Plastic Welding Nozzle For Heat Gun

The rise of plastic consumption has brought with it a parallel challenge: managing plastic waste. A novel solution gaining traction is the adaptation of heat guns for plastic welding, specifically through specialized nozzles designed for this purpose.
This development promises not only enhanced repair capabilities but also a more sustainable approach to plastic use, but questions about long-term durability and scalability remain.
At the heart of this innovation lies the plastic welding nozzle for heat guns, a seemingly simple attachment with the potential to reshape how we interact with plastic materials. It aims to facilitate the repair and reuse of plastics, extending their lifespan and diverting them from landfills.
This tool allows for targeted heating and melting of plastic, creating a bond between separate pieces. By offering a localized and controlled heating area, the nozzle mitigates the risk of warping or burning the surrounding plastic.
The Technology Behind the Nozzle
The concept is relatively straightforward. Standard heat guns expel hot air, but these specialized nozzles focus the heat into a narrow stream. This focused heat is crucial for creating a strong weld without damaging the integrity of the surrounding material.
Materials used for the nozzles themselves vary, but often include heat-resistant metals like stainless steel. These materials ensure the nozzle can withstand the high temperatures required for melting plastic.
Different nozzle designs cater to various types of plastic welding, including butt welding, lap welding, and corner welding. The choice of nozzle depends heavily on the specific application and the type of plastic being worked with.
Applications Across Industries
The applications of plastic welding nozzles for heat guns are wide-ranging. The automotive industry, for example, benefits greatly from this technology. Damaged bumpers, interior trim, and other plastic components can be repaired instead of replaced.
In the construction sector, plastic pipes, sheeting, and other building materials can be joined and repaired on-site. This saves time and reduces material waste.
Furthermore, the nozzles are gaining popularity in DIY and hobbyist circles. People are using them to repair household items, create custom plastic projects, and recycle plastic waste into new objects.
Environmental and Economic Benefits
The environmental benefits of plastic welding are significant. By repairing and reusing existing plastics, we reduce the demand for new plastic production.
According to a report by the EPA, plastic production contributes significantly to greenhouse gas emissions. Reduced production translates directly to a smaller carbon footprint.
Economically, plastic welding can also be a cost-effective alternative to replacing damaged plastic items. Repairs are often cheaper than purchasing new parts, saving consumers and businesses money.
Challenges and Considerations
Despite the potential benefits, there are challenges to overcome. The strength and durability of plastic welds can vary depending on the type of plastic, the skill of the operator, and the quality of the equipment.
Not all plastics are created equal. Some plastics, like PVC, weld more easily than others, such as polyethylene.
Proper ventilation is crucial, as some plastics release harmful fumes when heated. Operators should always wear appropriate safety gear, including respirators and eye protection.
Future Outlook
The future of plastic welding nozzles for heat guns appears promising. Ongoing research and development are focused on improving nozzle designs, expanding the range of weldable plastics, and streamlining the welding process.
The increased availability of tutorials and training resources is also helping to democratize the technology, making it accessible to a wider audience. This means more widespread adoption across various industries and applications.
While it's unlikely that plastic welding will completely eliminate the need for new plastic production, it offers a valuable tool in the fight against plastic waste and promotes a more circular economy. With continued innovation and responsible implementation, this technology has the potential to make a significant contribution to a more sustainable future.
As consumer awareness grows and regulations tighten around plastic waste, the demand for plastic welding solutions is likely to increase.
"This technology represents a significant step forward in our efforts to manage plastic waste," says Dr. Anya Sharma, a materials scientist at the University of California, Berkeley. "By empowering individuals and businesses to repair and reuse plastics, we can reduce our reliance on virgin materials and minimize the environmental impact of plastic production."
