Partially Complete Units Are Known As Inventory.
.jpg)
The intricacies of inventory management often extend beyond finished goods sitting in warehouses. Work-in-process (WIP) inventory, also known as partially completed units, represents a significant component of a company's assets and a critical factor in understanding its operational efficiency. The value of this inventory type is based on the cost of raw materials, labor, and overhead that have been added to it.
Understanding WIP inventory is crucial for businesses across various sectors, from manufacturing to software development. It helps in accurate financial reporting, efficient resource allocation, and ultimately, improved profitability. Accurately accounting for WIP inventory allows businesses to manage costs effectively.
What is Work-in-Process Inventory?
WIP inventory represents goods or services that are currently being transformed into finished products but are not yet ready for sale. This includes materials that have been introduced into the production process but have not been completed, which makes WIP a current asset on a company's balance sheet.
The calculation of WIP inventory involves tracking costs associated with raw materials, direct labor, and manufacturing overhead. Companies meticulously track each of these elements to arrive at a comprehensive valuation.
The Significance of WIP Inventory
WIP inventory is a key indicator of a company’s production cycle efficiency. High levels of WIP may suggest bottlenecks or inefficiencies in the production process. Effective management of WIP is linked directly to optimal production schedules.
Accurate tracking of WIP inventory is essential for financial reporting purposes. Misrepresenting the value of WIP can lead to inaccurate financial statements and misinformed decision-making. Public companies have a duty to report on inventory meticulously.
Who is Affected?
The concept of WIP inventory impacts a broad spectrum of stakeholders. Manufacturers are arguably the most directly affected, as they are the entities that directly manage the transformation of raw materials into finished products.
Accountants and financial analysts rely on accurate WIP data for financial reporting, cost analysis, and budgeting. Investors and shareholders assess a company’s financial health partly based on its inventory management efficiency.
Examples Across Industries
In manufacturing, WIP inventory could include partially assembled automobiles, components waiting for further processing, or batches of chemicals undergoing refinement. Software companies also have WIP, in the form of software code that is being developed and tested but is not yet ready for release.
Construction companies deal with WIP constantly, as projects move through various stages. WIP in construction might represent costs associated with a building under construction where a significant portion of work has been done. These companies must ensure that all costs are correctly recorded.
How to Manage WIP Inventory Effectively
Efficient WIP inventory management requires the implementation of robust tracking systems. Businesses often use sophisticated Enterprise Resource Planning (ERP) systems to monitor inventory levels.
Implementing just-in-time (JIT) inventory management can minimize WIP by ensuring that materials arrive only when they are needed. This approach reduces the risk of accumulating excess inventory. JIT is a proven method that has helped countless businesses save money and reduce waste.
The Role of Technology
Modern technologies such as barcode scanners and RFID tags can improve the accuracy and efficiency of WIP tracking. Real-time data provides enhanced visibility into the production process.
Data analytics can be used to identify patterns, predict potential bottlenecks, and optimize production schedules. Predictive analytics empowers business leaders to be proactive in maintaining efficient processes.
Potential Challenges and Pitfalls
One of the primary challenges in managing WIP inventory is accurately valuing the partially completed units. Estimating the percentage of completion and attributing costs accordingly can be complex.
Obsolete or damaged WIP inventory can result in significant losses. Regular inspections and proactive measures can prevent such losses, protecting against devaluation of assets.
Impact of Economic Fluctuations
Changes in raw material prices and labor costs can affect the valuation of WIP inventory. Businesses need to factor in these fluctuations to ensure financial reporting accurately reflects the company's financial position.
Economic downturns can lead to a decrease in demand for finished goods, resulting in a build-up of WIP inventory. In turn, this can increase storage costs and tie up capital.
Conclusion
Effectively managing work-in-process inventory is crucial for maintaining operational efficiency and financial accuracy. Businesses must implement robust tracking systems, regularly assess valuation methods, and proactively address challenges related to WIP.
By understanding the intricacies of WIP inventory, companies can enhance decision-making, improve profitability, and gain a competitive edge in their respective industries. The implications of understanding WIP inventory can be very beneficial for the accounting processes of all companies.
