Which Of These Statements Is True About Surface Finish
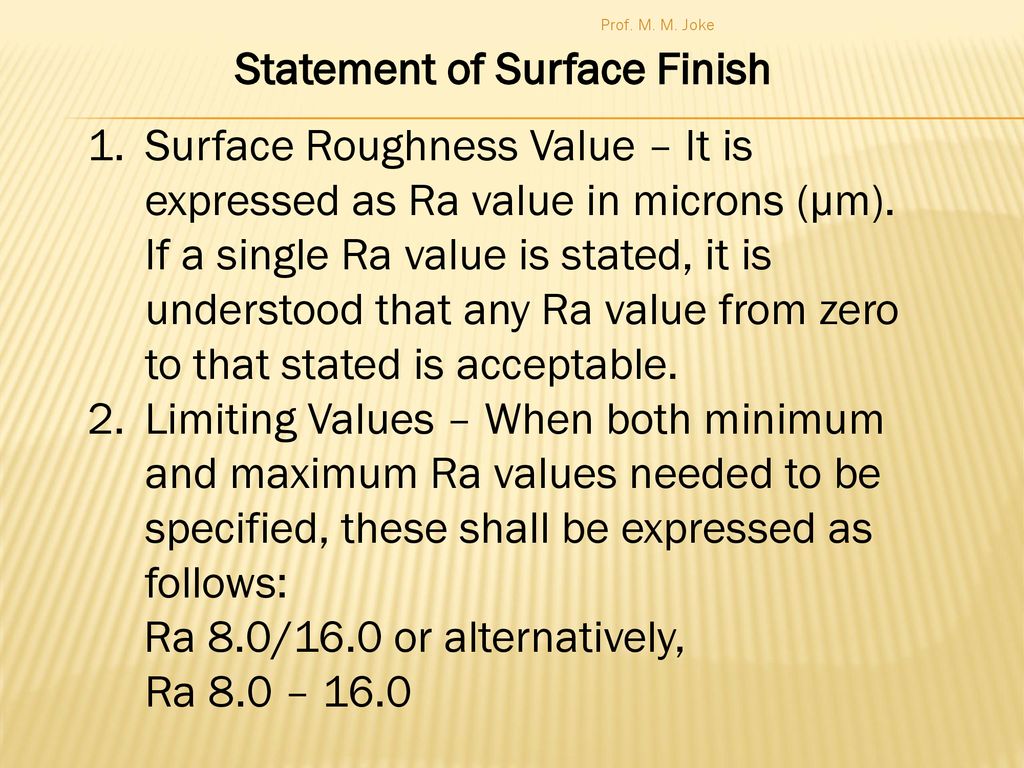
In manufacturing and engineering, the term "surface finish" is ubiquitous, yet often misunderstood. The texture of a component's surface, determined by the production processes, significantly impacts its performance, longevity, and aesthetic appeal. Choosing the appropriate surface finish is paramount, but misconceptions about its characteristics and measurement methods can lead to costly errors and compromised product quality.
This article delves into the nuances of surface finish, examining common statements about its properties and verifying their accuracy based on scientific evidence and industry standards. We explore the complex interplay of parameters, measurement techniques, and functional implications, providing a clearer understanding of this critical aspect of engineering design and manufacturing.
Understanding Surface Finish Parameters
Surface finish isn't simply about whether something feels smooth or rough. It is characterized by a multitude of parameters that quantify various aspects of the surface texture. These parameters are essential for specifying and controlling the surface characteristics required for a particular application.
Ra, or average roughness, is perhaps the most widely used parameter. It represents the arithmetic average of the absolute values of the deviations of the roughness profile from the mean line. A low Ra value generally indicates a smoother surface, but it's crucial to remember that Ra alone doesn't provide a complete picture of the surface texture.
Other important parameters include Rz, the average maximum height of the profile, and Rq, the root mean square roughness. These parameters provide more information about the peaks and valleys of the surface profile, which can be critical in applications where friction, wear, or sealing are important considerations. Skewness (Rsk) and kurtosis (Rku) describe the asymmetry and sharpness of the profile, respectively.
Common Statements About Surface Finish: Fact vs. Fiction
"A lower Ra value always means better performance."
