How To Make A Lithium Ion Battery

The global demand for lithium-ion batteries is skyrocketing. Master the core steps to build your own.
This guide provides a streamlined overview of the lithium-ion battery manufacturing process, focusing on essential steps from electrode preparation to final assembly. This article delivers the core processes that drive the future of energy storage.
Electrode Preparation: The Foundation
The process begins with creating the cathode and anode. These electrodes are crucial for ion flow.
Cathode materials, typically lithium metal oxides like Lithium Cobalt Oxide (LCO) or Lithium Iron Phosphate (LFP), are mixed with conductive additives like carbon black and a polymer binder, often PVDF. This mixture forms a slurry.
Similarly, anode materials, generally graphite, are mixed with conductive additives and a binder. The anode slurry is then ready for coating.
These slurries, prepared with meticulous control over particle size and composition, are thinly coated onto metallic foils. Aluminum foil serves as the current collector for the cathode, while copper foil is used for the anode.
After coating, the electrodes undergo a drying process to remove solvents. This ensures proper adhesion of the active material to the foil.
Calendering follows, where the electrodes are compressed to increase density and improve electrical conductivity. This step is vital for maximizing battery performance.
Cell Assembly: Putting it Together
The next stage involves assembling the battery cell. This process requires precision and controlled environments.
The cathode and anode, now prepared, are layered with a separator in between. The separator, typically a thin polymer membrane like polypropylene or polyethylene, prevents direct electrical contact between the electrodes.
There are various cell designs, including cylindrical, prismatic, and pouch cells. Cylindrical cells are widely used due to their robust design and ease of manufacturing.
Prismatic cells offer efficient space utilization. Pouch cells provide flexibility in design.
The layered electrode-separator assembly is then wound or stacked, depending on the cell design. This structure is placed within the cell casing.
Electrolyte Filling and Formation: Activating the Battery
Once the cell is assembled, it needs an electrolyte. The electrolyte facilitates ion transport between the electrodes.
A liquid electrolyte, typically a lithium salt dissolved in an organic solvent, is injected into the cell. The electrolyte must be of high purity to ensure optimal performance and safety.
Following electrolyte filling, the cell undergoes a formation process. This involves charging and discharging the battery for the first few cycles.
The formation process stabilizes the electrode-electrolyte interface and forms a solid electrolyte interphase (SEI) layer.
This SEI layer is critical for battery life and performance.
Testing and Quality Control: Ensuring Reliability
Rigorous testing is essential to ensure the battery meets performance and safety standards. These tests are vital to ensure user safety.
Capacity, voltage, and internal resistance are measured. Cycle life testing assesses the battery's performance over repeated charge-discharge cycles.
Safety tests, including overcharge, over-discharge, and short-circuit tests, are conducted. Thermal stability and abuse tolerance are also assessed to prevent failures.
Quality control measures are implemented throughout the entire manufacturing process. This minimizes defects and ensures consistency.
Where are lithium-ion batteries manufactured?
Asia is the major hub for lithium-ion battery manufacturing. China, South Korea, and Japan are leaders in the industry.
North America and Europe are increasing their manufacturing capacity. Government incentives and growing demand for electric vehicles are driving this trend.
These facilities implement advanced manufacturing techniques and automation. This process maximizes efficiency and precision.
What's Next?
Research and development efforts are focused on improving battery performance, safety, and cost. Solid-state batteries, which replace the liquid electrolyte with a solid one, are a promising area.
These batteries offer higher energy density and improved safety. Lithium-sulfur batteries and lithium-air batteries are also under development.
Advancements in manufacturing techniques, such as dry electrode coating and continuous manufacturing, are being explored. These methods can reduce costs and improve efficiency. The future of battery technology is rapidly evolving.
