Theory And Design For Mechanical Measurements

In an era defined by unprecedented technological advancement and relentless pursuit of accuracy, the principles underpinning mechanical measurements stand as a critical, yet often overlooked, foundation. From ensuring the structural integrity of bridges to refining the precision of medical devices, the understanding and application of measurement theory and design are paramount. Failing to adhere to these rigorous standards can have catastrophic consequences, impacting safety, efficiency, and innovation across numerous sectors.
This article delves into the core tenets of Theory and Design for Mechanical Measurements, exploring its significance in contemporary engineering and scientific practice. It examines the fundamental concepts, emerging challenges, and future trends shaping the field, drawing on insights from leading experts and organizations. Ultimately, it aims to highlight the crucial role this discipline plays in guaranteeing the reliability and progress of modern technology.
The Foundation: Understanding Measurement Principles
At its heart, Theory and Design for Mechanical Measurements encompasses a systematic approach to quantifying physical quantities. This includes displacement, force, pressure, temperature, and many other variables relevant to mechanical systems. The objective is to develop measurement systems that are accurate, precise, and reliable, providing meaningful data for analysis and decision-making.
Central to this endeavor is a thorough understanding of measurement principles. This involves defining the measurand, selecting appropriate sensors, and implementing signal conditioning techniques to enhance data quality.
Key Concepts in Measurement Theory
Accuracy, precision, and resolution are three cornerstones of measurement theory. Accuracy refers to how closely a measurement agrees with the true value of the measurand, while precision reflects the repeatability of measurements. Resolution defines the smallest change in the measurand that the measurement system can detect.
Error analysis is another critical aspect, involving the identification and quantification of various sources of error. These errors can be systematic (consistent and predictable) or random (unpredictable variations), and understanding their origins is crucial for minimizing their impact on measurement accuracy.
Calibration plays a vital role in ensuring the accuracy of measurement systems. It involves comparing the output of a sensor to a known standard and adjusting the system to minimize deviations. Regular calibration is essential for maintaining the reliability of measurement data over time, as outlined in ISO 9001 standards.
Design Considerations for Measurement Systems
Designing effective measurement systems requires careful consideration of various factors. These include the operating environment, the required accuracy and resolution, and the available resources. The selection of appropriate sensors, signal conditioning circuits, and data acquisition systems is crucial for achieving optimal performance.
Sensor selection is guided by factors such as sensitivity, linearity, and response time. The chosen sensor must be capable of accurately detecting and responding to changes in the measurand under the specific operating conditions.
Signal conditioning circuits are used to amplify, filter, and convert sensor outputs into a usable form. These circuits can improve the signal-to-noise ratio, compensate for sensor non-linearities, and provide the necessary voltage or current levels for data acquisition.
Addressing Uncertainty and Error
Uncertainty quantification is a fundamental aspect of measurement system design. It involves estimating the range of possible values within which the true value of the measurand is likely to lie.
This requires a thorough understanding of all potential sources of error and their contributions to the overall uncertainty. Statistical methods are often used to analyze measurement data and estimate uncertainty intervals.
According to the National Institute of Standards and Technology (NIST), a comprehensive uncertainty analysis should consider both systematic and random errors. Systematic errors can be corrected through calibration, while random errors can be minimized by averaging multiple measurements.
Applications Across Industries
The principles of Theory and Design for Mechanical Measurements are applied across a wide range of industries. From aerospace to biomedical engineering, accurate and reliable measurements are essential for ensuring product quality, safety, and performance.
In the aerospace industry, measurement systems are used to monitor the structural integrity of aircraft and spacecraft. Strain gauges, accelerometers, and pressure sensors provide critical data for detecting potential failures and optimizing performance.
In the biomedical field, precise measurements are crucial for diagnostic and therapeutic applications. Medical devices such as blood pressure monitors, glucose meters, and MRI scanners rely on accurate sensors and signal processing techniques to provide reliable data for patient care.
Case Study: Automotive Engineering
The automotive industry heavily relies on measurement systems for various purposes. This includes engine performance testing, crash testing, and quality control of manufactured components.
Pressure sensors are used to monitor engine performance, fuel efficiency, and emissions. Accelerometers and force sensors are used in crash testing to assess the impact forces and structural integrity of vehicles.
Automotive Research Association of India (ARAI) emphasizes the importance of rigorous testing and validation procedures to ensure the safety and reliability of vehicles. This involves extensive use of measurement systems and data analysis techniques.
Emerging Challenges and Future Trends
The field of mechanical measurements faces several emerging challenges. These include the need for more accurate and reliable sensors, the increasing complexity of measurement systems, and the growing demand for real-time data acquisition and analysis.
