceeding 400 degrees Celsius (750 degrees Fahrenheit), and then fed into the base of the distillation column. As the heated crude oil vaporizes and rises through the column, it gradually cools.
Hydrocarbons with higher boiling points condense into liquids at the bottom of the column. Substances like bitumen and heavy fuel oils are extracted from this area.
Lighter hydrocarbons, such as gasoline, kerosene, and diesel, condense at progressively higher levels in the column, where temperatures are lower. These different fractions are collected at various points.
Even lighter fractions, including gases like methane and ethane, remain in vapor form and are collected at the top of the column. Each fraction obtained in this manner is sent for further processing.
Refining Processes: Enhancing Gasoline Quality
The gasoline fraction obtained from fractional distillation isn't immediately ready for use in vehicles. It needs to be further refined to improve its octane rating and overall performance.
Several key refining processes are employed at this stage, including cracking, isomerization, and reforming. These processes chemically alter the hydrocarbons to produce a higher quality gasoline blend.
Cracking
Cracking breaks down large hydrocarbon molecules into smaller, more desirable ones, including those suitable for gasoline. This is achieved through either thermal cracking (using high heat) or catalytic cracking (using a catalyst to speed up the reaction).
Catalytic cracking, particularly fluid catalytic cracking (FCC), is widely used. According to the Energy Information Administration (EIA), FCC units are essential for converting heavy oils into gasoline and other valuable products.
Isomerization
Isomerization converts straight-chain hydrocarbons into branched-chain isomers. Branched hydrocarbons have higher octane ratings, meaning they are less prone to knocking in engines.
This process typically involves the use of a catalyst and moderate temperatures. It's vital for improving the antiknock properties of gasoline.
Reforming
Reforming converts low-octane naphthas into high-octane aromatic hydrocarbons. This process uses catalysts and high temperatures to rearrange the molecular structure of the hydrocarbons.
Reforming is essential for producing high-octane blending components for gasoline. It significantly enhances the fuel's ability to resist knocking.
Blending and Additives: Finalizing the Gasoline Product
After refining, different hydrocarbon streams are blended together to meet specific gasoline grades and performance standards. Various additives are incorporated to further enhance gasoline properties.
Additives can improve engine cleanliness, reduce emissions, and prevent corrosion. They play a crucial role in ensuring that gasoline meets regulatory requirements and consumer expectations.
Examples of additives include detergents, antioxidants, and anti-icing agents. The specific blend and additive package can vary depending on the grade of gasoline and regional requirements.
According to the EPA (Environmental Protection Agency) regulations, all gasoline sold in the United States must contain a minimum level of detergent additives to help keep engines clean.
Environmental Considerations and Future Trends
The production of gasoline from crude oil has significant environmental implications, including greenhouse gas emissions and air pollution. Efforts are underway to develop cleaner and more sustainable gasoline production methods.
These efforts include improving refinery efficiency, reducing emissions, and exploring alternative feedstocks such as biomass. The transition to alternative fuels, like biofuels and electricity, is also gaining momentum.
The future of gasoline production will likely involve a combination of improved refining processes and a gradual shift towards more sustainable energy sources. The exact timeline for this transition remains uncertain and depends on technological advancements, policy decisions, and economic factors.