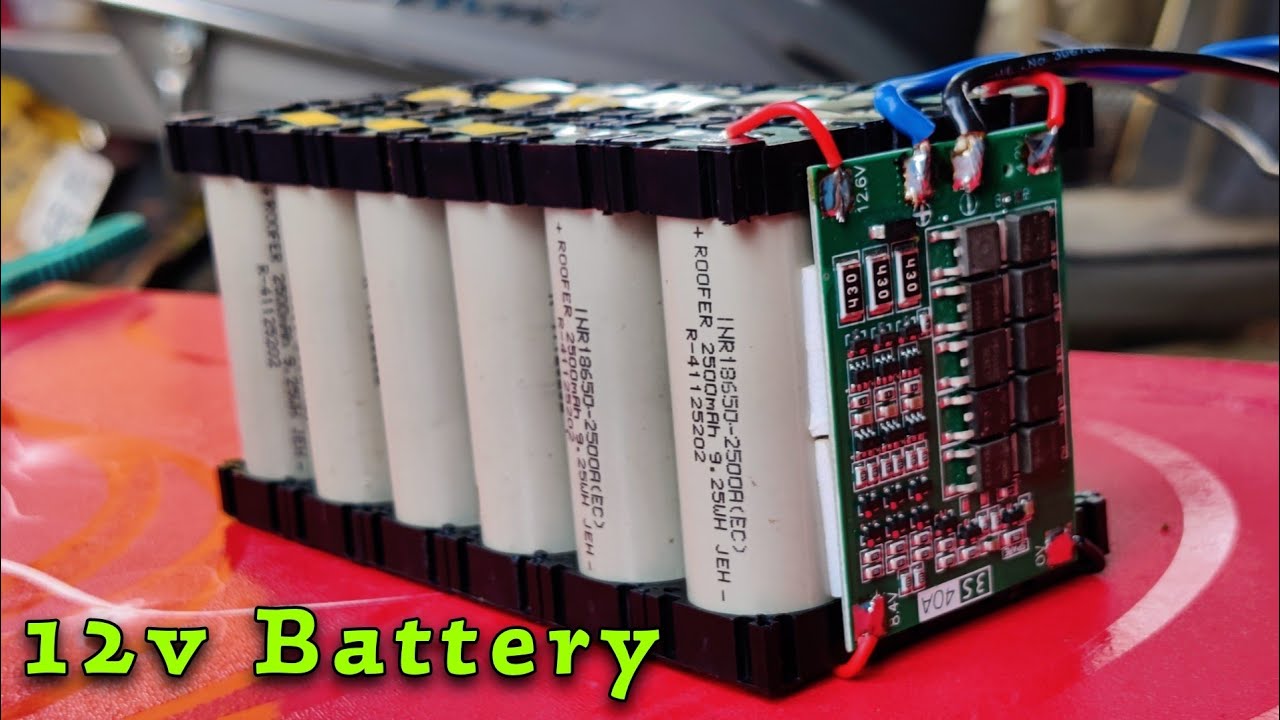
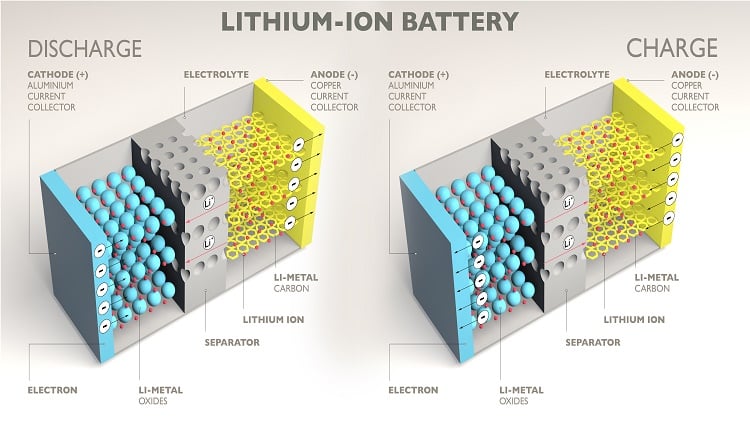