This statement is FALSE. While a lower Ra value often indicates a smoother surface, which can be beneficial in some applications, it is not universally true that lower is always better. For example, a surface that is too smooth might exhibit excessive stiction (static friction) or inadequate lubrication retention. Surfaces requiring lubrication often need a controlled degree of roughness to provide reservoirs for oil.
According to a study published in the Journal of Tribology, the optimal surface roughness for sliding contact applications depends on the specific materials, lubricants, and operating conditions. In some cases, a slightly rougher surface can improve the load-carrying capacity and reduce wear by promoting hydrodynamic lubrication.
"Surface finish only affects aesthetics."
This statement is demonstrably FALSE. While surface finish certainly contributes to the aesthetic appeal of a product, its impact extends far beyond visual considerations. Surface texture directly influences functional properties such as friction, wear resistance, sealing performance, fatigue life, and corrosion resistance.
The National Institute of Standards and Technology (NIST) emphasizes that surface finish is a critical factor in determining the performance and reliability of mechanical components. A poor surface finish can lead to premature failure due to stress concentrations, increased friction, or accelerated corrosion.
"All measurement techniques are equally accurate for determining surface finish."
This statement is FALSE. There are several different methods to measure surface finish, each with its strengths and limitations. Contact profilometry, which involves dragging a stylus across the surface, is a common technique, but it can be slow and may damage delicate surfaces.
Optical methods, such as interferometry and confocal microscopy, are non-contact techniques that can provide high-resolution measurements without damaging the surface. However, optical methods may be affected by surface reflectivity and transparency. Atomic force microscopy (AFM) offers the highest resolution but is limited to small areas.
The choice of measurement technique depends on the specific application, the required accuracy, and the nature of the surface being measured. Understanding the limitations of each method is crucial for obtaining reliable and meaningful results.
"Surface finish is solely determined by the manufacturing process."
This statement is mostly TRUE, but it oversimplifies the situation. The manufacturing process, such as machining, grinding, polishing, or casting, is the primary determinant of surface finish. However, other factors can also play a role.
Material properties, environmental conditions (e.g., temperature and humidity), and post-processing treatments can all affect the final surface texture. For instance, heat treatment can cause surface oxidation, while coatings can alter the surface roughness and chemistry.
The Importance of Specifying and Controlling Surface Finish
Properly specifying and controlling surface finish is crucial for ensuring product quality and performance. Drawings and specifications should clearly define the required surface finish parameters and the acceptable tolerances. Furthermore, quality control procedures should include appropriate measurement techniques to verify that the specified surface finish has been achieved.
Failure to control surface finish can lead to a variety of problems, including premature wear, leakage, increased friction, and reduced fatigue life. In critical applications, such as aerospace and medical devices, these problems can have serious consequences.
Looking Ahead
Advancements in manufacturing technology are leading to new and improved methods for creating and controlling surface finish. Additive manufacturing, for example, offers the potential to create complex geometries with customized surface textures. Similarly, new measurement techniques, such as advanced optical methods, are providing more detailed and accurate surface characterization.
As technology evolves, a deeper understanding of surface finish and its impact on functional performance will be even more critical. Continued research and development in this area are essential for improving product quality, reducing manufacturing costs, and enabling new and innovative designs.
By dispelling common misconceptions and embracing a more nuanced understanding of surface finish, engineers and manufacturers can make informed decisions that lead to improved product performance and enhanced customer satisfaction. The ongoing pursuit of knowledge in this field will undoubtedly shape the future of manufacturing.