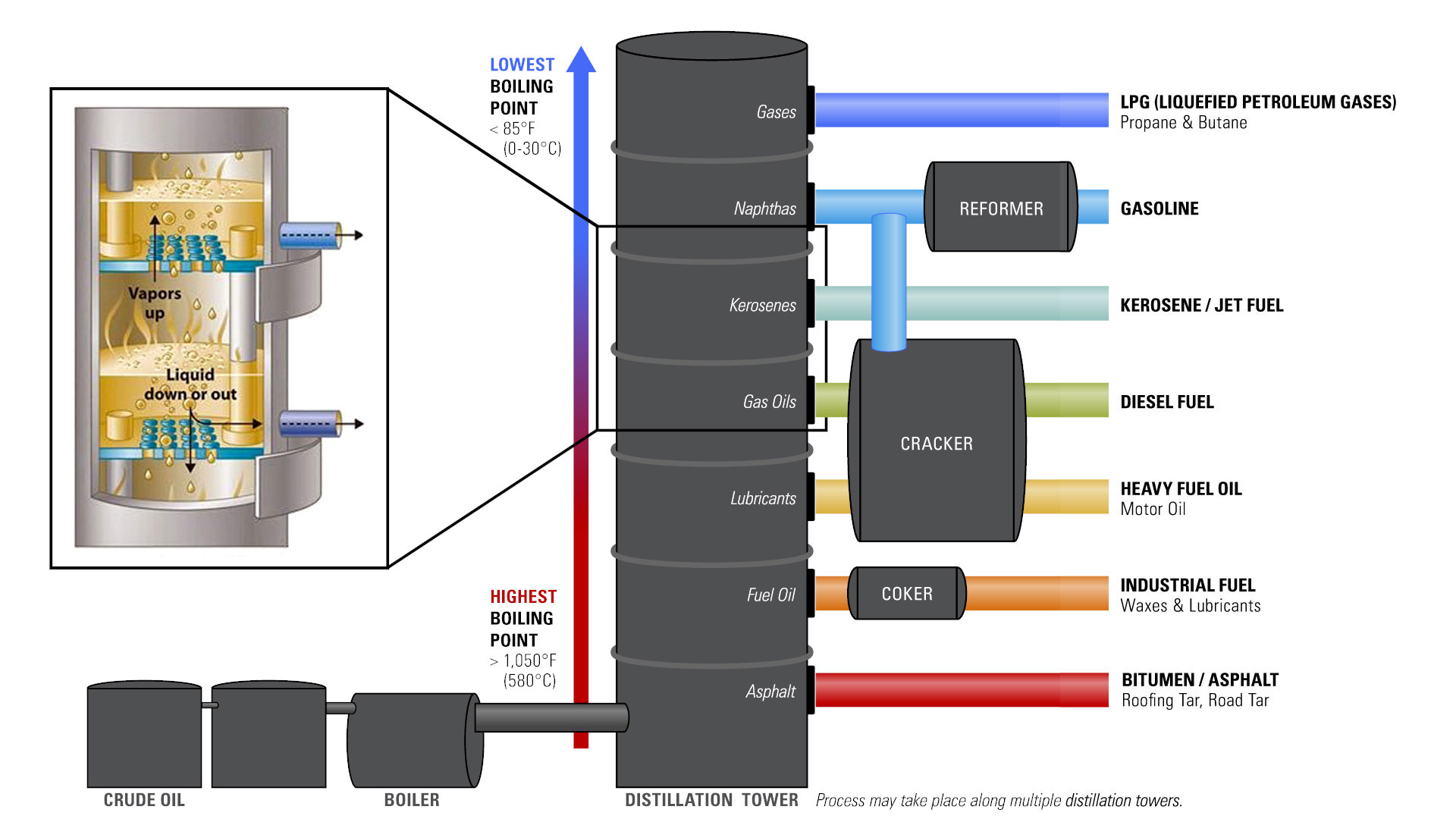
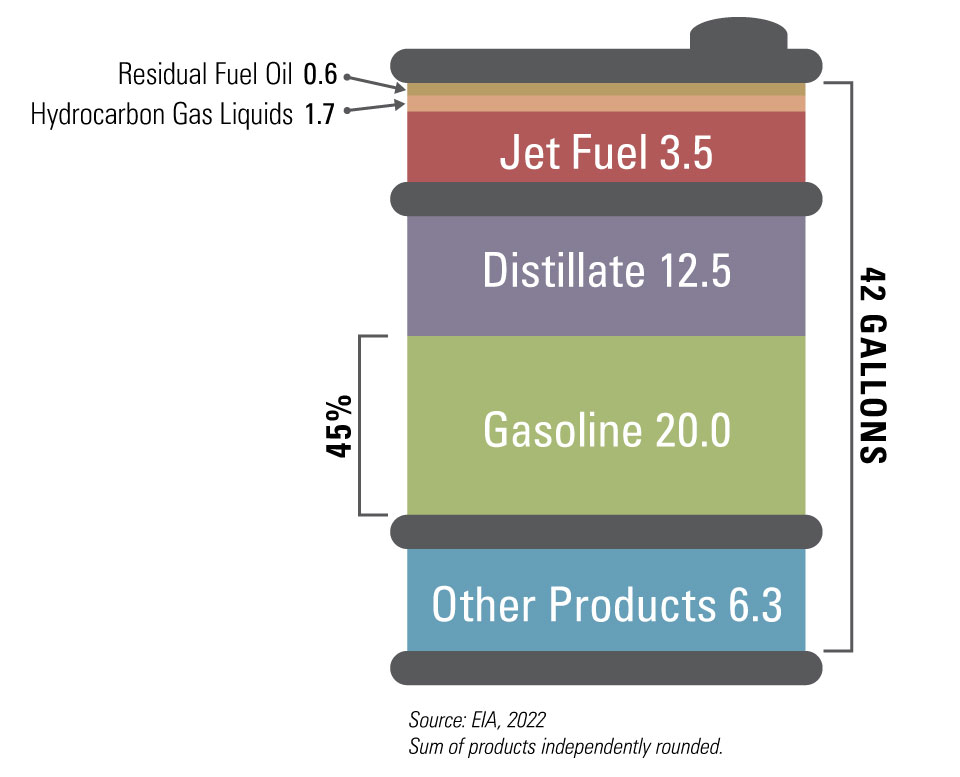