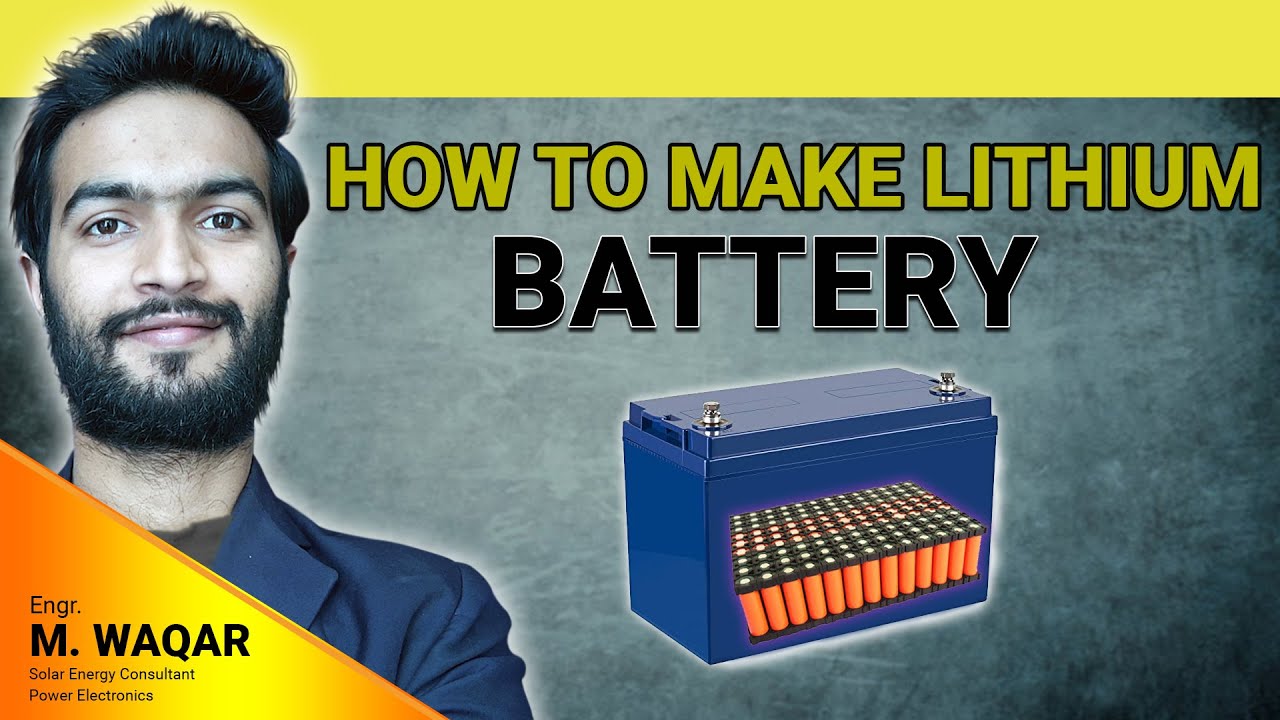