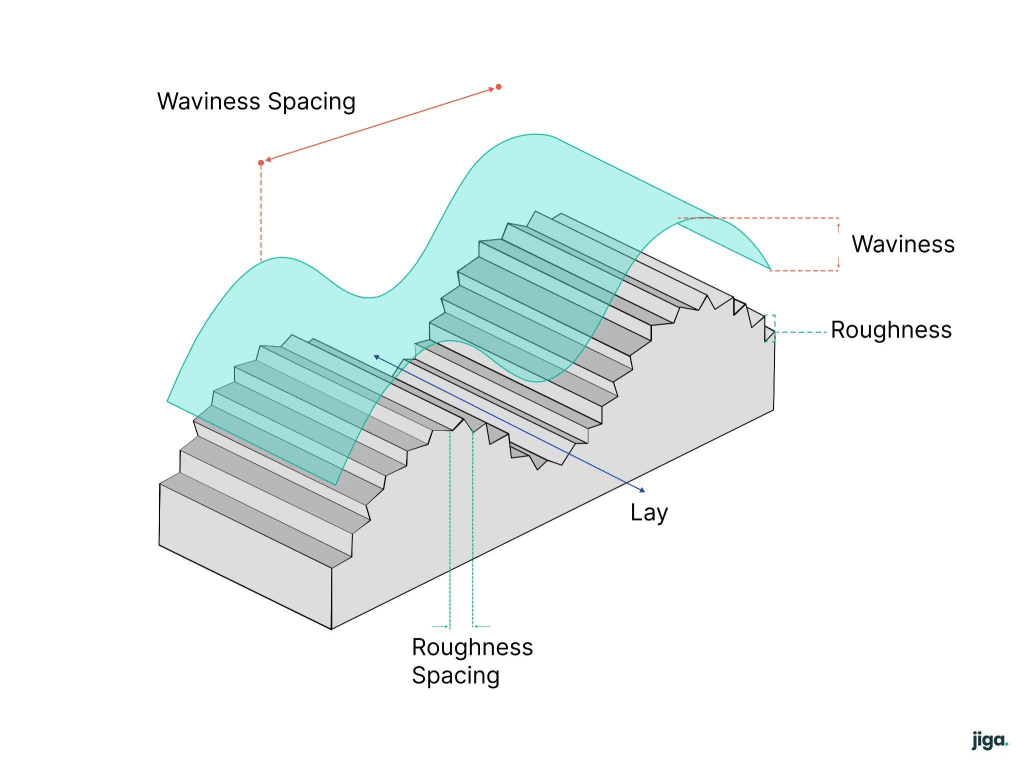
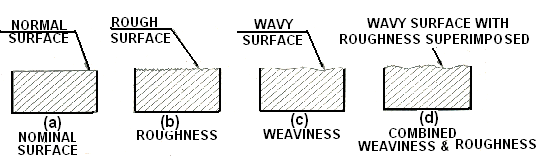