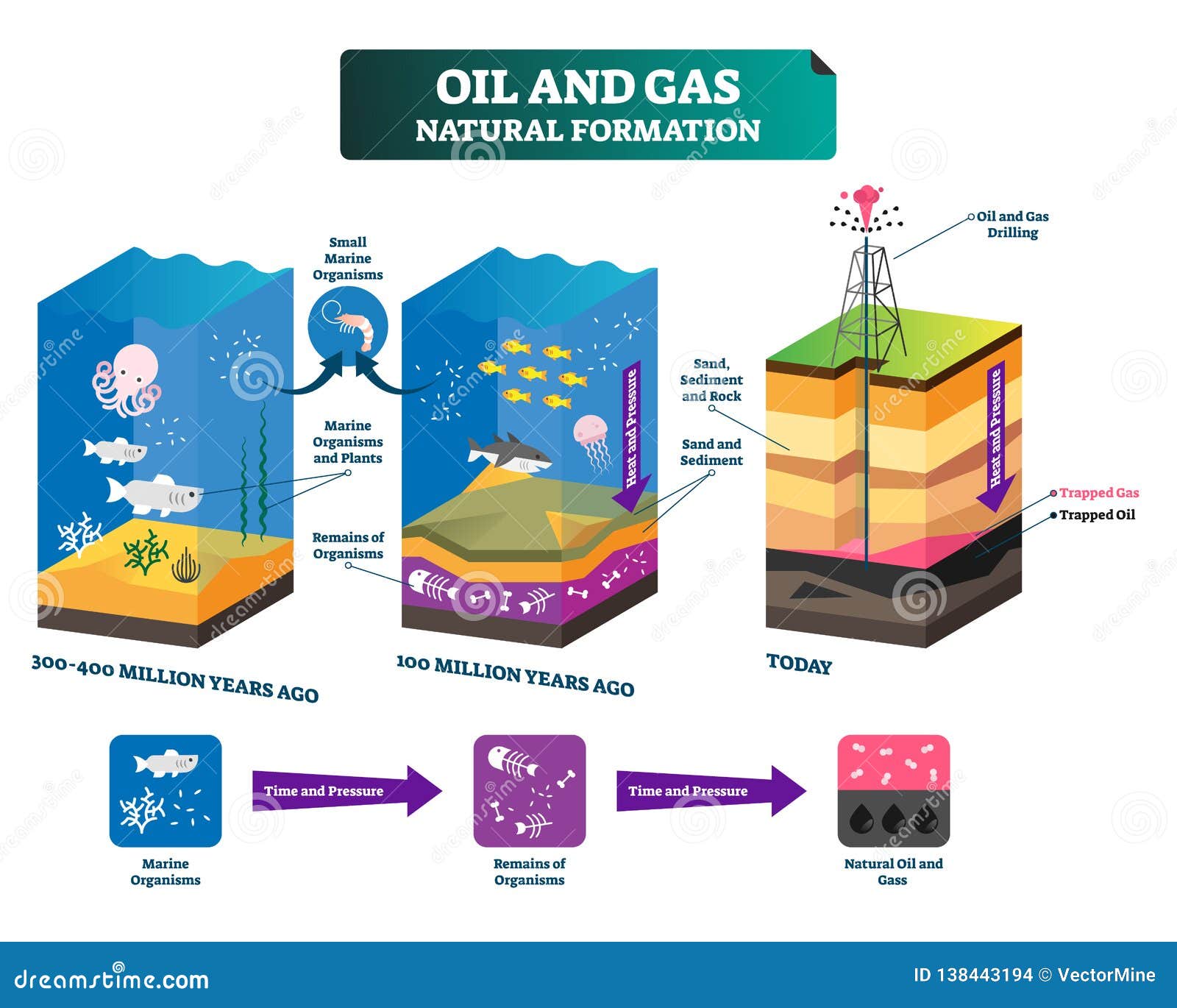





