How To Find Direct Materials Cost

Imagine yourself in a bustling workshop, the scent of freshly cut wood filling the air, the rhythmic hum of machinery a constant companion. You’re surrounded by stacks of lumber, bolts of fabric, containers of paint – the raw ingredients that, with skill and precision, will transform into something beautiful and functional. But beneath the creative energy lies a critical question: How much did all of this actually cost?
Unlocking the secrets of direct materials cost is fundamental for any business involved in manufacturing or production. This isn’t just about knowing the price tag; it's about understanding a key driver of profitability, enabling accurate pricing, and making informed decisions about sourcing and production efficiency. This article will break down the process of identifying and calculating direct materials cost, providing a clear roadmap for businesses of all sizes to master this essential element of cost accounting.
The Foundation: Defining Direct Materials
Before diving into calculations, let's solidify the definition of direct materials. These are the raw materials and components that become an integral part of the finished product. Think of the wood in a chair, the steel in a car, or the flour in a loaf of bread. These materials can be directly traced back to the final product.
Distinguishing direct materials from indirect materials is crucial. Indirect materials, such as cleaning supplies or machine lubricants, are necessary for the production process but don't become part of the final product and are typically categorized as overhead costs.
Step-by-Step: Calculating Direct Materials Cost
The journey to calculating direct materials cost involves a few key steps, each building upon the previous one. We need to carefully track all purchases and usage.
1. Determine Beginning Inventory
Start by identifying the value of your beginning inventory of direct materials. This is the value of raw materials you had on hand at the start of the accounting period (month, quarter, or year). Accurate inventory records are essential.
A physical count and valuation are usually required.
2. Calculate Purchases of Direct Materials
Next, track all purchases of direct materials made during the accounting period. This includes not only the invoice price of the materials but also any associated costs like freight, insurance during transit, and applicable taxes.
Carefully review your accounting records and receipts.
3. Adjust for Purchase Discounts and Returns
Account for any purchase discounts received from suppliers. These discounts reduce the actual cost of the materials. Similarly, deduct the cost of any materials returned to suppliers due to defects or other reasons.
Maintaining organized records of discounts and returns is key.
4. Calculate Materials Available for Use
Add the beginning inventory to the net purchases (purchases less discounts and returns) to determine the total value of materials available for use during the period. This represents the total pool of direct materials that could have been used in production.
This figure is a crucial intermediate step in the calculation.
5. Determine Ending Inventory
Now, determine the value of your ending inventory of direct materials. This is the value of raw materials remaining on hand at the end of the accounting period. Again, a physical count and valuation are usually necessary.
Consistency in valuation methods (e.g., FIFO, LIFO, weighted-average) is important.
6. Calculate Direct Materials Used
Finally, subtract the ending inventory from the materials available for use to arrive at the direct materials used in production during the period. This is the core figure we've been working towards.
The formula is: Direct Materials Used = Beginning Inventory + Purchases - Purchase Discounts - Purchase Returns - Ending Inventory.
Illustrative Example
Let's bring these steps to life with a simple example. Imagine a small bakery that makes artisanal bread.
At the beginning of the month, the bakery had $500 worth of flour (beginning inventory). During the month, they purchased an additional $2,000 worth of flour. They received a $100 discount on a bulk order and returned $50 worth of damaged flour.
At the end of the month, they had $400 worth of flour remaining (ending inventory). Let's calculate the direct materials used.
Materials available for use: $500 (beginning inventory) + $2,000 (purchases) - $100 (discount) - $50 (returns) = $2,350.
Direct materials used: $2,350 (materials available for use) - $400 (ending inventory) = $1,950. Therefore, the direct materials cost for flour used in bread production during the month is $1,950.
The Importance of Accurate Tracking
The accuracy of direct materials cost calculations hinges on diligent record-keeping. Implementing a robust inventory management system, whether manual or automated, is essential. This system should track all purchases, usage, discounts, and returns of direct materials.
Regular inventory counts and reconciliations help ensure accuracy. Consider using barcode scanners or RFID tags for more efficient tracking.
Using a system like First-In, First-Out (FIFO), Last-In, First-Out (LIFO) or the weighted-average method should also be considered to value inventory.