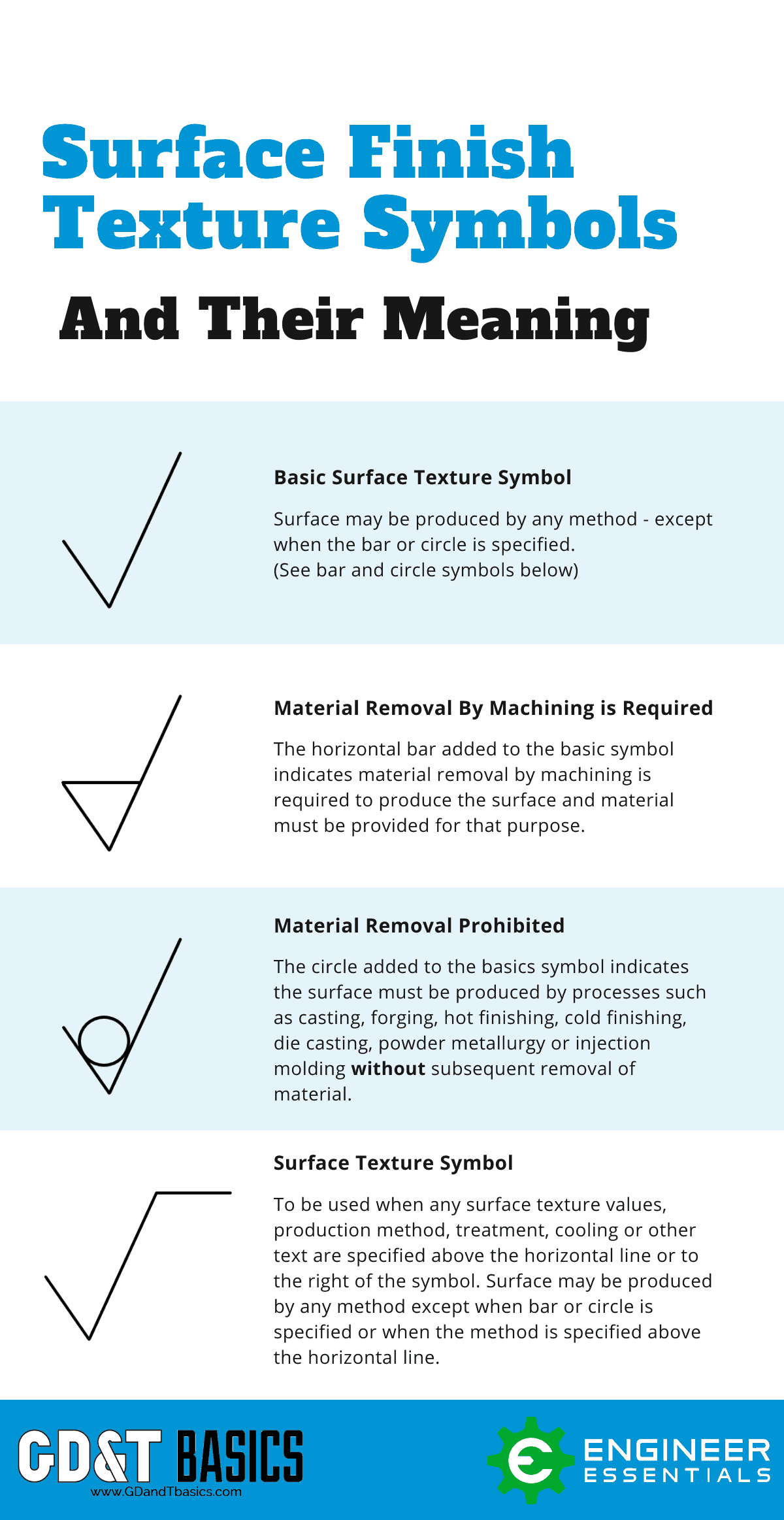

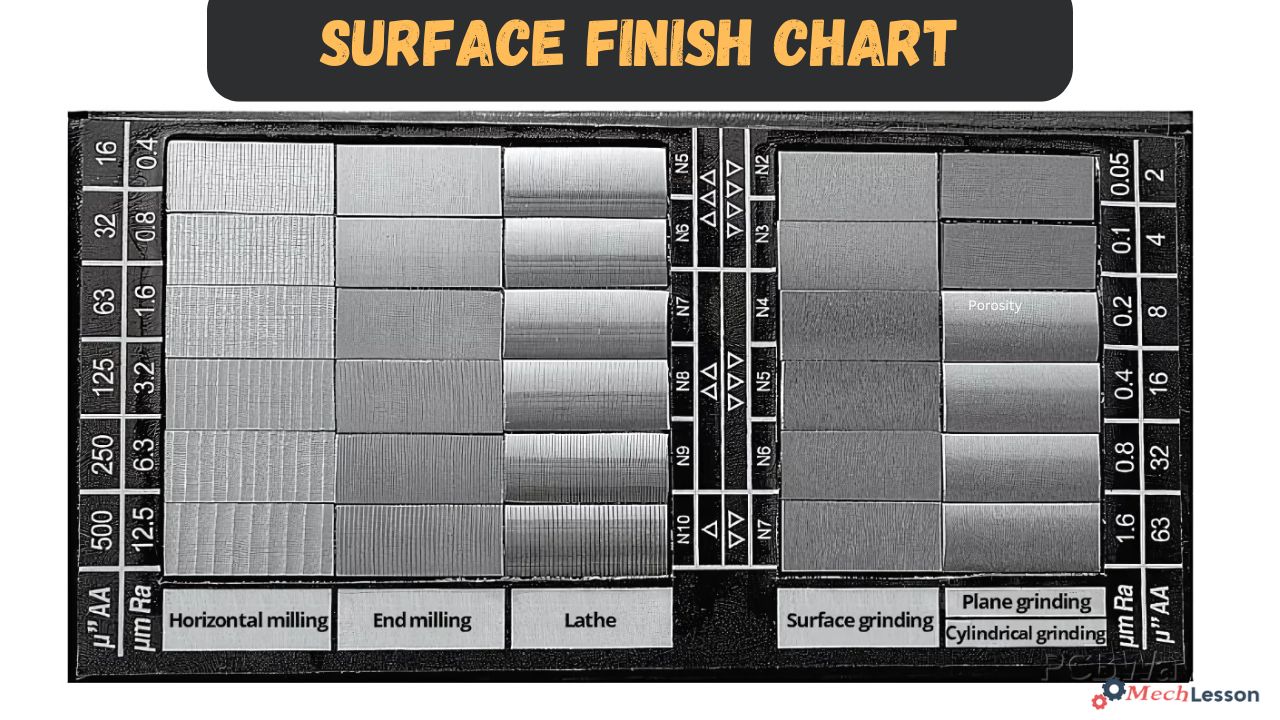