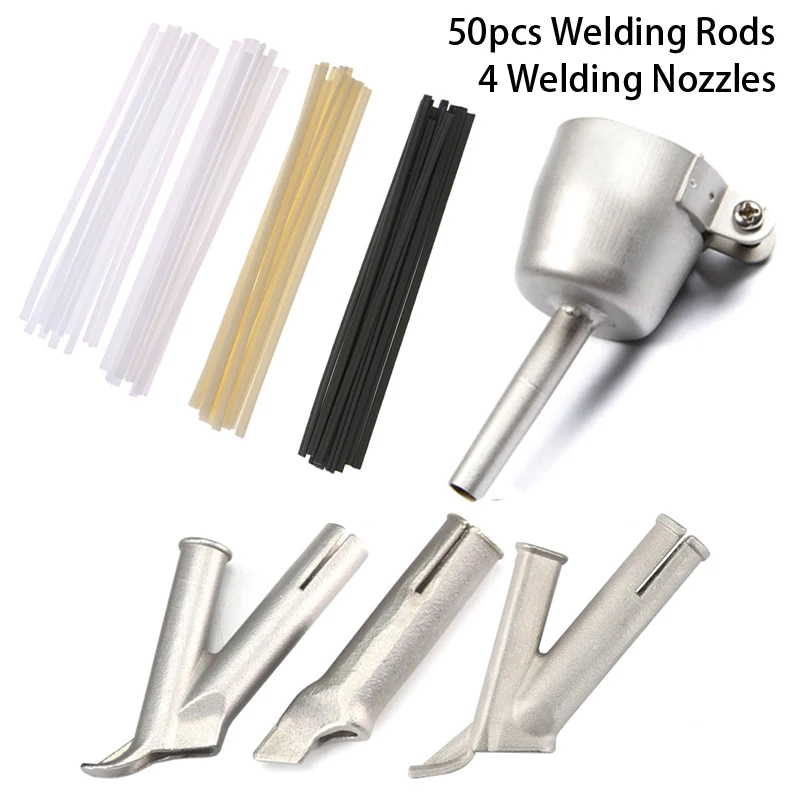