Miniaturization of sensors is another significant trend. Micro-electromechanical systems (MEMS) technology enables the development of smaller, more affordable sensors with improved performance characteristics.
The integration of artificial intelligence (AI) and machine learning (ML) techniques is transforming the field. AI algorithms can be used to analyze measurement data, detect anomalies, and predict future performance. This paves the way for more intelligent and autonomous measurement systems.
Conclusion
Theory and Design for Mechanical Measurements remains a cornerstone of modern engineering and scientific practice. As technology continues to advance, the importance of accurate and reliable measurements will only increase. By understanding the fundamental principles, addressing emerging challenges, and embracing new technologies, we can ensure the continued reliability and progress of mechanical systems across all sectors.
Moving forward, greater emphasis should be placed on education and training in this critical discipline. Investing in research and development will foster innovation in sensor technology, data analysis, and measurement system design. Ultimately, this will lead to more accurate, efficient, and safer mechanical systems that benefit society as a whole.
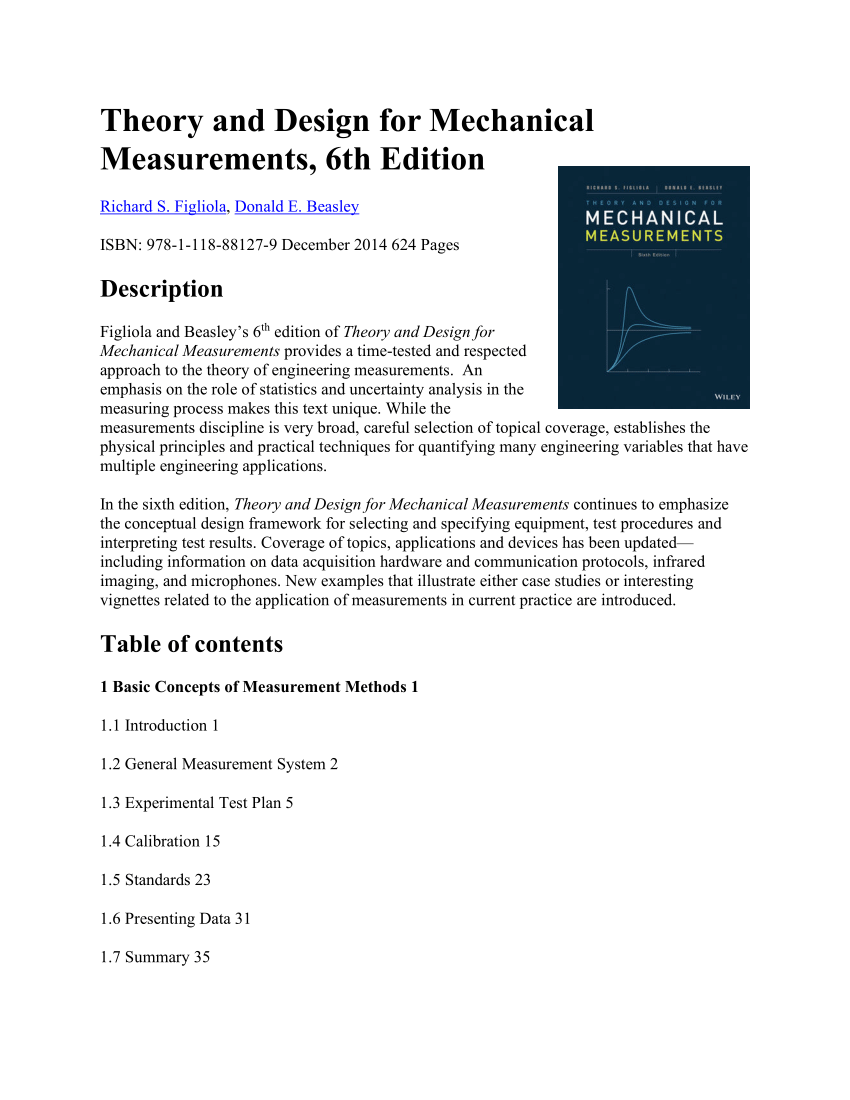





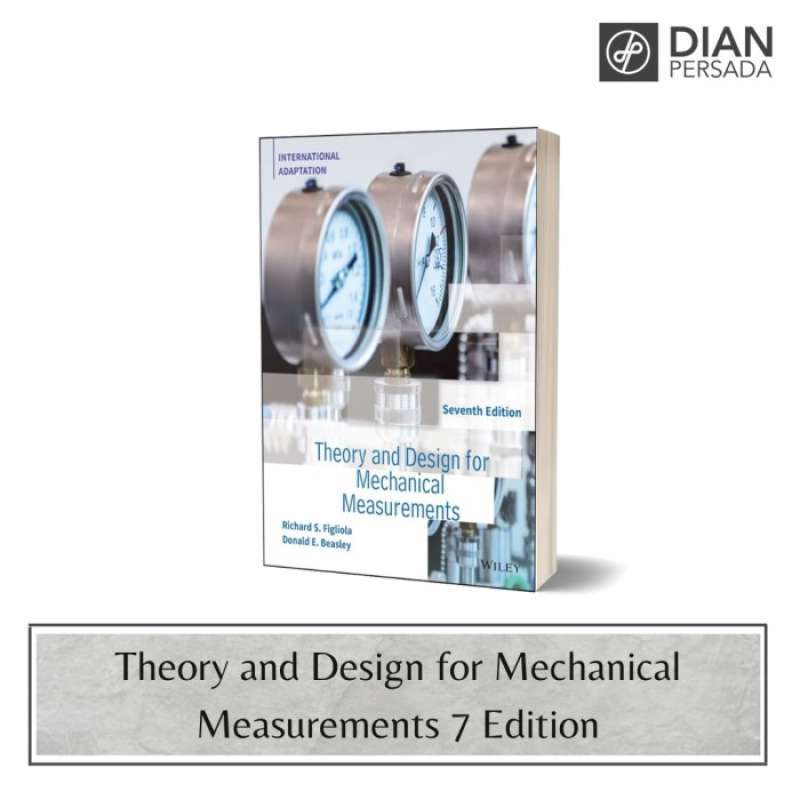
![Theory And Design For Mechanical Measurements [DOWNLOAD $PDF$] Theory and Design for Mechanical Measurements Full-Acces](https://www.yumpu.com/en/image/facebook/64330921.jpg)
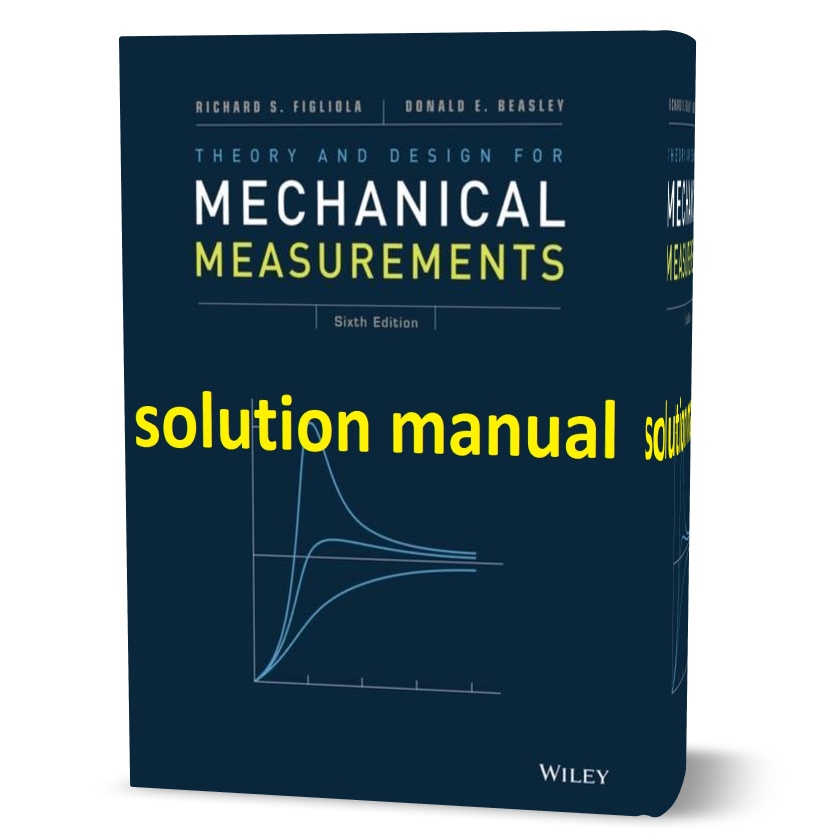


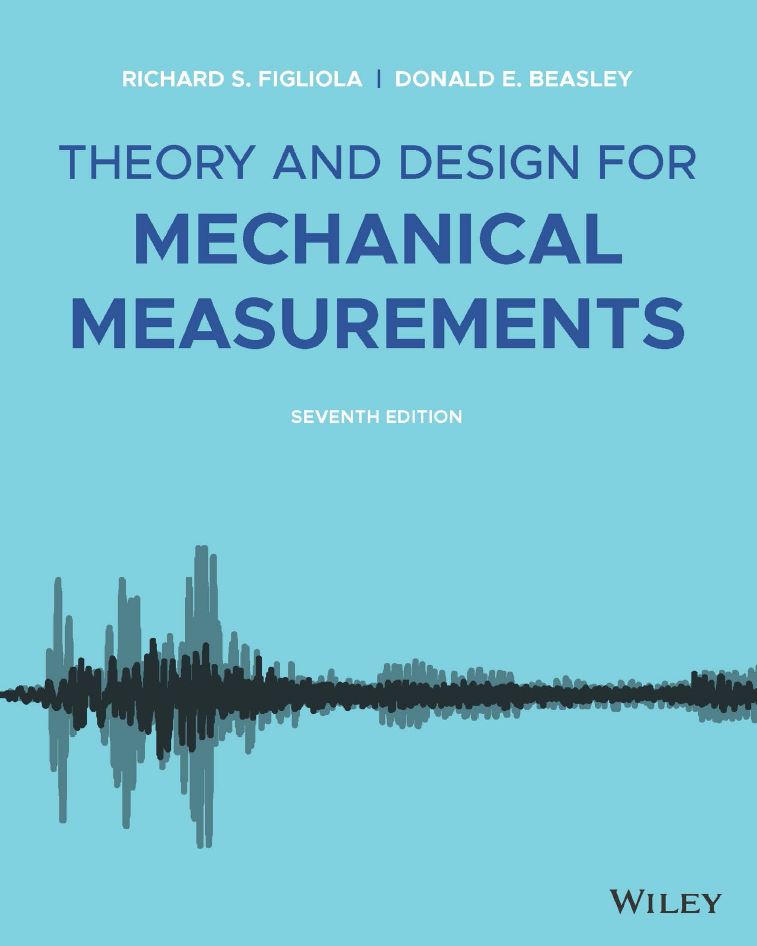



![Theory And Design For Mechanical Measurements PPT - [W.O.R.D] Theory and Design for Mechanical Measurements {read](https://cdn5.slideserve.com/11182148/w-o-r-d-theory-and-design-for-mechanical-n.jpg)
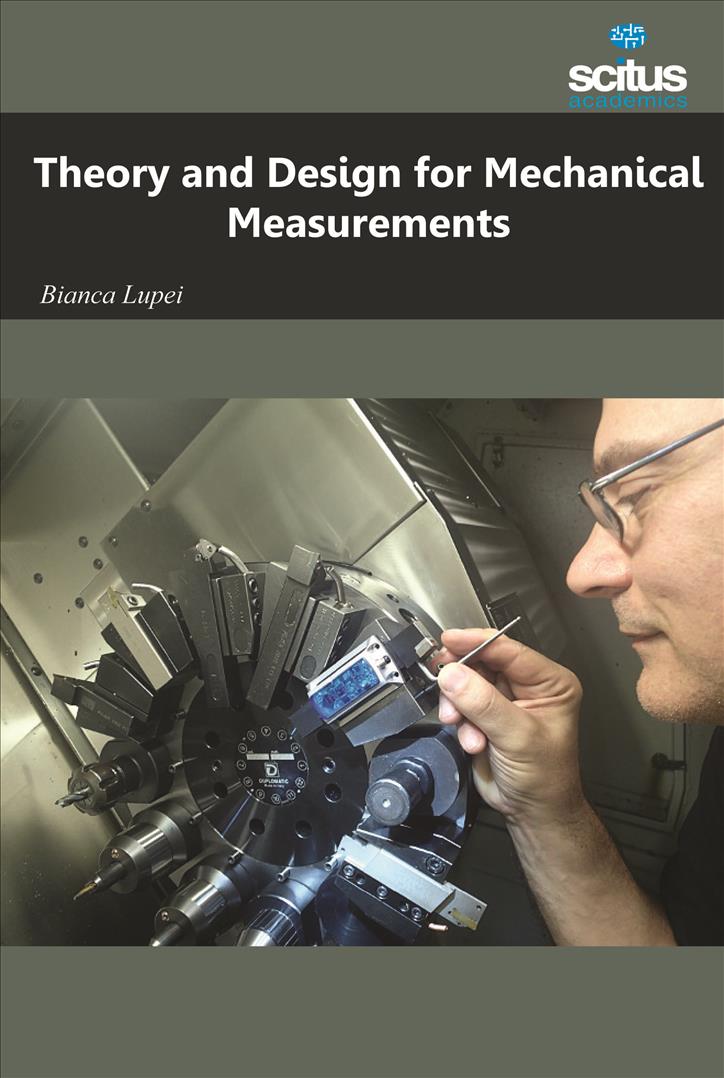