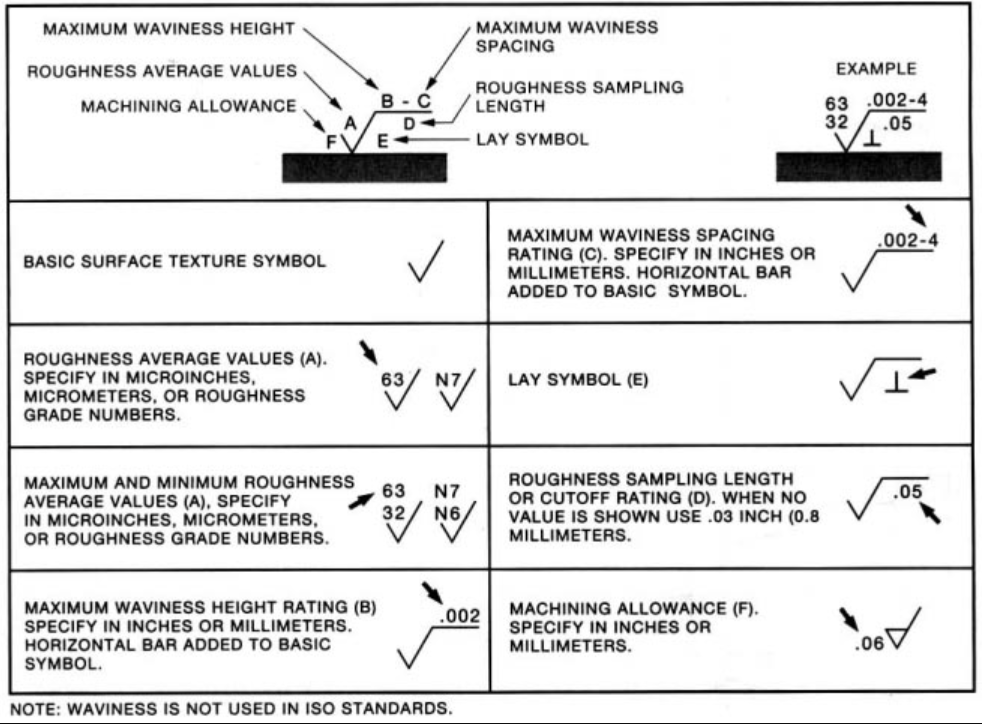