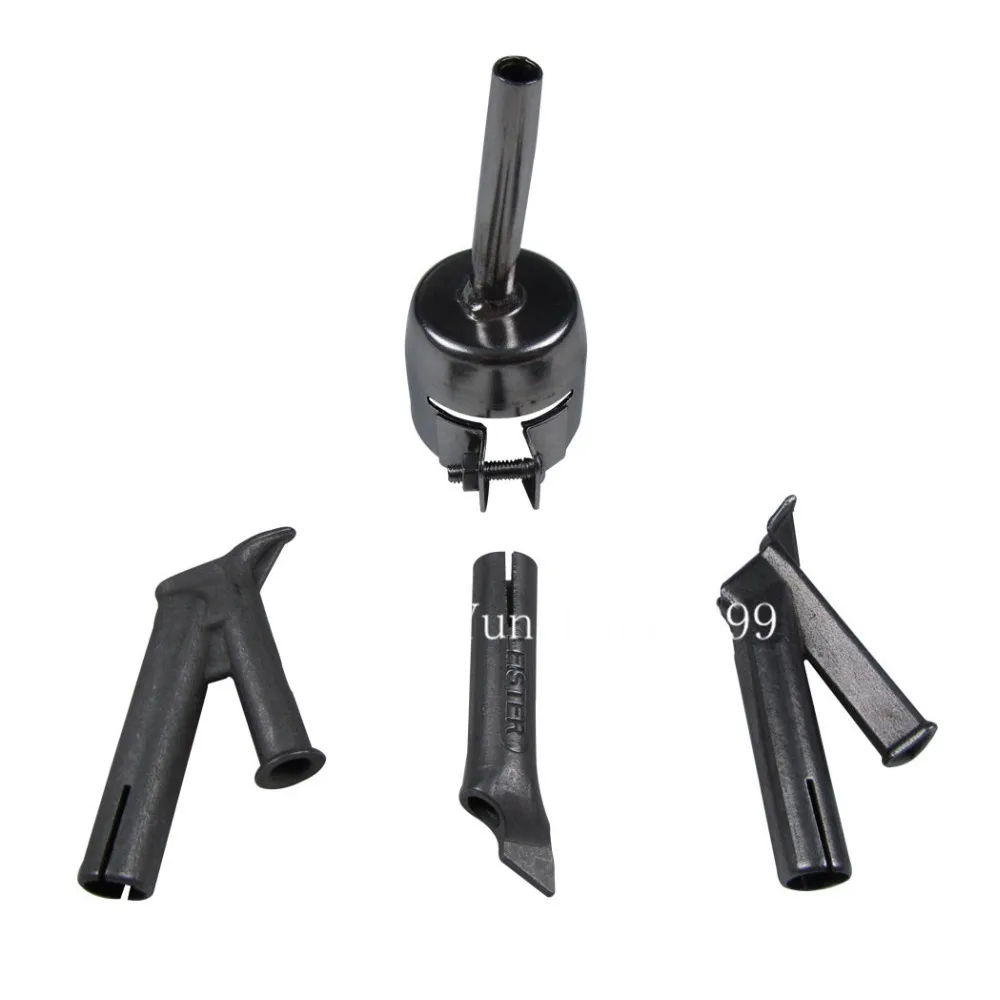



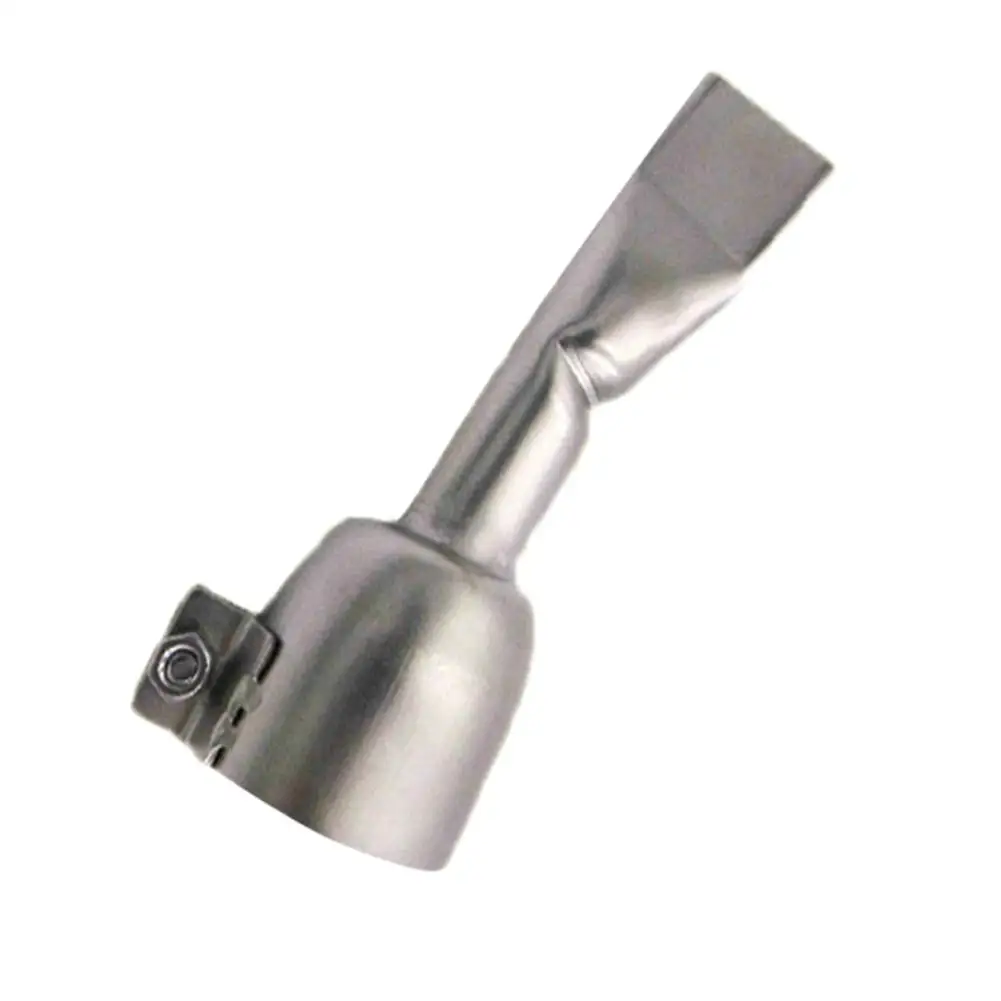