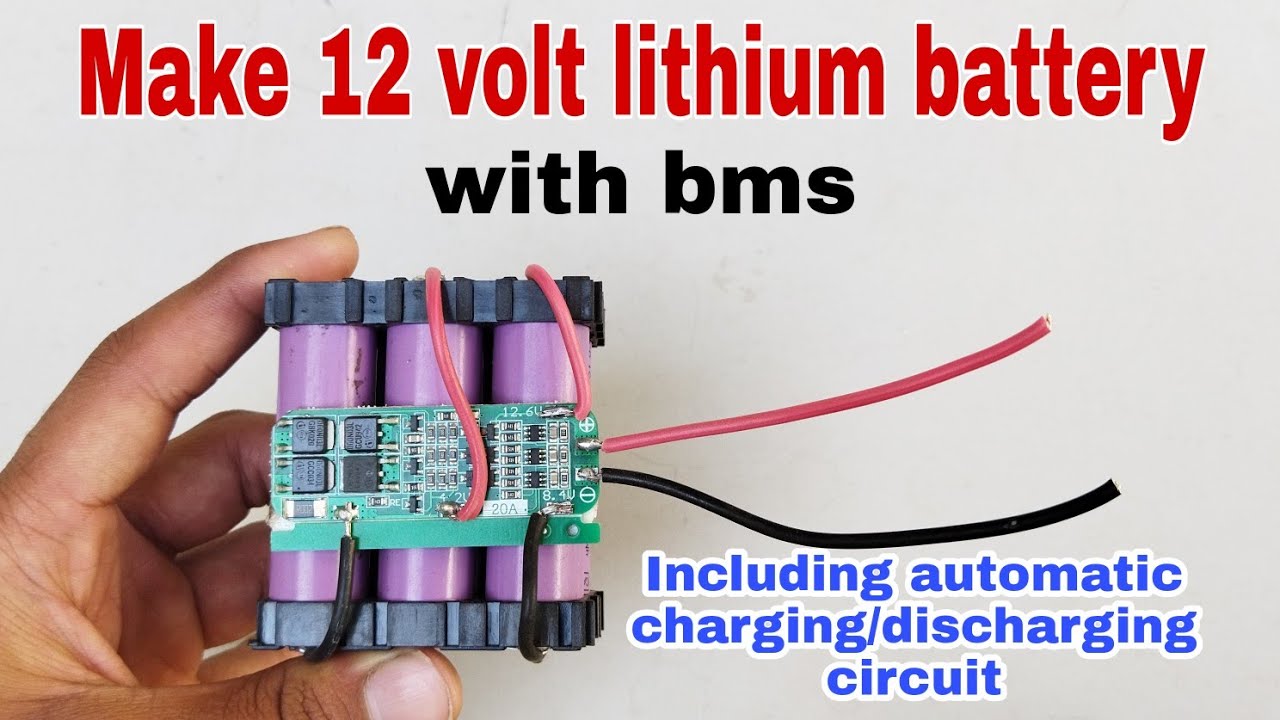

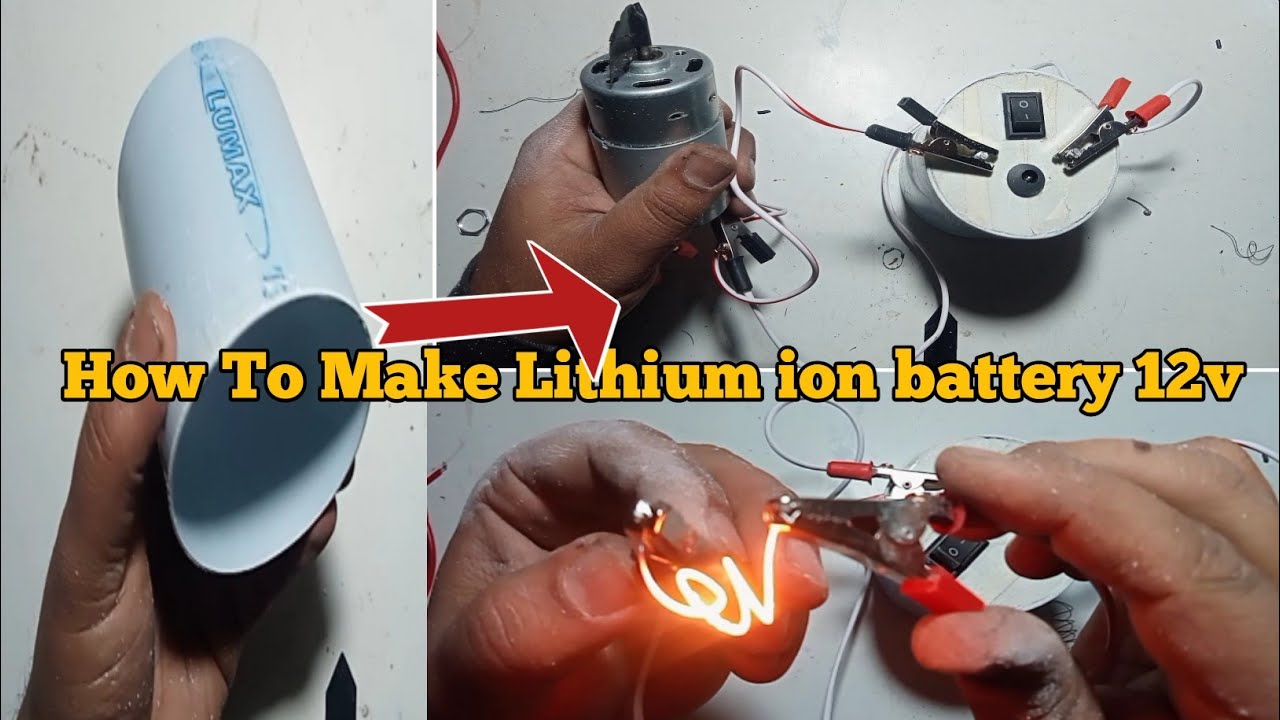