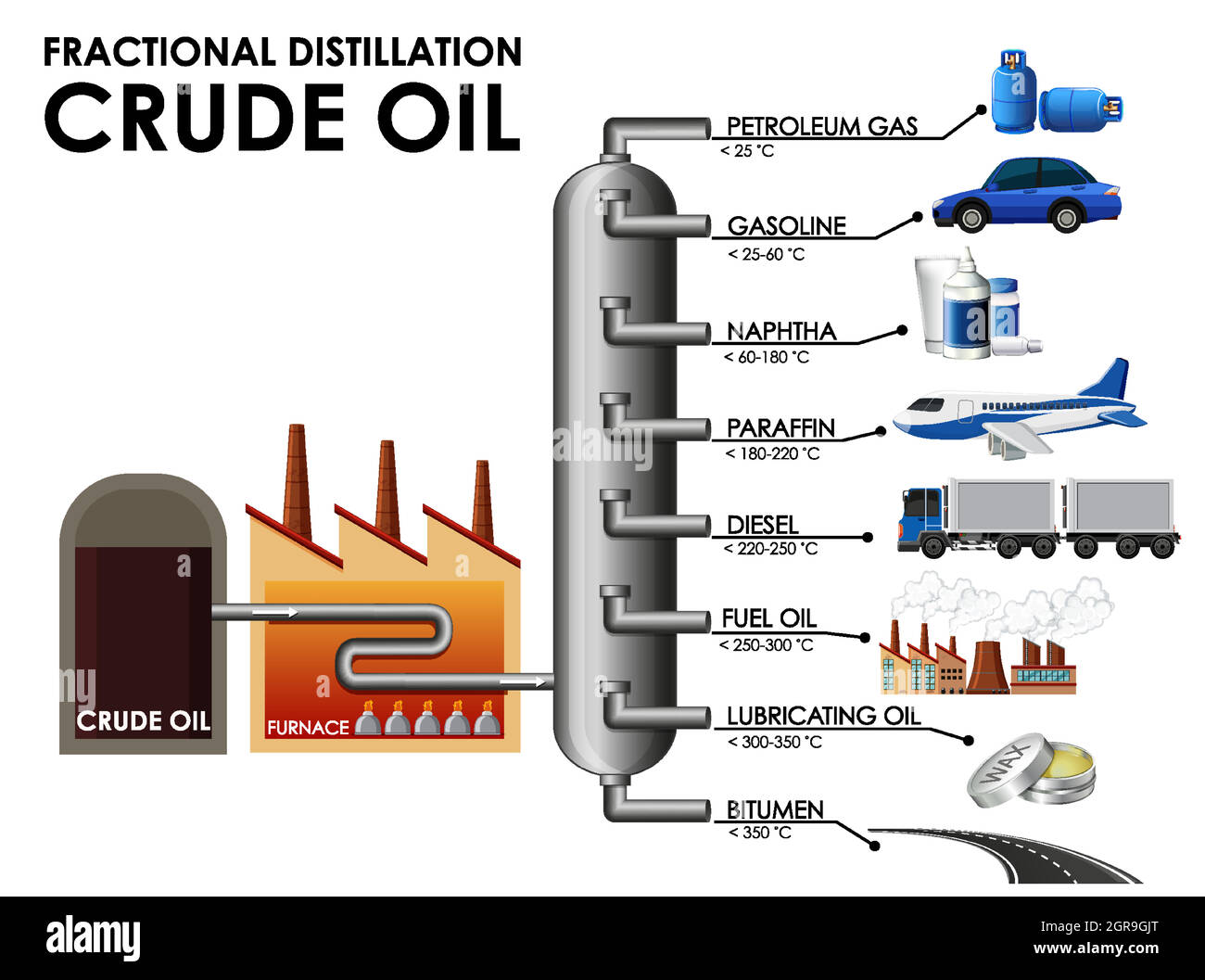
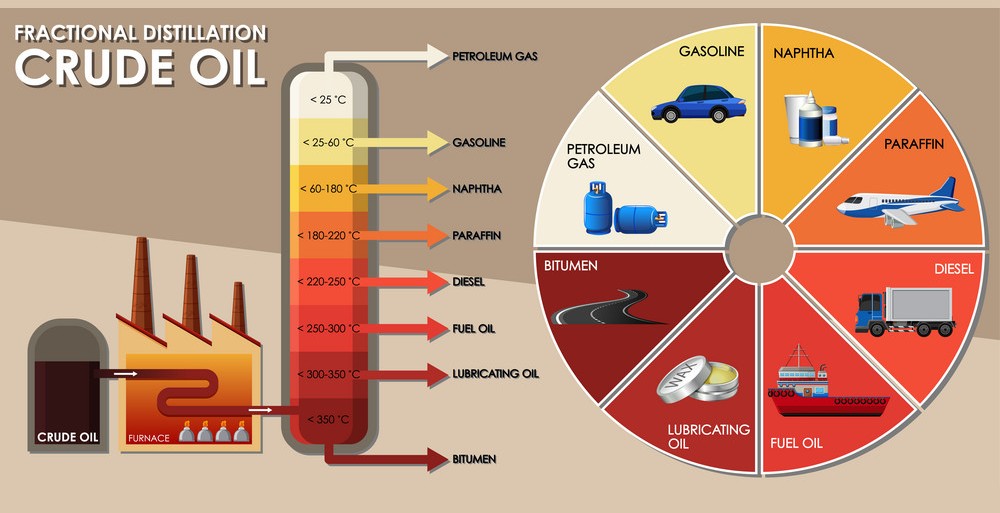