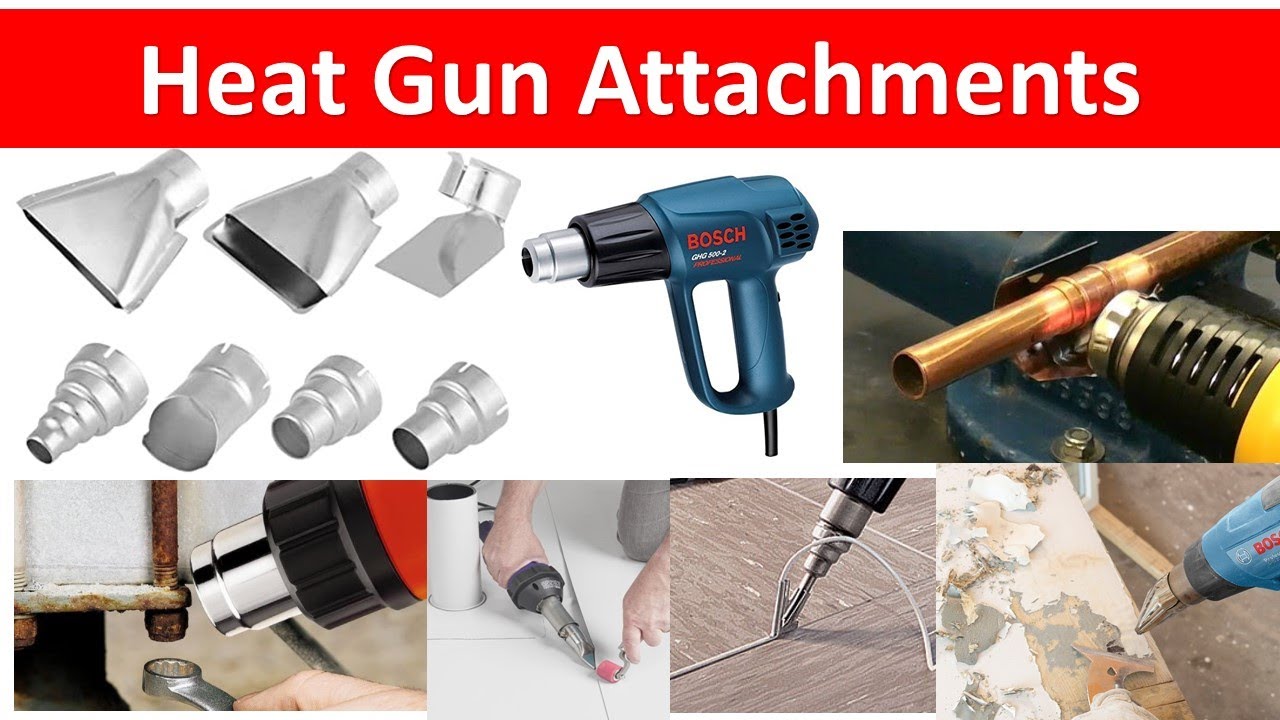