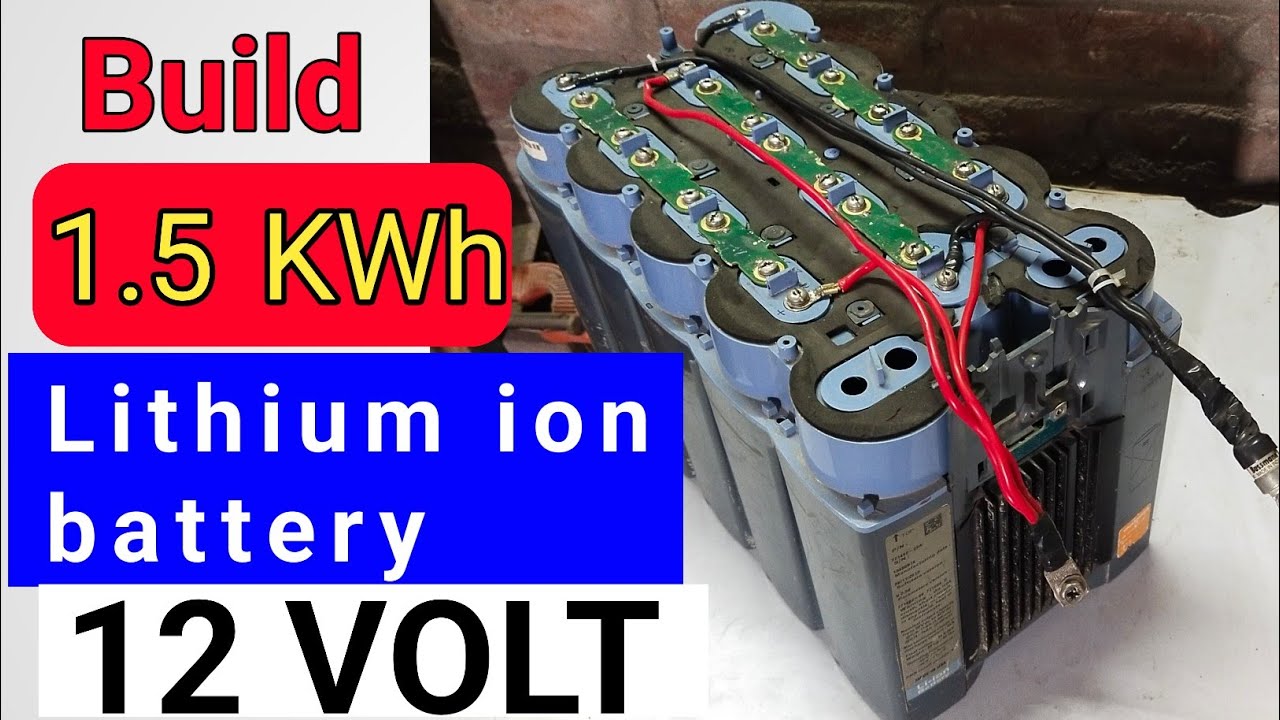

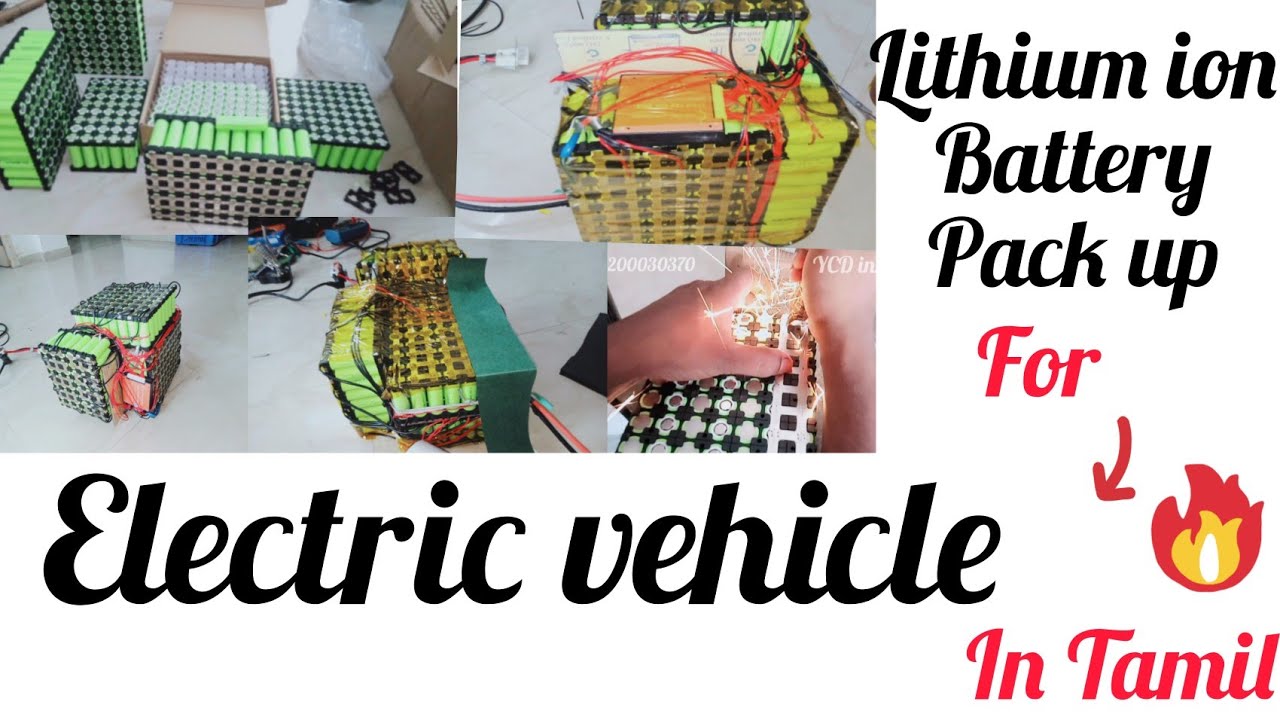