The Impact on Profitability and Pricing
Understanding direct materials cost is crucial for determining the cost of goods sold (COGS). COGS is a key component in calculating gross profit, which is a direct measure of profitability. An accurate COGS is essential for financial reporting and tax purposes.
Direct materials cost also plays a vital role in pricing decisions. Businesses need to understand their costs to set prices that are competitive yet profitable.
Underestimating direct materials cost can lead to underpricing and reduced profitability. Conversely, overestimating costs can lead to overpricing and lost sales.
Beyond the Basics: Advanced Considerations
For more complex manufacturing processes, calculating direct materials cost can become more intricate. Bills of materials (BOMs), which list all the components required to produce a product, are essential tools for tracking material usage.
Standard costing, a cost accounting technique, involves setting predetermined costs for direct materials. This allows for variance analysis, where actual costs are compared to standard costs, highlighting areas for improvement.
In today's global marketplace, sourcing materials from different suppliers and countries can add complexity. Fluctuations in exchange rates and import duties need to be factored into the direct materials cost calculation.
Embracing Efficiency and Sustainability
Beyond the financial aspects, understanding direct materials cost can also drive improvements in operational efficiency and sustainability. By identifying areas where material waste is high, businesses can implement measures to reduce waste and improve resource utilization.
Negotiating better prices with suppliers, exploring alternative materials, and optimizing production processes can all lead to lower direct materials costs and a more sustainable business model. The Environmental Protection Agency (EPA) offers resources and best practices for sustainable materials management.
Consider implementing lean manufacturing principles to minimize waste and improve efficiency. This leads to lower costs and a more sustainable business operation.
Conclusion: Mastering the Material World
Calculating direct materials cost is more than just a bookkeeping exercise; it's a strategic imperative. It empowers businesses to understand