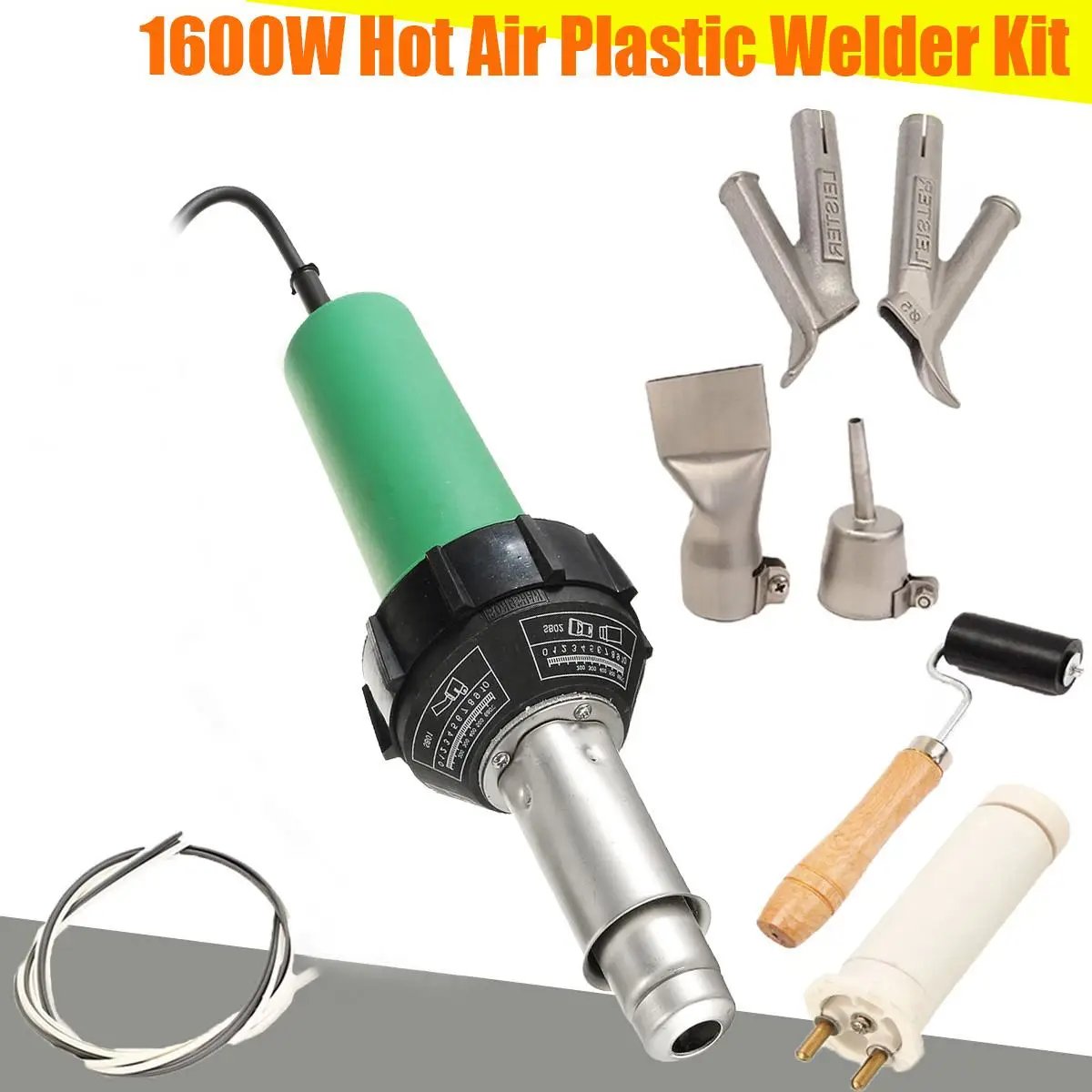

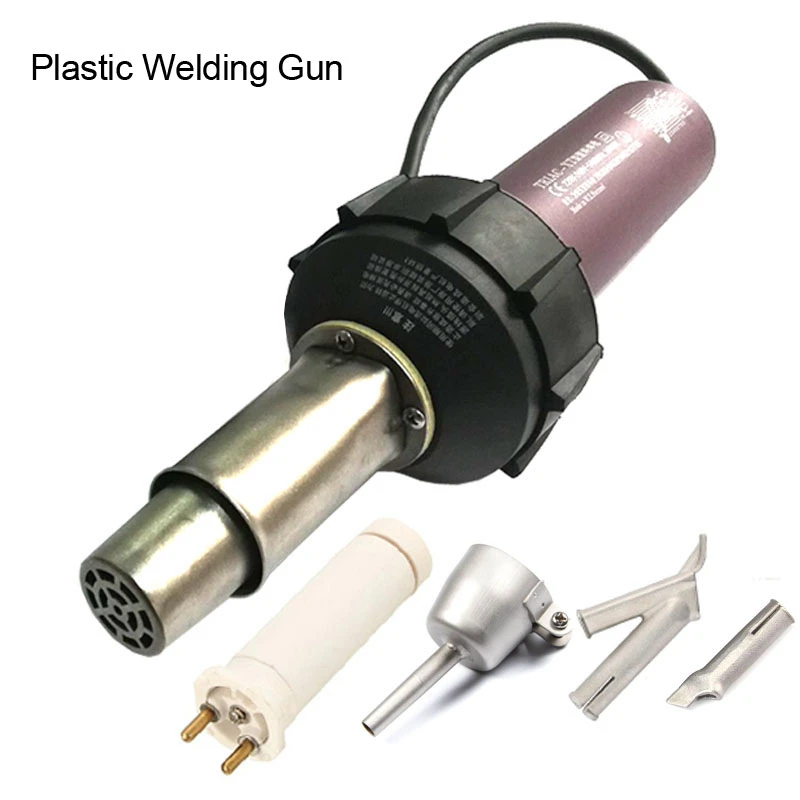