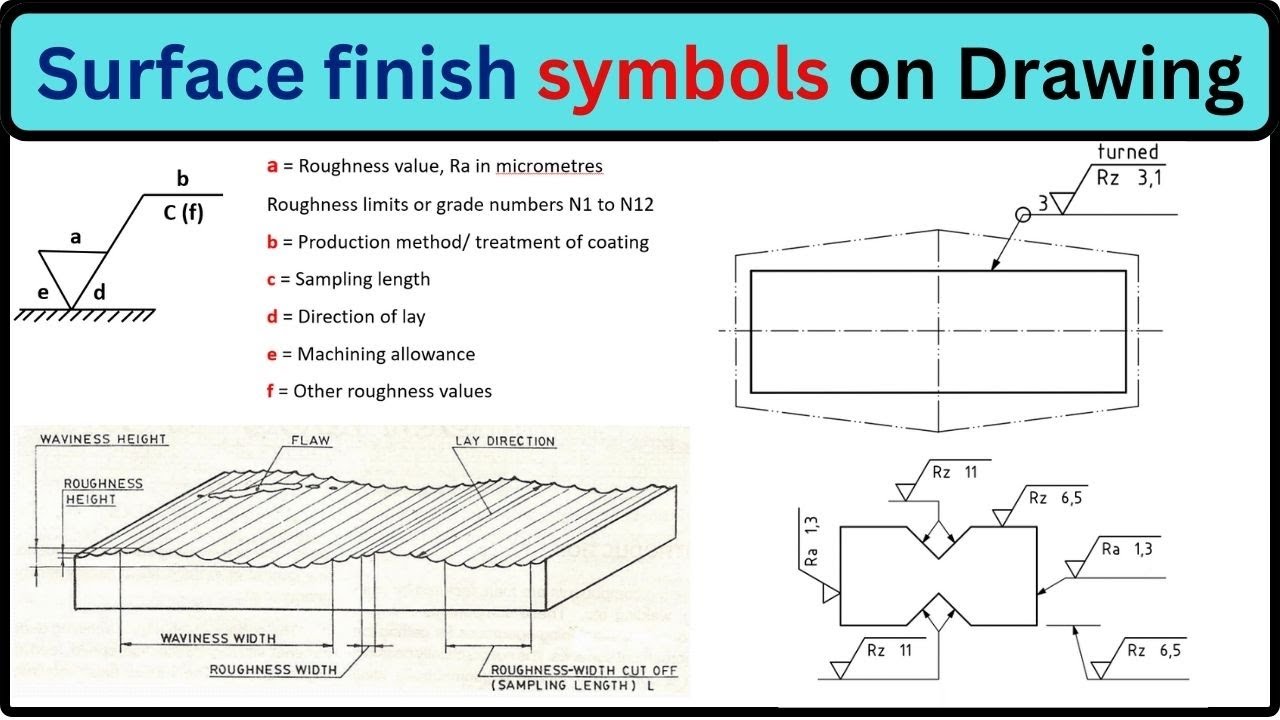




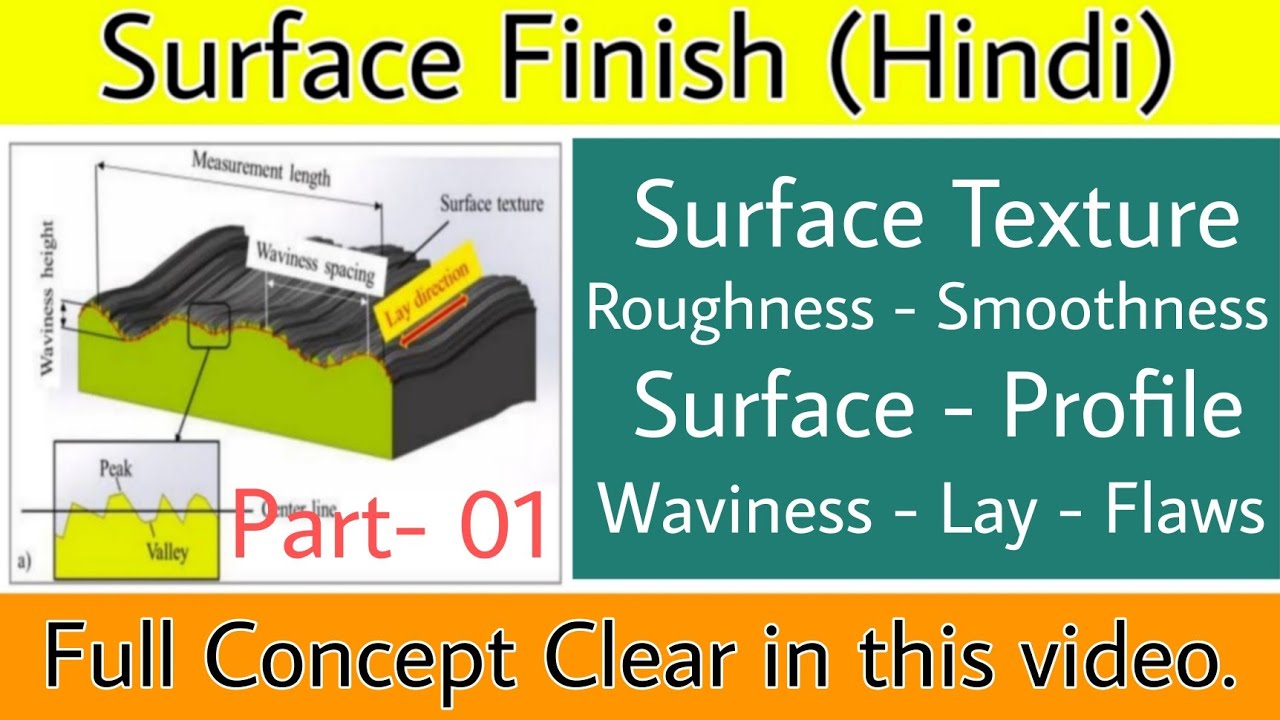