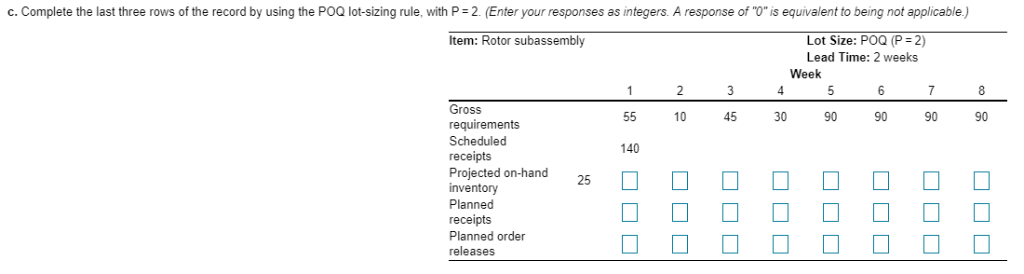


.jpg)
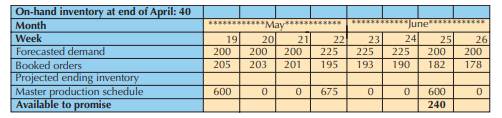
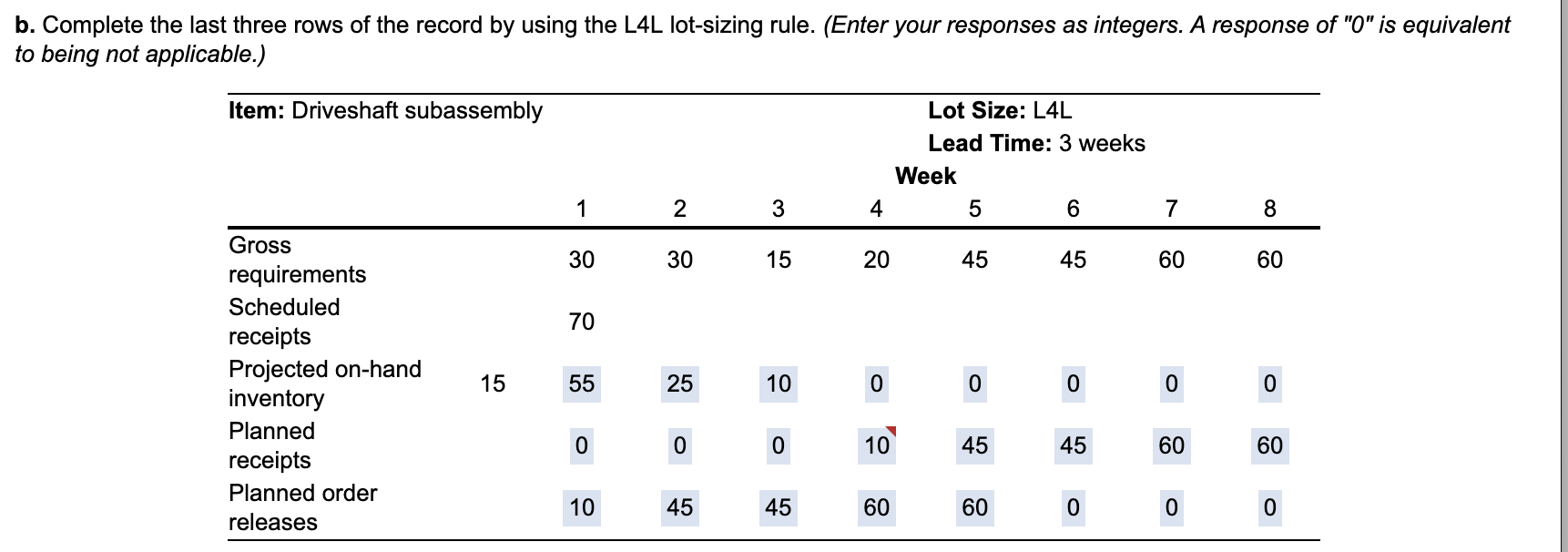
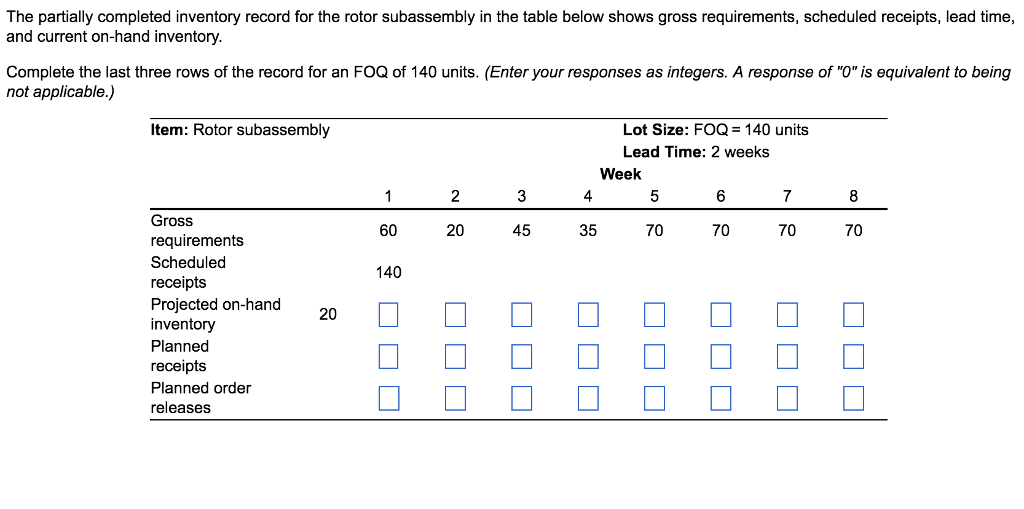
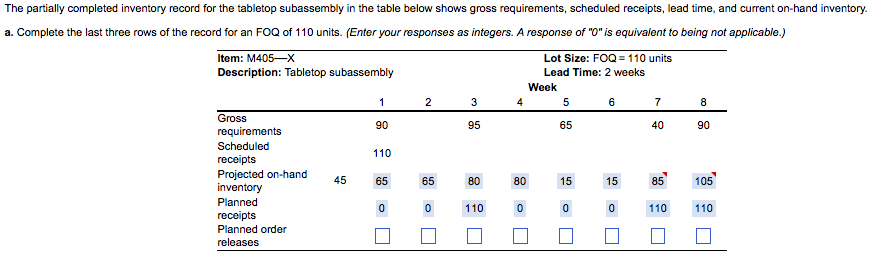