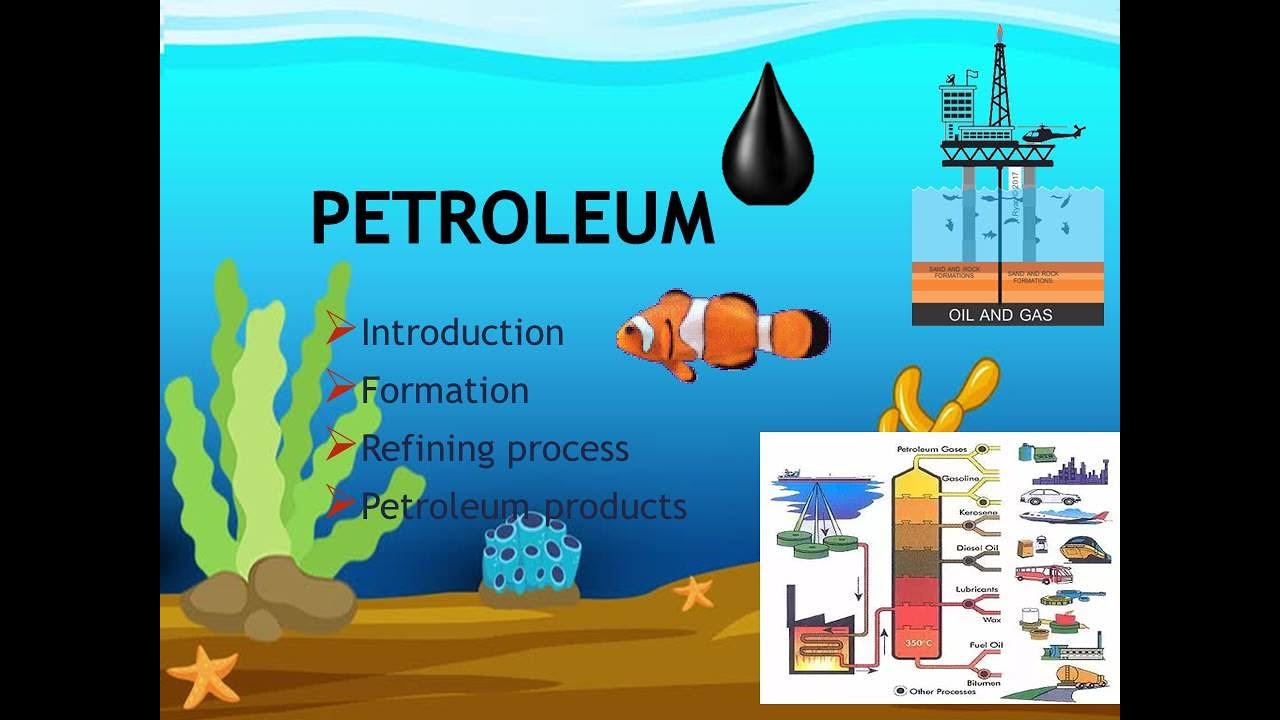