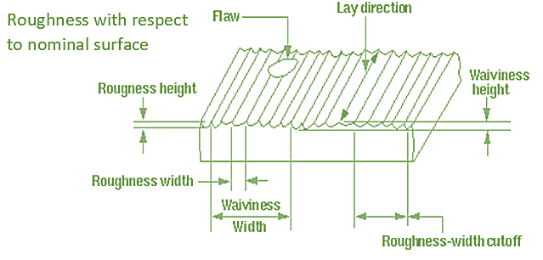

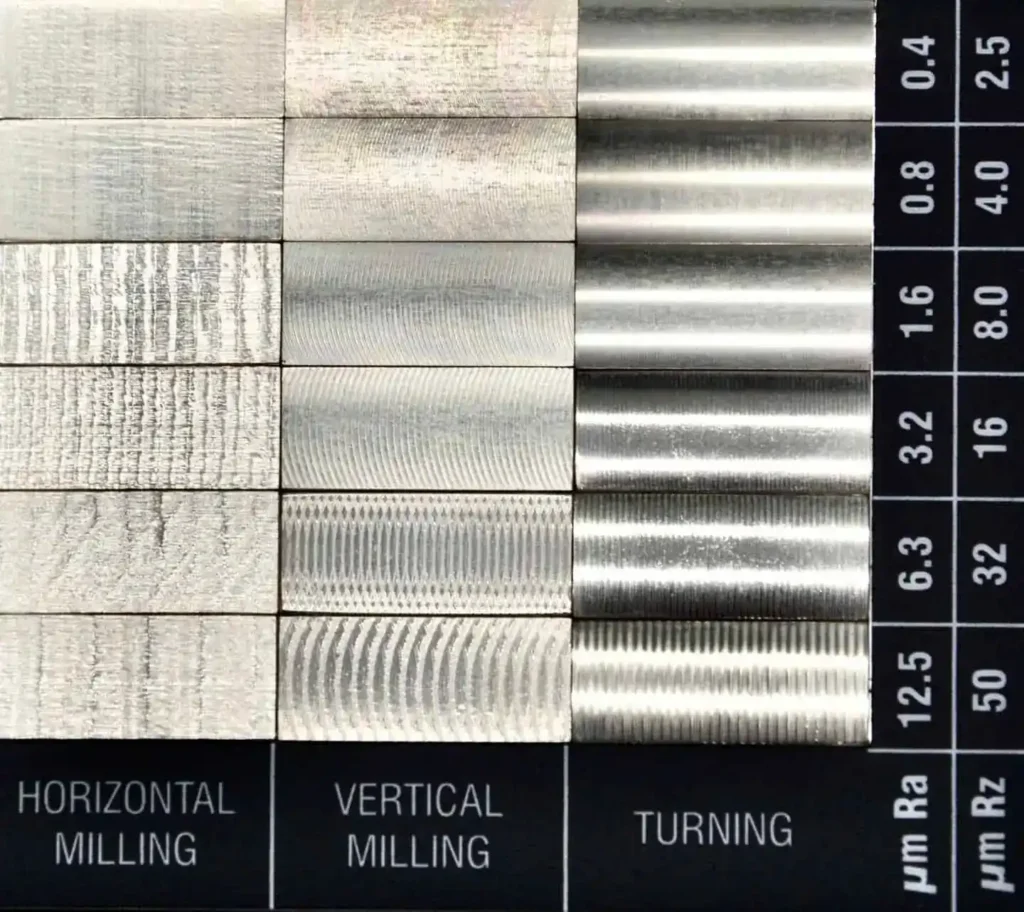