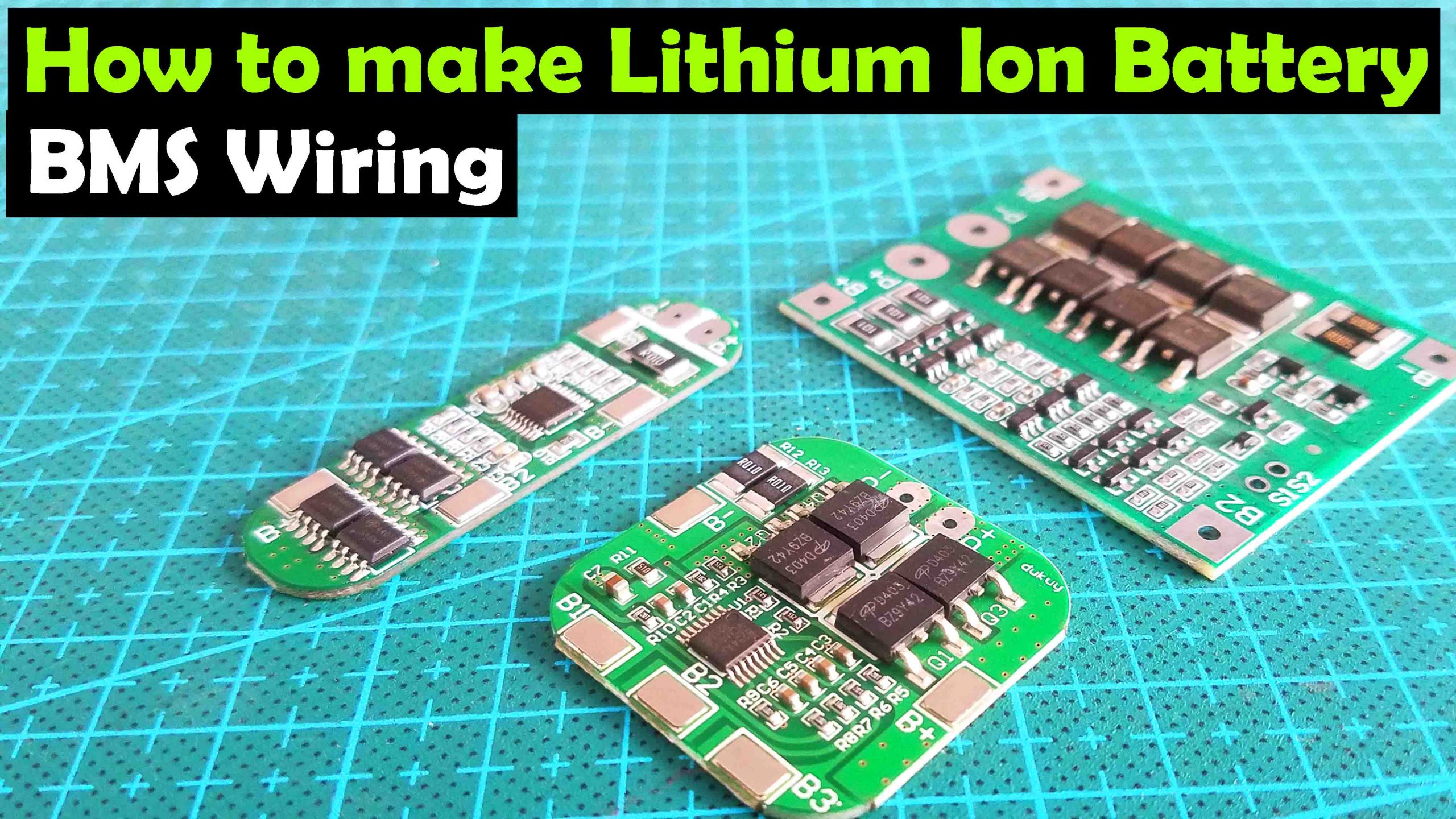
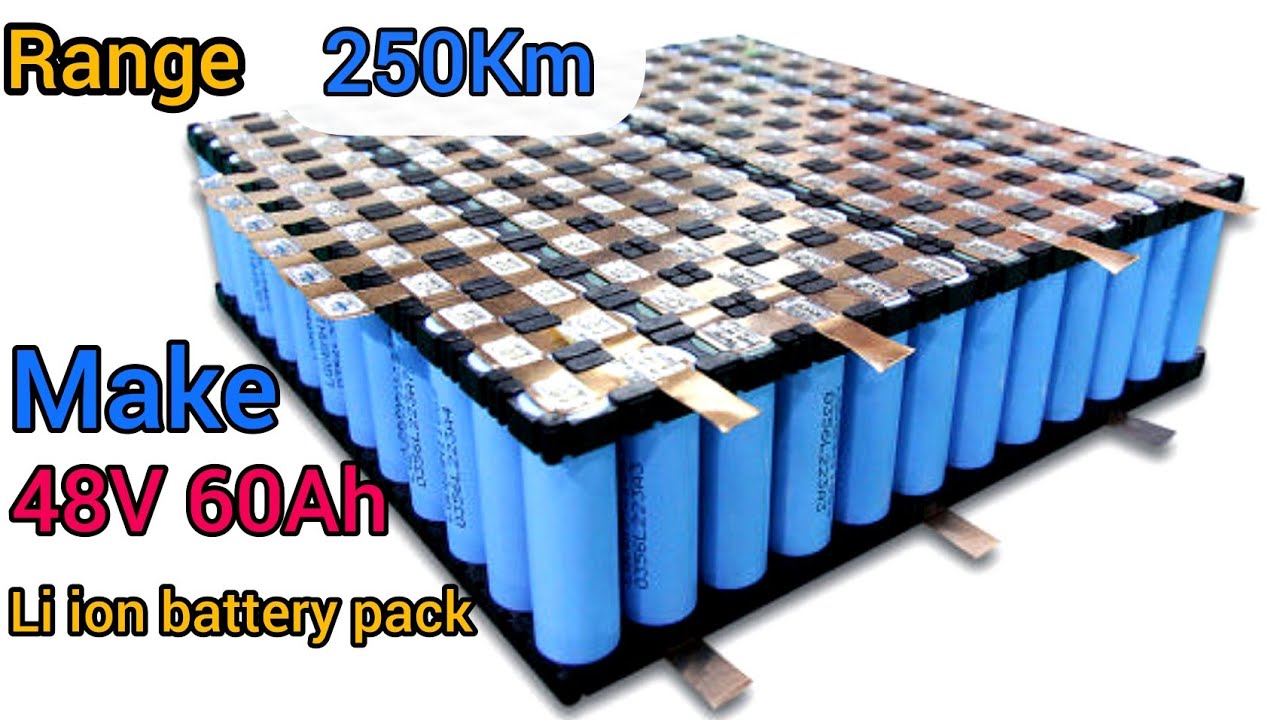