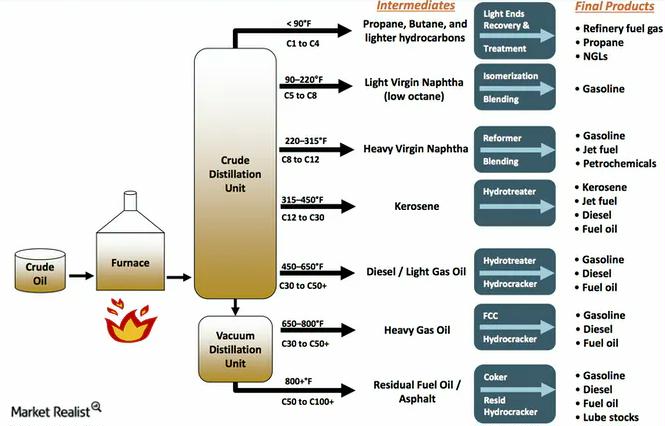

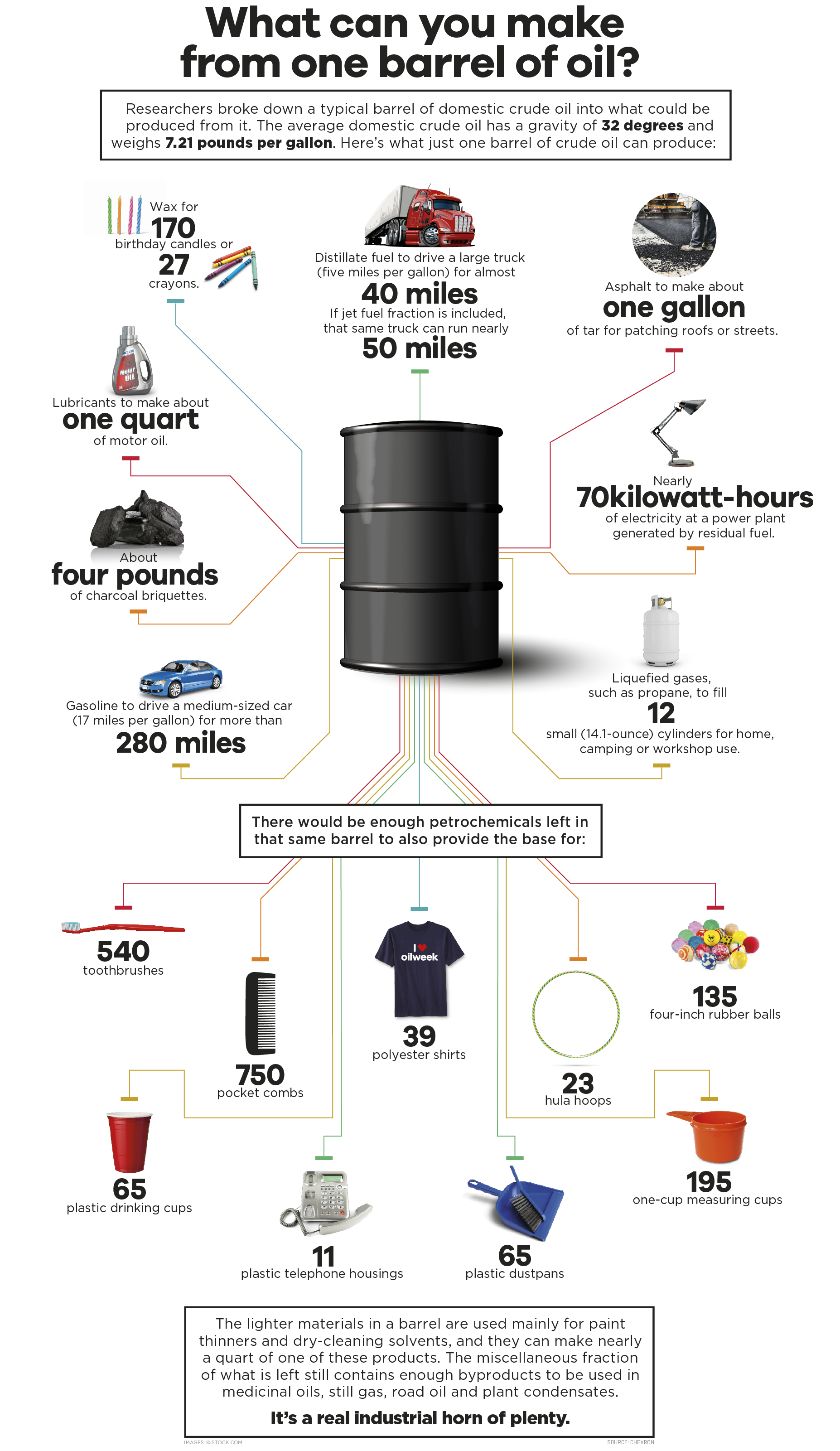