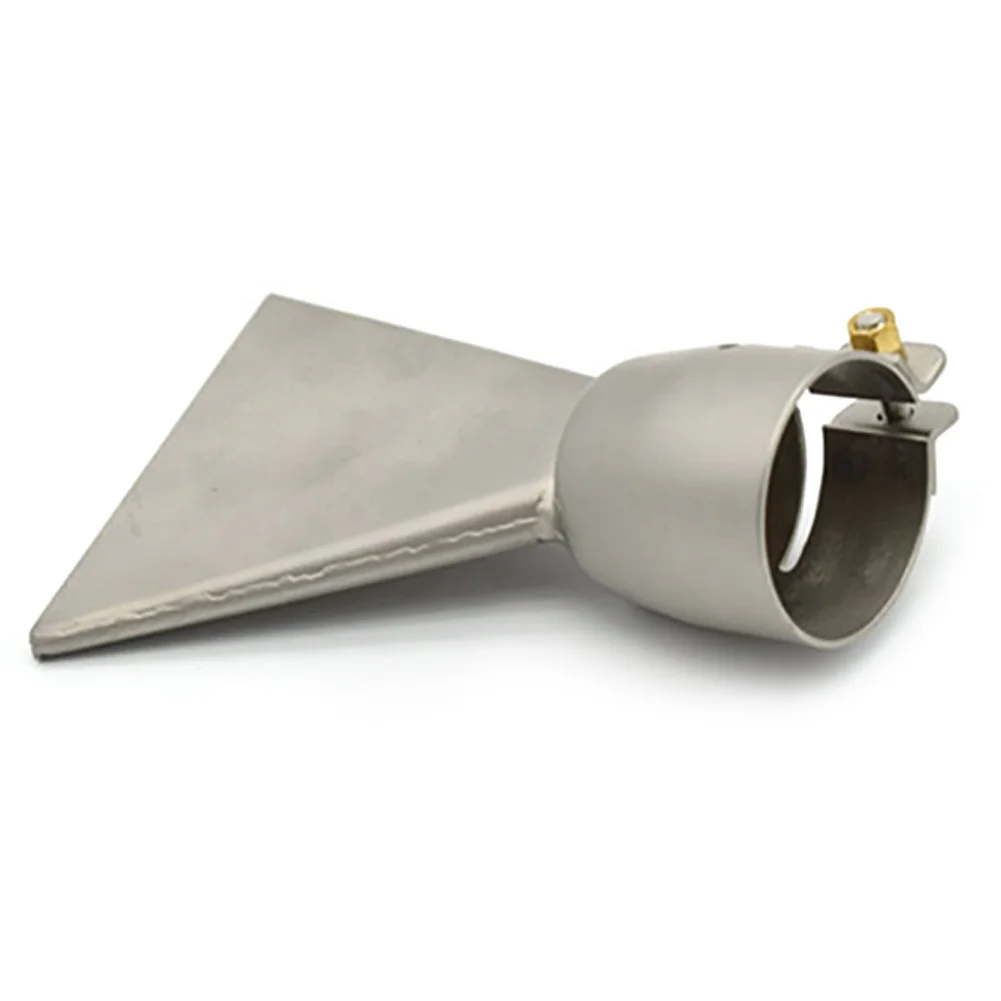