their costs, make informed decisions, and ultimately improve their profitability and sustainability. By mastering the principles and techniques outlined in this article, you can unlock the full potential of your materials and build a more resilient and successful business.
So, step back into that bustling workshop, armed with a newfound understanding of direct materials cost. The hum of machinery takes on a new meaning, the stacks of lumber and bolts of fabric now represent not just raw materials, but also the potential for profitability and sustainable growth. You have the tools; now go create something amazing!

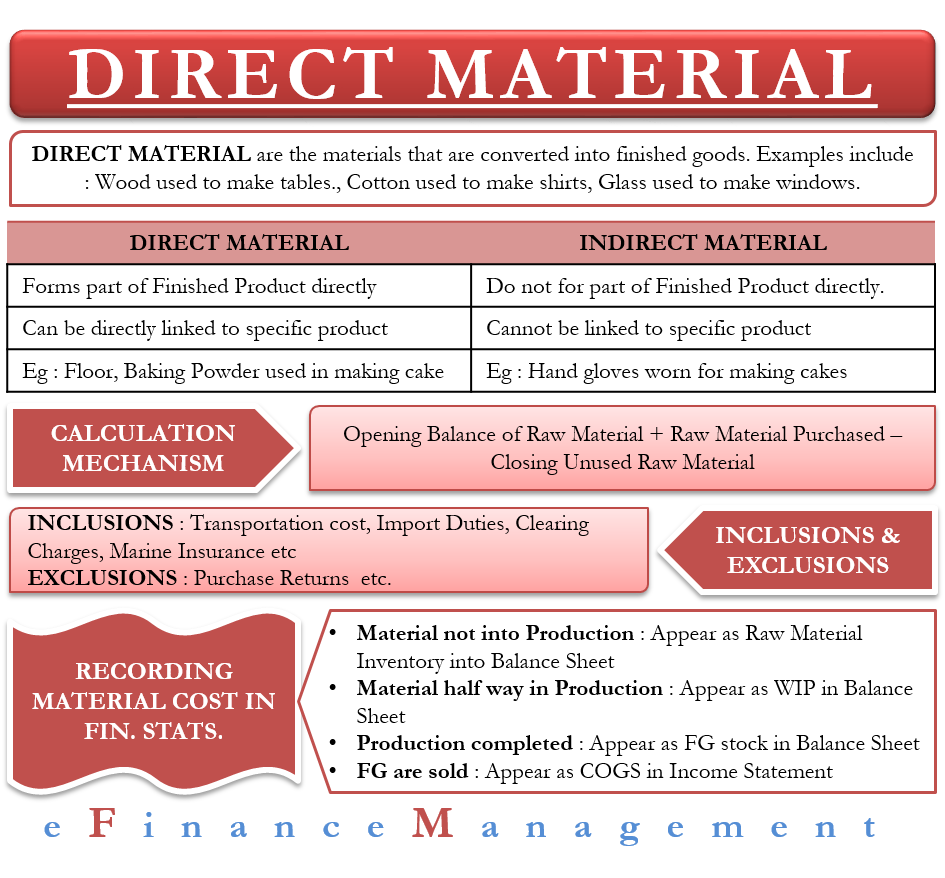
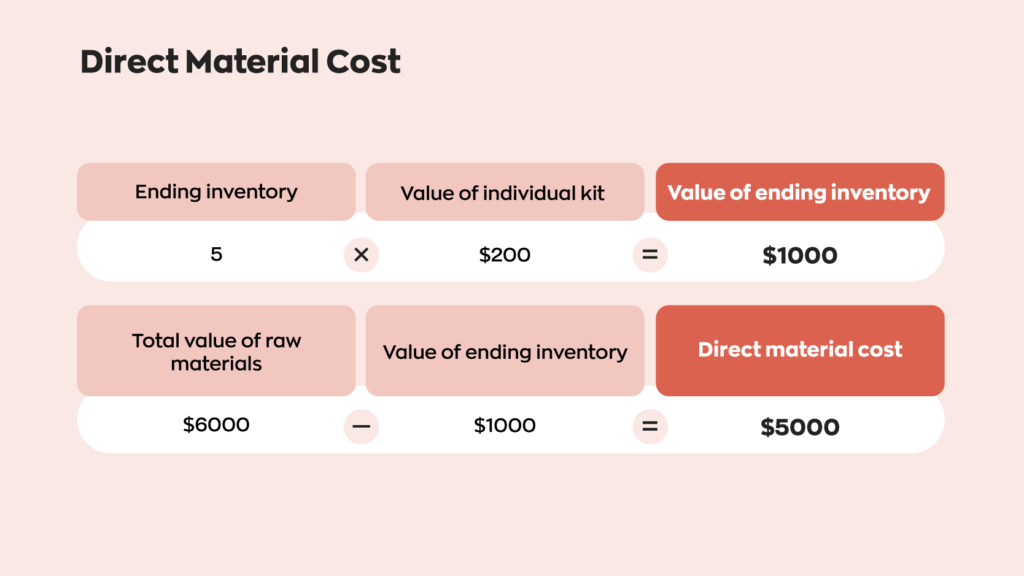
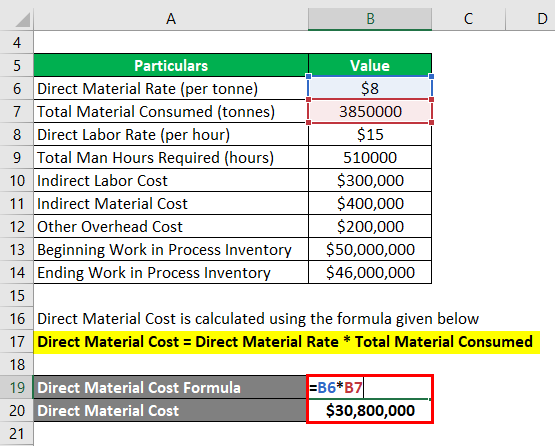
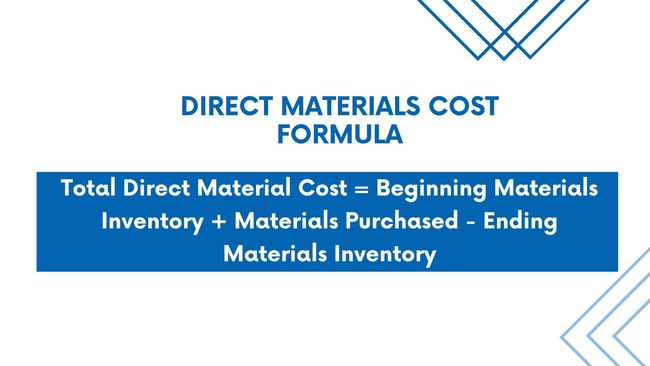

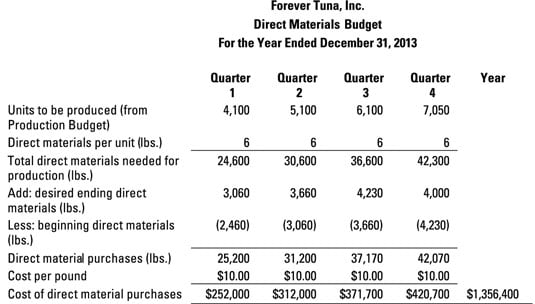
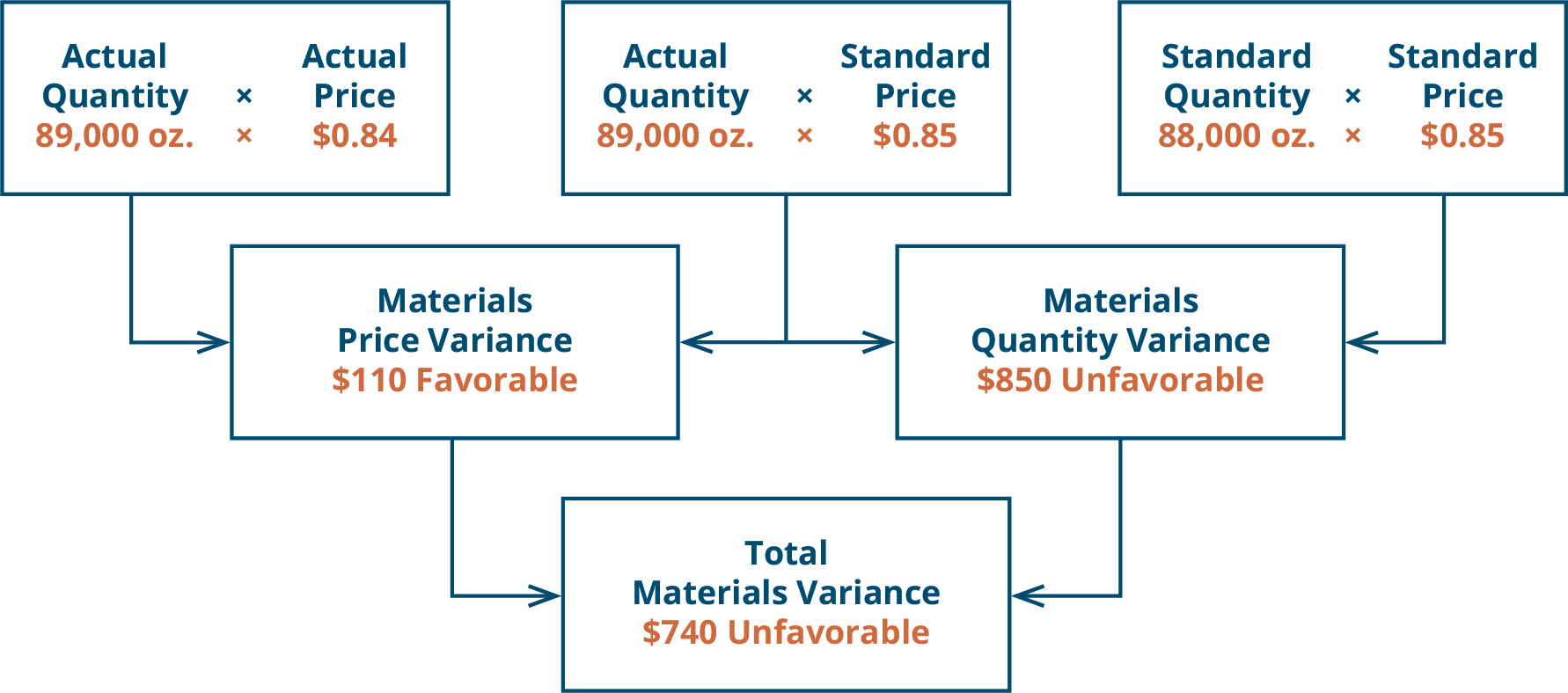
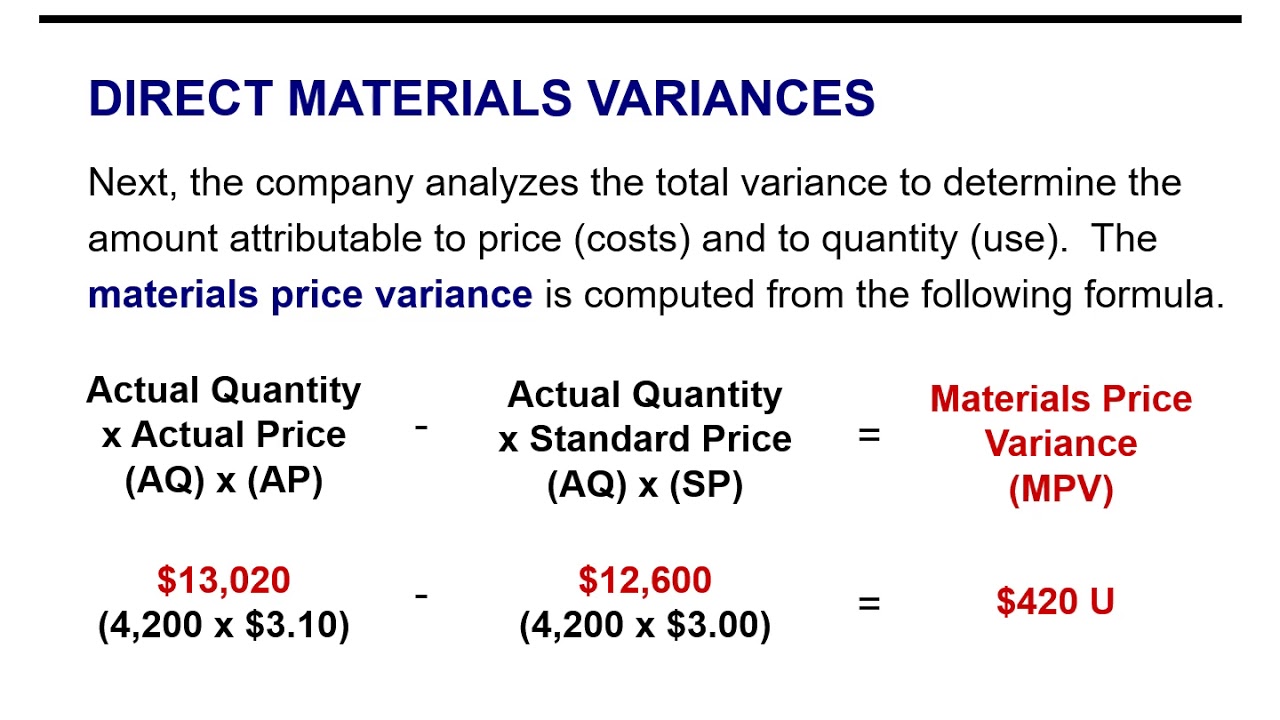
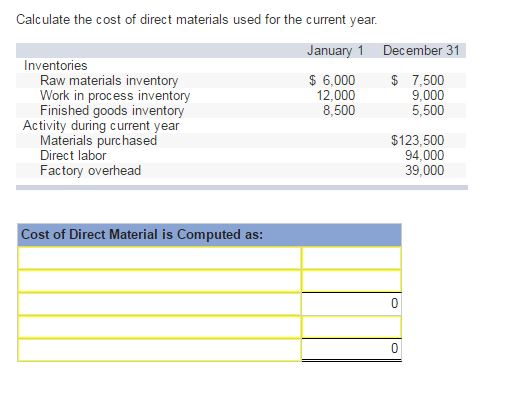
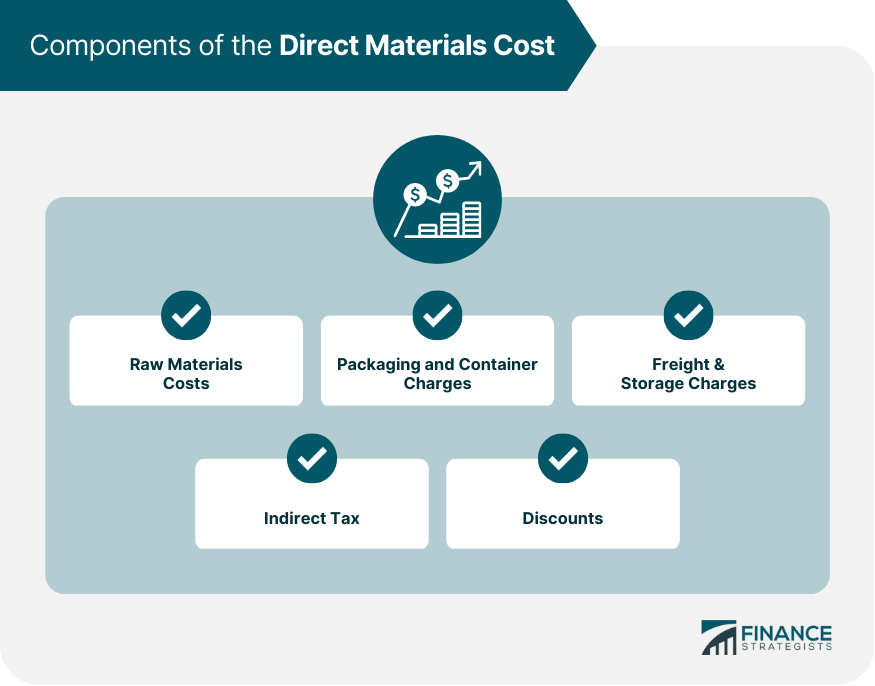
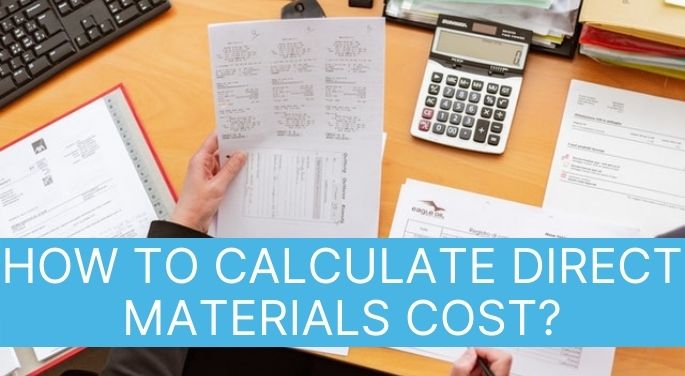
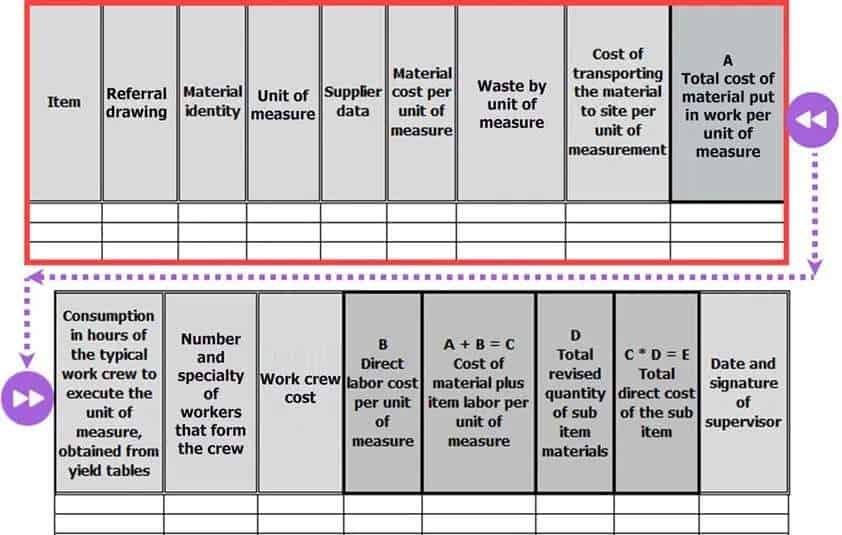
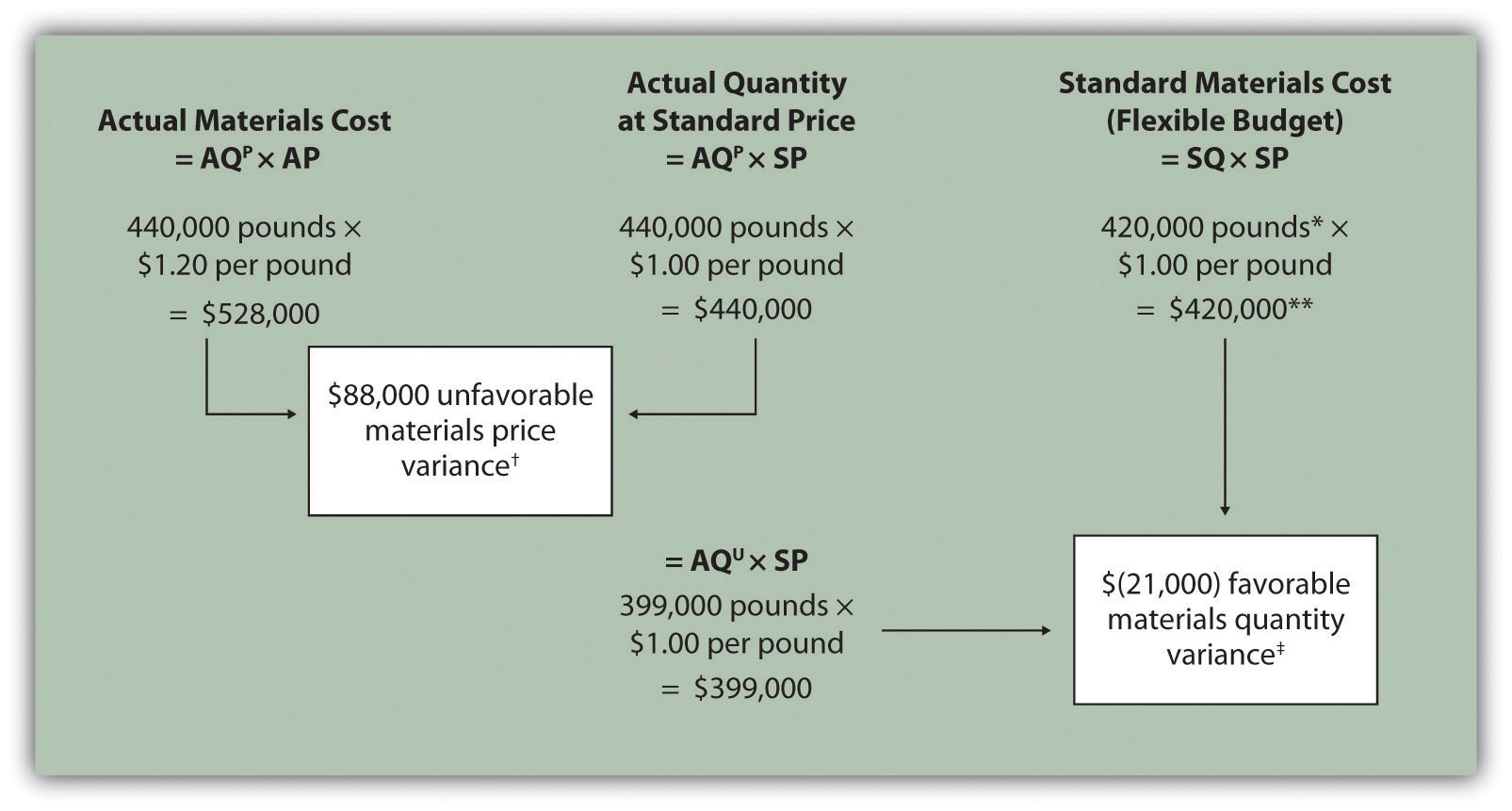

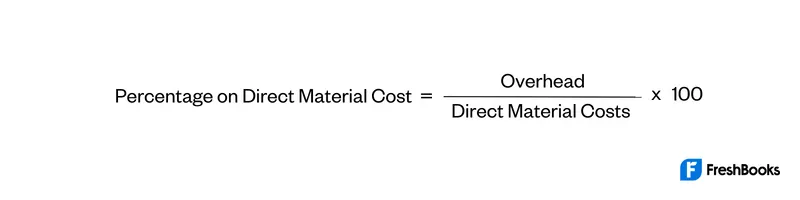