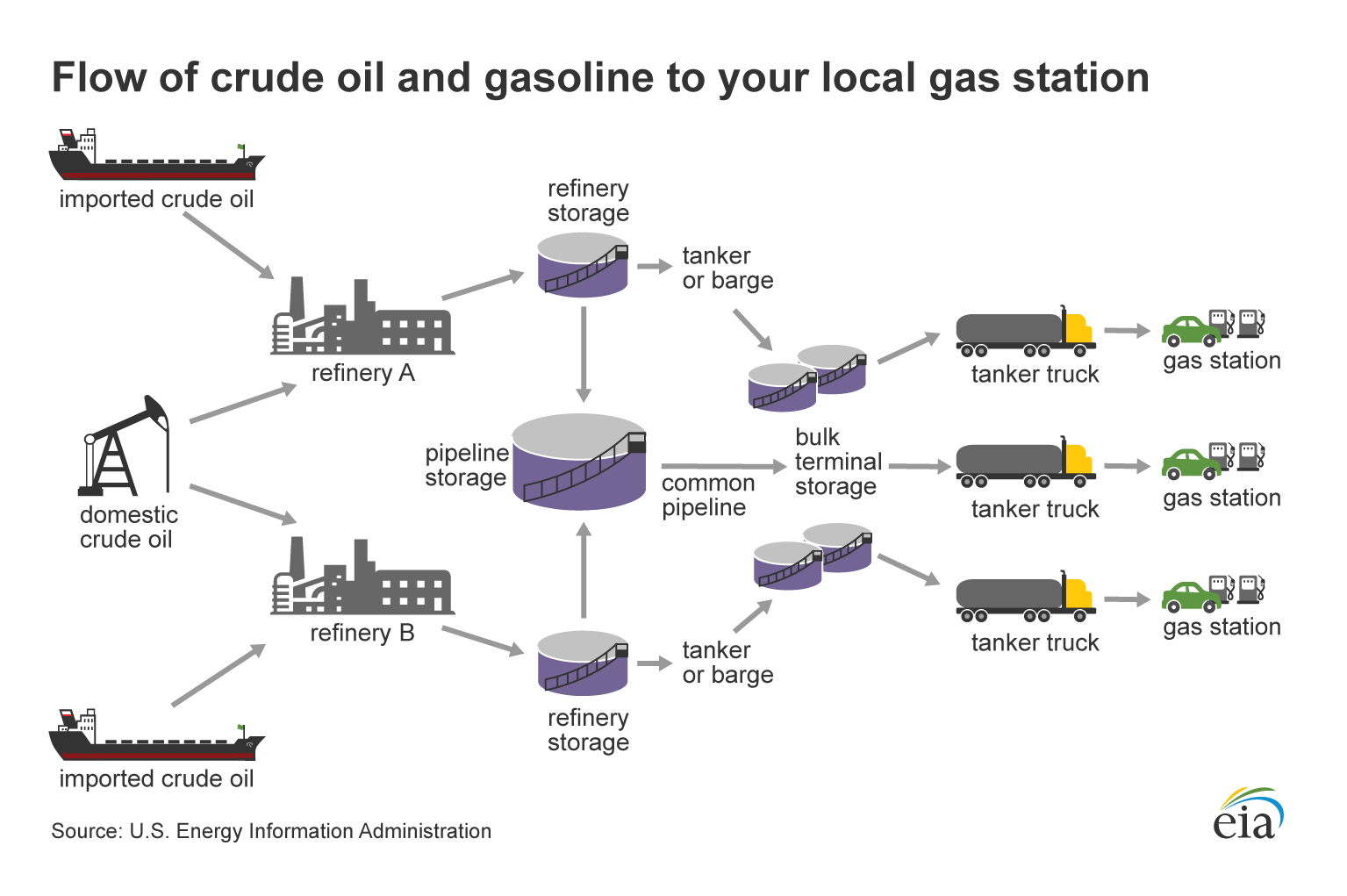