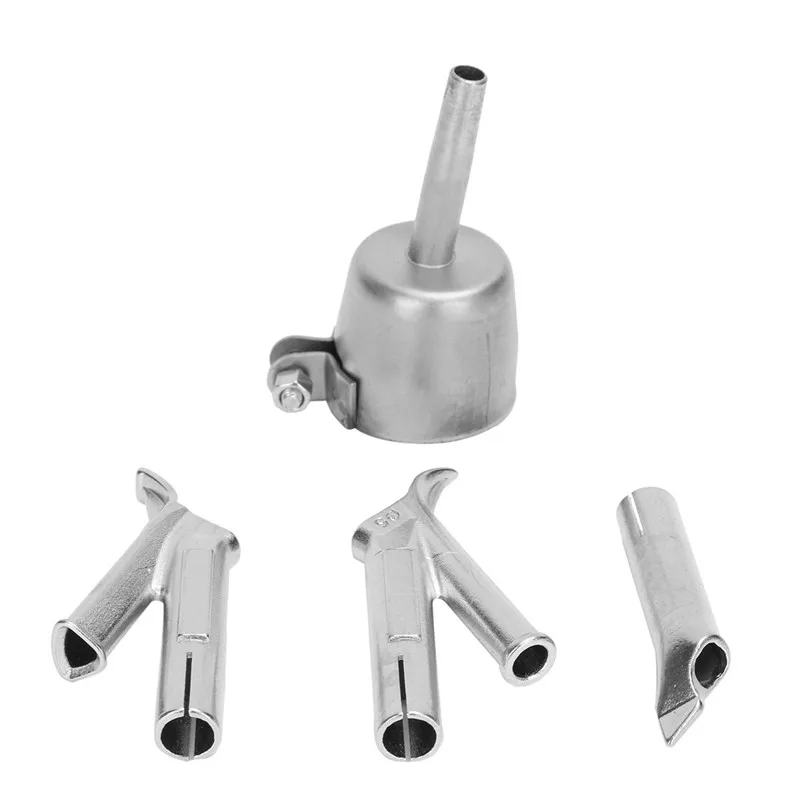

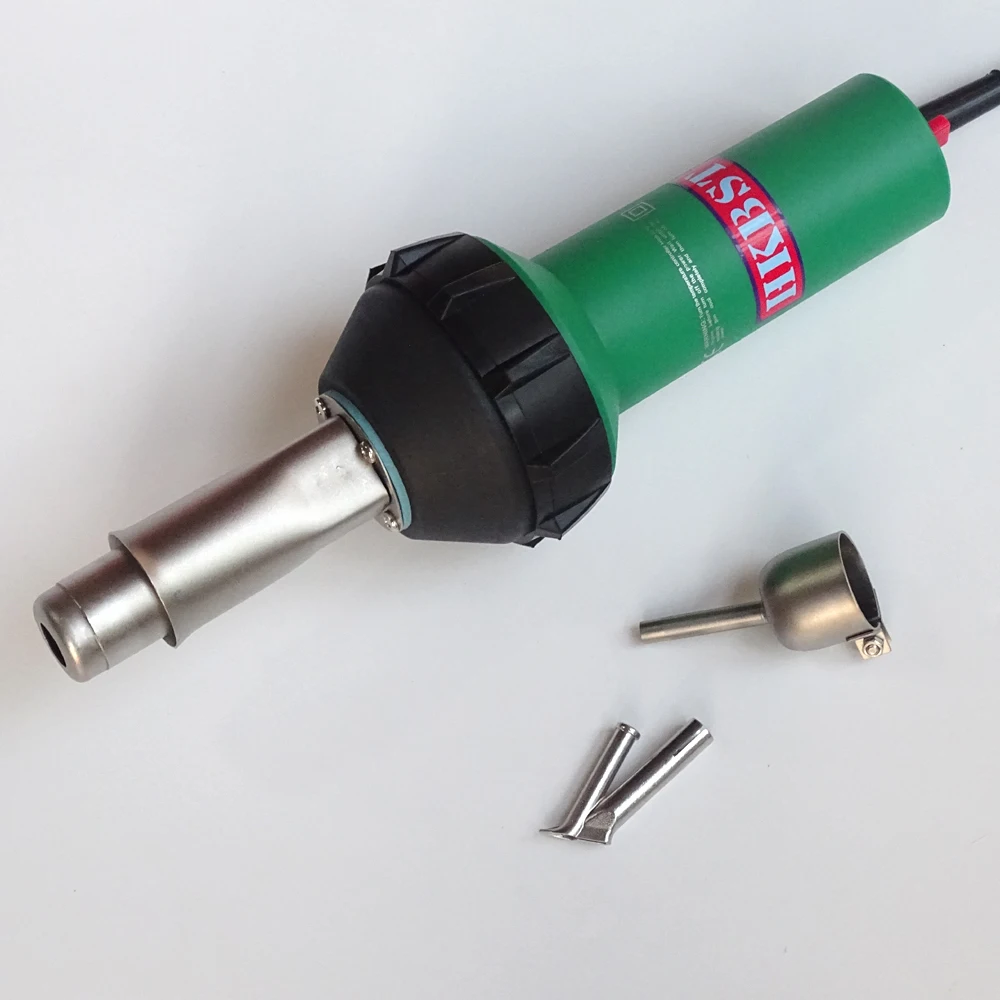