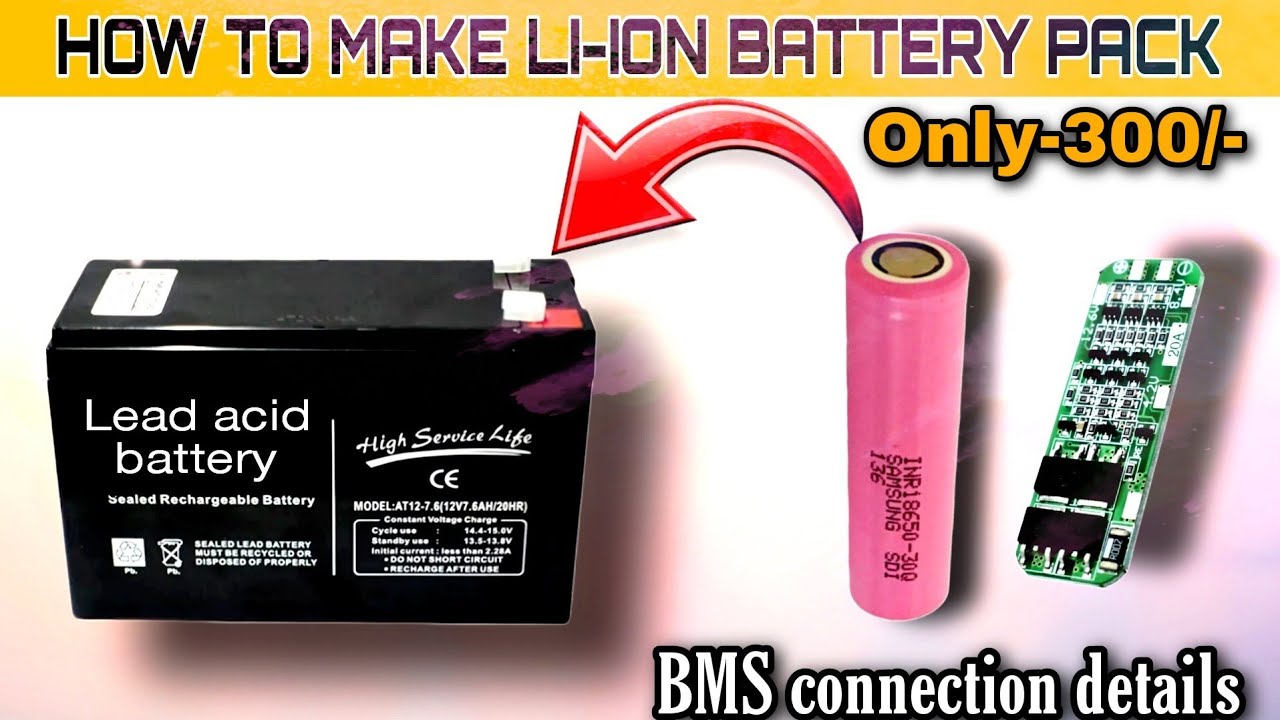