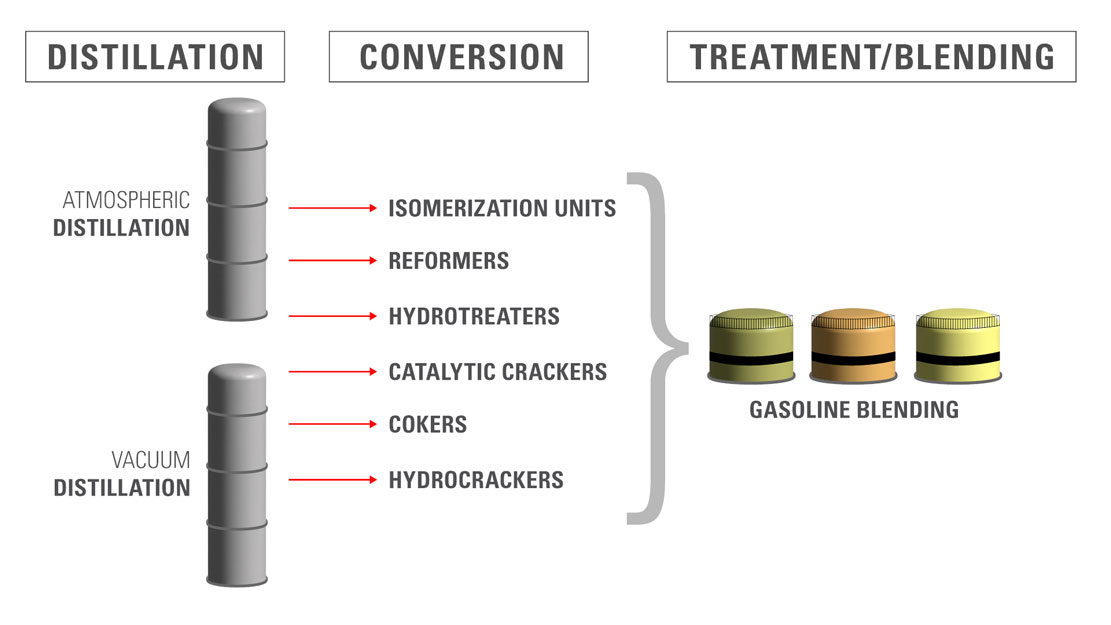

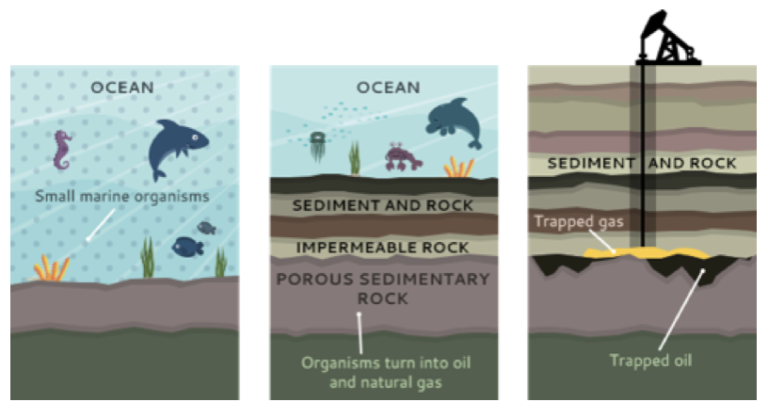