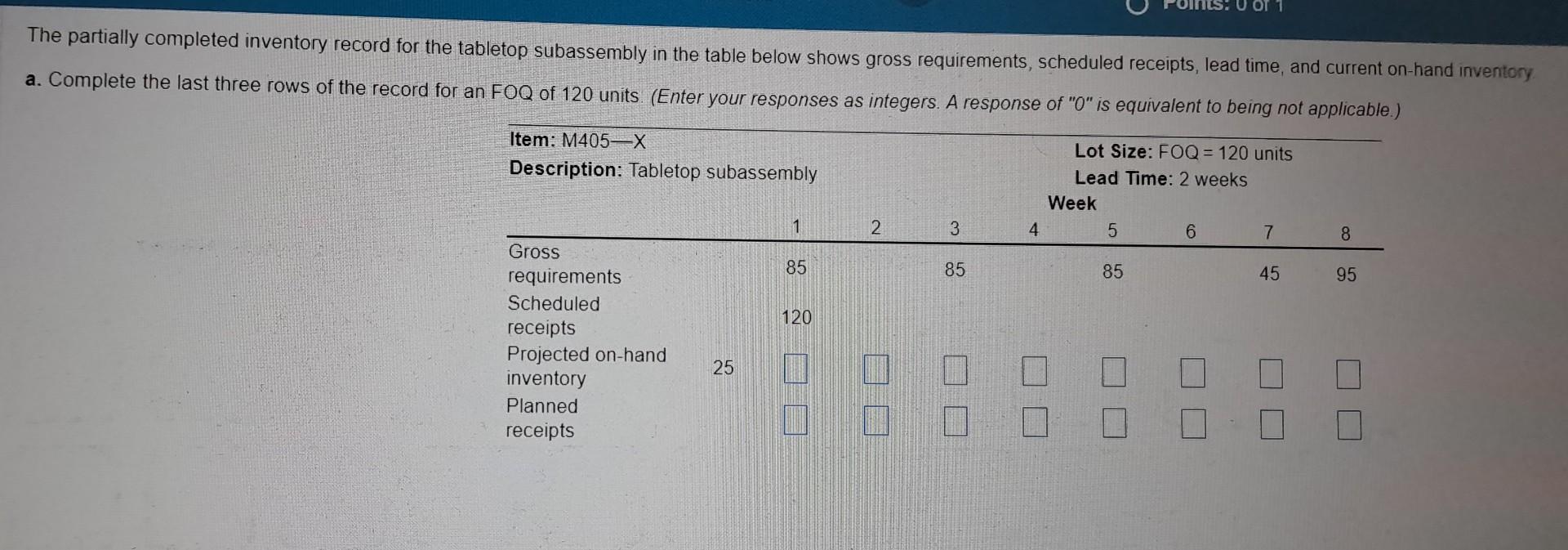
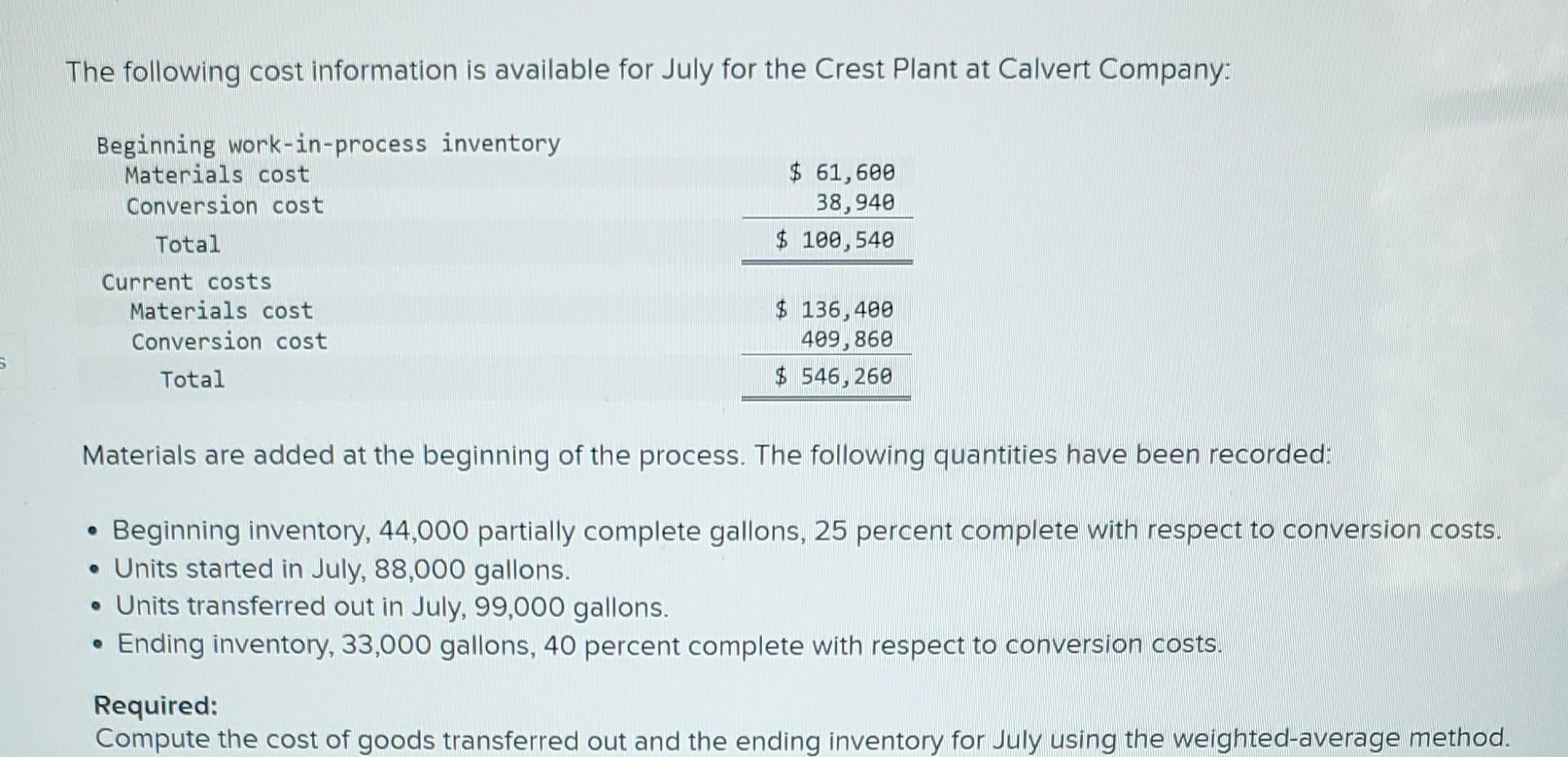