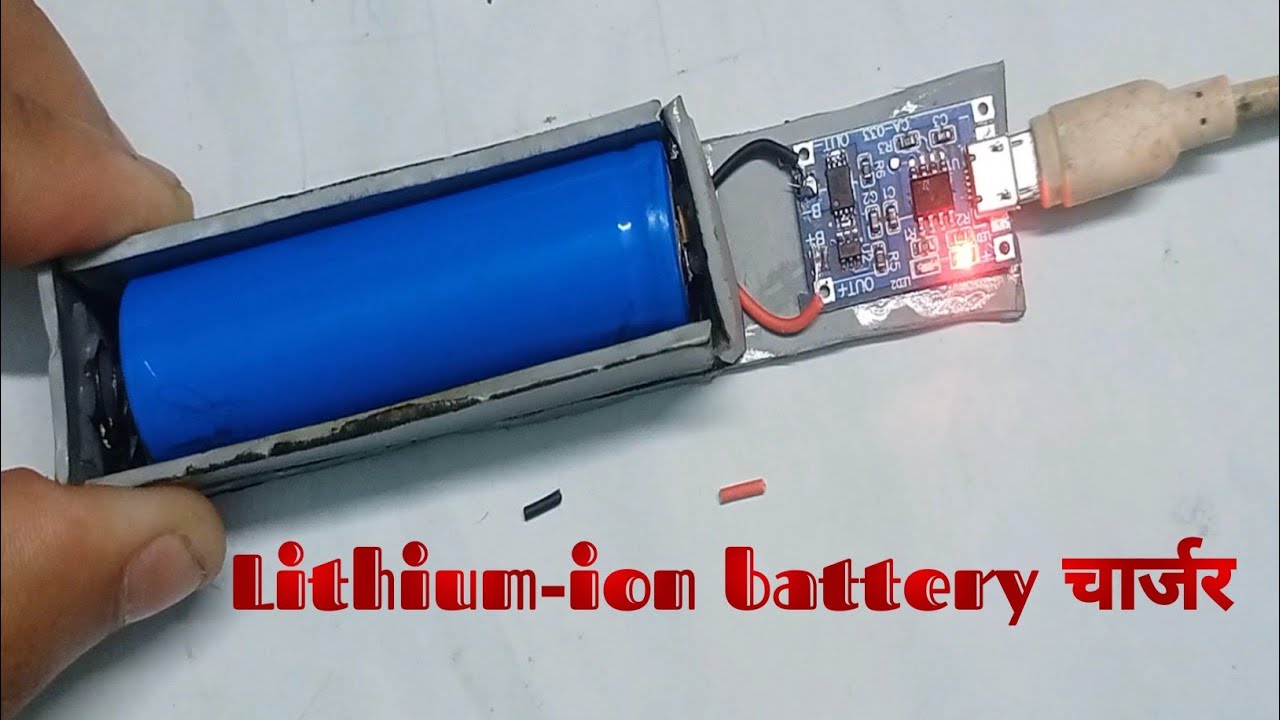
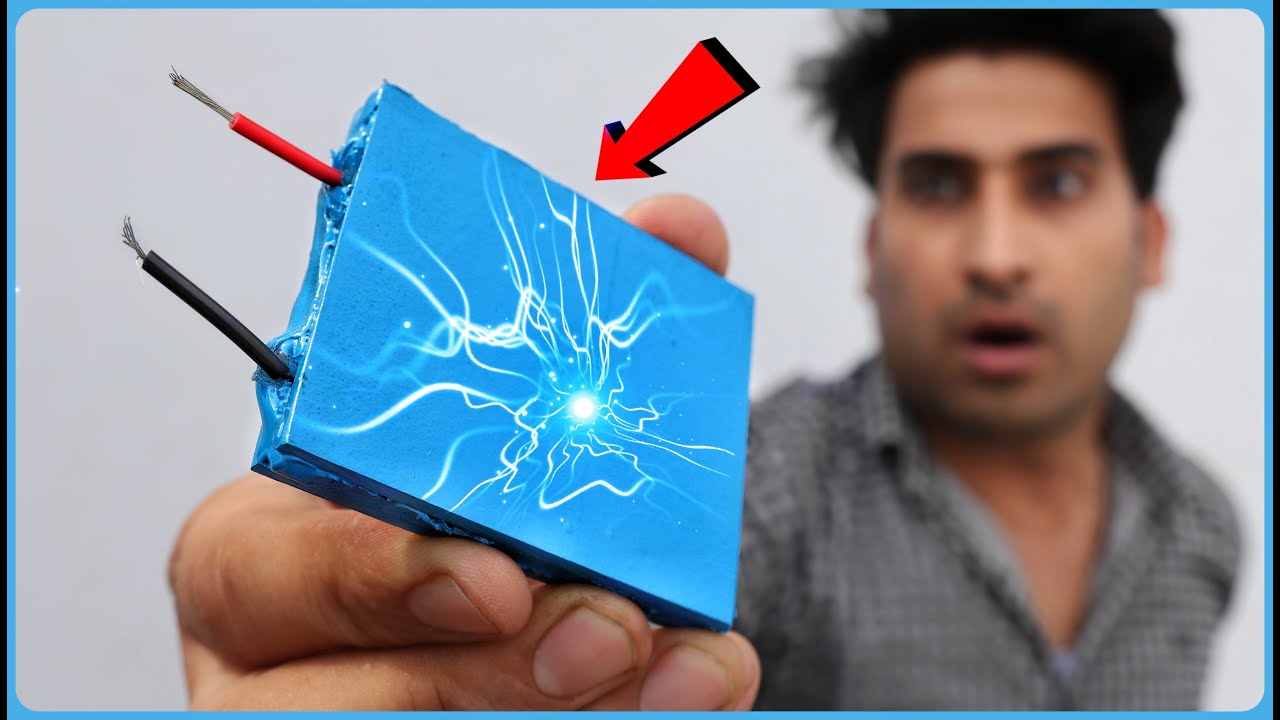